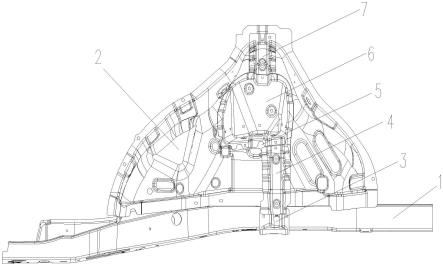
1.本实用新型涉及车辆零部件领域,具体涉及一种后轮罩总成结构。
背景技术:2.目前现有车型,轮罩内板刚度较弱,减震器和纵梁相连,减震器压缩方向和摆臂运动方向角度大,减震效果差,若为螺旋簧减震器的车辆,在颠簸路况中易出现结构变形,疲劳情况下甚至破裂,为此在防止轮罩破裂的情况,一般会设置轮罩加强板,但加强效果有限。
3.因此,为解决以上问题,需要一种后轮罩总成结构,解决上述问题。
技术实现要素:4.有鉴于此,本技术方案的后轮罩总成结构,减震器安装板形成了腔体结构,确保结构的刚度以及强度,提升了减震器的安装稳定性能,减震器加强板对腔体结构形成有效支撑,确保了减震器的连接安装,轮罩内板实现减震器安装功能,有效的优化了减震器布置位置,让减震器压缩方向和摆臂摆动方向一致,加强了缓冲效果,提升了轮罩的刚度,避免因刚强度不足导致的轮罩变形及开裂现象。
5.一种后轮罩总成结构,包括安装于纵梁上的轮罩内板、安装于轮罩内板内的减震器安装板组件以及轮罩内连接板组件,所述减震器安装板组件包括安装于轮罩内板内的减震器加强板以及配合减震器加强板使用的减震器安装板,所述减震器安装板贴合安装于轮罩内板并形成腔体式结构。
6.进一步,所述减震器加强板整体呈“l”型结构,所述减震器加强板包括下端贴合安装于轮罩内板内表面的贴合部以及上端贴合安装于减震器安装板内的支撑部。
7.进一步,所述减震器安装板中部向外凸起形成用于安装减震器的安装凸台,减震器安装板周向方向形成有配合轮罩内板安装的翻边结构。
8.进一步,所述减震器安装板下端贴合安装于贴合部上,支撑部贴合安装于所述安装凸台的内表面,所述安装凸台上设置有定位安装孔。
9.进一步,所述轮罩内连接板组件包括轮罩上板以及轮罩下板,所述轮罩上板一端贴合安装于轮罩内板上,轮罩上板另一端与减震器安装板贴合安装。
10.进一步,所述轮罩上板沿长度方向向外凸起形成凸筋,所述轮罩上板上沿凸筋周向方向凸起形成多条加强筋。
11.进一步,所述减震器安装板上端向外凸起形成配合凸筋进行连接安装的让位结构。
12.进一步,所述轮罩下板一端连接安装于减震器安装板下端,轮罩下板另一端延伸至纵梁上,所述纵梁上设置有配合轮罩下板进行连接安装的纵梁连接板。
13.进一步,还包括轮罩外加强板,所述轮罩外加强板贴合安装于轮罩内板外表面。
14.本实用新型的有益效果是:本技术方案的后轮罩总成结构,减震器安装板形成了
腔体结构,确保结构的刚度以及强度,提升了减震器的安装稳定性能,减震器加强板对腔体结构形成有效支撑,确保了减震器的连接安装,轮罩内板实现减震器安装功能,有效的优化了减震器布置位置,让减震器压缩方向和摆臂摆动方向一致,加强了缓冲效果,提升了轮罩的刚度,避免因刚强度不足导致的轮罩变形及开裂现象。
附图说明
15.下面结合附图和实施例对本实用新型作进一步描述:
16.图1为本实用新型整体结构示意图;
17.图2为本实用新型俯视图;
18.图3为本实用新型爆炸示意图。
具体实施方式
19.图1为本实用新型整体结构示意图;图2为本实用新型俯视图;图3为本实用新型爆炸示意图;如图所示,一种后轮罩总成结构,包括安装于纵梁1上的轮罩内板2、安装于轮罩内板2内的减震器安装板组件以及轮罩内连接板组件,所述减震器安装板组件包括安装于轮罩内板内的减震器加强板5以及配合减震器加强板使用的减震器安装板6,所述减震器安装板6贴合安装于轮罩内板并形成腔体式结构;本技术方案的后轮罩总成结构,减震器安装板形成了腔体结构,确保结构的刚度以及强度,提升了减震器的安装稳定性能,减震器加强板对腔体结构形成有效支撑,确保了减震器的连接安装,轮罩内板实现减震器安装功能,有效的优化了减震器布置位置,让减震器压缩方向和摆臂摆动方向一致,加强了缓冲效果,提升了轮罩的刚度,避免因刚强度不足导致的轮罩变形及开裂现象。
20.本实施例中,所述减震器加强板5整体呈“l”型结构,所述减震器加强板5包括下端贴合安装于轮罩内板2内表面的贴合部以及上端贴合安装于减震器安装板内的支撑部。(如图3所示)“l”型结构的减震器加强板5下端贴合安装与轮罩内板2,减震器加强板5的支撑部垂直于贴合部并形成对减震器安装板6的有效支撑。
21.本实施例中,所述减震器安装板6中部向外凸起形成用于安装减震器的安装凸台,减震器安装板周向方向形成有配合轮罩内板安装的翻边结构62。减震器安装板6贴合安装在轮罩内板2并凸起形成腔体结构,有效的对减震器安装提供了支撑平台,翻边结构62与轮罩内板2贴合后固定安装,确保整体结构连接的稳定性。
22.本实施例中,所述减震器安装板下端贴合安装于贴合部上,支撑部贴合安装于所述安装凸台的内表面,所述安装凸台上设置有定位安装孔63。减震器安装板下端通过翻边结构62叠合安装在贴合部上,定位安装孔63的设置便于实现减震器的定位安装。
23.本实施例中,所述轮罩内连接板组件包括轮罩上板7以及轮罩下板4,所述轮罩上板7一端贴合安装于轮罩内板上,轮罩上板另一端与减震器安装板6贴合安装。轮罩上板7以及轮罩下板4起到过渡连接安装的作用,确保整体结构安装的稳定性。
24.本实施例中,所述轮罩上板沿长度方向(即图3中竖直方向)向外凸起形成凸筋,所述轮罩上板上沿凸筋周向方向凸起形成多条加强筋71。通过凸筋以及周向形成的多条加强筋71结构,提升了轮罩上板7整体结构的强度,保证减震器安装板6定位安装后的稳定性能。
25.本实施例中,所述减震器安装板6上端向外凸起形成配合凸筋进行连接安装的让
位结构61。让位结构61配合凸筋进行定位安装,确保了减震器安装板6安装精度以及整体安装的结构强度。
26.本实施例中,所述轮罩下板4一端连接安装于减震器安装板6下端,轮罩下板另一端延伸至纵梁1上,所述纵梁上设置有配合轮罩下板进行连接安装的纵梁连接板3。通过轮罩下板以及纵梁连接板3的设置,使得轮罩整体结构与纵梁形成有效连接安装,确保整体结构的稳定性。
27.本实施例中,还包括轮罩外加强板8,所述轮罩外加强板8贴合安装于轮罩内板外表面。轮罩外加强板8确保了轮罩外部的结构强度。
28.最后说明的是,以上实施例仅用以说明本实用新型的技术方案而非限制,尽管参照较佳实施例对本实用新型进行了详细说明,本领域的普通技术人员应当理解,可以对本实用新型的技术方案进行修改或者等同替换,而不脱离本实用新型技术方案的宗旨和范围,其均应涵盖在本实用新型的权利要求范围当中。
技术特征:1.一种后轮罩总成结构,其特征在于:包括安装于纵梁上的轮罩内板、安装于轮罩内板内的减震器安装板组件以及轮罩内连接板组件,所述减震器安装板组件包括安装于轮罩内板内的减震器加强板以及配合减震器加强板使用的减震器安装板,所述减震器安装板贴合安装于轮罩内板并形成腔体式结构。2.根据权利要求1所述的后轮罩总成结构,其特征在于:所述减震器加强板整体呈“l”型结构,所述减震器加强板包括下端贴合安装于轮罩内板内表面的贴合部以及上端贴合安装于减震器安装板内的支撑部。3.根据权利要求2所述的后轮罩总成结构,其特征在于:所述减震器安装板中部向外凸起形成用于安装减震器的安装凸台,减震器安装板周向方向形成有配合轮罩内板安装的翻边结构。4.根据权利要求3所述的后轮罩总成结构,其特征在于:所述减震器安装板下端贴合安装于贴合部上,支撑部贴合安装于所述安装凸台的内表面,所述安装凸台上设置有定位安装孔。5.根据权利要求4所述的后轮罩总成结构,其特征在于:所述轮罩内连接板组件包括轮罩上板以及轮罩下板,所述轮罩上板一端贴合安装于轮罩内板上,轮罩上板另一端与减震器安装板贴合安装。6.根据权利要求5所述的后轮罩总成结构,其特征在于:所述轮罩上板沿长度方向向外凸起形成凸筋,所述轮罩上板上沿凸筋周向方向凸起形成多条加强筋。7.根据权利要求6所述的后轮罩总成结构,其特征在于:所述减震器安装板上端向外凸起形成配合凸筋进行连接安装的让位结构。8.根据权利要求7所述的后轮罩总成结构,其特征在于:所述轮罩下板一端连接安装于减震器安装板下端,轮罩下板另一端延伸至纵梁上,所述纵梁上设置有配合轮罩下板进行连接安装的纵梁连接板。9.根据权利要求1所述的后轮罩总成结构,其特征在于:还包括轮罩外加强板,所述轮罩外加强板贴合安装于轮罩内板外表面。
技术总结本实用新型公开了一种后轮罩总成结构,包括安装于纵梁上的轮罩内板、安装于轮罩内板内的减震器安装板组件以及轮罩内连接板组件,减震器安装板组件包括安装于轮罩内板内的减震器加强板以及配合减震器加强板使用的减震器安装板,所述减震器安装板贴合安装于轮罩内板并形成腔体式结构,本技术方案的后轮罩总成结构,减震器安装板形成了腔体结构,确保结构的刚度以及强度,提升了减震器的安装稳定性能,减震器加强板对腔体结构形成有效支撑,确保了减震器的连接安装,轮罩内板实现减震器安装功能,有效的优化了减震器布置位置,让减震器压缩方向和摆臂摆动方向一致,加强了缓冲效果,提升了轮罩的刚度,避免因刚强度不足导致的轮罩变形及开裂现象。罩变形及开裂现象。罩变形及开裂现象。
技术研发人员:胡欢 狄武飞 张明星 禹贵春 彭启明
受保护的技术使用者:东风小康汽车有限公司重庆分公司
技术研发日:2022.03.28
技术公布日:2022/7/22