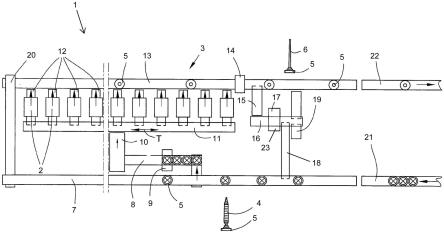
1.本发明涉及用于识别从纺纱筒子筒管去除卷绕残余物(winding residues)的检测装置,包括用光照亮纺纱筒子筒管的光源、用于形成纺纱筒子筒管的数字图像的图像拍摄装置以及用于评估数字图像的评估装置。本发明还涉及包括这种检测装置的用于去除卷绕残余物的筒管清洁装置,还有包括这种筒管清洁装置的卷绕机。最后,本发明涉及用于纺纱筒子筒管上的卷绕残余物的方法。
背景技术:2.在卷绕机的卷绕位置上,喂给筒子例如在环锭纺纱机上生产的包含较低纱线量的纺纱筒子被倒筒成大卷装交叉卷绕筒子。给卷绕位置供应纱线材料例如在可人工装载的卷绕机中通过卷绕位置自身的筒子库进行,筒子库被设计成所谓的圆形筒子库,而在自动化联合体中纺纱机通过输送系统与卷绕机相连,在输送系统中纺纱筒子在纺纱机和卷绕机之间被自动输送。
3.现代纺纱机的大量且通常定期的纺纱筒子产量对后置卷绕机的处理能力提出更高的要求。还需要将足够量的退绕筒管送回至纺纱机。因此,为了保证高度自动化而流行在卷绕机区域内的闭合输送循环以及或许与纺纱机的直接连接。纺纱筒子和纺纱筒子筒管因此经历循环过程,由此材料流形成所谓的闭合式纺纱筒子和筒管输送系统。
4.在环锭纺纱机中制成纱线之后,所出现的纺纱筒子自动到达卷绕机并在那里被插装到纺纱筒子载体或输送盘上。通过输送带,纺纱筒子从插装站被送至纺纱筒子准备站,以便在那里开松纱线末端并且提供用于晚些的可靠抓住。随后,纺纱筒子移入一个在此进行倒筒的卷绕位置。
5.正常情况下,纺纱筒子在卷绕位置中被退绕全空,即,它们作为空纺纱筒子筒管离开卷绕位置。但可能出现留下一个或多或少大的卷绕残余物,其纱线头在卷绕位置内无法再被供给相应的导纱部件或接纱装置并且假设是空的纺纱筒子筒管最终从卷绕位置被抛出。因此未保证所抛出的纺纱筒子筒管实际上总是空的。
6.相反,所抛出的纺纱筒子筒管在留下的卷绕残余物和由此导致的继续加工方面不同。因此,卷绕过程的自动化需要确定自卷绕位置抛出的纺纱筒子的状态,以便因此能可靠掌握单独的剩余纱线或或许有的纺纱筒子筒管卷绕残余物。
7.为此,在这样的输送系统中设有筒管监测器,其探测或许余留在纺纱筒子筒管上的卷绕残余物。完全退绕的纺纱筒子、即空筒管被自动回输至纺纱机以便再次满装。而如果筒管监测器发现纺纱筒子筒管上留有卷绕残余物,则例如借助道岔如此转向相应纺纱筒子筒管的输送方向,即该纺纱筒子筒管通过副输送路径被供给筒管清洁装置。该筒管清洁装置的任务是从纺纱筒子筒管去除卷绕残余物。但因为也可能出现留在筒管上的卷绕残余物还能再用且因此可被重新供给卷绕位置的情况,故筒管监测器也说明在纺纱筒子筒管上发现的卷绕残余物是否可再用。如果是这种情况,则纺纱筒子筒管未被供给筒管清洁装置,而是再次被送至纺纱筒子准备装置,其又叼住纺纱筒子的纱线头并且在将纱线头搁置在预定
位置之后又将纺纱筒子供给一个卷绕位置。
8.这种筒管监测器例如在de102014016784a1中被公开。在纺纱筒子或纺纱筒子筒管在旁边经过时形成一个图像,据此来确定其进一步处理。为了改善残余纱线和尤其是少量纱线残余的识别,在该文献中所述的装置具备用于用光照射纺纱筒子筒管的光源,其中该光源发出集束光,并且光源光轴与纺纱筒子筒管轴线形成在2
°
至8
°
之间的角度。另外,设有用于形成数字图像的图像拍摄装置以及用于评估数字图像的评估装置,其中所述评估借助评估窗进行,评估窗的尺寸被设定为它位于纺纱筒子筒管的外轮廓内。
9.如果发现仅少量且因此不再值得退绕的卷绕残余物,则相应的纺纱筒子必须在其又能被加入纺纱过程/卷绕过程之前被完全清除,即除去其卷绕残余物并因此被输送至筒管清洁装置。这种用于从尤其立于输送件上的纺纱筒子去除纱线残余的装置例如在de4131667a1中有所描述。在此清洁过程中将工具压靠到筒管上并且平行于筒管移动。为此,滑架连带用于所谓刮钳的支座离开其上死点并且向下移动到纺纱筒子根部。在这里,刮钳闭合并且在卷绕残余物下方贴靠纺纱筒子筒管根部。卷绕残余物随后通过沿筒管可向前运动的刮除器被分离且接着被吸走。纺纱筒子或具有卷绕残余物的筒管此时垂直于盘状输送件的插装芯轴,输送件通过输送带被输送入卷绕机的筒管清洁装置区域并通过相应输送段也又被送走。
10.实际上,纺纱筒子从卷绕位置被输送至筒管监测器,并且如果发现是不再值得退绕的卷绕残余物,则随后将其输送至筒管清洁装置。在清洁之后,纺纱筒子被再次引导至筒管监测器,并且检查卷绕残余物是否已被成功去除。如果清洁成功并且在筒管上不再有卷绕残余物,则筒管被排出或又被供给纺纱机。但如果尽管进行了清洁但筒管监测器总还是确定有卷绕残余物,则纺纱筒子被再一次输送至筒管清洁装置并且执行再次清洁。当多次由筒管监测器发现筒管清洁装置未成功清洁纺纱筒子时,纺纱筒子被送至在此进行人工干预的工站。于是在这里,纺纱筒子一般从纺纱筒子和筒管输送系统被取出,以人工方式被除去卷绕残余物,又被送入循环中。
11.由于清洁的检查只发生在筒管监测器处,故被多次移动到筒管清洁装置的纺纱筒子相应需要更多时间并且加重材料流负担。因为筒管监测器典型地一般在机器一侧布置在出口区域中,而筒管清洁装置布置在供应段区域中。即,来自卷绕位置的纺纱筒子/纺纱筒子筒管被排出至卷绕机的前侧且被送至机器一侧。在这里,所述纺纱筒子/纺纱筒子筒管经过该筒管监测器。如果发现纱线残余,则纺纱筒子又被引领至设于背侧区域内的供应段,并且与卷绕残余物相关地或是被送入筒管清洁装置、或是被送入纺纱筒子准备装置。筒管清洁装置和筒管监测器的空间分隔因此决定了在所述装置之间的长距离运输。
12.这种余留在纺纱筒子上的卷绕残余物还总是滋生以下危险,纱线端头开松,有时退卷并且最后在继续输送纺纱筒子时留挂在所述机器或输送系统之上或之内的任何地方。这样的拖纬纱线不仅干扰全部材料流,最后端头也可能造成机器停止并且可能需要人工干预。
13.卷绕残余物去除装置还具有固定的清洁过程,即,刮除器总是向下一直移动到纺纱筒子根部,随后压到纺纱筒子上又向上移动以便能刮除卷绕残余物。如果卷绕残余物例如位于纺纱筒子的中央区域或上侧区域中,则需要刮除器向下移动到纺纱筒子根部并且在那里开始清洁行程。
技术实现要素:14.本发明的第一方面因此涉及一种用于识别纺纱筒子筒管上的卷绕残余物的检测装置,包括用光照亮纺纱筒子筒管的光源、用于形成纺纱筒子筒管的数字图像的图像拍摄装置以及用于评估数字图像的评估装置。
15.所提出的检测装置的特点是,它具有用于反射由光源为了照亮纺纱筒子筒管所发出的光的反光器,该评估装置设立用于完成该纺纱筒子筒管上是否有卷绕残余物以及所确定的卷绕残余物位于该纺纱筒子筒管上的哪个区域的评估,该评估装置为了转发评估结果能与控制装置相连,并且依据该评估结果,该控制装置设计用于启动基于需求的筒管清洁或纺纱筒子筒管的继续输送。
16.在检测装置中,纺纱筒子根据本发明就位于反光背景的前面,反光背景在形成纺纱筒子图像时通过照明装置被照射并且反射光。最好可以垂直于纺纱筒子布置的摄像头(camera)此时形成纺纱筒子图像。通过这种方式,可以拍摄纺纱筒子图像,并且评估装置可以确定纺纱筒子筒管的粗细。依据该数据,可以通过该评估装置不仅探测纺纱筒子筒管上是否有卷绕残余物,也探测其位于纺纱筒子筒管的何处或哪个高度。在评估之后,评估结果按照是否有卷绕残余物且如果有则是在纺纱筒子筒管的哪个区域中的意义被转发至控制装置。如果控制装置收到在纺纱筒子筒管上没有卷绕残余物的信号,则针对该纺纱筒子筒管不进行筒管清洁。但如果由控制装置收到筒管上有卷绕残余物的信号,则或是执行筒管清洁、或是将纺纱筒子输送至筒子准备装置。
17.对于启动筒管清洁的情况,控制装置也接收关于卷绕残余物位于纺纱筒子筒管上何处的信息。如果卷绕残余物至少也位于纺纱筒子筒管下侧区域中,则该机构或剥纱器移动到纺纱筒子筒管根部,在那里压到纺纱筒子筒管上并且向上移动。而如果发现布置在纺纱筒子筒管中央区域或上侧区域中的卷绕残余物,则该机构仅向下移动至其在卷绕残余物下方能压靠纺纱筒子筒管,随后它又向上移动以刮除卷绕残余物。按需筒管清洁因此按照适配于卷绕残余物的清洁的意义来理解,此时清洁行程仅被设计成像所需程度那样远。
18.通过这种方式可执行适应要求的且相应控制的清洁。通过识别卷绕残余物位于纺纱筒子上的哪个位置,可以有目的地在正确高度开始所述清洁。在初期仅在批次开始时或当采用有差别的纺纱筒子筒管时必须示教一个空纺纱筒子筒管以便能用作参考物。
19.由于依据纺纱筒子满装程度按需控制所述清洁而节省了时间,因为用于刮除卷绕残余物的机构仅向下移动能在卷绕残余物下方压靠到纺纱筒子筒管所需的程度。
20.在一个有利设计方案中,该评估装置被集成到摄像头中。
21.如果摄像头壳体也包括评估装置,则可以实现紧凑的设计。进行所形成的图像的评估,仅将评估结果转送至该控制装置,由此数据交流总体看被减少至最低程度。
22.但也可以想到,该评估装置设计成在摄像头外。在本发明的一个替代设计方案中,该评估装置被集成到该控制装置中。
23.通过将评估装置集成到控制装置中,可以放弃附加的组件。所形成的图像被转送至该控制装置并被评估。在此可以在本发明的范围内想到该控制装置通过卷绕位置计算机或中央控制装置构成。
24.该光源优选被集成到摄像头中。
25.无论评估装置是否被集成到摄像头壳体中,该光源也可以被布置在摄像头壳体
内。
26.或者该光源布置在摄像头外。
27.当光源安放在摄像头壳体外时,获得不太紧凑的设计结构。对本发明重要的是光源所发出的光能被设于纺纱筒子之后的反光器反射。
28.在一个有利设计方案中将所形成的数字图像与预定参考图像相比较。
29.如果在批次开始时或随着这种不带卷绕残余物的新纺纱筒子筒管的使用借助检测装置形成一个数字图像,则该图像被用作参考图像。即,将在生产期间的后续纺纱筒子图像与参考图像相比较,由此能确定纺纱筒子筒管粗细的偏差。在此,在所述评估中不仅能评估在待比较图像中纺纱筒子筒管是否需要比依据参考图像更多的空间,也评估当前图像在哪个区域与参考图像不同。
30.在另一替代设计方案中,依据该数字图像将获得数据与参考数据相比较。
31.除了直接比较两幅图像外,也可以依据数字图像来确定代表纺纱筒子筒管尺寸的图像数据。接着,从在生产期间各自形成的图像中将由此算出的图像数据与参考图像的图像数据相比较。因而也在此情况下不仅掌握是否有卷绕残余物位于纺纱筒子上,也掌握其位于何处。
32.最好在卷绕残余物下方开始筒管清洁。
33.因为能可靠确定卷绕残余物在纺纱筒子/纺纱筒子筒管位于哪个区域或哪个高度,故该筒管清洁装置可被控制,使得该机构刚好在满装度下方抵靠。即,该机构只需向下移动到其能在卷绕残余物下方压靠纺纱筒子筒管的程度,以便接着在其向上运动时能从筒管上刮除卷绕残余物。因为迄今在筒管清洁中并不知道卷绕残余物位于纺纱筒子上何处,在现有技术中常见的是清洁过程的固定过程,即,在每次清洁时该机构例如像刮除器一直向下移动到纺纱筒子根部并从那里尝试向上从筒管刮除卷绕残余物。
34.本发明的第二方面因此涉及一种用于从尤其立于输送盘上的纺纱筒子筒管去除卷绕残余物的筒管清洁装置,在此用于去除卷绕残余物的机构可以沿纺纱筒子筒管运动。
35.筒管清洁装置的特点是,该筒管清洁装置包括用于识别卷绕残余物的检测装置,其按照前述实施例之一来设计。
36.如果筒管清洁装置配备有根据本发明的可借此确定纺纱筒子上有卷绕残余物以及卷绕残余物位置的检测装置,则纺纱筒子的清洁可以适应于各自满装程度地被控制。
37.即,纺纱筒子被送入该筒管清洁装置,停留在那里并且位于例如如上所述地可以由带有刮钳的支座构成的机构的区域中。通过该检测装置来形成数字图像并且识别是否有卷绕残余物和卷绕残余物位于纺纱筒子筒管上何处。而如果发现纺纱筒子筒管上没有卷绕残余物或可被再次供给卷绕位置的卷绕残余物,则纺纱筒子筒管从筒管清洁装置被送走。但如果收到筒管上有不再值得退绕的卷绕残余物的信号,则启动筒管清洁。
38.在执行了筒管清洁后,当该机构到达其上死点或向上游移动经过筒管时,再次通过检测装置来创建纺纱筒子图像。如之前那样,当在筒管上不再发现卷绕残余物时,筒管被继续输送或者在识别出总还是存在的卷绕残余物时启动再次筒管清洁。因此,通过使用本发明的检测装置能在每次清洁行程之后检查清洁结果。由于该检查还发生在筒管清洁装置本身中,故清洁不成功并且还是具有卷绕残余物的纺纱筒子不一定重新被送至筒管监测器并从那里又被送至筒管清洁装置。这不仅使材料流减压,也带来时间节约,从而这样的纺纱
筒子筒管最后又更快速地被供给纺纱机。
39.进一步的优点是,不再将具有卷绕残余物的纺纱筒子从筒管清洁装置送至筒管监测器并从这里又送至筒管清洁装置,由此至少在该区域内将影响材料流且可能导致整个机器停机的拖纬纱线的危险减至最低。
40.因为也识别在筒管上的卷绕残余物位置,故还必须使卷绕残余物刮除机构仅向下游移动,直到它能在卷绕残余物下方被压到纺纱筒子上。因为毕竟也经常出现卷绕残余物位于纺纱筒子筒管的中央区域或上侧区域中,故可以通过这种方式缩短该清洁过程,从而总体提升筒管清洁装置的效率。
41.在现有技术中迄今常见的是该筒管清洁机构按照固定流程,即对于每次清洁过程首先向下移动到纺纱筒子根部以便随后向上移动以从纺纱筒子上刮掉卷绕残余物,而现在因知晓了卷绕残余物位于纺纱筒子上何处而可以按需控制每次单独清洁过程。因为也能紧跟在清洁过程之后检查清楚是否成功或卷绕残余物是否还位于纺纱筒子上,故总体上减压所述材料流并且抑制形成拖纬纱线的危险。如果尽管执行了清洁过程但还是有卷绕残余物,则马上可以开始一个新的清洁过程。
42.本发明的第三方面因此涉及一种卷绕机,其包括多个工位、用于纺纱筒子和纺纱筒子筒管的输送系统和筒管清洁装置。
43.卷绕机的特点是,至少一个筒管清洁装置根据前述实施例来设计。
44.从卷绕位置抛出的空筒管、带有少量卷绕残余物的筒管和带有更多的可再用的卷绕残余物的筒管一般共同被送出至设于机器端侧的筒管监测器。在这里,纺纱筒子筒管关于留下的卷绕残余物和由此导致的不同继续处理被拣选。带有少量且因而不再值得退绕的卷绕残余物的纺纱筒子/纺纱筒子筒管从筒管监测器起被继续送至筒管清洁装置。
45.在卷绕位置中的纺纱筒子移动时间通常与纱线量和卷绕机功率能力相关地在1分钟到3分钟之间。因此,在具有许多卷绕位置的卷绕机处,许多纺纱筒子筒管被很频繁地送至筒管监测器且进而也送至筒管清洁装置。
46.如果卷绕机具备一个如前所述的筒管清洁装置,则可以通过按需清洁过程的控制在更短时间内针对此时卷绕残余物只位于纺纱筒子根部的情况执行几个单独清洁过程,由此该筒管清洁装置可以总体上更高效工作。
47.但因为通过这种方式可以在筒管清洁装置本身中检查每个单独清洁过程是否成功,因此也减少了卷绕机或连接系统的材料流的负担。因为在清洁不成功时不必又将纺纱筒子输送至筒管监测器并从那里送至筒管清洁装置,故尤其在清洁尝试不成功时缩短能执行再次清洁尝试的时间。最后,这样的纺纱筒子能更快速地又被供给纺纱机。
48.另外有以下有利效果,即,使必须从筒管清洁装置带着卷绕残余物被送至筒管监测器并从那里又被送至筒管清洁装置的多个纺纱筒子的数量最小化。这又具有以下有利效果,在该区域中没有卷绕残余物纱线松脱、缠住并由此形成所谓的拖纬纱线(trailing ends)。这样的拖纬纱不仅不利地影响材料流动,也通常需要人工干预且甚至会造成机器停机。
49.本发明的另一方面因此涉及一种用于识别纺纱筒子筒管上的卷绕残余物的方法。
50.该方法的特点是,在第一步骤中形成纺纱筒子筒管的数字图像,在第二步骤中进行该纺纱筒子筒管上是否有卷绕残余物且所确定的卷绕残余物位于该纺纱筒子筒管的哪
个区域中的评估,并且在第三步骤中将评估结果转送至控制装置,在第四步骤中依据该评估结果启动基于需求的筒管清洁或该纺纱筒子筒管的继续输送。
51.由此能获得与此相关所描述的优点和作用。
52.在本发明的方法中,纺纱筒子在反光性背景前方被照亮并且形成数字图像。将阴影图像或透光图像与在不带卷绕残余物的纺纱筒子筒管批次开始时所形成的图像相比较。在最简单情况下,纺纱筒子筒管的厚度或直径被评估。在此,所述评估可借助图像比较或从所形成图像中获得的图像数据进行。通过这种方式,能够不仅探测纺纱筒子筒管上是否有卷绕残余物,也探测其位于纺纱筒子/纺纱筒子筒管的哪个区域。所述评估结果被转送至控制装置,其最终依据所述结果启动纺纱筒子/纺纱筒子筒管的进一步处理。即,纺纱筒子被判别是否没有卷绕残余物、有值得退绕的卷绕残余物或有不再值得退绕的卷绕残余物。如果未发现卷绕残余物,则空纺纱筒子筒管被供给环锭纺纱机。对于发现了尚有值得退绕的卷绕残余物,纺纱筒子被送至纺纱筒子准备装置,它在这里被准备好以用于在卷绕位置中的再次退绕过程。而如果在纺纱筒子上发现不再有值得退绕的卷绕残余物,则其接受筒管清洁,其中该筒管清洁装置获得在纺纱筒子筒管的哪个区域中有卷绕残余物的信息。由此允许根据针对各自卷绕残余物和其位置的需要来控制筒管清洁。通过这种方式,可以时间最佳地执行多个清洁过程,只要卷绕残余物位于纺纱筒子或纺纱筒子筒管的中间区域或上侧区域中。
附图说明
53.从以下对本发明优选实施例的说明、结合示出本发明重要细节的图和附图和权利要求书得到本发明的其它特征和优点。一些特征可以本身单独地或多个任意组合地在本发明的优选实施方式中实现。
54.以下将结合图来详述本发明的优选实施例。
55.图1以俯视示意图示出布置在卷绕机区域中的包括本发明检测装置的输送系统;和
56.图2示出用于识别卷绕残余物的本发明检测装置。
57.附图标记列表
[0058]1ꢀꢀꢀꢀ
卷绕机
[0059]2ꢀꢀꢀꢀ
卷绕位置
[0060]3ꢀꢀꢀꢀ
输送系统
[0061]4ꢀꢀꢀꢀ
纺纱筒子
[0062]5ꢀꢀꢀꢀ
输送盘
[0063]6ꢀꢀꢀꢀ
纺纱筒子筒管
[0064]7ꢀꢀꢀꢀ
供应段
[0065]8ꢀꢀꢀꢀ
准备段
[0066]9ꢀꢀꢀꢀ
准备装置
[0067]
10
ꢀꢀꢀ
连接段
[0068]
11
ꢀꢀꢀ
储蓄段
[0069]
12
ꢀꢀꢀ
横向输送段
[0070]
13
ꢀꢀꢀ
回输段
[0071]
14
ꢀꢀꢀ
筒管监测器
[0072]
15
ꢀꢀꢀ
横向通道
[0073]
16
ꢀꢀꢀ
筒管清洁器段
[0074]
17
ꢀꢀꢀ
筒管清洁装置
[0075]
18
ꢀꢀꢀ
连接段
[0076]
19
ꢀꢀꢀ
人工准备段
[0077]
20
ꢀꢀꢀ
连接部
[0078]
21
ꢀꢀꢀ
连接段
[0079]
22
ꢀꢀꢀ
连接段
[0080]
23
ꢀꢀꢀ
检测装置
[0081]
24
ꢀꢀꢀ
光源
[0082]
25
ꢀꢀꢀ
图像拍摄装置
[0083]
26
ꢀꢀꢀ
评估装置
[0084]
27
ꢀꢀꢀ
反光器
[0085]
28
ꢀꢀꢀ
控制装置
[0086]
29
ꢀꢀꢀ
轴线
[0087]
30
ꢀꢀꢀ
轴
[0088]
t
ꢀꢀꢀꢀ
输送方向
具体实施方式
[0089]
在图1中示意性示出卷绕机1的(纺纱筒子和筒管)输送系统3,其通过连接段21或22被连接至环锭纺纱机的未示出的输送系统。在工作期间,通过入口侧的连接段21,按照竖直取向安置在输送盘5上的且在一台或多台环锭纺纱机上制成的纺纱筒子4被馈入卷绕机1的输送系统3中。
[0090]
在卷绕机1的卷绕位置2上退绕的纺纱筒子筒管6的排出随后通过出口侧的连接段22进行。如图1所示的本身已知的输送系统3具备许多其它的不同输送段,许多卷绕位置2借此被供应纺纱筒子4,或者借此能排出退绕完的纺纱筒子筒管6。
[0091]
输送盘5连带纺纱筒子4首先到达位于卷绕机1背侧区域中的供应段7,从那里分支出所谓的准备段8。在准备段8区域中设置准备装置9,在准备装置上准备好所提供的纺纱筒子4以用于随后倒筒过程。
[0092]
准备好的纺纱筒子4从准备段8经由连接段10到达所谓的储蓄段11。能可逆驱动的储蓄段11将输送盘5连带准备好的纺纱筒子4又分配到多个横向输送段12之一。每个横向输送段12经过卷绕机1的众多卷绕位置2之一并且在出口侧被连接至位于卷绕机1的前侧的回输段13。
[0093]
出现以下情况,即,纺纱筒子4未被完全退绕,并且卷绕残余物留在纺纱筒子筒管6上。这例如出现在在断纱之后无法再找到纺纱筒子4上的纱线末端且未完全退绕的纺纱筒子4从卷绕位置2被放出时。
[0094]
在此实施例中,在筒管回输段13区域内设置筒管监测器14,其检查在输送盘5上提
供的纺纱筒子筒管6的满装状态。纺纱筒子4或纺纱筒子筒管6的进一步处理依据已识别的卷绕残余物进行。即,输送盘5带着完全空的纺纱筒子筒管6通过出口侧的连接段22马上又被回输至环锭纺纱机,而其纺纱筒子筒管6还具有卷绕残余物的输送盘5首先被分流到所谓横向通道15。带有尚可用的卷绕残余物的纺纱筒子筒管6通过连接部20又被供给准备装置9。准备装置9找到纱线端头并且将带有卷绕残余物的纺纱筒子4准备好用于在卷绕位置2上的继续处理。在余纱不可用时需要在筒管清洁装置17中清洁纺纱筒子4。筒管清洁装置17也被称为筒管清洁器。
[0095]
为此,带有筒管清洁器17的筒管清洁器段16被连接至横向通道15。此外,从筒管清洁器段16分支出通至供应段7的连接段18以及例如人工准备段19。显然,筒管监测器14和/或筒管清洁器段16或筒管清洁器17也可以就位在卷绕机1的输送系统3内的其它位置上,例如在供应段7区域内在卷绕机1的背面上。筒管清洁器17或筒管清洁装置本身未被详细说明,因为一方面是已知的且另一方面并非本技术的主题。筒管清洁器17在此例如可以具有如de4131667a1所述的结构。
[0096]
如图1所示,在卷绕作业期间许多输送盘5在输送系统3内总是在输送方向t上循环,输送盘装备有一个纺纱筒子4或一个纺纱筒子筒管6。前述的供应段7通常还通过连接部20直接连接至回输段13。
[0097]
图1仅示出用于识别卷绕残余物的检测装置23的壳体。图2示出检测装置23的原理性结构。如已经说明地,纺纱筒子4或纺纱筒子筒管6借助输送系统3在输送盘5上被送入检测装置23中,检测装置如图1所示可被集成到筒管清洁器17中。也可以想到检测装置23布置在筒管清洁器17之后。纺纱筒子筒管6的轴线带有附图标记29。图像拍摄装置25具有光轴30。光源24以及评估装置26在此实施例中被集成到图像拍摄装置25中,但也可以单独地或两者分开地构成。
[0098]
可设计成摄像头的图像拍摄装置25例如可以发出红外光。它具备物镜以及成像传感器并且形成纺纱筒子筒管6的数字图像。摄像头的光轴30或确切说摄像头物镜的光轴与纺纱筒子筒管6的轴线29形成直角。
[0099]
在反光器27前方形成纺纱筒子筒管6的图像。所述照明借助光源24进行并且反光背景亮起来。形成剪影图像或阴影图像。在评估装置26中,所形成的图像或由此获得的图像数据与在先所存储的图像或图像数据相比较,从而识别已有的卷绕残余物连同其在纺纱筒子筒管上的位置。
[0100]
形成唯一图像就足以检测卷绕残余物。光源24最好仅在形成图像的时刻被启用。就可能有的卷绕残余物而言的数字图像的评估借助与控制装置28相连的评估装置26进行。不同于图2所示地,光源24、评估装置26和图像拍摄装置25也能单独构成。评估装置26也可以被集成到控制装置28中。