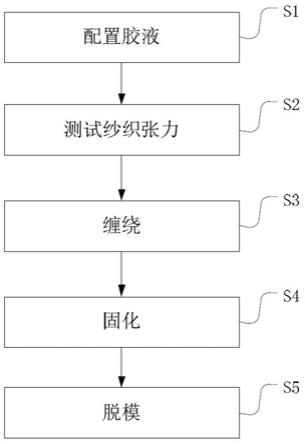
[0001]
本发明涉及一种火箭发动机壳体,特别涉及一种复合材料制火箭发动机壳体。
背景技术:[0002]
复合材料发动机壳体作为火箭发动机的推进剂储箱、燃烧室,同时还是火箭的弹体,需要承受推进剂燃烧时壳体的内压、具有适当的结构刚度、材料密度小;目前发动机壳体发展的趋势从金属材料偏向于非金属复合材料;固体火7bad0020发动机壳体要求复合材料具有高的比强度、比模量和断裂应变;火箭发动机的壳体结构质量是构成发动机消极质量的主要部分,对发动机性能影响极大,因此选用高轻质的碳纤维材料作为壳体的外壳材料,能够缠绕出受内压高、质量比低的缠绕层壳体也是大家目前需要解决的问题。目前发动机壳体主要采用金属材料,金属材料密度较高,制造出的发动机壳体重量较重,对火箭的射程、速度影响较大,并且金属发动机壳体的燃料消耗量较大,目前商业卫星需求量越来越高,因此质量轻、性能高、成本低的火箭发动机壳体需求量越来越大。
技术实现要素:[0003]
本发明的目的是提供一种大型复合材料火箭发动机壳体缠绕方法,采用碳纤维与环氧树脂树脂湿法缠绕,能承受8.5mpa的内压,最大程度地减轻发动机壳体的重量。
[0004]
本发明的目的是这样实现的:一种大型复合材料火箭发动机壳体缠绕方法,包括以下步骤:
[0005]
1)配置胶液:按照树脂、固化剂配比配置树脂,使用电动搅拌机搅拌,配置完成后静置待用;
[0006]
2)测试纱织张力:缠绕前对所用碳纤维纱进行烘干,将碳纤维纱放入烘箱烘干;将烘干后的碳纤维纱充分浸渍在上述树脂中,对浸渍过树脂的碳纤维纱进行张力测试,测量合格后进入下一步骤;
[0007]
3)缠绕:通过螺旋倾斜缠绕配合环向缠绕进行缠绕,缠绕过程中保持碳纤维纱的张力在设定范围,螺旋倾斜缠绕时,螺旋缠绕层端面距离前端头孔为:2.5
±
0.2mm,螺旋缠绕层端面距离后端头孔为:15
±
1mm,缠绕过程需刮除缠绕层表面胶液;
[0008]
4)固化:将缠绕完成后的产品送入烘箱加热,进行固化;
[0009]
5)脱模:固化过程结束后,关闭烘箱加热,待产品表面温度下降至室温后,再静置一段时间即可脱模。
[0010]
作为本发明的进一步限定,步骤1)中使用电动搅拌机搅拌3-4次,每次搅拌3-4min,转速为1000
±
50r/min,每次间隔5-6min,配置完成后静置25-35min使用。
[0011]
作为本发明的进一步限定,步骤2)烘干温度为:60℃~80℃,且保温4h。
[0012]
作为本发明的进一步限定,步骤2)中充分浸渍时,将配置好的树脂倒入胶槽,同时在教槽内设置纱梳,将碳纤维纱均匀穿过纱梳,使得碳纤维纱充分浸渍在胶槽中。
[0013]
作为本发明的进一步限定,步骤3)中刮除缠绕层表面胶液为;每间隔一端时间刮
胶一次,控制缠绕层表面没有明显胶残留,同时对刮落的胶液进行称重检测,若粘度超出设定范围0.35pa.s~1.0pa.s,则废气缠绕。
[0014]
作为本发明的进一步限定,步骤4)中固化过程具体如下:
[0015]
4-1)室温-80℃,保温2h,刮胶;升温速率25℃~30℃/h;
[0016]
4-2)80℃-95℃,保温6h;升温速率25℃~30℃/h;
[0017]
4-3)95℃-125℃,保温5h;升温速率25℃~30℃/h;
[0018]
4-4)125℃-155℃,保温8h;升温速率25℃~30℃/h;
[0019]
4-5)155℃-60℃,加热源关闭,烘箱门不开,风机开启,自然降温。
[0020]
与现有技术相比,本发明的有益效果在于:
[0021]
(1)本发明制造的壳体能承受内压8.5mpa的爆破压强,质量比同结构的金属壳体轻50%以上;
[0022]
(2)本发明制造的壳体缠绕结构的方向强度比可根据结构要求而定,可充分发挥材料的结构,各部位载荷要求的强度都与各部位材料提供的实际强度相适应,这是金属材料做不到的;
[0023]
(3)本发明的纤维缠绕结构工艺简单、制造周期短、成本低。
附图说明
[0024]
图1为本发明工作流程图。
[0025]
图2为本发明中浸渍示意图。
具体实施方式
[0026]
实施例1
[0027]
如图1所示一种大型复合材料火箭发动机壳体缠绕方法,包括以下步骤:
[0028]
s1)配置胶液:按照树脂、固化剂配比配置树脂,使用电动搅拌机搅拌3次,每次搅拌3min,转速为1000r/min,每次间隔5min,配置完成后静置25min使用;
[0029]
s2)测试纱织张力:缠绕前对所用碳纤维纱4进行烘干,烘干温度为:60℃℃,且保温4h,将碳纤维纱4放入烘箱烘干;如图2所示,将烘干后的碳纤维纱4充分浸渍在上述树脂2中,充分浸渍时,将配置好的树脂2倒入胶槽1,同时在教槽内设置纱梳3,将碳纤维纱4均匀穿过纱梳3,使得碳纤维纱4充分浸渍在胶槽1中,对浸渍过树脂2的碳纤维纱4进行张力测试,测量合格后进入下一步骤;
[0030]
s3)缠绕:通过螺旋倾斜缠绕配合环向缠绕进行缠绕,缠绕过程中保持碳纤维纱的张力在设定范围,螺旋倾斜缠绕时,螺旋缠绕层端面距离前端头孔为:2.5mm,螺旋缠绕层端面距离后端头孔为:15mm,缠绕过程需刮除缠绕层表面胶液,每间隔一端时间刮胶一次,控制缠绕层表面没有明显胶残留,同时对刮落的胶液进行称重检测,若粘度超出设定范围0.35pa.s~1.0pa.s,则废气缠绕;
[0031]
s4)固化:将缠绕完成后的产品送入烘箱加热,进行固化,具体如下:
[0032]
s401)室温-80℃(即从室温升至80℃),而后保温2h,刮胶;升温速率25℃/h;
[0033]
s402)80℃-95℃,保温6h;升温速率25℃/h;
[0034]
s403)95℃-125℃,保温5h;升温速率25℃/h;
[0035]
s404)125℃-155℃,保温8h;升温速率25℃/h;
[0036]
s405)155℃-60℃,加热源关闭,烘箱门不开,风机开启,自然降温;
[0037]
s5)脱模:固化过程结束后,关闭烘箱加热,待产品表面温度下降至室温后,再静置一段时间即可脱模。
[0038]
实施例2
[0039]
如图1所示一种大型复合材料火箭发动机壳体缠绕方法,包括以下步骤:
[0040]
s1)配置胶液:按照树脂、固化剂配比配置树脂,使用电动搅拌机搅拌4次,每次搅拌4min,转速为1000r/min,每次间隔5min,配置完成后静置35min使用;
[0041]
s2)测试纱织张力:缠绕前对所用碳纤维纱4进行烘干,烘干温度为:80℃,且保温4h,将碳纤维纱4放入烘箱烘干;如图2所示,将烘干后的碳纤维纱4充分浸渍在上述树脂2中,充分浸渍时,将配置好的树脂2倒入胶槽1,同时在教槽内设置纱梳3,将碳纤维纱4均匀穿过纱梳3,使得碳纤维纱4充分浸渍在胶槽1中,对浸渍过树脂2的碳纤维纱4进行张力测试,测量合格后进入下一步骤;
[0042]
s3)缠绕:通过螺旋倾斜缠绕配合环向缠绕进行缠绕,缠绕过程中保持碳纤维纱的张力在设定范围,螺旋倾斜缠绕时,螺旋缠绕层端面距离前端头孔为:2.5mm,螺旋缠绕层端面距离后端头孔为:15mm,缠绕过程需刮除缠绕层表面胶液,每间隔一端时间刮胶一次,控制缠绕层表面没有明显胶残留,同时对刮落的胶液进行称重检测,若粘度超出设定范围0.35pa.s~1.0pa.s,则废气缠绕;
[0043]
s4)固化:将缠绕完成后的产品送入烘箱加热,进行固化,具体如下:
[0044]
s401)室温-80℃(即从室温升至80℃),而后保温2h,刮胶;升温速率30℃/h;
[0045]
s402)80℃-95℃,保温6h;升温速率30℃/h;
[0046]
s403)95℃-125℃,保温5h;升温速率30℃/h;
[0047]
s404)125℃-155℃,保温8h;升温速率30℃/h;
[0048]
s405)155℃-60℃,加热源关闭,烘箱门不开,风机开启,自然降温;
[0049]
s5)脱模:固化过程结束后,关闭烘箱加热,待产品表面温度下降至室温后,再静置一段时间即可脱模。
[0050]
下面结合具体设计过程以及模拟计算对本发明做进一步说明。
[0051]
1.1技术指标
[0052]
燃烧室最大工作压强p
max
:6.1mpa。
[0053]
最大爆破压强:9.1mpa。
[0054]
发动机壳体外径d
out
:φ2200mm。
[0055]
1.2选材方案
[0056]
固体火箭发动机壳体要求复合材料具有高的比强度、比模量和断裂应变;考虑碳纤维的力学性能、材料来源的广泛性及价格因素,前后接头和前后裙采用t700s-12k/tde-85热熔法环氧树脂体系,即增强材料为t700碳纤维,基体材料为tde-85环氧树脂;壳体采用碳纤维t700s-12k缠绕,树脂采用环氧树脂tde-85。
[0057]
t700s-12k/tde-85复合材料单向板力学性能
[0058][0059][0060]
t700-12k碳纤维复丝的性能指标
[0061][0062]
1.3纤维缠绕设计计算
[0063]
对于长径比较大的壳体来说,采用平面缠绕时前后封头位置会出现严重的纤维堆积现象,所以筒身段的缠绕均采用螺旋方向缠绕加环向缠绕的方式。
[0064]
螺旋方向缠绕角α的计算公式:
[0065]
α=sin-1
(d0/d
out
)
ꢀꢀ
(1)
[0066]
其中,d0为两端封头极孔平均直径,d
out
为发动机壳体直径;
[0067]
螺旋向纤维缠绕厚度h
α
及环向纤维缠绕厚度h
θ
计算公式:
[0068]
[0069]
式中:k
safe
:纤维强度安全系数;k
s
:螺旋缠绕应力平衡系数,对碳纤维一般取为0.75。
[0070]
复合壳体的筒身段厚度h
g
的计算公式:
[0071][0072]
式中:v
f
:纤维体积含量;
[0073]
壳体缠绕层数的计算公式:
[0074][0075]
式中:h为螺旋向或环向的厚度,b为纱片的宽度,取8mm,m为纤维团数,取为2团;
[0076]
考虑发动机工作时内压的作用,当发动机壳体承载较大的外载荷时,因此在对壳体质量的计算中,取纤维缠绕筒身段的壁厚9.52mm得到。
[0077]
1.4纤维缠绕圆筒段爆破压强计算
[0078]
纤维缠绕壳体封头是在圆筒纵向缠绕过程中成型的,由于封头形状及开头等诸多因素的影响,由圆筒纵向缠绕决定的封头壁厚往往不能满足内压强度要求,需要增加纵向纤维厚度;在这种情况下,圆筒爆破往往在环向发生,因此爆破压强估算公式为:
[0079][0080]
式中:h
f
为纤维层总厚度,为h
f
=h
α
+h
θ
[0081]
纤维缠绕段的理想状态下按壁厚9.52mm进行估算纤维层厚度,将相关数据带入上式,可得设计方案的爆破压强及安全系数;计算结果表明纤维缠绕段的安全系数均达到1.3以上,能满足使用要求。
[0082]
本发明并不局限于上述实施例,在本发明公开的技术方案的基础上,本领域的技术人员根据所公开的技术内容,不需要创造性的劳动就可以对其中的一些技术特征作出一些替换和变形,这些替换和变形均在本发明的保护范围内。