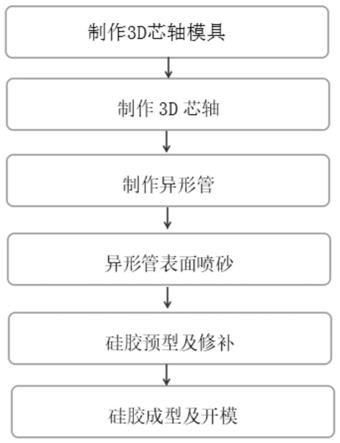
1.本发明涉及一种成型工艺,具体涉及一种使用随形的3d芯轴作为支撑制作连续纤维薄壁管件,并在其表面二次加热成型硅胶的复合材料薄壁异形管表面成型硅胶的成型工艺。
背景技术:2.复合材料产品表面成型硅胶的常用工艺为模压,但是在模压成型复合材料薄壁异形管件的过程中,薄壁中空的管件可能因为较大的外压而开裂,影响产品的密封性能,甚至造成产品报废,影响产品的成品率,或是在管壁内部产生裂痕,影响产品质量,而异型管件往往造型复杂,用传统的芯轴难以取出,往往都是分两半式在模具内铺贴成型,这样做出的异形管纤维不连续强度较差不能承受二次模压成型硅胶的压力。
技术实现要素:3.针对上述问题,本发明的主要目的在于提供一种使用随形的3d芯轴作为支撑制作连续纤维薄壁管件,并在其表面二次加热成型硅胶的复合材料薄壁异形管表面成型硅胶的成型工艺。
4.本发明是通过下述技术方案来解决上述技术问题的:一种复合材料薄壁异形管表面成型硅胶的成型工艺,所述成型工艺包括如下步骤:
5.步骤1:依据异形管内壁三维模型图,整体内缩一定尺寸得到3d芯模模型图,并加工木质芯模;
6.步骤2:制作3d芯轴,选用面密度100
‑
200g/
㎡
的玻璃纤维预浸布,在木质芯模表面铺贴两至三层玻璃纤维预浸布,然后在表面包裹一层耐高温的保鲜膜进行隔离,然后再缠绕bopp塑料带,最后放入烘箱中加热固化成型,将固化后的玻璃纤维壳体从木质芯模上取下来得到薄壁3d芯轴;
7.步骤3:首先在3d芯轴内部放置耐高温的风管,然后在该3d芯轴表面连续铺贴碳纤维预浸料,将铺贴完成后的预型体放入模具,加热加压固化成型获得强度较高的异形管;
8.步骤4:对碳纤维复合材料薄壁异形管表面待成型硅胶的区域进行喷砂处理,使用清洗剂或酒精擦洗处理后晾干;
9.步骤5:将硅胶成型模具上模和硅胶成型模具下模预热至30
‑
40℃;
10.步骤6:在硅胶成型模具上模和硅胶成型模具下模的型腔内分别铺贴生硅胶,然后在异形管硅胶成型区域外表面包裹一层保鲜膜,然后将步骤4中得到的异形管放入硅胶成型模具下模中,最后将硅胶成型模具上模与硅胶成型模具下模合模,待多余的硅胶沿着合模面挤出后,沿模具面削去多余的生硅胶片;
11.步骤7:将步骤6中包含了异形管的模具放入硫化机进行预热压,使硅胶与硅胶成型模具上下模充分贴合但是不至于固化;
12.步骤8:开模,取出异形管,去除表面包裹的保鲜膜,检查硅胶成型模具内硅胶形状
是否饱满,在有缺失部位进行生硅胶补贴,然后再次将异形管放入硅胶成型下模内,最后合上硅胶成型上模;
13.步骤9:将模具置于硫化机进行高温热压处理,使得硅胶固化成型,然后转移至冷却栈板上冷却;
14.步骤10:开模,清理边缘残留的硅胶。
15.在本发明的具体实施例子中:步骤2中固化成型温度控制在130℃—150℃,外压通过bopp带受热收缩提供压力,固化时间控制在40
‑
50min。
16.在本发明的具体实施例子中:步骤3中固化成型需要温度控制在130℃—150℃,外压控制在1
‑
1.5mpa,固化时间控制在40
‑
50min。
17.在本发明的具体实施例子中:步骤7中控制硫化机加温50
‑
80℃、加压1
‑
1.5mpa预型,热压时间不超过1分钟。
18.在本发明的具体实施例子中:步骤9中固化成型需要加热温度控制在130
‑
160℃,加压3
‑
4mpa,保温时间控制在10
‑
20分钟。
19.本发明的积极进步效果在于:本发明提供的复合材料薄壁异形管表面成型硅胶的成型工艺,使用随形的3d芯轴制作的连续纤维异形管,能够承受二次加热模压成型表面硅胶的外压,该工艺有如下优点:
20.1、使用玻纤制作的随形3d芯轴,使得造型复杂的异形管件也可以进行连续铺贴预浸料,比传统的分半式铺贴搭接获得的异形管强度要好很多。
21.2、用随形3d芯轴制作的异形管能够承受二次模压成型表面硅胶的压力,降低了报废率。
附图说明
22.图1为复合材料薄壁异型管表面硅胶成型工艺的流程图。
23.图2
‑
1为复合材料薄壁异型管表面硅胶成型模具的示意图的主视图。
24.图2
‑
2为复合材料薄壁异型管表面硅胶成型模具的示意图的俯视图(不含硅胶成型模具上模)。
25.图2
‑
3为本发明中的硅胶成型模具上模的立体图。
26.图2
‑
4为本发明中的硅胶成型模具下模的立体图。
27.图2
‑
5为本发明中的复合材料薄壁异型管表面硅胶成型模具的立体图。
28.下面是本发明中标号对应的名称:
29.硅胶成型模具上模1,3d芯轴2,硅胶成型模具下模3。
具体实施方式
30.下面结合附图给出本发明较佳实施例,以详细说明本发明的技术方案。
31.图1为复合材料薄壁异型管表面硅胶成型工艺的流程图,如图1所示:本发明提供的复合材料薄壁异形管表面成压硅胶的成型工艺,该成型工艺包括如下步骤:
32.步骤1:依据异形管内壁三维模型图,整体内缩一定尺寸(一般可以选0.2mm)得到3d芯模模型图,并加工木质芯模。
33.步骤2:制作3d芯轴2,选用面密度100
‑
200g/
㎡
的玻璃纤维预浸布,在木质芯模表
面铺贴两至三层玻璃纤维预浸布,然后在表面包裹一层耐高温的保鲜膜进行隔离,然后再缠绕bopp塑料带,最后放入烘箱中加热固化成型,将固化后的玻璃纤维壳体从木质芯模上取下来得到薄壁3d芯轴2。
34.步骤3:首先在3d芯轴2内部放置耐高温的风管,然后在该3d芯轴表面连续铺贴碳纤维预浸料,将铺贴完成后的预型体放入模具,加热加压固化成型获得强度较高的异形管。
35.步骤4:对碳纤维复合材料薄壁异形管表面待成型硅胶的区域进行喷砂处理,使用清洗剂或酒精擦洗处理后晾干。
36.步骤5:将硅胶成型模具上模1和硅胶成型模具下模3预热至30
‑
40℃。
37.步骤6:在硅胶成型模具上模1(如图2
‑
1、图2
‑
3、图2
‑
5)和硅胶成型模具下模3(如图2
‑
1、图2
‑
2、图2
‑
4、图2
‑
5)的型腔内分别铺贴生硅胶,然后在异形管硅胶成型区域外表面包裹一层保鲜膜,然后将步骤4中得到的异形管放入硅胶成型下模中,最后将硅胶成型上模与下模合模,待多余的硅胶沿着合模面挤出后,沿模具面削去多余的生硅胶片。
38.步骤7:将步骤6中包含了异形管的模具放入硫化机进行预热压,控制硫化机加温50
‑
80℃、加压1
‑
1.5mpa预型,热压时间不超过1分钟,使硅胶与硅胶成型模具上下模充分贴合但是不至于固化。
39.步骤8:开模,取出异形管,去除表面包裹的保鲜膜,检查硅胶成型模具内硅胶形状是否饱满,在有缺失部位进行生硅胶补贴,然后再次将异形管放入硅胶成型下模内,最后合上硅胶成型上模。
40.步骤9:将模具置于硫化机进行高温热压处理,使得硅胶固化成型,然后转移至冷却栈板上冷却。
41.步骤10:开模,清理边缘残留的硅胶。
42.在本发明中,第一次开合模为预热,目的是使硅胶产生一定的流动性,起塑型作用;第二次开合模为固化过程,使得硅胶固化。
43.在本发明的具体实施例子中:步骤2中固化成型温度控制在130℃—150℃,外压通过bopp带受热收缩提供压力,固化时间控制在40
‑
50min。
44.在本发明的具体实施例子中:步骤3中固化成型需要温度控制在130℃—150℃,外压控制在1
‑
1.5mpa,固化时间控制在40
‑
50min。
45.下面是具体的实施例子:
46.实施例一:
47.步骤1:依据异形管三维图复制提取异形管内壁三维模型图,然后将内壁模型图整体内缩0.2mm得到3d芯模模型图,按照该模型图加工木质芯模;
48.步骤2:制作3d芯轴,选用面密度100g/
㎡
的玻璃纤维预浸布,在木质芯模表面铺贴2层玻璃纤维预浸布,然后在表面包裹一层耐高温的保鲜膜进行隔离,然后再缠绕bopp塑料带,最后放入烘箱中加热固化成型,固化温度150℃、固化时间40min。将固化后的玻璃纤维壳体从木质芯模上取下来得到薄壁3d芯轴;
49.步骤3:首先在3d芯轴内部放置耐高温的风管,然后在该3d芯轴表面连续铺贴碳纤维预浸料,将铺贴完成后的预型体放入模具,加热加压固化成型,固化温度150℃、固化时间40min。获得强度较高的异形管;
50.步骤4:对碳纤维复合材料薄壁异形管表面待成型硅胶的区域进行喷砂处理,使用
清洗剂或酒精擦洗处理后晾干;
51.步骤5:将硅胶成型模具上模和硅胶成型模具下模预热至30℃。
52.步骤6:在硅胶成型模具上模1和硅胶成型模具下模3的型腔内分别铺贴生硅胶,然后在异形管硅胶成型区域外表面包裹一层保鲜膜,然后将步骤4中得到的异形管放入硅胶成型下模中,最后将硅胶成型上模与下模合模,待多余的硅胶沿着合模面挤出后,沿模具面削去多余的生硅胶片;
53.步骤7:将模具放入硫化机,控制硫化机加温80℃、加压1.2mpa预型,保温控制时间45s,使硅胶与硅胶成型模具上下模充分贴合但是不至于固化;
54.步骤8:开模,取出异形管,去除表面包裹的保鲜膜,检查硅胶成型模具内硅胶形状是否饱满,若有缺失部位需要补贴少量生硅胶,然后再次将异形管放入硅胶成型下模内,最后合上硅胶成型上模。
55.步骤9:将模具置于硫化机上,加热145℃、加压3.4mpa,保温13分钟,使得硅胶固化成型,然后转移至冷却栈板上冷却;
56.步骤10:开模,清理边缘残留的硅胶。
57.实施例二:
58.步骤1:依据异形管三维图复制提取异形管内壁三维模型图,然后将内壁模型图整体内缩0.1mm得到3d芯模模型图,按照该模型图加工木质芯模;
59.步骤2:制作3d芯轴,选用面密度200g/
㎡
的玻璃纤维预浸布,在木质芯模表面铺贴2层玻璃纤维预浸布,然后在表面包裹一层耐高温的保鲜膜进行隔离,然后再缠绕bopp塑料带,最后放入烘箱中加热固化成型,固化温度135℃、固化时间45min。将固化后的玻璃纤维壳体从木质芯模上取下来得到薄壁3d芯轴;
60.步骤3:首先在3d芯轴内部放置耐高温的风管,然后在该3d芯轴表面连续铺贴碳纤维预浸料,将铺贴完成后的预型体放入模具,加热加压固化成型,固化温度135℃、固化时间45min。获得强度较高的碳纤维复合材料异形管;
61.步骤4:对碳纤维复合材料异形管表面待成型硅胶的区域进行喷砂处理,使用清洗剂或酒精擦洗处理后晾干;
62.步骤5:将硅胶成型模具上模和硅胶成型模具下模预热至40℃。
63.步骤6:在硅胶成型模具上模1和硅胶成型模具下模3的型腔内分别铺贴生硅胶,然后在异形管硅胶成型区域外表面包裹一层保鲜膜,然后将步骤4中得到的异形管放入硅胶成型下模中,最后将硅胶成型上模与下模合模,待多余的硅胶沿着合模面挤出后,沿模具面削去多余的生硅胶片;
64.步骤7:合模,在硫化机上加热、加压预型,硫化机温度设定为75℃,压力设定为1.2mpa,保温控制时间60s;使硅胶与成型模具上下模充分贴合;
65.步骤8:开模,取出异形管,去除表面包裹的保鲜膜,检查硅胶成型模具内硅胶形状是否饱满,若有缺失部位需要补贴少量生硅胶,然后再次将异形管放入硅胶成型下模内,最后合上硅胶成型上模。
66.步骤9:将模具置于硫化机上,加热、加压固化,硫化机温度设定为130℃,压力设定为3mpa,成型时间设定为15min,然后转移至冷却栈板上,冷却至模具表面温度低于45℃;
67.步骤10:开模,清理边缘残留的硅胶。
68.本发明的实施例1中,各段固化温度高,保温时间缩短,有利于批量生产过程中缩短工时,降低成本。
69.本发明的实施例2中,固化温度偏低、保温时间相对延长,产品表面质量相对更高。
70.两个实施例所表述的各项数据均在相关材料的可实施参数范围内,可根据实际情况进行调控。
71.本发明制作的产品和现有技术制作的产品相比:
72.1、使用玻纤制作的随形3d芯轴,相比传统的分半式铺贴、合模线处料片搭接处理,搭接处拉伸及压缩强度为树脂粘接强度,在20mpa左右。本发明可在造型复杂的异形管件进行预浸料连续铺贴,合模线处拉伸及压缩强度为连续纤维增强复合材料的强度,在600mpa左右,有效的提高了合模线处的强度。
73.2、用随形3d芯轴制作的异形管能够承受二次模压成型表面硅胶的压力,降低了报废率,二次模压成型表面硅胶的报废率由原来的95%降低至0%。
74.以上显示和描述了本发明的基本原理和主要特征和本发明的优点。本行业的技术人员应该了解,本发明不受上述实施例的限制,上述实施例和说明书中描述的只是说明本发明的原理,在不脱离本发明精神和范围的前提下,本发明还会有各种变化和改进,这些变化和改进都落入要求保护的本发明范围内,本发明要求保护范围由所附的权利要求书及其等效物界定。