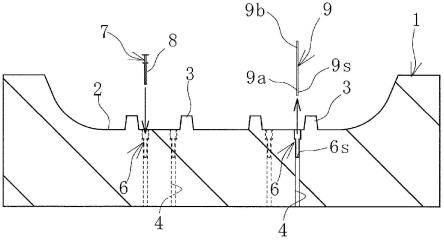
1.本发明涉及轮胎硫化用模具的制造方法及维护方法,更详细而言,涉及能够将排气单元(英文:vent unit)高精度且高效地设置于轮胎硫化用模具的轮胎成形面的预定位置的轮胎硫化用模具的制造方法及能够高效地进行排气单元的维护的维护方法。
背景技术:2.已知为了将生胎与轮胎成形面之间的不需要的空气等向模具外部排出,而向在轮胎成形面开口的排气孔设置排气单元(例如,参照专利文献1)。为了将该排气单元设置于模具,在轮胎成形面的预定位置形成排气孔后,将排气单元从轮胎成形面的开口压入并固定于该排气孔。
3.排气孔通过钻孔等形成,但为了在轮胎成形面的预定位置高精度地形成为目标规格,需要高精度的加工技术。因此,为了形成多个排气孔而需要相当的工夫。将排气单元定位于排气孔也要求高精度。而且,由于模具由铝等硬度比较低的材质形成,因此,即使排气孔形成于预定位置,如果不准确地进行排气单元的安装,则也会在排气单元的设置位置产生偏移。因此,为了将排气单元高精度且高效地设置于轮胎成形面的预定位置,存在改善的余地。
4.通过反复使用模具,污垢会附着于排气单元,因此需要进行除去污垢等维护作业。例如,为了除去污垢,提出了将清洗单元移动控制到排气孔的位置的方法(参照专利文献2)。在专利文献2中,作为预先存储的排气孔的位置,提出了使用轮胎成形面的cad数据(第0025段),但无法保证在cad数据中的排气孔的位置高精度地设置排气孔。另外,提出了将包含排气孔的位置的成形面的预先存储的形状信息、与由检测单元得到的成形面的形状进行比较并利用控制单元计算排气孔的位置的方案,但不清楚如何能够以比较的结果高精度地掌握排气孔的位置。而且,每当清洗排气孔时,利用检测单元检测排气孔的位置需要很多时间。因此,为了高效地进行排气单元的维护,存在改善的余地。
5.现有技术文献
6.专利文献
7.专利文献1:日本特开2017-13312号公报
8.专利文献2:日本特开2017-128013号公报
技术实现要素:9.发明所要解决的课题
10.本发明的目的在于,提供能够高效且高精度地将排气单元设置于轮胎硫化用模具的预定位置的轮胎硫化用模具的制造方法及能够高效地进行排气单元的维护的维护方法。
11.用于解决课题的手段
12.为了达成上述目的,本发明的轮胎硫化用模具的制造方法制造具有与制造的轮胎表面相同的表面形状的主模,接着制造转印了所述主模的表面的橡胶模,接着制造转印了
所述橡胶模的表面的石膏铸模,接着铸造转印了所述石膏铸模的表面的模具,在该模具的轮胎成形面的预定位置设置排气单元,所述制造方法的特征在于,使定位构件的顶端部突出设置于所述主模的表面的相当于所述预定位置的安装位置,使用该主模制造所述橡胶模,由此利用所述顶端部在所述橡胶模形成定位孔,并成为使所述顶端部埋设于所述定位孔并使所述定位构件的后端部从所述橡胶模的表面突出的状态,使用该橡胶模制造所述石膏铸模,由此成为使所述后端部埋设于所述石膏铸模并使所述顶端部从所述石膏铸模的表面突出的状态,将构成排气单元的壳体以能够装卸的方式固定于所述顶端部,使用该石膏铸模铸造所述硫化用模具,由此将所述壳体铸入并固定于所述硫化用模具,将构成排气单元的阀芯插入并安装于取下了所述定位构件的所述壳体,由此将所述排气单元设置于所述轮胎成形面。
13.本发明的轮胎硫化用模具的维护方法是对设置于通过上述的轮胎硫化用模具的制造方法制造出的所述轮胎硫化用模具的所述排气单元进行维护的轮胎硫化用模具的维护方法,其特征在于,将所述主模中的所述安装位置的位置数据存储于存储部,在对所述排气单元进行维护时,基于存储于所述存储部的所述安装位置的位置数据,使维护机构的头移动。
14.发明效果
15.根据本发明的轮胎硫化用模具的制造方法,在制造轮胎硫化用模具的工序的最初阶段,使定位构件的顶端部突出设置于所述主模的表面的相当于所述预定位置的安装位置,通过利用该定位构件,能够将构成排气单元的壳体铸入到所述硫化用模具并高精度地固定于所述预定位置。并且,通过将阀芯插入并安装于取下了以能够装卸的方式固定于所述后端部的所述定位构件的所述壳体,能够以不需要大量的工时的方式,将所述排气单元高精度地设置于所述轮胎成形面的所述预定位置。
16.根据本发明的轮胎硫化用模具的维护方法,存储于所述存储部的所述安装位置的位置数据表示与所述轮胎硫化用模具中的固定所述排气单元的所述预定位置的位置数据相同的位置。因此,在对所述排气单元进行维护时,基于存储于所述存储部的所述安装位置的位置数据,使维护机构的头移动,由此能够将该头定位于设置有所述排气单元的所述预定位置。伴随于此,每当维护时,能够以不进行检测排气单元的位置等工序的方式迅速地使头移动到设置有排气单元的位置来进行所需的维护作业。
附图说明
17.图1是以俯视例示通过本发明制造出的轮胎硫化用模具的说明图。
18.图2是以剖视例示图1的模具的说明图。
19.图3是图2的局部放大图。
20.图4是以剖视例示主模的说明图。
21.图5是以剖视例示制造橡胶模的工序的说明图。
22.图6是以剖视例示使制造出的橡胶模从主模分离的状态的说明图。
23.图7是以剖视例示制造石膏铸模的工序的说明图。
24.图8是以剖视例示使制造出的石膏铸模从橡胶模分离的状态的说明图。
25.图9是以剖视例示铸造模具的工序的说明图。
26.图10是以剖视例示铸造出的模具的说明图。
27.图11是以俯视例示阀芯的安装机构及排气单元的维护机构的说明图。
28.图12是以剖视例示安装阀芯的工序的说明图。
29.图13是以剖视例示清洗排气单元的工序的说明图。
具体实施方式
30.以下,基于附图所示的实施方式对本发明的轮胎硫化用模具的制造方法及维护方法进行说明。
31.通过本发明的轮胎硫化用模具的制造方法,制造图1~图3所例示的轮胎硫化用模具1(以下,称为模具1)。该模具1是组合型(英文:sectional type)模具的扇形模具。在轮胎成形面2突出设置有各种各样的槽成形部3。
32.在模具1形成有用于将生胎的硫化时产生的不需要的气体等向模具1的外部排出而防止硫化故障的排气孔4,排气孔4的一端在轮胎成形面2的预定位置pm开口。在排气孔4设置有排气单元5。即,在轮胎成形面2的预定位置pm设置有排气单元5。
33.如图3所例示,排气单元5具有壳体6和内设于壳体6的阀芯7及弹簧8。壳体6是筒状体,阀芯7具有轴部7a和固定于轴部7a的顶端的扩径部7b。阀芯7由外插于轴部7a的弹簧8始终向壳体6的一侧的开口施力。扩径部7b从轮胎成形面2稍微突出,在扩径部7b位于这样使排气孔4开口的位置时,模具1的内部和外部通过排气孔4连通。在生胎的硫化时,阀芯7由生胎按压,抵抗弹簧8的作用力而后退。并且,在扩径部7b位于封锁排气孔4的一端的开口的位置时,通过排气孔4的模具1的内部与外部的连通被切断。
34.为了制造该模具1,首先,制造图4所例示的主模11。主模11具有与制造的轮胎的轮胎表面相同的表面形状。在主模11的表面中的安装位置pc埋设定位构件9的后端部9b,使顶端部9a从表面突出地设置。该安装位置pc是与在模具1中设置排气单元5的预定位置pm相当的位置。
35.定位构件9例如是棒状体,能够使用不锈钢、铁、铝、铝合金等金属或各种各样的树脂等来制造。在定位构件9的至少顶端部9a形成有螺纹部9s。可以遍及定位构件9的全长地形成螺纹部9s。
36.接着,如图5~图6所例示,使用该主模11制造转印了主模11的表面的橡胶模12。因此,如图5所例示,将主模11的表面作为上侧而配置在模框10a中。在模框10a的上方配置支撑板12a,使支撑板12a的表面与主模11的表面成为相对的状态。向相对的支撑板12a的表面与主模11的表面之间的空间流入并填充橡胶材料r。当填充的橡胶材料r固化时,制造出转印了主模11的表面的橡胶模12。
37.如图6所示,制造出的橡胶模12与主模11分离。在制造出的橡胶模12的表面,利用顶端部9a形成定位孔9h。定位构件9保持立起设置在主模11的表面的状态。
38.接着,如图7~图8所例示,制造转印了橡胶模12的表面的石膏铸模13。因此,在制造出的橡胶模12,安装从主模11取下了的定位构件9。具体而言,使顶端部9a埋设于定位孔9h且使后端部9b成为从橡胶模12的表面突出的状态。
39.然后,将橡胶模12在使支撑板12a紧贴于背面的状态下配置于模框10b中。向该橡胶模12的表面流入石膏p。当流入的石膏p固化时,制造出转印了橡胶模12的表面的石膏铸
模13。
40.如图8所例示,制造出的石膏铸模13从橡胶模12分离。在该石膏铸模13埋设有定位构件9的后端部9b,顶端部9a成为从石膏铸模13的表面突出的状态。
41.接着,如图9~图10所例示,铸造转印了石膏铸模13的表面的模具1。于是,将壳体6以能够装卸的方式固定于从石膏铸模13的表面突出的顶端部9a。即,使定位构件9的螺纹部9s与壳体6的螺纹部6s螺纹接合而将壳体6以能够装卸的方式固定于定位构件9。
42.将该石膏铸模13的表面作为上侧而配置在模框10c中。然后,向石膏铸模13的表面流入例如铝材料等熔融金属m。当流入的熔融金属m固化时,铸造出转印了石膏铸模13的表面的模具1。在熔融金属m固化之后,使模具1从石膏铸模13分离。
43.壳体6铸入并固定于模具1。铸造出的模具1的表面成为轮胎成形面2,在轮胎成形面2形成槽成形部3。由于在壳体6固定有定位构件9,因此,解除螺纹部6s、9s彼此的螺纹接合,如图10所例示那样将定位构件9从壳体6取下。之后,将弹簧8与阀芯7一起插入并安装于取下了定位构件9的壳体6。此外,在适当的定时,从模具1的背面侧通过钻孔加工等形成与壳体6的内部连通的排气孔4。
44.如上所述,在制造模具1的工序的最初阶段,使定位构件9的顶端部9a突出设置于主模11的表面的相当于预定位置pm的安装位置pc,通过利用该定位构件9,能够将壳体6铸入于模具1并高精度地固定于预定位置pm。并且,在从铸入到模具1的壳体6取下定位构件9之后,通过将阀芯7插入并安装于该壳体6,从而不需要大量的工时,就能够将排气单元5高精度地设置于轮胎成形面2的预定位置pm。
45.在该实施方式中,由于在壳体6和定位构件9具有相互螺纹接合的螺纹部6s、9s,因此,在图9所例示的工序中,能够容易地将壳体6以能够装卸的方式固定于定位构件9。另外,在图10所例示的工序中,能够容易地将定位构件9从壳体6取下。
46.对模具1安装阀芯7及弹簧8的工序也能够通过手动作业来进行,但也可以如图11、图12所例示那样使用安装机构14a来进行。安装机构14a具有载置所铸造的模具1的基台15、机械臂16、头17以及控制装置18。机械臂16由多个臂部旋转自如地连结而构成。在机械臂16的顶端部安装有头17。作为控制装置18,使用了计算机。控制装置18具有存储部18a。在存储部18a中存储有主模11中的安装位置pc的位置数据、主模11的形状数据。机械臂16的动作由控制装置18控制。在该实施方式中,作为头17,使用对外插有弹簧8的阀芯7进行把持的把持头。
47.在基台15设置有用于将模具1的基准点及朝向按照目标进行对位而载置模具1的引导件15a。例如,与模具1的角的侧面抵接的l型突起被用作引导件15a。通过这样将模具1载置于基台15,从而存储于存储部18a的主模11中的安装位置pc的位置数据的坐标轴与基台15上的模具1的坐标轴一致。
48.之后,如图12所例示,基于存储于存储部18a的安装位置pc的位置数据使头17移动。该安装位置pc的位置数据表示在模具1中设置有各个壳体6的位置,因此,通过这样经由机械臂16控制头17的动作,能够使头17高精度地移动到设置有各个壳体6的模具1的预定位置pm。并且,通过在移动到的预定位置pm处使头17朝向壳体6接近移动,从而将阀芯7及弹簧8插入并安装于壳体6。由此,完成图1~图3所例示的排气单元5设置于轮胎成形面2的预定位置的模具1。
49.当反复使用模具1对生胎进行硫化时,污垢x会附着于排气单元5。当附着的污垢x的堆积量变多时,由排气单元5进行的排气有可能无法正常发挥功能而发生硫化故障。因此,需要适时除去附着于排气单元5的污垢x的清洗作业。
50.因此,如图11、图13所例示,使用维护机构14b对模具1进行维护作业。该维护机构14b是仅更换了前述的安装机构14a的头17的机构。在本实施方式中,作为头17,使用除去附着于排气单元5的污垢x的清洗头。
51.在对排气单元5进行维护时,如上所述,使存储于存储部18a的主模11中的安装位置pc的位置数据的坐标轴与基台15上的模具1的坐标轴一致,将模具1载置于基台15。之后,如图13所例示,基于存储于存储部18a的安装位置pc的位置数据使头17移动。
52.该安装位置pc的位置数据表示在模具1中设置有各个壳体6(排气单元5)的位置,因此,通过这样经由机械臂16控制头17的动作,能够使头17高精度地移动到设置有各个壳体6(排气单元5)的模具1的预定位置pm。然后,在移动到的预定位置pm处利用头17对排气单元5进行除去污垢x的处理。
53.例如,从移动到排气单元5的稍靠上方位置的头17向排气单元5照射激光,除去附着于扩径部7b的表面及其周边、扩径部7b与轮胎成形面2的间隙等的污垢x。或者,从头17照射等离子体,喷射压缩流体而除去污垢x。此外,能够使用除去污垢x的各种各样的公知的头17。每当维护排气单元5时,能够以不进行检测排气单元5的位置等工序的方式迅速地使头17移动到排气单元5的位置来进行所需的维护作业。
54.作为维护作业,除了除去污垢x之外,还能够进行更换阀芯7及弹簧8的作业。在进行该作业时,例如,作为头17使用卡挂或刺入于扩径部7b的拔取头,将弹簧8与阀芯7一起从壳体6拔取。然后,使用把持头作为头17,将新的阀芯7及弹簧8插入到该壳体6来进行更换。
55.本发明并不限定于组合型的模具,也能够适用于所谓的二分割型的模具。另外,本发明不限于用于制造充气轮胎的模具,能够适用于用于制造其他各种类型的轮胎的模具。
56.附图标记说明
57.1 模具
58.2 轮胎成形面
59.3 槽成形部
60.4 排气孔
61.5 排气单元
62.6 壳体
63.6s 螺纹部
64.7 阀芯
65.7a 轴部
66.7b 扩径部
67.8 弹簧
68.9 定位构件
69.9a 顶端部
70.9b 后端部
71.9s 螺纹部
72.9h 定位孔
73.10a、10b、10c 模框
74.11 主模
75.12 橡胶模
76.12a 支撑板
77.13 石膏铸模
78.14a 安装机构
79.14b 维护机构
80.15 基台
81.16 臂
82.17 头
83.18 控制装置
84.18a 存储部
85.m 熔融金属
86.p 石膏
87.r 橡胶材料
88.x 污垢