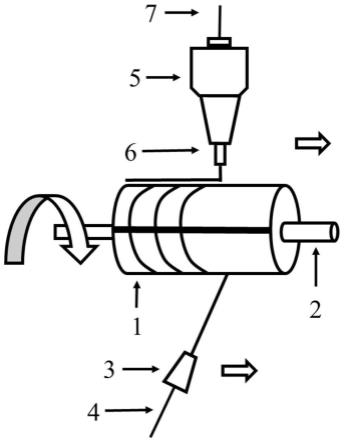
基于缠绕与3d打印技术的复合材料轻质夹心结构成型方法
技术领域
1.本发明属于连续纤维增强复合材料夹心结构制造技术领域,尤其涉及一种基于缠绕与3d打印技术的复合材料轻质夹心结构成型方法。
背景技术:2.连续纤维增强复合材料轻质夹心结构被广泛应用于航空航天、先进兵器、海洋船舶等领域,发挥了缓冲、吸能、隔振的重要作用,其减重效果显著、但其形状复杂。然而,采用现有模压、注塑等成型工艺在保证连续纤维增强复合材料轻质夹心结构内壁纤维连续性的同时,成型效率与材料利用率却不高。尽管采用现有模压、注塑等成型工艺制备的复合材料轻质夹心结构具有优异的力学性能,若能将其抗拉性能、吸能性能和缓冲性能作进一步优化则对连续纤维增强复合材料夹心结构的开发应用具有非常重要的意义。
技术实现要素:3.针对背景技术中存在的问题,本发明目的之一在于提供一种成型效率和材料利用率高的基于缠绕与3d打印技术的复合材料轻质夹心结构成型方法。
4.为实现前述目的,本发明采用如下技术方案。
5.一种基于缠绕与3d打印技术的复合材料轻质夹心结构成型方法,步骤包括:步骤1,将芯模安装到回转主轴上;步骤2,控制主轴转动,控制缠绕出丝嘴运动使连续纤维增强树脂基预浸料均匀缠绕到芯模上,成型出等厚度的复合材料第1内层结构;步骤3,控制主轴固定,驱动3d打印设备的喷嘴沿着芯模往复轴向运动,以在所述第1内层结构表面打印成型等截面的支撑肋,完成一条支撑肋的打印后,控制主轴旋转预设角度后再打印下一条支撑肋,完成所述第1内层结构表面所有支撑肋的打印后,对打印好的支撑肋进行固化处理,得第1层复合结构;步骤4,继续控制主轴转动,控制缠绕出丝嘴运动使连续纤维增强树脂基预浸料均匀缠绕到第1层复合结构上,成型出等厚度的复合材料第2内层结构;步骤5,参照步骤3,在所述第2内层结构表面继续打印支撑肋,得第2层复合结构;步骤6,按照设计的支撑肋位置与截面形状,参照步骤2和步骤3进行操作,直到完成所有缠绕工序、所有支撑肋的打印和固化处理,得复合材料轻质夹心结构;步骤7,从芯模上取出所得复合材料轻质夹心结构,对其整体再次进行固化处理,结束后分切成符合要求的产品。
6.作为优选方案,所述芯模采用截面为圆形、三角形、正方形、规则六边形等多边形的柱状芯模,模具采用石膏、石墨以及可拆卸金属等形式。
7.作为优选方案,所述连续纤维增强树脂基预浸料采用碳纤维、玻璃纤维、玄武岩纤维、凯夫拉纤维中的一种或多种组合。
8.作为优选方案,所述连续纤维增强树脂基预浸料的树脂材料采用pe-聚乙烯类、
pp-聚丙烯类、pvc-聚氯乙烯类、ps-聚苯乙烯类、pa-聚酰胺类、pom-聚甲醛类、pc-聚碳酸酯类、聚苯醚类、聚砜类中的一种或多种混合。
9.作为优选方案,步骤3中,固化处理的方式采用冷风固化、热风固化或紫外线固化;步骤7中,固化处理的方式采用热压罐固化、冷风固化、热风固化、紫外线固化一种或多种组合。
10.作为优选方案,利用连续纤维增强树脂基预浸料缠绕的内层结构径向截面呈圆形和/或矩形和/或椭圆形。
11.作为优选方案,相应步骤中,主轴转动的速度为10-500rad/min。
12.为进一步提高复合材料轻质夹心结构的抗拉性能、吸能性能和缓冲性能,缠绕连续纤维增强树脂基预浸料的方法采用环向缠绕和/或螺旋缠绕。
13.为更进一步提高复合材料轻质夹心结构的抗拉性能、吸能性能和缓冲性能,在每次完成同一内层结构表面所有支撑肋的打印后,先围绕该内层结构表面所有支撑肋根部环向缠绕或螺旋缠绕连续纤维增强树脂基预浸料,然后对打印好的支撑肋进行固化处理。
14.有益效果:本发明具有工序步骤简单、工艺流程短、可操作性强等优点;本方法成型结构壁面复合材料孔隙率小于3%,可有效提高轻质夹心结构内部纤维的连续性,提升制件的一致性;传统注塑工艺成型结构尺寸φ200
×
50的轻质夹层结构时间在1h以上,且需要设计复杂流道的金属模具,本发明成型时间小于30min,模具结构简单,成型效率提高50%以上;同时相比于模压方法(先成型整体轮廓,而后去除材料成型多孔结构),本方法材料利用率可达95%以上,相比之下提高30%以上;而且,采用本发明制备的复合材料轻质夹心结构,具有优异的性能,其抗拉性能能够达到1200mpa以上,结构有效抗冲击能300j以上,结构轴向承载力40kn以上。
附图说明
15.图1为实施例中3d打印与缠绕复合成型设备工作布局示意图;图2为实施例1中复合材料轻质夹心结构制备过程示意图;图3为实施例2中复合材料轻质夹心结构制备过程示意图;图4为实施例3中复合材料轻质夹心结构制备过程中的局部示意图;图5为实施例1中复合材料轻质夹心结构立体图;图6为实施例2中复合材料轻质夹心结构立体图。
具体实施方式
16.下面结合附图对本发明作进一步说明。实施例1
17.一种基于缠绕与3d打印技术的复合材料轻质夹心结构成型方法,用于制备轴向、径向截面均呈矩形的复合材料轻质夹心结构,具体制备过程如下并结合图1和图2所示:步骤11,设计安装矩形截面的芯模1,将芯模1安装到回转主轴2上;步骤12,控制主轴2以25rad/min的速度转动,采用环向缠绕方法,通过缠绕出丝嘴3运动将连续碳纤维增强聚醚醚酮树脂预浸料4(碳纤维-聚醚醚酮复合材料,属于市售产品,丝径为1mm)均匀缠绕到芯模1上,成型出第一层10mm厚的复合材料壳体结构101(即成型
出等厚度的复合材料第1内层结构),如图2中的第1幅小图所示;步骤13,控制主轴2固定,控制3d打印设备5的喷嘴6沿着芯模1轴向运动,采用往返轨迹逐层打印,沉积3d打印用连续碳纤维增强聚醚醚酮树脂基预浸料7,在主轴2中线处打印成型等截面的支撑肋,完成一条支撑肋的打印后,控制主轴旋转90
°
,打印下一条支撑肋,逐步实现支撑肋在复合材料壳体101四个壁面的均布打印,完成支撑肋的打印后,采用先加热130℃并保温15min的固化方法固化打印好的支撑肋102,得第1层复合结构(由复合材料壳体结构101和支撑肋102构成的整体),如图2中的第2幅小图所示;步骤14,控制主轴2以22rad/min的速度转动,控制缠绕出丝嘴3运动使连续纤维增强聚醚醚酮树脂预浸料均匀缠绕到第1层复合结构上,成型出等厚度的复合材料第2内层结构,具体是采用横向缠绕方法,将连续碳纤维增强聚醚醚酮树脂预浸丝跨越缠绕在打印完成的支撑肋102上,缠绕成型出12mm厚的复合材料壳体结构103,如图2中的第3幅小图所示;步骤15,控制主轴2固定,调整3d打印设备5与缠绕出丝嘴3的姿态,控制3d打印设备5的喷嘴6沿着芯模1轴向运动,采用往返轨迹逐层打印,沉积3d打印用预浸料7,继续在主轴2中线出打印成型等截面的支撑肋,完成一条支撑肋的打印后,控制主轴旋转90
°
,打印下一条支撑肋,逐步实现支撑肋在复合材料壳体四个壁面的均布打印,完成该壁面所有支撑肋的打印后,采用先加热130℃保温8min的固化方法固化打印的支撑肋104,如图2中的第4幅小图所示;步骤16,控制主轴2以28rad/min的速度转动,采用缠绕方法,将预浸料跨越缠绕打印完成的支撑肋104,缠绕成型出等厚度(10mm厚)的复合材料壳体结构105(即成型出等厚度的复合材料第3内层结构),如图2中的第5幅小图所示;步骤17,控制轴2固定,调整3d打印设备5与缠绕出丝嘴3的姿态,控制3d打印设备5的喷嘴6沿着芯模1轴向运动,采用往返轨迹逐层打印,沉积3d打印用预浸料7,在主轴中线及两侧处打印成型等截面的支撑肋,完成一侧支撑肋的打印后,主轴旋转30-60
°
,打印下一侧支撑肋,逐步实现支撑肋在复合材料壳体四个壁面的均布打印,完成该壁面支撑肋的打印后,采用先加热140℃保温6min的固化方法固化打印的支撑肋106,如图2中的第6幅小图所示;步骤18,控制主轴2以10rad/min的速度转动,采用缠绕方法,将连续纤维预浸料跨越缠绕打印完成的支撑肋106,缠绕成型10mm厚的复合材料壳体结构107(即成型出等厚度的复合材料第4层结构),如图2中的第7幅小图所示;步骤19,按照设计的支撑肋位置与截面形状,调整3d打印设备5与缠绕出丝嘴3的姿态,多次重复打印与缠绕动作,完成支撑肋的打印、固化与复合材料壳体结构的制造;步骤20,将制作完成的复合材料轻质夹心结构整体放入热压罐中,在100℃氛围下保温40min进行二次固化,然后取出芯模1;或者:取出芯模1后将复合材料轻质夹心结构整体放入热压罐中,在100℃氛围下保温10min进行二次固化;步骤21,将所得复合材料轻质夹心结构采用水刀切割成所需宽度的轻质复合材料夹心结构108,其实物结构见图5所示。实施例2
18.一种基于缠绕与3d打印技术的复合材料轻质夹心结构成型方法,用于制备径向截面呈圆形的复合材料轻质夹心结构,具体制备过程如下并结合图1和图3所示:
步骤101,设计安装圆形截面的芯模1,将芯模1安装到回转主轴2上;步骤102,控制主轴2以35rad/min的速度转动,采用环向缠绕方法,通过缠绕出丝嘴3运动将连续玻璃纤维增强聚丙烯树脂预浸料4均匀缠绕到芯模1上,成型出第一层15mm厚的复合材料壳体结构201(即成型出等厚度的复合材料第1内层结构),如图3中的第1幅小图所示;步骤103,控制主轴2固定,控制3d打印设备5的喷嘴6沿着芯模1轴向运动,采用往返轨迹逐层打印,沉积3d打印用连续玄武岩纤维增强树脂基预浸料7,在主轴2中线处打印成型等截面的支撑肋,完成一条支撑肋的打印后,控制主轴旋转180
°
,打印下一条支撑肋,逐步实现支撑肋在复合材料壳体201表面的均布打印,完成支撑肋的打印后,采用先加热150℃并保温20min的固化方法固化打印好的支撑肋202,得第1层复合结构(由复合材料壳体结构201和支撑肋202构成的整体),如图3中的第2幅小图所示;步骤104,控制主轴2以30rad/min的速度转动,控制缠绕出丝嘴3运动使连续纤维增强树脂基预浸料均匀缠绕到第1层复合结构上,成型出等厚度的复合材料第2内层结构,具体是采用横向缠绕方法,将连续纤维预浸料跨越缠绕在打印完成的支撑肋202上,缠绕成型出15mm厚的复合材料壳体结构203,如图3中的第3幅小图所示;步骤105,控制主轴2固定,控制3d打印设备5的喷嘴6沿着芯模1轴向运动,采用往返轨迹逐层打印,沉积3d打印连续纤维增强树脂基预浸料7,继续在主轴2中线出打印成型等截面的支撑肋,完成一条支撑肋的打印后,控制主轴旋转180
°
,打印下一条支撑肋,逐步实现支撑肋在复合材料壳体表面的均布打印,完成支撑肋的打印后,采用先加热120℃保温10min的固化方法固化打印的支撑肋204,如图3中的第4幅小图所示;步骤106,控制主轴2以35rad/min的速度转动,采用缠绕方法,将连续纤维预浸料跨越缠绕打印完成的支撑肋204,缠绕成型出等厚度(12mm厚)的复合材料壳体结构205(即成型出等厚度的复合材料第3内层结构),如图3中的第5幅小图所示;步骤107,控制主轴2固定,调整3d打印设备5与缠绕出丝嘴3的姿态,控制3d打印设备5的喷嘴6沿着芯模1轴向运动,采用往返轨迹逐层打印,沉积3d打印用连续纤维增强树脂基预浸料7,在主轴2中线及两侧处打印成型等截面的支撑肋,完成一侧支撑肋的打印后,主轴旋转120-180
°
,打印下一侧支撑肋,逐步实现支撑肋在复合材料壳体表面的均布打印,完成支撑肋的打印后,采用先加热150℃保温8min的固化方法固化打印的支撑肋206,如图3中的第6幅小图所示;步骤108,控制主轴2以30rad/min的速度转动,采用缠绕方法,将连续纤维预浸料跨越缠绕打印完成的支撑肋206,缠绕成型15mm厚的复合材料壳体结构207(即成型出等厚度的复合材料第4层结构),如图3中的第7幅小图所示;步骤109,按照设计的支撑肋位置与截面形状,调整3d打印设备5与缠绕出丝嘴3的姿态,多次重复前述打印与缠绕动作,完成支撑肋的打印、固化与复合材料壳体结构的制造;步骤110,将制作完成的复合材料轻质夹心结构整体放入热压罐中,在200℃氛围下保温30min进行二次固化,然后取出芯模1;或者:取出芯模1后将复合材料轻质夹心结构整体放入热压罐中,在200℃氛围下保温10min进行二次固化;步骤111,将所得复合材料轻质夹心结构采用水刀切割成所需宽度的轻质复合材
料夹心结构208,其实物结构见图6所示。实施例3
18.一种基于缠绕与3d打印技术的复合材料轻质夹心结构成型方法,用于制备径向截面呈椭圆形的复合材料轻质夹心结构,具体制备过程如下:步骤211,设计安装椭圆形截面的芯模1,将芯模1安装到回转主轴2上;步骤212,控制主轴2以50rad/min的速度转动,采用环向缠绕方法,通过缠绕出丝嘴3运动将连续纤维增强树脂基预浸料4(碳纤维/聚醚酮酮复合材料)均匀缠绕到芯模1上,成型出第一层20mm厚的复合材料壳体结构301(即成型出等厚度的复合材料第1内层结构),参照图4中的第1幅小图所示;步骤213,控制主轴2固定,控制3d打印设备5的喷嘴6沿着芯模1轴向运动,采用往返轨迹逐层打印,沉积3d打印用连续纤维增强树脂基预浸料7(凯夫拉纤维/聚醚酮酮复合材料),在主轴2中线处打印成型等截面的支撑肋,完成一条支撑肋的打印后,控制主轴旋转180
°
,打印下一条支撑肋,逐步实现支撑肋在复合材料壳体301表面的均布打印,完成支撑肋的打印后,然后围绕第1内层结构表面所有支撑肋根部分别环向缠绕连续纤维增强树脂基预浸料,第1内层结构表面每个支撑肋采用同一根纤维料进行环向缠绕,每个支撑肋根部环向缠绕成型出最大量为5mm厚的连续纤维增强树脂基预浸料(如图4中第2幅小图所示),并采用先加热200℃并保温20min的固化方法固化打印好的支撑肋302,得第1层复合结构(由复合材料壳体结构301和支撑肋302构成的整体),参照图4中的第2幅小图所示;步骤214,控制主轴2以50rad/min的速度转动,控制缠绕出丝嘴3运动使连续纤维增强树脂基预浸料均匀缠绕到第1层复合结构上,成型出等厚度的复合材料第2内层结构,具体是采用横向缠绕方法,将连续纤维预浸料跨越缠绕在打印完成的支撑肋302上,缠绕成型出15mm厚的复合材料壳体结构303,参照图4中的第3幅小图所示;步骤215,控制主轴2固定,控制3d打印设备5的喷嘴6沿着芯模1轴向运动,采用往返轨迹逐层打印,沉积3d打印连续纤维增强树脂基预浸料7,继续在主轴2中线出打印成型等截面的支撑肋,完成一条支撑肋的打印后,控制主轴旋转180
°
,打印下一条支撑肋,逐步实现支撑肋在复合材料壳体表面的均布打印,完成支撑肋的打印后,然后围绕第2内层结构表面所有支撑肋根部分别环向缠绕连续纤维增强树脂基预浸料,每个支撑肋根部环向缠绕成型出最大量为5mm厚的连续纤维增强树脂基预浸料,并采用先加热150℃保温5min的固化方法固化打印的支撑肋304,参照图4中的第4幅小图所示;步骤216,控制主轴2以50rad/min的速度转动,采用缠绕方法,将连续纤维预浸料跨越缠绕打印完成的支撑肋304,缠绕成型出等厚度(15mm厚)的复合材料壳体结构(即成型出等厚度的复合材料第3内层结构),参照图4中的第4幅小图所示;步骤217,按照设计的支撑肋位置与截面形状,调整3d打印设备5与缠绕出丝嘴3的姿态,多次重复前述打印与缠绕动作,完成支撑肋的打印、固化与复合材料壳体结构的制造;步骤218,将制作完成的复合材料轻质夹心结构整体放入热压罐中,在250℃氛围下保温15min进行二次固化,然后取出芯模1;或者:取出芯模1后将复合材料轻质夹心结构整体放入热压罐中,在250℃氛围下保温15min进行二次固化;步骤219,将所得复合材料轻质夹心结构采用水刀切割成所需宽度的轻质复合材
料夹心结构。实施例4
19.一种基于缠绕与3d打印技术的复合材料轻质夹心结构成型方法,参照实施例3,其与实施例3的主要区别在于:在复合材料的同一层结构上,先采用3d打印方法打印完成支撑肋结构,随后围绕所有支撑肋根部螺旋缠绕连续纤维增强树脂基预浸料,每个支撑肋根部环向缠绕成型出最大量为8mm厚的连续纤维增强树脂基预浸料。对比实施例1
20.采用传统的注塑成型工艺制备出与实施例1中同规格(各轮廓尺寸相同)的复合材料轻质夹心结构,其材质全部为碳纤维-聚醚醚酮复合材料。对比实施例2
21.采用传统的热模压成型工艺制备出与实施例2中同规格(各轮廓尺寸相同)的复合材料轻质夹心结构,其材质全部为玻璃纤维增强聚丙烯复合材料。
22.对各实施例和对比实施例中制备复合材料轻质夹心结构的成型效率和材料利用率进行统计,结果见表1。表1复合材料轻质夹心结构的成型效率和材料利用率
23.对各实施例和对比实施例中制备复合材料轻质夹心结构的性能进行检测,结果见表2。表2复合材料轻质夹心结构的性能