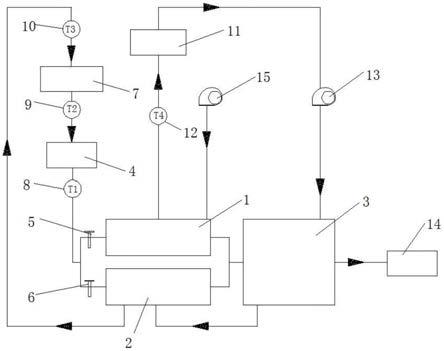
1.本实用新型涉及废气治理技术领域,具体涉及一种用于转轮吸脱附的催化焚烧控制系统。
背景技术:2.挥发性有机废气(简称vocs)是石油化工企业特征大气污染物,是指在20℃条件下蒸汽压大于或等于0.01kpa,或者特定适用条件下具有相应挥发性的有机化合物的统称。vocs是石油化工、轻工、塑料、印刷、涂料等行业排放的常见污染物。有机废气中常含有烃类化合物,含氧有机化合物,含氮、硫、卤素及含磷有机化合物等。这些废气如果不加处理,直接排入大气将会对环境造成严重污染。
3.常规的催化焚烧系统由换热器、催化床、转轮、电加热器、脱附电加热器和催化床组成,其中换热器一般是催化焚烧后的高温烟气先加热脱附废气,然后再加热浓缩废气,这种设计的缺点是:(1)需要脱附电加热器:此设计时无法保证脱附气温度达到要求,需要增加脱附电加热器;(2)换热面积大:因在设计过程中未考虑“高位能高用,低位能低用”,使整个设计过程中对数平均温差小,从而造成换热面积过大;(3)在保证同样的换热量时,换热器的阻力大:因设计过程对数平均温差小,所以回程数变多,换热器的阻力变大;(4)脱附气温度不稳定,影响转轮的使用寿命。
技术实现要素:4.实用新型目的:本实用新型目的是提供一种用于转轮吸脱附的催化焚烧控制系统,解决了常规的催化焚烧系统中换热器一般是催化焚烧后的高温烟气先加热脱附废气,然后再加热浓缩废气,导致需要脱附电加热器,且脱附气温度不稳定,影响转轮使用寿命的问题。
5.技术方案:本实用新型一种用于转轮吸脱附的催化焚烧控制系统,包括并联设置的第一气体板式换热器和第二气体板式换热器,所述第一气体板式换热器和第二气体板式换热器的烟气出口均通过管道与第三气体板式换热器的烟气进口相连接,第一气体板式换热器和第二气体板式换热器的烟气进口均通过管道与催化床的排气口相连接,所述催化床的进气口通过管道与电加热器的出风口相连接,所述电加热器的进风口通过管道与第二气体板式换热器的冷侧出口相连接,所述第二气体板式换热器的冷侧入口与第三气体板式换热器的冷侧出口相连接,所述第一气体板式换热器的冷侧出口通过管道与转轮相连接,所述转轮通过管道与第三气体板式换热器的冷侧入口相连接,所述第三气体板式换热器的烟气出口通过管道与烟囱相连接。
6.进一步的,所述第一气体板式换热器的冷侧入口通过管道与第一风机相连接。
7.进一步的,所述转轮与第三气体板式换热器冷侧入口之间的管道上安装有第二风机。
8.进一步的,与催化床的排气口相连接的管道上安装有第一热电偶。
9.进一步的,所述电加热器的出风口与催化床的进气口之间的管道上安装有第二热电偶。
10.进一步的,与电加热器的进风口相连接的管道上安装有第三热电偶。
11.进一步的,所述第一气体板式换热器的冷侧出口与转轮之间的管道上安装有第四热电偶。
12.进一步的,与第一气体板式换热器烟气进口相连接的管道上安装有第一电动风阀;与第二气体板式换热器烟气进口相连接的管道上安装有第二电动风阀。
13.有益效果:与现有技术相比,本实用新型显著的效果如下:
14.(1)无需设置脱附电加热器:可通过控制第一电动风阀来控制进入第一气体板式换热器的烟气量,当第四热电偶温度过高时,可通过调节第一电动风阀和第二电动风阀使进入第一气体板式换热器的烟气量减少,增加进入第二气体板式换热器的烟气量,保证脱附气温度,也不浪费热量;当第四热电偶温度过低时,可通过调节第一电动风阀和第二电动风阀使进入第一气体板式换热器的烟气量增加,减少进入第二气体板式换热器的烟气量,从而增强第一气体板式换热器换热,保证脱附气温度;
15.(2)换热面积小:采用“高位能高用,低位能低用”的原则,先用高温烟气同时加热脱附气和废气,再用降温后的烟气去加热刚进入第三气体板式换热器温度比较低的废气,使得整个换热系统换热过程更容易,从而增大了对数平均温,减少了换热面积;
16.(3)通过控制第一电动风阀精确控制脱附气温度,防止脱附气超温,从而保证了转轮的使用效果,同时也延长了转轮的使用寿命;同时对换热的内部优化设计,在保证脱附气的温度时,将热量转移给废气,故烟气排放温度低。
附图说明
17.图1为本实用新型主视图。
具体实施方式
18.下面结合附图和实施例对本实用新型做进一步描述:
19.如图1所示,本实用新型一种用于转轮吸脱附的催化焚烧控制系统,包括并联设置的第一气体板式换热器1和第二气体板式换热器2,第一气体板式换热器1和第二气体板式换热器2的烟气出口均通过管道与第三气体板式换热器3的烟气进口相连接,第一气体板式换热器1和第二气体板式换热器2的烟气进口均通过管道与催化床4的排气口相连接,与第一气体板式换热器1烟气进口相连接的管道上安装有第一电动风阀5;与第二气体板式换热器2烟气进口相连接的管道上安装有第二电动风阀6;可通过调节第一电动风阀5和第二电动风阀6使进入第一气体板式换热器1的烟气量和进入第二气体板式换热器2的烟气量进行变化;
20.催化床4的进气口通过管道与电加热器7的出风口相连接,与催化床4的排气口相连接的管道上安装有第一热电偶8,电加热器7的出风口与催化床4的进气口之间的管道上安装有第二热电偶9;电加热器7的进风口通过管道与第二气体板式换热器2的冷侧出口相连接,与电加热器7的进风口相连接的管道上安装有第三热电偶10,第二气体板式换热器2的冷侧入口与第三气体板式换热器3的冷侧出口相连接,第一气体板式换热器1的冷侧出口
通过管道与转轮11相连接,第一气体板式换热器1的冷侧入口通过管道与第一风机15相连接,第一风机15将脱附气鼓入第一气体板式换热器1中换热,第一气体板式换热器1的冷侧出口与转轮11之间的管道上安装有第四热电偶12,转轮11通过管道与第三气体板式换热器3的冷侧入口相连接,转轮11与第三气体板式换热器3冷侧入口之间的管道上安装有第二风机13,第三气体板式换热器3的烟气出口通过管道与烟囱14相连接;
21.本实用新型根据“高位能高用、低位能低用”的设计原则,将一股热介质加热两股冷介质的换热原理设计为三个气体板式换热器内部集成,首先通过高温烟气同时加热脱附气和废气,再用降温后的烟气去加热刚进入第三气体板式换热器3温度比较低的废气,充分利用烟气的热能,使得整个换热系统换热过程更容易;同时利用热电偶对气体板式换热器的冷热流体介质温度进行监控,使得内部换热更加优化,从而增大了对数平均温,保证在总交换热量不变情况下减少了换热面积;
22.通过控制第一电动风阀5和第二电动风阀6来控制进入第一气体板式换热器1和第二气体板式换热器2的烟气量,当第四热电偶12温度过高时,可通过调节第一电动风阀5和第二电动风阀6使进入第一气体板式换热器1的烟气量减少,增加进入第二气体板式换热器2的烟气量,保证脱附气温度,也不浪费热量;当第四热电偶12温度过低时,可通过调节第一电动风阀5和第二电动风阀6使进入第一气体板式换热器1的烟气量增加,减少进入第二气体板式换热器2的烟气量,从而增强第一气体板式换热器1换热,保证脱附气温度,保证了热量的合理利用,同时延长了转轮的使用寿命;
23.工作过程为:浓缩废气催化后形成的高温烟气先进入第一气体板式换热器1和第二气体板式换热器2,同时与加热到一定温度后的浓缩废气和脱附气进行热交换,交换后温度较低的烟气在第三气体板式换热器3中与从转轮11出来的浓缩废气换热,然后烟气排入烟囱14;预热后的脱附气首先进入转轮11将吸附在转轮11上的voc脱附出来,从而形成浓缩废气,浓缩废气经过第二风机13进入第三气体板式换热器3换热,接着进入第二气体板式换热器2换热,当第三热电偶10检测到浓缩废气温度不够达到起燃温度时,电加热器7开始,使得经过电加热之后的浓缩废气温度达到起燃温度,然后进入催化床4催化燃烧,而第二热电偶9检测到电加热之后的浓缩废气温度过高可降低电加热器7频率,使系统能耗降低,浓缩废气催化后形成的高温烟气再进入第一气体板式换热器1和第二气体板式换热器2中,从而形成循环工作。
24.相对于现有工艺,可达到节约换热面积和减小阻力的效果,参考一般工况,以6000nm3/h处理量,高温烟气入口温度380℃,脱附气入口温度100℃,出口温度200℃,浓缩废气进口温度60℃,考虑排烟温度120℃,即废气加热到215℃来设计,本实用新型与传统工艺(先加热脱附气再加浓缩废气)相比较结果如表1所示:
25.表1本实用新型与传统工艺相比较结果
[0026][0027]
由上表可知,本实用新型可节省换热面积13.7%,阻力换失10.9%,大幅减少了设备制造成本和运行成本,存在如此大差距的主要原因是将低对数平均温差换热段(
△
tm<60℃)的热负荷从348kw减少到112kw,将高对数平均温差换热段(
△
tm>90℃)的热负荷从225kw增加到461kw,实现了“高位能高用、低位能低用”,特别利用夹点技术优化了整个换热,阻止了跨越夹点的传热,并减少了整个系统的回程数,大大减小了阻力损失。
[0028]
本实用新型降低了整个换热过程的负荷,减少了换热面积,减少了过程的阻力损失,节约了占地面积,并延长了转轮的使用寿命,从而达到了降低设备制作和运行成本的目的。