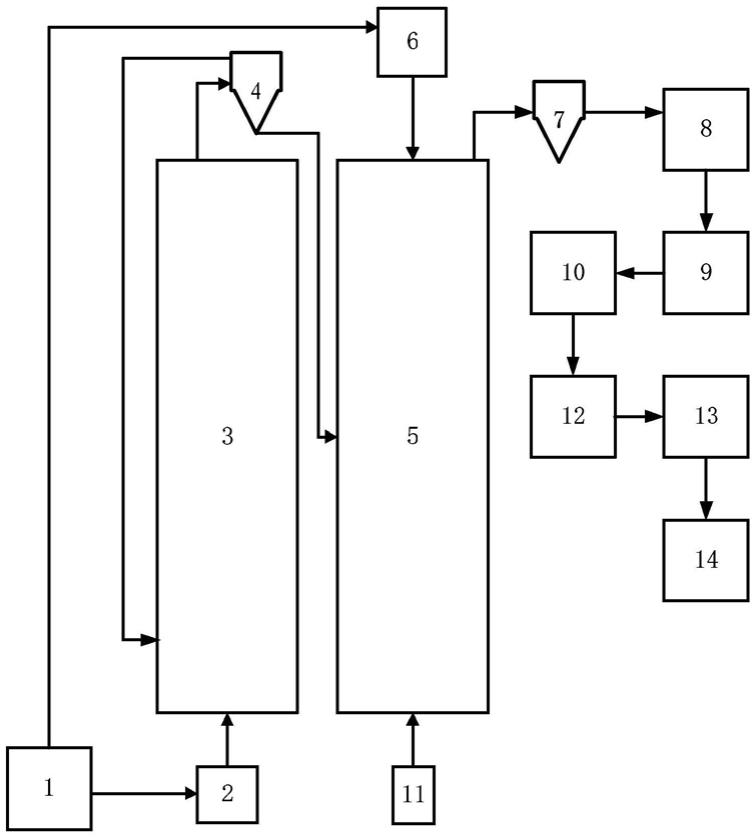
1.本发明涉及废弃物处理技术领域,尤其涉及一种流化床富氧燃烧与移动床热解气化的耦合设备及方法。
背景技术:2.农林废弃物作为碳中性的环境友好型可再生能源,具有产量大、种类多和分布广等特点,如能高效利用农林废弃物,将有效助力成功实现双碳目标。农林废弃物种类繁多,其化学组成与物理结构也差异巨大,性质的不同也导致其适用用途迥异,例如高挥发分农林废弃物适用于燃烧,低挥发分农林废弃物适用于生产生物质炭。此外不同的工艺设备也适用于不同的农林废弃物,例如移动床适用于颗粒较大、空隙度较高、堆积后床层压降较低的农林废弃物,而流化床则适用于颗粒小、易流化农林废弃物。如果采用单一工艺或设备去处理多种农林废弃物,不仅造成物料的浪费,同时可能影响整个工艺的稳定运行,直接或间接造成了资源浪费,导致了环境污染。
3.专利cn1377826提供了一种垃圾焚烧炉耦合生物质活化炉制备生物质活性炭的方法,其核心是利用垃圾焚烧炉产生的高温,达到活化所需温度,利用焚烧炉尾气作为活化所需的氧化剂,活化炉尾气返回垃圾焚烧炉再次燃烧。但该技术存在的问题是首先垃圾在空气中焚烧,容易出现焚烧不完全现象,其工艺的尾气中污染含有大量污染物,用垃圾焚烧尾气去做气化对气化设备腐蚀严重,同时垃圾焚烧的尾气中co2含量较低,需要添加催化剂活化,活化效果不佳。其次是后续使用卧式活化炉,无法实现物料的连续进样,生产效率较低。然后是活化过程仅仅利用了焚烧过程产生的尾气携带的热量作为气体热载体,存在整体能量利用率低,同时活化时间长的问题。最后是项目需要同时处理垃圾和生物质,对于同一个工艺场地,同时堆积两种来源的原料需要场地大,不利于技术落地。专利cn113187571提供了一种生物质纯氧燃烧发电系统及方法,利用谷电制氢,消除了弃风、弃光、弃水等能源生产中的浪费,降低了氢能生产过程中的碳排放,降低了纯氧燃烧的成本,实了现生物质能的利用和碳的负排放,固废草木灰还可肥田利用,一举数得。但是所有生物质,无论原料品位高低均用于燃烧,导致高品位资源低值化利用,造成资源的浪费。
技术实现要素:4.为了解决以上技术问题,本发明提供一种流化床富氧燃烧与移动床热解气化的耦合设备及方法。本发明提供的流化床富氧燃烧与移动床热解气化的耦合设备不仅低碳环保而且原料适应性广,兼顾能量利用率高,污染小,产品品质好等优点。
5.具体的,本发明首先提供一种流化床富氧燃烧与移动床热解气化的耦合设备,包括:流化床提升管3、第一高温旋风分离器4、移动床反应器5、第二高温旋风分离器7、氧气提供装置和高温过热器8;其中,所述流化床提升管3与所述第一高温旋风分离器4连接;所述第一高温旋风分离器4与所述移动床反应器5连接,所述移动床反应器5与所述第二高温旋风分离器7连接,所述高温过热器8与所述第二高温旋风分离器7连接,所述氧气提供装置与
所述移动床反应器5连接。
6.本发明发现,采用流化床与移动床两种床型耦合,原料适用性广,既可处理适用于流化床的粉末农林废弃物,又可处理适用于移动床的颗粒农林废弃物。农林废弃物中的碳来自大气环境,经光合作用被固定下来,在燃烧过程中又被释放进入大气环境,因此农林废弃物燃烧工艺是一个零碳排放工艺。但是农林废弃物在空气中燃烧容易出现燃烧效率不高,从而导致生物质利用率低。纯氧燃烧能非常好的避免这个问题,同时纯氧燃烧还兼具污染小,尾气组分中水蒸气及co2浓度高的优点。高温、高浓度的水蒸气和co2尾气是非常合适的农林废弃物气化活化载气,将纯氧燃烧的尾气和热量用于农林废弃物的气化活化,能最大化的利用农林废弃物燃烧产生的能量与物质。再结合碳捕集、利用和封存技术即能实现负排放。最后结合生物质炭与草木灰在土壤修复的不同作用,形成一种高效的草木灰与生物质炭土壤修复缓释剂。集成的整个技术可以形成一套负碳排放、低能耗、高利用率的农林废弃物资源化耦合工艺。
7.根据本发明提供的流化床富氧燃烧与移动床热解气化的耦合设备,还包括粉末农林废弃物预热干燥给料单元2,所述粉末农林废弃物预热干燥给料单元2与所述流化床提升管3连接。
8.根据本发明提供的流化床富氧燃烧与移动床热解气化的耦合设备,还包括颗粒农林废弃物预热干燥给料单元6,所述颗粒农林废弃物预热干燥给料单元6与所述移动床反应器5连接。
9.根据本发明提供的流化床富氧燃烧与移动床热解气化的耦合设备,还包括分质分类预处理系统1,所述分质分类预处理系统1与所述粉末农林废弃物预热干燥给料单元2连接,所述分质分类预处理系统1与所述颗粒农林废弃物预热干燥给料单元6连接。
10.根据本发明提供的流化床富氧燃烧与移动床热解气化的耦合设备,还包括高温过热器8,所述高温过热器8与所述第二高温旋风分离器7连接。
11.根据本发明提供的流化床富氧燃烧与移动床热解气化的耦合设备,还包括低温过热器9、省煤器10和除尘器12;所述高温过热器8、所述低温过热器9、所述省煤器10和所述除尘器12依次连接。
12.根据本发明提供的流化床富氧燃烧与移动床热解气化的耦合设备,还包括氧气预热器11,所述氧气预热器11设于所述氧气提供装置和所述移动床反应器5之间。
13.根据本发明提供的流化床富氧燃烧与移动床热解气化的耦合设备,所述省煤器10与所述氧气预热器11连接。
14.根据本发明提供的流化床富氧燃烧与移动床热解气化的耦合设备,所述氧气预热器11与所述粉末农林废弃物预热干燥给料单元2连接,所述氧气预热器11与所述颗粒农林废弃物预热干燥给料单元6连接。
15.本发明中,产生的高温烟气依次流经高温过热器8、低温过热器9和省煤器10,将烟气温度降至200~220℃,进入氧气预热器11进行换热,将电解水工艺副产物纯氧加热到150~170℃,同时烟气温度降至150~170℃;然后150~170℃烟气分别流经粉末农林废弃物预热干燥给料单元2和颗粒农林废弃物预热干燥给料单元6,将物料预热至85~105℃干燥,同时烟气温度降至85~105℃;降温后烟气进入除尘器12进行过滤、除尘。
16.根据本发明提供的流化床富氧燃烧与移动床热解气化的耦合设备,还包括冷凝器
13和压缩分离单元14,所述除尘器12、所述冷凝器13和所述压缩分离单元14依次连接。
17.本发明中,经除尘器12除尘后部分烟气进入冷凝器13,被冷却到30~35℃,去除其中的水蒸气,剩余烟气进入压缩分离单元14,分离出h2和co用于下游合成氨或者合成甲醇等工艺,并将co2净化压缩,用于后续工业利用或埋存。
18.本发明还提供一种高效低碳农林废弃物流化床富氧燃烧与移动床热解气化的耦合方法,采用所述的流化床富氧燃烧与移动床热解气化的耦合设备。
19.根据本发明提供的流化床富氧燃烧与移动床热解气化的耦合方法,包括:将粉末农林废弃物原料在流化床提升管3内进行纯氧燃烧,纯氧燃烧的产物进入第一高温旋风分离器4内进行气固分离;分离的高温床料返回流化床提升管3;分离的高温烟气通入移动床反应器5下端;和/或,将块状农林废弃物原料在移动床反应器5内进行热解活化,热解活化尾气经过高温旋风分离器7进行气固分离,分离得到的高温床料降温后作为肥料;分离得到的高温烟气进入所述高温过热器8。
20.根据本发明,优选所述纯氧燃烧的氧气浓度》95%,所述氧气优选为电解水工艺副产物的纯氧,燃烧温度为1000~1200℃,所述热解活化的热源包括所述流化床提升管3中燃烧的热量和燃烧尾气的热量,优选的,所述纯氧燃烧采用氧气预热器11预热后的氧气。
21.根据本发明提供的流化床富氧燃烧与移动床热解气化的耦合方法,所述高温旋风分离器7分离的高温烟气依次流经高温过热器8、低温过热器9、省煤器10、除尘器12和冷凝器13处理,得到30~35℃的低温烟气,所述低温烟气进入压缩分离单元14,分离得到h2、co和co2。
22.根据本发明,优选的所述省煤器10将烟气温度降至200~220℃的烟气,所述烟气进入氧气预热器11进行换热,将所述氧气加热到150~170℃,同时所述烟气的温度降至150~170℃;然后所述烟气分别流经粉末农林废弃物预热干燥给料单元2和颗粒农林废弃物预热干燥给料单元6,将物料预热至85~105℃,同时所述烟气温度降至85~105℃。
23.根据本发明提供的流化床富氧燃烧与移动床热解气化的耦合方法,还包括对农林废弃物原料进行分质分类预处理,得到所述粉末农林废弃物原料和所述块状农林废弃物原料,然后将粉末农林废弃物原料进行预热干燥,预热干燥后的粉末农林废弃物原料进入所述流化床提升管3,将块状农林废弃物原料进行预热干燥,预热干燥后的块状农林废弃物原料进入所述移动床反应器5。
24.根据本发明提供的流化床富氧燃烧与移动床热解气化的耦合方法,农林废弃物经过分质分类预处理系统1处理,分为高品位高固定碳含量可成型农林废弃物和低品位高挥发分含量不可成型农林废弃物,对块状的高品位高固定碳含量可成型农林废弃物进行切块成型,生成1厘米见方的颗粒农林废弃物小块。该过程中产生的边角料以及锯末归入低品位高挥发分含量不可成型农林废弃物,然后将低品位高挥发分含量不可成型农林废弃物进行粉碎形成3毫米以下的粉末农林废弃物。粉末农林废弃物预热干燥给料单元2将粉末农林废弃物原料余热干燥后送入流化床提升管3内进行纯氧燃烧(氧气浓度》95%),燃烧温度为1000-1200℃,产生的烟气携带高温床料进入第一高温旋风分离器4内进行气固分离,分离效率为99%;分离得到的高温床料返回流化床提升管3;产生的高温烟气直接通入移动床反应器5下端,co2体积浓度约为60%,水蒸气体积浓度约为40%。颗粒农林废弃物预热干燥给料单元6将块状农林废弃物原料送入移动床反应器5进行热解炭化物理活化一体化,热源为
内部流化床提升管3燃烧的热量以及燃烧尾气作为气体热载体带入热量。热解活化尾气经过第二高温旋风分离器7进行气固分离,分离效率为99%;分离得到的高温床料换热降温后堆积作为肥料;产生的高温烟气依次流经高温过热器8、低温过热器9和省煤器10,将烟气温度降至200-220℃,进入氧气预热器11进行换热,将电解水工艺副产物纯氧加热到150-170℃,同时烟气温度降至150-170℃;然后150-170℃烟气分别流经粉末农林废弃物预热干燥给料单元2和颗粒农林废弃物预热干燥给料单元6,将物料预热至85-105℃干燥,同时烟气温度降至85-105℃;降温后烟气进入除尘器12进行过滤、除尘;除尘后部分烟气进入冷凝器13,被冷却到30-35℃,去除其中的水蒸气,剩余烟气进入压缩分离单元14,分离出h2和co用于下游合成氨或者合成甲醇等工艺,并将co2净化压缩,用于后续工业利用或埋存。本实施例将燃烧过程产生的底渣、飞灰等草木灰与颗粒生物质碳混合,可以作为一种低成本且高效的草木灰与生物质炭土壤修复缓释剂。活化后的农林废弃物可以吸附净化土壤,同时起到透气作用,而且一定程度的防止土壤板结。
25.本发明的有益效果至少在于:
26.1)本发明耦合了流化床与移动床两种床型,具有非常广的原料适用性,既可处理适用于流化床的粉末农林废弃物,又可处理适用于移动床的颗粒农林废弃物。本发明采用的耦合技术既避免了将所有大块废弃农林废弃物粉碎成粉末,使其全适用于流化床的高物料粉碎成本,又避免了移动床只能利用颗粒状废弃农林废弃物,造成大量的农林废弃物无法处理的资源浪费。综合高效利用所有农林废弃物,避免了所有农林废弃预处理到同一尺寸的成本较高问题,让合适的物料归于合适的工艺,生成合适的产品,起到物尽其用的目的,避免资源的浪费。
27.2)流化床采用纯氧燃烧,首先燃烧效率高,彻底解决了不完全燃烧飞灰中存在pahs污染环境的可能性。其次整个燃烧工艺隔绝了n2,避免了nox的生成,而且后续工艺无分离n2的成本。
28.3)移动床热解炭化和气化活化的热源以及活化介质充分利用流化床的尾气及余热,上下游高度协同,物料及能量利用率高,整个过程能量自给。得益于纯氧燃烧,流化床尾气中co2和h2o浓度高,尾气不经降温直接通入移动床,不仅是非常合适的活化介质,而且移动床热解炭化和气化活化过程的气体热载体。同时夹套内层的流化床反应器的产生的热量作为外层移动床的热源,换热流程短,换热效率高,综合能量利用率高。该活化过程为co2和h2o耦合活化,h2o利于造大孔,co2利于造微孔,两种气体耦合活化会提升生物质炭的比表面积。
29.4)尾气污染组分低,移动床尾气中组分较为集中,易于分离有效组分含量高。主要为co,co2,h2,h2o,ch4等热解气体,这些组分沸点或分子量差距较大,易于冷凝或变压吸附分离,避免了尾气中n2和co分离成本较高的问题。该工艺可以调整上游流化床或移动床物料的干燥程度获得适合后续工艺所需氢碳比的活化气。生物质热化学转化过程是一个“零碳”工艺加上碳捕集工艺即成为“负碳”工艺,整体项目环境友好度高,经济性高。
30.5)生物质炭与草木灰的应用契合度高。草木灰可用于土壤改良与修复,缓解因化肥农药和酸雨导致的土壤酸化,补充因土壤酸化过度流失的k、si、ca、mg、p等营养元素,但是其添加量不好掌握,一次添加过多容易造成土壤盐碱化和板结,造成植物根部缺氧或烧死。同时草木灰中营养元素水溶性较好,容易流失。生物质碳能提升土壤中有机质含量,提
高土壤微生物的生物量和活性,对有机污染物和重金属进行吸附固定降低其毒性,提高土壤持水能力等积极效应。草木灰与生物质炭协同形成土壤修复缓释剂,不仅兼顾各自的效果,而且生物质碳能起到控制草木灰中营养元素迅速释放对土壤生态的冲击,同时避免了营养元素的流失。
附图说明
31.为了更清楚地说明本发明实施例或现有技术中的技术方案,下面将对实施例或现有技术描述中需要使用的附图作简单介绍,显而易见,下面描述中的附图仅仅是本发明的一些实施例,对于本领域普通技术人员来讲,在不付出创造性劳动的前提下,还可以根据这些附图获得其他的附图。
32.图1为本发明实施例中流化床富氧燃烧与移动床热解气化的耦合设备示意图;
33.图2为本发明实施例中农林废弃物分质分类预处理流程示意图;
34.图3为本发明实施例中流化床富氧燃烧与移动床热解气化的耦合处理流程示意图。
35.图中,1、农林废弃物分质分类预处理系统;2、粉末农林废弃物预热干燥给料单元;3、流化床提升管;4、第一高温旋风分离器;5、移动床反应器;6、颗粒农林废弃物预热干燥给料单元;7、第二高温旋风分离器;8、高温过热器;9、低温过热器;10、省煤器;11、氧气预热器;12、除尘器;13、冷凝器;14、压缩分离单元。
具体实施方式
36.为使本发明实施例的目的、技术方案和优点更加清楚,下面将结合本发明实施例中的附图,对本发明实施例中的技术方案进行清楚、完整地描述,以下实施例用于说明本发明,但不用来限制本发明的范围。实施例中未注明具体技术或条件者,按照本领域内的文献所描述的技术或条件,或者按照产品说明书进行。所用试剂或仪器未注明生产厂商者,均为可通过正规渠道商购买得到的常规产品。
37.实施例1
38.本实施例提供一种流化床富氧燃烧与移动床热解气化的耦合设备,包括:流化床提升管3、第一高温旋风分离器4、移动床反应器5、第二高温旋风分离器7、氧气提供装置和高温过热器8;其中,所述流化床提升管3与所述第一高温旋风分离器4连接;所述第一高温旋风分离器4与所述移动床反应器5连接,所述移动床反应器5与所述第二高温旋风分离器7连接,所述高温过热器8与所述第二高温旋风分离器7连接,所述氧气提供装置与所述移动床反应器5连接。
39.实施例2
40.本实施例提供一种流化床富氧燃烧与移动床热解气化的耦合设备,如图1所示,耦合设备包括:分质分类预处理系统1、粉末农林废弃物预热干燥给料单元2、流化床提升管3、第一高温旋风分离器4、移动床反应器5、颗粒农林废弃物预热干燥给料单元6、第二高温旋风分离器7、高温过热器8、低温过热器9、省煤器10、氧气预热器11、除尘器12、冷凝器13、压缩分离单元14。所述流化床提升管3与所述第一高温旋风分离器4连接;所述第一高温旋风分离器4与所述移动床反应器5连接,所述移动床反应器5与所述第二高温旋风分离器7连
接,所述高温过热器8与所述第二高温旋风分离器7连接,所述氧气提供装置与所述移动床反应器5连接。所述粉末农林废弃物预热干燥给料单元2与所述流化床提升管3连接。所述颗粒农林废弃物预热干燥给料单元6与所述移动床反应器5连接。所述分质分类预处理系统1与所述粉末农林废弃物预热干燥给料单元2连接,所述分质分类预处理系统1与所述颗粒农林废弃物预热干燥给料单元6连接。所述高温过热器8与所述第二高温旋风分离器7连接。所述高温过热器8、所述低温过热器9、所述省煤器10和所述除尘器12依次连接。所述氧气预热器11设于所述氧气提供装置和所述移动床反应器5之间。所述省煤器10与所述氧气预热器11连接,所述氧气预热器11与所述粉末农林废弃物预热干燥给料单元2连接,所述氧气预热器11与所述颗粒农林废弃物预热干燥给料单元6连接。
41.本实施例提供一种上述流化床富氧燃烧与移动床热解气化的耦合设备的耦合方法:如图2和3所示,农林废弃物经过分质分类预处理系统1处理,分为高品位高固定碳含量可成型农林废弃物和低品位高挥发分含量不可成型农林废弃物,对块状的高品位高固定碳含量可成型农林废弃物进行切块成型,生成1厘米见方的颗粒农林废弃物小块。该过程中产生的边角料以及锯末归入低品位高挥发分含量不可成型农林废弃物,然后将低品位高挥发分含量不可成型农林废弃物进行粉碎形成3毫米以下的粉末农林废弃物。粉末农林废弃物预热干燥给料单元2将粉末农林废弃物原料余热干燥后送入流化床提升管3内进行纯氧燃烧(氧气浓度》95%),燃烧温度为1000-1200℃,产生的烟气携带高温床料进入第一高温旋风分离器4内进行气固分离,分离效率为99%;分离得到的高温床料返回流化床提升管3;产生的高温烟气直接通入移动床反应器5下端,co2体积浓度约为60%,水蒸气体积浓度约为40%。颗粒农林废弃物预热干燥给料单元6将块状农林废弃物原料送入移动床反应器5进行热解炭化物理活化一体化,热源为内部流化床提升管3燃烧的热量以及燃烧尾气作为气体热载体带入热量。热解活化尾气经过第二高温旋风分离器7进行气固分离,分离效率为99%;分离得到的高温床料换热降温后堆积作为肥料;产生的高温烟气依次流经高温过热器8、低温过热器9和省煤器10,将烟气温度降至200-220℃,进入氧气预热器11进行换热,将电解水工艺副产物纯氧加热到150-170℃,同时烟气温度降至150-170℃;然后150-170℃烟气分别流经粉末农林废弃物预热干燥给料单元2和颗粒农林废弃物预热干燥给料单元6,将物料预热至85-105℃干燥,同时烟气温度降至85-105℃;降温后烟气进入除尘器12进行过滤、除尘;除尘后部分烟气进入冷凝器13,被冷却到30-35℃,去除其中的水蒸气,剩余烟气进入压缩分离单元14,分离出h2和co用于下游合成氨或者合成甲醇等工艺,并将co2净化压缩,用于后续工业利用或埋存。本实施例将燃烧过程产生的底渣、飞灰等草木灰与颗粒生物质碳混合,可以作为一种非常低成本且高效的草木灰与生物质炭土壤修复缓释剂。活化后的农林废弃物可以吸附净化土壤,同时起到透气作用,而且一定程度的防止土壤板结。
42.虽然,上文中已经用一般性说明及具体实施方案对本发明作了详尽的描述,但在本发明基础上,可以对之作一些修改或改进,这对本领域技术人员而言是显而易见的。因此,在不偏离本发明精神的基础上所做的这些修改或改进,均属于本发明要求保护的范围。