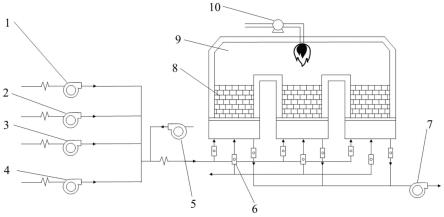
1.本发明属于节能环保技术领域,具体地说是涉及一种蓄热式热力氧化炉智能调控系统及方法。
背景技术:2.蓄热式热力氧化炉(rto)是vocs废气治理应用最为广泛的设备之一,具有净化效率高、处理风量范围宽、运行状况要求低的优点。然而在医药化工等行业中,有机废气具有来源多、间歇性排放等特点,进入rto的废气流量和vocs浓度波动大。当vocs浓度过低时,废气燃烧的热量不足以维持装置运行,需添加辅助燃料;当vocs浓度过高时,废气燃烧的热量过高,易造成设备损坏甚至带来安全风险。
3.目前针对rto的控制方式大多采用基于温度反馈的pid调节,当检测到燃烧室温度低于设定范围时打开辅助燃料开关,当监测到燃烧室温度高于设定范围时关闭辅助燃料开关。但由于温度变化和传感器响应具有滞后性,这种调节会导致温度波动范围较大,存在运行稳定性下降、辅助燃料浪费的情况,且无法对温度过高的情况进行调节。一些设计通过添加缓冲罐来平衡vocs浓度的波动,但需投入缓冲罐系统的额外建设成本,且缓冲罐发挥的作用受到容量的限制。
4.因此,构建rto的智能调控系统及方法,在基本维持原有装置结构的基础上实现rto高效节能稳定运行具有重要意义。
技术实现要素:5.为了克服现有技术存在的不足,本发明提供了一种蓄热式热力氧化炉智能调控系统及方法,通过实时参数提前预测rto燃烧室温度变化趋势,优化运行参数,并反馈至控制系统实现智能调控。本发明首先通过相对稳定的污水处理站低浓度废气对间歇性的车间高浓度废气混合缓冲,将rto入口废气浓度调节至2000~3000mg/m3;然后通过rto上游废气参数及rto实时运行参数并结合长短期记忆神经网络(lstm)预测燃烧室温度变化情况,建立rto燃烧热量衡算机理模型计算出调节燃烧室温度的稀释风和辅助燃料供应的需求量;将目标调节量传输至控制系统完成智能调控,使燃烧室温度稳定维持在预设温度附近,解决因生产侧废气排放波动引起的rto运行不稳定、燃料消耗大、安全风险大等问题,实现vocs的高效节能稳定脱除。
6.为了达到上述目的,本发明采用的技术方案是:
7.一种蓄热式热力氧化炉智能调控系统,包括装置部分、感知模块、预测模块、优化模块和控制模块;
8.所述装置部分包括高浓度废气风机、低浓度废气风机、稀释风机、提升阀、烟气引风机、蓄热式热力氧化炉、燃料供应泵,所述蓄热式热力氧化炉包括蓄热体、燃烧室,
9.所述感知模块包括采集数据的仪器仪表及传感器、分析数据的处理器,通过仪器仪表及传感器的在线检测,结合通讯设备,完成信息采集、传输与存储;
10.所述预测模块包括燃烧室的温度预测模型,温度预测模型根据感知模块获取的数据,提前预测燃烧室温度变化;
11.所述优化模块包括位于服务器上的rto燃烧热量衡算的机理模型,根据燃烧室预测温度与目标温度的差距计算出稀释风和燃料供应的调节量;
12.所述控制模块包括控制器,控制器通过网络通信模块接收优化模块的调节量后驱动执行机构完成调控。
13.作为优选,通过装置部分完成高、低浓度废气混合与燃烧过程;
14.高、低浓度废气混合(混合过程):首先通过废水处理站排出的低浓度废气(80~120mg/m3)对生产车间排出的间歇性、高浓度废气(20000~50000mg/m3)进行混合缓冲,将废气浓度调节至2000~3000mg/m3,再控制稀释风机的变频频率,调节蓄热式热力氧化炉入口废气的总浓度和流量;
15.燃烧过程:混合后的废气进入燃烧室中进行燃烧,产生的高温气体流经蓄热室,使其中的蓄热体升温,用于预热后续进入的废气;蓄热室包括一个以上,每个蓄热室依次经历蓄热-放热-清扫过程,周而复始,连续工作。
16.作为优选,感知模块感知蓄热式热力氧化炉入口上游的废气参数以及蓄热式热力氧化炉实时运行参数,所述废气参数包括蓄热式热力氧化炉入口上游支管以及总管处的废气温度、流量、vocs浓度、氧含量、湿度;所述蓄热式热力氧化炉实时运行参数包括燃烧室温度、蓄热体上层温度、蓄热体中层温度、蓄热体下层温度。
17.作为优选,预测模块中的模型基于历史运行数据由机器学习训练得出,采用适用于处理延迟系统的参数预测问题的长短期记忆神经网络(lstm)算法进行模型建立,模型的输入参数为总管废气温度、总管废气流量、总管废气vocs浓度、总管废气氧含量、总管废气湿度、蓄热式热力氧化炉蓄热体上层温度、蓄热式热力氧化炉蓄热体中层温度、蓄热式热力氧化炉蓄热体下层温度,模型的输出参数为蓄热式热力氧化炉燃烧室温度;
18.预测模块中lstm模型的数据输入量维度设置为100,时间步长维度设置为10,表示每次使用前100个时刻数据预测未来10个时刻的燃烧室温度;
19.预测模块中共包括3层lstm网络和1层全连接层,为防止网络模型过拟合,在每一层的lstm层后设置dropout层,dropout层在前向传播的过程中让神经元以一定的概率停止工作,增加模型的泛化能力,降低模型的过拟合几率;
20.预测模块中选取sigmoid作为激活函数,对神经元进行激活;
[0021][0022]
其中,x为原始值,y为激活值;
[0023]
预测模块中选取均方误差mse作为损失函数;
[0024][0025]
其中,n为样本总量,i为样本点,yi为样本真实值,为样本预测值;
[0026]
预测模块中选取adam作为优化函数,对lstm模型中的神经元数值进行更新,不断降低损失函数的数值,最终实现rto燃烧温度的精准预测。
[0027]
作为优选,优化模块中采用建立rto热量衡算机理模型,对燃烧室温度的优化调节值进行计算,判断预测模块计算的燃烧室温度是否在设定范围内,当此预测温度超出设定范围则通过热量衡算机理模型计算出目标调节量;当预期温度低于设定范围时,添加辅助燃料,提供更多热量、保持燃烧室温度稳定;当预期温度高于设定范围时,停止辅助燃料的添加,打开稀释风机,对废气浓度进行稀释;
[0028]
建立的rto燃烧热量衡算机理模型之间的关系如下:
[0029]
首先计算出废气从入口温度提升至目标设定温度所需的总热量,进而计算废气燃烧释放的总热量,根据两者的差值计算出所需燃料补充的热量或稀释风稀释的热量;
[0030]
废气从入口温度提升至目标设定温度所需的总热量为:
[0031]qsum
=(t
obj-t
in
)*c
gas
*v
gas
*ρ
gas
*(1-θ)
[0032]
废气燃烧释放的总热量为:
[0033]qgas
=q
gas
*v
gas
*(1-μ)
[0034]
废气需要进行调节的总热量为:
[0035]qadj
=q
sum-q
gas
[0036]
若q
adj
小于0,证明当前废气状态下燃烧出的总热量将使燃烧室温度超出预定目标值,此时的热量需要稀释风进行稀释,所需的稀释风量为:
[0037][0038]
若q
adj
大于0,证明当前废气状态下燃烧出的总热量不足以使燃烧室温度达到预定目标值,此时需要补充燃料进行热量填充,所需的补充燃料为:
[0039][0040]
式中,q
sum
为废气升温所需的总热量,t
obj
为废气目标温度,t
in
为废气入口温度,c
gas
为废气平均比热容,v
gas
为废气流量,ρ
gas
为废气平均密度,θ为蓄热体蓄热效率,q
gas
为废气燃烧释放热量,q
gas
为废气燃烧热,μ为rto散热系数,v
dil
为稀释风流量,t
dil
为稀释风入口温度,c
dil
为稀释风比热容,ρ
dil
为稀释风密度,v
fuel
为燃料流量,q
fuel
为燃料燃烧热,m
fuel
为燃料分子质量。
[0041]
作为优选,控制模块中所述控制器选取dcs或plc控制器,控制器与服务器之间通过opc协议完成数据交互,获取优化模块的参数调节量,反馈至控制器进行精准控制。
[0042]
本发明还提供了上述蓄热式热力氧化炉智能调控系统的调控方法,包括下述步骤:
[0043]
s1:对装置部分上的各个关键点位布置仪器仪表、传感器,过感知模块收集蓄热式热力氧化炉智能调控系统的关键运行及设计参数,通过网络通信模块将数据传输到云端数据库;
[0044]
s2:通过构建的历史参数数据库,对预测模块中的燃烧室的温度预测模型进行训练,使用大批量历史数据以及对超参数的不断调整,拟合出最优的基于lstm温度预测模型,并通过对rto燃烧热量衡算的机理模型计算出实时的热量,完成热量的调节;
[0045]
s3:基于预测模型和优化模型,提前预测出燃烧室温度的未来变化趋势,精准计算出目标参数的调节量,维持rto的稳定燃烧;
[0046]
s4:通过服务器与控制器的数据交互,获取目标控制参数的调节量,使控制器完成精准调节。
[0047]
作为优选,将训练好的燃烧室温度预测模型,对输入的实时参数进行预测,预测出的温度与目标温度进行比对,通过先前建立的rto燃烧热量衡算机理模型,计算出目标调节量。
[0048]
作为优选,数据收集于dcs/plc控制器后通过opc交换上传至服务器,利用预测模型预测燃烧室温度,并根据优化模型计算参数调节量,将调节量反馈至dcs/plc控制器完成预测性控制。
[0049]
作为优选,所述网络通信模块包括4g通信卡、5g通信卡和nb-lot。
[0050]
本发明的有益效果在于:
[0051]
通过大流量低浓度废气与小流量高浓度废气混合缓冲、关键参数预测控制的方法使rto燃烧室稳定维持在合理水平,有效减少辅助燃料使用量,提高设备运行的稳定性与可靠性。
附图说明
[0052]
图1是本发明蓄热式热力氧化炉智能调控系统的结构示意图;
[0053]
图2是本发明蓄热式热力氧化炉智能调控方法的流程图;
[0054]
图3是本发明蓄热式热力氧化炉智能调控方法实施效果图;
[0055]
图示说明:
[0056]
1.a区高浓度废气风机;2.b区高浓度废气风机;3.c区高浓度废气风机;4.低浓度废气风机;5.稀释风机;6.提升阀;7.烟气引风机;8.蓄热体;9.燃烧室;10.燃料供应泵。
具体实施方式
[0057]
下面结合具体实施例对本发明做出进一步的说明,这些实施例并非对本发明的限定,依照本领域现有的技术,本发明的实施方式并不限于此,凡依照本发明公开内容所做出的本领域的等同替换,均属本发明的保护内容。
[0058]
参照图1,图2,一种蓄热式热力氧化炉智能调控系统,包括装置部分、感知模块、预测模块、优化模块和控制模块;
[0059]
所述装置部分包括高浓度废气风机(a区高浓度废气风机1,b区高浓度废气风机2,c区高浓度废气风机3)、低浓度废气风机4、稀释风机5、提升阀6、烟气引风机7、蓄热式热力氧化炉、燃料供应泵10,所述蓄热式热力氧化炉包括蓄热体8、燃烧室9,装置部分用于将有机废气加热分解至其中的vocs氧化成二氧化碳和水;
[0060]
所述感知模块包括采集数据的仪器仪表及传感器、分析数据的处理器,通过仪器仪表及传感器的在线检测,结合通讯设备,完成信息采集、传输与存储;
[0061]
所述预测模块包括燃烧室的温度预测模型,温度预测模型根据感知模块获取的数据,提前预测燃烧室温度变化;
[0062]
所述优化模块包括位于服务器上的机理与数据协同驱动的优化模型,根据燃烧室预测温度与目标温度的差距计算出稀释风和燃料供应的调节量;
[0063]
所述控制模块包括控制器,控制器通过通讯网络接收优化模块的调节量后驱动执
行机构完成调控。
[0064]
通过装置部分完成高、低浓度废气混合与燃烧过程;
[0065]
高、低浓度废气混合(混合过程):首先通过废水处理站排出的低浓度废气(80~120mg/m3)对生产车间排出的间歇性、高浓度废气(20000~50000mg/m3)进行混合缓冲,将废气浓度调节至2000~3000mg/m3,再控制稀释风机的变频频率,调节蓄热式热力氧化炉入口废气的总浓度和流量;
[0066]
燃烧过程:混合后的废气进入燃烧室中进行燃烧,产生的高温气体流经蓄热室,使其中的蓄热体升温,用于预热后续进入的废气;蓄热室包括一个以上,每个蓄热室依次经历蓄热-放热-清扫过程,周而复始,连续工作。
[0067]
感知模块感知蓄热式热力氧化炉入口上游的废气参数以及蓄热式热力氧化炉实时运行参数,所述废气参数包括蓄热式热力氧化炉入口上游支管以及总管处的废气温度、流量、vocs浓度、氧含量和湿度;所述蓄热式热力氧化炉实时运行参数包括燃烧室温度、蓄热体上层温度、蓄热体中层温度和蓄热体下层温度。
[0068]
预测模块中的模型基于历史运行数据由机器学习训练得出,采用适用于处理延迟系统的参数预测问题的长短期记忆神经网络(lstm)算法进行模型建立,模型的输入参数为总管废气温度、总管废气流量、总管废气vocs浓度、总管废气氧含量、总管废气湿度、蓄热式热力氧化炉蓄热体上层温度、蓄热式热力氧化炉蓄热体中层温度和蓄热式热力氧化炉蓄热体下层温度,模型的输出参数为蓄热式热力氧化炉燃烧室温度;
[0069]
预测模块中lstm模型的数据输入量维度设置为100,时间步长维度设置为10,表示每次使用前100个时刻数据预测未来10个时刻的燃烧室温度;
[0070]
预测模块中共包括3层lstm网络和1层全连接层,为防止网络模型过拟合,在每一层的lstm层后设置dropout层,dropout层在前向传播的过程中让神经元以一定的概率停止工作,增加模型的泛化能力,降低模型的过拟合几率;
[0071]
预测模块中选取sigmoid作为激活函数,对神经元进行激活;
[0072][0073]
其中,x为原始值,y为激活值;
[0074]
预测模块中选取均方误差mse作为损失函数;
[0075][0076]
其中,n为样本总量,i为样本点,yi为样本真实值,为样本预测值;
[0077]
预测模块中选取adam作为优化函数,对lstm模型中的神经元数值进行更新,不断降低损失函数的数值,最终实现rto燃烧温度的精准预测。
[0078]
优化模块中采用建立rto热量衡算机理模型,对燃烧室温度的优化调节值进行计算,判断预测模块计算的燃烧室温度是否在设定范围内,当此预测温度超出设定范围则通过热量衡算机理模型计算出目标调节量;当预期温度低于设定范围时,添加辅助燃料,提供更多热量、保持燃烧室温度稳定;当预期温度高于设定范围时,停止辅助燃料的添加,打开稀释风机,对废气浓度进行稀释;
[0079]
建立的rto燃烧热量衡算机理模型之间的关系如下:
[0080]
首先计算出废气从入口温度提升至目标设定温度所需的总热量,进而计算废气燃烧释放的总热量,根据两者的差值计算出所需燃料补充的热量或稀释风稀释的热量;
[0081]
废气从入口温度提升至目标设定温度所需的总热量为:
[0082]qsum
=(t
obj-t
in
)*c
gas
*v
gas
*ρ
gas
*(1-θ)
[0083]
废气燃烧释放的总热量为:
[0084]qgas
=q
gas
*v
gas
*(1-μ)
[0085]
废气需要进行调节的总热量为:
[0086]qadj
=q
sum-q
gas
[0087]
若q
adj
小于0,证明当前废气状态下燃烧出的总热量将使燃烧室温度超出预定目标值,此时的热量需要稀释风进行稀释,所需的稀释风量为:
[0088][0089]
若q
adj
大于0,证明当前废气状态下燃烧出的总热量不足以使燃烧室温度达到预定目标值,此时需要补充燃料进行热量填充,所需的补充燃料为:
[0090][0091]
式中q
sum-废气升温所需的总热量,t
obj-废气目标温度,t
in-废气入口温度,c
gas-废气平均比热容,v
gas-废气流量,ρ
gas-废气平均密度,θ-蓄热体蓄热效率,q
gas-废气燃烧释放热量,q
gas-废气燃烧热,μ-rto散热系数,v
dil-稀释风流量,t
dil-稀释风入口温度,c
dil-稀释风比热容,ρ
dil-稀释风密度,v
fuel-燃料流量,q
fuel-燃料燃烧热,m
fuel-燃料分子质量。
[0092]
控制模块中所述控制器选取dcs或plc控制器,控制器与服务器之间通过opc协议完成数据交互,获取优化模块的参数调节量,反馈至控制器进行精准控制。
[0093]
本实施例的实施对象为某制药企业废气治理系统,该企业的废气来自于维生素、胡萝卜素、克拉霉素、盐酸万古霉素制剂等药剂加工车间,在生产过程中会经历投料、过滤、提纯、冷凝、冷却等工艺,各工艺过程中均会产生废气,废气来源复杂,同时会产生多种类有机废气,包括丙酮、二氯甲烷、二甲苯、甲苯等。
[0094]
该企业的废气末端治理工艺如图1所示,各车间的生产废气在车间内部经冷凝回收,车间预处理等工序后进入到收集管路,通过高浓度废气风机进入区域废气管路,高浓度废气风机1-3分别汇总a、b、c等区域废气,低浓度废气风机4收集该企业污水处理站的低浓度废气,此废气较为平稳且流量高可对生产车间排出的间歇性的低流量、高浓度废气进行混合缓冲,缓冲后废气浓度调节至2000~3000mg/m3。各区域废气汇总后进入废气总管,总管外接入可调节的变频风机5用于添加空气将废气进行稀释缓冲,经过混合后的废气进入rto燃烧室中进行燃烧,产生的高温气体流经调节阀6进入特制的陶瓷蓄热体8,使蓄热室中的陶瓷体升温而“蓄热”,此“蓄热”用于预热后续进入的有机废气。蓄热室共包括三个,每个蓄热室依次经历蓄热-放热-清扫过程,周而复始,连续工作。蓄热室“放热”后应立即引入适量洁净空气对该蓄热室进行“清扫”,清扫后的蓄热室再次进入“蓄热”过程。燃烧室外接燃料供应泵10用于维持燃烧室温度,最终废气经烟气引风机7排出。
[0095]
该企业的rto采用三室结构,设计风量为37000m3/h,通过plc直接控制,添加燃料
为甲醇,系统带有蓄热体上层温度、蓄热体中层温度、蓄热体下层温度、燃烧室温度、废气入口lel浓度、废气入口温度、废气入口湿度、废气入口压力、废气入口氧含量浓度、rto出口温度等在线监测点位,可在各区域废气管路、低浓度废管路以及总管路上添加气体流量传感器、vocs浓度传感器。
[0096]
其中蓄热式热力氧化炉智能调控方法包括如下技术路线:
[0097]
s1:通过感知模块中对装置部分上的各个关键点位布置仪器仪表、传感器,收集蓄热式热力氧化炉智能调控系统的关键运行及设计参数(废气参数及rto运行参数);通过网络通信模块如4g通信卡、5g通信卡、nb-lot等将数据传输到云端数据库,构建系统多维数据库;
[0098]
s2:通过构建的历史参数数据库(系统多维数据库),对预测模块中的燃烧室的温度预测模型进行训练,使用大批量历史数据以及对超参数的不断调整,拟合出最优的基于lstm温度预测模型,并通过建立rto燃烧热量衡算的机理模型,计算出实时的热量,完成热量的调节;
[0099]
s3:基于上述模型,提前预测出燃烧室温度的未来变化趋势,精准计算出目标参数的调节量,维持rto的稳定燃烧;
[0100]
s4:通过服务器与控制器的数据交互,获取目标控制参数的调节量,并反馈至控制器(控制系统),使plc控制系统完成精准调节。
[0101]
具体而言,在步骤s1过程中将rto入口废气参数以及rto内部参数进行采集,包括总管废气温度、总管废气流量、总管废气vocs浓度(lel浓度)、总管废气氧含量、总管废气湿度、蓄热式热力氧化炉左侧蓄热体上层温度、蓄热式热力氧化炉左侧蓄热体中层温度、蓄热式热力氧化炉左侧蓄热体下层温度、蓄热式热力氧化炉中间蓄热体上层温度、蓄热式热力氧化炉中间蓄热体中层温度、蓄热式热力氧化炉中间蓄热体下层温度、蓄热式热力氧化炉右侧蓄热体上层温度、蓄热式热力氧化炉右侧蓄热体中层温度、蓄热式热力氧化炉右侧蓄热体下层温度、蓄热式热力氧化炉燃烧室温度,共计十五个参数。
[0102]
在步骤s2中的预测模型中,将采集的历史数据中除蓄热式热力氧化炉燃烧室温度以外的十四个参数作为模型的输入参数,蓄热式热力氧化炉燃烧室温度作为预测温度。作为优选,选取一天24h(24*60*60)共计86400的数据长度用作模型训练,其中80%的数据作为训练集,20%的数据作为测试集,通过测试集准确程度对模型的参数进行调节。作为优选,预测模型的数据输入量维度设置为100,时间步长维度设置为10,每次使用前100个时刻数据预测未来10个时刻的燃烧室温度。即每次的输入训练数据为100*14的矩阵,输出数据为第110个时刻的蓄热式热力氧化炉燃烧室温度值。在步骤s2中的机理模型中,首先设定目标燃烧室温度,作为优选,燃烧室温度的选值为800℃(尽可能地降低平均燃烧温度,并保证燃烧的稳定进行),进而根据入口废气的基本参数计算出达到800℃燃烧室温度的总热量,q
sum
=(t
obj-t
in
)*c
gas
*v
gas
*ρ
gas
*(1-θ),同时根据气体浓度计算出全部废气燃烧释放出的总热量,q
gas
=q
gas
*v
gas
*(1-μ),最后通过对比两个热量数值,q
adj
=q
sum-q
gas
,若废气燃烧热量较大计算出所需的稀释风量,若废气燃烧热量较小计算出所需的甲醇添加量,
[0103]
式中q
sum-废气升温所需的总热量,t
obj-废气目标温度,t
in-废气入口温度,c
gas-废气平均比热容,v
gas-废气流量,ρ
gas-废气平均密度,θ-蓄热体蓄热效率,q
gas-废气燃烧释放热量,q
gas-废气燃烧热,μ-rto散热系数,v
dil-空气流量,t
dil-空气入口温度,c
dil-空气比热容,ρ
dil-空气密度,v
fuel-甲醇流量,q
fuel-甲醇燃烧热,m
fuel-甲醇分子质量。
[0104]
在步骤s3中,将训练好的燃烧室温度预测模型,对输入的实时参数进行预测,预测出的温度与目标温度进行比对,通过先前建立的rto燃烧热量衡算机理模型,计算出目标调节量。
[0105]
在步骤s4中,通过opc协议完成与服务器的数据交互,获取优化模块的参数调节量,反馈至plc控制系统进行调节。
[0106]
根据以上实施方案,本发明蓄热式热力氧化炉智能调控方法实施效果如图3所示,原系统温度通常在800~920℃波动(为了抑制二噁英生成,一般需850℃以上),通过智能调控将rto燃烧室温度波动下降约80%,有利于在满足vocs高效处理的较低温度区域卡边运行,预计燃烧室平均温度可降低40℃左右。按该平均废气处理量为30000m3/h计算,40℃的温降每年节约的热量折合甲醇60吨左右,节能效果显著。
[0107]
本发明首先通过相对稳定的污水处理站低浓度废气对间歇性的车间高浓度废气混合缓冲,将rto入口挥发性有机物(vocs)浓度调节至2000~3000mg/m3;然后利用实时监测参数和长短期记忆神经网络(lstm)预测燃烧室温度变化趋势,优化计算出稀释风和辅助燃料供应的调节量;进行调控后使燃烧室温度稳定维持在预设温度附近,解决因生产侧废气排放波动引起的rto运行不稳定、燃料消耗大、安全风险大等问题,实现vocs的高效节能稳定脱除。
[0108]
上述实施例仅例示性说明本发明的较佳方案,而非用于限制本发明。任何熟悉此技术的人士皆可在不超出记载的技术方案的范畴下,对上述实施例进行修饰或改变。因此,举凡所属技术领域中具有通常知识者在未脱离本发明所揭示的精神与技术思想下所完成的一切等效修饰或改变,仍应由本发明的权利要求所涵盖。