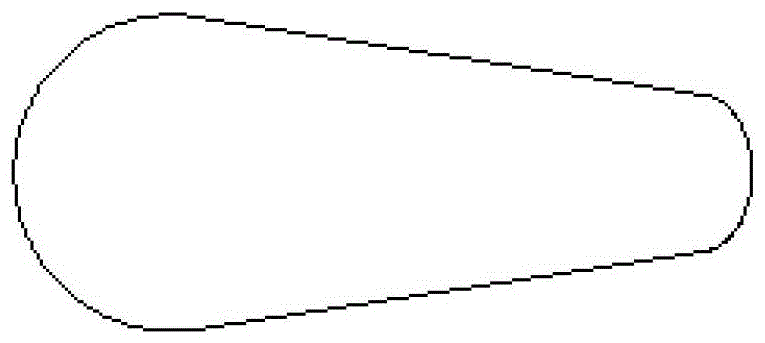
本发明涉及一种换热管,特别是涉及一种用于化工、热电厂、冶金及食品加工领域具有增强传热效果、减小管内壁结垢的换热管,该换热管内部表面设置有强化传热元件。
背景技术:通过换热管壁实现管内外介质交换能量在实际工程中应用广泛,普通的换热管为光管,其内外管壁比较平滑,结构简单,加工方便,应用广泛,可在高温、高压等苛刻的条件下使用,且检修方便。但是在实际应用中存在热效率不高等缺陷,在有些对换热能力要求高的工况下不宜采用,在某些管内介质存在可能沉积杂质的情况下使用也受到了限制。为增强换热效果,目前已有板翅式换热器等多种单位体积换热面积大大高于管式换热器的换热设备,但是由于受设计、制造、选材和加工工艺等多方面限制原因,难以应用于高温、高压等苛刻条件,更无法处理含有固体或易生成可沉淀物质的或可结焦介质。另外,由于其结构特点,当换热器内部发生泄漏时难以发现泄漏点,不易维修。授权公告号为CN202074870的实用新型专利公开了一种换热管,该换热管包括蛇形管,该蛇形管弯折形成多个换热管段,相邻的换热管段之间连接有换热片,该换热片为沿垂直于换热管段轴线的方向发生折弯的折弯件,从而防止换热片与换热管段之间的连接位置由于热膨胀而发生撕裂,显著提高了换热管的使用寿命。但该结构的换热管不具有增强传热效果、减小管内壁结垢的效果。授权公告号为CN202101591的实用新型专利公开了一种翅片换热管,通过将管体内壁设置成齿条状结构,通过齿条状结构增加了管体内壁的换热面积,同时使得管内部的换热流体处于紊流状态,增大了扰动性,极大地提高了换热效率,延长了换热管的使用寿命。但该结构的换热管内壁较容易结垢,不容易清理,难以处理含有固体或易生成可沉淀物质的介质。专利号为ZL200380103179.3的发明专利公开一种具有螺旋翅片的裂化管,翅片形成在管的内表面上并且相对于管的轴线倾斜,离散地布置在一个或多个螺旋轨迹上,从管的一个轴向端到其另一个轴向端的管的整个轴向长度上不存在翅片。翅片用于搅拌管内流体,可最大程度地抑制压力损失,同时有效地促进热量传输到流体上。由于管内翅片相对于管的轴线倾斜,且呈螺旋形分布,在压力损失较小和增强传热方面具有很好的效果,但如果用于管内介质存在可能沉积杂质的情况,则不可避免的造成管内壁结垢,不易清理和维修。
技术实现要素:本发明发明的目的是提供一种具有强化传热元件的换热管,具有增强传热效果、减小管内壁结垢的换热管。本发明所述的一种具有强化传热元件的换热管,所述强化传热元件为水滴状的流线型、三棱锥形或半椭球形,离散地布置在换热管的内壁上,当换热管的内表面展开时,强化传热元件在换热管内壁上的排布方式为:呈三角形排布或由多个三角形组合而成的排布方式或能分解为多个三角形的排布方式,其中优选所述三角形为等腰三角形。本发明的换热管,其中优选所述强化传热元件的高度与换热管半径的比值(d1/R)为0.05-0.4,更优选0.08-0.2,强化传热元件的长度与其高度的比值(d2/d1)为0.5-10,更优选2-6。本发明的换热管,其中优选所述两个强化传热元件的纵向(沿管长)距离与强化传热元件的长度比(D1/d2)为0.5-20,更优选1.5-3,所述强化传热元件的横向(垂直于管长)距离与换热管横截面的周长比(D2/2πR)为0.05-0.5,更优选0.08-0.2。所述纵向距离是指当换热管的内表面展开时,顺着流体方向前后两个相邻强化传热元件之间的距离;所述横向距离是指当换热管的内表面展开时,垂直于流体方向上两个相邻强化传热元件之间的距离。本发明的换热管,其中所述水滴状的流线型强化传热元件的排布方式与管内流体的方向呈0~90度夹角。所述水滴状的流线型可以是任意表面光滑的头圆尾尖的水滴的形状。更优选在换热管内壁上的排布是圆头部迎着流体方向,尖尾部顺着流体方向。本发明的换热管,其中所述三棱锥形强化传热元件的尖头部分迎着流体方向,宽头部分顺着流体方向。优选所述三棱锥形强化传热元件为正三棱锥形的形状。本发明的换热管,其中所述半椭球形强化传热元件长径与流体方向的夹角为0~90度。其中优选所述半椭球形的强化传热元件的短径长度与其高度的比值为1-3,长径长度与短径长度的比值为1-10,更优选1-3。所述高度是指强化传热元件在换热管半径方向上延伸的尺寸。所述长径为半椭球形传热元件与换热管接触的面中较长的轴,所述短径为半椭球形传热元件与换热管接触的面中较短的轴。本发明还涉及上述换热管的应用,可用于热电厂、化工、冶金或食品加工领域的换热设备。进一步地,本发明的换热管特别适用于工业炉中管式炉炉管且管内介质含有易结垢物质的工况。本发明的换热管,其内设有水滴状的流线型、三棱锥形或半椭球形的强化传热元件,且强化传热元件的排布方式是这样的:呈三角形排布或由多个三角形组合而成的排布方式或其排布方式可分解为多个三角形。使流体在管内壁局部突起部位(强化传热元件)形成扰流,改变了管内介质的稳定流动,特别是改变管壁处的边界层内流体的流动状态,减小边界层的厚度,大大提高了换热管传热效率,也减缓或彻底消除了管壁形成污垢层的可能。进一步地,流线型的强化传热元件,圆形头部迎着流体方向,尖形尾部顺着流体方向;三棱锥形的强化传热元件,尖头部分迎着流体方向,宽头部分顺着流体方向。对于含有固体颗粒或易生成可沉淀物质的流体,增加该形状的强化传热元件可以进一步减少了结垢的可能。所以本发明的换热管可大大提高传热效率,同时又可应用于高温、高压以及处理管内含有固体杂质或可沉积物质等苛刻条件,易于清洗和维修。附图说明图1为换热管中水滴状的流线型强化传热元件的侧视结构示意图;图2为换热管中水滴状的流线型强化传热元件的俯视结构示意图;图3为换热管的内表面的展开示意图,用于示出水滴状的流线型强化传热元件的排布方式;图4为光管出口沿径向温度分布图;图5为加入强化传热元件后换热管出口沿径向温度分布图;图6为换热管的内表面的展开示意图,用于示出水滴状的流线型强化传热元件的另一种排布方式;图7为换热管的内表面的展开示意图,用于示出水滴状的流线型强化传热元件的另一种排布方式;图8a、图8b分别为本发明换热管中三棱锥形强化传热元件的侧视和俯视结构示意图;图9为换热管的内表面的展开示意图,用于示出三棱锥形强化传热元件的另一种排布方式;图10a、图10b分别为换热管中半椭球形强化传热元件的俯视和侧视结构示意图;其中:d1-强化传热元件的高度;d2-强化传热元件的长度;D1-强化传热元件的纵向距离;D2-强化传热元件的横向距离;d3-半椭球形强化传热件的短径的长度。具体实施方式以下结合附图、实施例和试验数据,对本发明上述的和另外的技术特征和优点作更详细的说明。如图1、2所示,本发明的换热管内表面上设有水滴状的流线型强化传热元件,该强化传热元件表面光滑,在换热管内壁上的排布是圆头部迎着流体方向,尖尾部顺着流体方向。如图3、图6、图7所示,当换热管的内表面展开时,水滴状的流线型强化传热元件在换热管内壁上的排布方式是这样的,呈三角形排布或由多个三角形组合而成的排布方式或是可分解为多个三角形的排布方式,优选所述三角形为等腰三角形。该水滴状的流线型强化传热元件的高度d1与换热管半径R的比值(d1/R)在0.05至0.4之间,优选0.08-0.2,强化传热元件的长度d2与其高度d1的比值(d2/d1)为0.5-10,优选2-6。两个强化传热元件的纵向距离与强化传热元件的长度比(D1/d2)为0.5-20,优选1.5-3,所述强化传热元件的横向距离与换热管横截面的周长比(D2/2πR)为0.05-0.5,优选0.08-0.2。如图8、9所示,本发明的换热管内表面上的强化传热元件还可以是三棱锥形,尖头部分迎着流体方向,宽头部分顺着流体方向,优选该三棱锥形为正三棱锥形。当换热管的内表面展开时,三棱锥形强化传热元件在换热管内壁上的排布方式、尺寸和上述水滴状的流线型强化传热元件的排布方式、尺寸相同。如图10所示,在其它的具体实施方式中,本发明的换热管内表面上的强化传热元件还可以是椭球形,其排布方式、尺寸和上述流线型强化传热元件的排布方式、尺寸相同。其中优选其短径与高度的比值为1-3,长度与短径的比值为1-10,更优选1-3;该半椭球形强化传热元件长径和流体流动方向夹角为0-90度。所述长径为半椭球形传热元件与换热管接触的面中较长的轴,所述短径为半椭球形传热元件与换热管接触的面中较短的轴。以3m长,内径(2R)为53mm的直换热管为研究对象,并在沿管程1米至2米处加入强化传热元件来考察流体流动传热情况,强化传热元件的排布方式如图3所示。输入条件:进口流量500kg/h;进口初始压力198.6KPa;进口温度873.15K;壁面温度1123.15K;介质为空气。实施例1至例4中水滴状强化传热元件的高度d1和长度d2各不同,具体数据见表1,强化传热元件的纵向距离为24.08mm,横向距离为13.87mm;实施例5在实施例2的基础上增大了强化传热元件的横向距离,将横向距离增大至16.64mm;实施例6在实施例2的基础上增大了强化传热元件的纵向距离,将纵向距离增大至36.12mm;以无强化传热元件的换热管(光管)为对比。压差选取1米至2米处的压差来表明经过强化传热元件后的压力变化情况,热通量选取1米至2米处的平均热通量。结果如表1所示。表1强化传热元件的不同尺寸、不同间距和光管的对比结果由表1中的结果可以看出,与光管相比增加了强化传热元件后换热管(实施例1-6)的换热能力(热通量)均有不同程度的增加,实施例1提高70%,实施例2提高77%,实施例3提高75%,实施例4提高67%,实施例5提高69%,实施例6提高63%;实施例1压降增加1.52倍,实施例2压降增加1.90倍,实施例3压降增加2.62倍,实施例4压降增加2.08倍,实施例5压降增加1.56倍,实施例6压降增加1.37倍。对比实施例2和实施例3,两实施例中强化传热元件的排布方式和间距相同,实施例3中强化传热元件的高度和长度均大于实施例2的强化传热元件的尺寸,但是其传热能力低于实施例2;实施例4和实施例2相比,强化传热元件的长度减小,其传热能力低于实施例2,结果和上述类似。从以上两组对比结果可以看出强化传热元件的外形尺寸对压降和传热效果都有比较显著的影响,由于实施例2的强化传热元件的外形更接近于流线型,因此压降要小,同时传热效果好于实施例4,因此选择合理的扰动元件外形尺寸非常重要。实施例5和实施例6与实施例2相比,分别增加了强化传热元件的横向和纵向间距,阻力降(压差)和换热能力(热通量)均有下降,这也证明了选择合适的强化传热元件不仅可以提高换热能力,同时可避免阻力降的大幅增加。图4和图5分别为计算的光管和加入强化传热元件后的换热管出口处沿径向温度分布图,由图的计算结果可以看出,增加强化传热元件后,径向温度更加均匀。对于管心(径向位置为0m)处的温度来看,加入强化传热元件后比未加强化传热元件的温度高,并且在-0.02m至0.02m处的温度明显比未加强化传热元件的温度分布要均匀(图5中该段接近于直线,图4中该范围的数值形成明显的曲线),这表明加入强化传热元件能够破坏流体平稳的流动,加强了径向的混合作用,提高整个流场流体的均匀性。本发明的换热管适用于径向温度均一性要求比较高的工况,例如:乙烯裂解炉管等在换热过程中管内同时发生对温度比较敏感的反应,或管内介质中含有易结垢物质的工况。当强化传热元件分别是三棱锥形、半椭球形时的实施例7-8:测试方法和上述实施例相同,强化传热元件的排布方式如图3所示,d3表示半椭球形强化传热件的短径的长度,强化传热元件的纵向距离D1为24.08mm,横向距离D2为13.87mm;三棱锥形强化传热元件的尺寸见表2实施例7,半椭球形强化传热元件的尺寸见表2实施例8;以实施例2(设有水滴状的流线型强化传热元件的换热管)和无强化传热元件的换热管(光管)作对比。表2不同强化传热元件与光管对比结果由表2中的结果中可以看出与光管相比,三棱锥形、半椭球形的强化传热元件,换热能力(热通量)均有不同程度的增加,分别是光管的1.23倍、1.84倍。与光管相比,三棱锥形、半椭球形的强化传热元件,阻力降(压差)均有提高,分别是光管的5.06倍、2.94倍。本发明上述结构的换热管可应用于高温、高压以及处理管内含有固体杂质或可沉积物质等苛刻条件,易于清洗和维修。在同工况的条件下,与现有普通结构的换热管相比,使用时间可延长0.5~1倍以上。