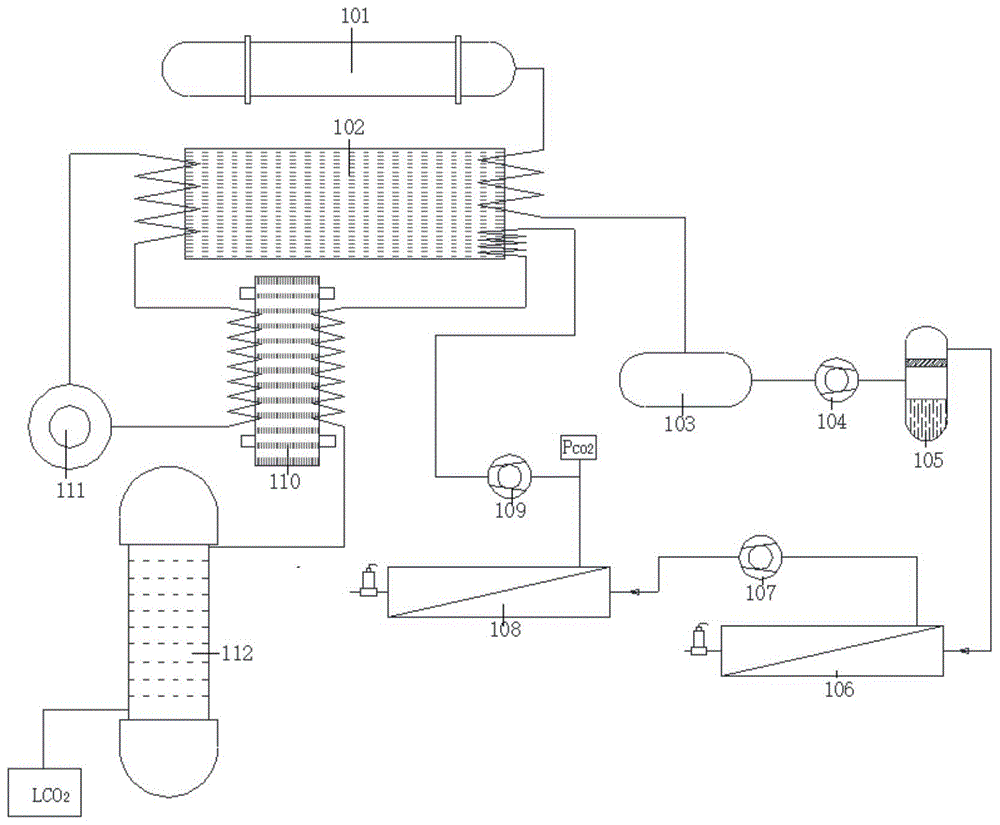
本发明属于节能和co2减排
技术领域:
,尤其涉及水泥窑炉烟气余热制冷辅助回收制取高纯co2的装置及方法。
背景技术:
:co2是温室气体之一,据了解水泥窑生产1吨孰料约排放二氧化碳0.86吨。据2018年统计,水泥生产所排放的co2约占全球排放总量的7%,因此水泥行业二氧化碳减排任务异常艰巨。水泥工业可以通过采取各种不同的技术措施来降低co2排放,例如富氧燃烧提高能量效率、使用替代燃料、替代原料等,然而这些技术革新所带来的减排效果有限。co2捕获和储存(ccs)技术近年来被逐步应用于减少水泥工业co2排放,被公认为是水泥工业深入全面碳减排的重大举措,被欧洲列为《2050欧洲低碳发展技术路线图》。我国也将ccs技术作为节能减排大力推举和扶持的措施之一。二氧化碳回收和提纯分离是ccs技术的关键,而水泥窑排放烟气中成分复杂、co2含量低(15~40%v/v)等导致co2回收和提纯面临技术难度大、工艺复杂、成本较高等特点。目前有mea化学吸收法、纯氧(o2+co2,co2为目标气体)燃烧法、冷却氨水法、膜分离法、分体式钙循环法和集成式钙循环法等多种co2捕获和减排工艺流程。水泥行业是co2排放重点产业集群之一,随着co2减排和碳交易指标越来越引起重视,如何高效捕获回收co2、降低设备投资和运行功耗将成为未来研究的热点。而目前应用较广的如mea吸收法、膜分离法等各种co2捕集技术,能耗高、投资大是绕不过的技术瓶颈之一。现有技术中专利申请号为201610344313.8提供了一种水泥窑余热回收装置,包括辐射换热器、第一管路系统以及第二管路系统,第一管路系统包括第一管道、给水泵、第一调节阀和流量计,辐射换热器的进水管上设有泄压阀、第一温度传感器和第一压力传感器;第二管路系统包括第二管道、第三管道以及第四管道,第三管道和或第四管道上设有第二调节阀,辐射换热器的出水管上设有第二温度传感器和第二压力传感器。该专利通过辐射换热器、第一管路系统以及第二管路系统的组合实现回转炉的辐射热直接将水加热送到锅炉汽包,不通过余热锅炉省煤器,增加余热锅炉的发电量的同时不影响排烟温度,充分有效利用辐射热,但是该专利并没有解决co2排放的问题。技术实现要素:本发明提供一种水泥窑炉烟气余热制冷辅助回收制取高纯co2的装置及方法,有效将烟气、压缩热等余热回收制冷技术和烟气低浓度co2回收提纯技术结合,降低能耗的同时,制取获得高纯液体co2,从而达到节能和co2减排的双重目的。一种水泥窑炉烟气余热制冷辅助回收制取高纯co2的装置,水泥窑和余热制冷设备连接,余热制冷设备一端和过滤组件连接,另一端和泵连接,一级膜分离组件的一端和过滤组件连接,另一端和风机连接,二级膜分离组件的一端和第一增压设备连接,另一端和第二增压设备连接,第二增压设备进一连接余热制冷设备,换热器的一端和泵连接,另一端和精馏塔连接。优选的是,所述过滤组件包括烟气经气体罐、风机、过滤器,所述余热制冷设备和气体罐、风机、过滤器依次连接。上述任一方案优选的是,所述第一增压设备为风机,第二增压设备为压缩机。上述任一方案优选的是,所述余热制冷设备包括发生器、冷凝器、蒸发器、吸收器及溶剂泵,余热制冷设备内置换热器,余热制冷设备所用的制冷工质为溴化锂和/或氨。上述任一方案优选的是,所述冷媒泵和换热器所用的冷媒介质为氨和/或乙二醇-水。上述任一方案优选的是,所述一级膜分离组件和二级膜分离组件尾气端均安装有用于尾气调节的自控阀门。一种采用上述的水泥窑炉烟气余热制冷辅助回收制取高纯co2装置的回收方法,包括以下步骤:步骤(1)、来自水泥窑窑尾烟气及co2成品气压缩余热经过余热制冷设备制冷,获得冷媒之后,冷媒经泵循环;步骤(2)、经余热回收后的烟气经回收增压、过滤后进入一级膜分离组件;步骤(3)、一级膜分离组件渗透出来的co2粗气经第一增压设备增压后进入二级膜分离组件,二级膜分离组件渗透出来的纯净co2成品气经第二增压设备增压后进入余热制冷设备;步骤(4)、co2成品气经充分余热回收后与冷媒在换热器中冷却并液化,而后进入精馏塔,经精馏后从精馏塔底部流出并获得高纯液态co2,尾气从精馏塔顶部排空。水泥窑窑尾烟气低浓度co2原料气为干式水泥窑尾烟,具体成分如下:二氧化碳co233.5%氮气n263.4%氧气o22.9%一氧化碳co0.2%上述任一方案优选的是,所述步骤(3)中所述第一增压设备为风机,第二增压设备为压缩机。上述任一方案优选的是,所述步骤(3)中第二增压设备的出口压力能够根据经换热器冷却的co2成品气温度实时调节,以确保co2被有效液化而不至于固化引起管路堵塞。上述任一方案优选的是,所述步骤(2)中经余热回收后的烟气经气体罐、风机回收增压、过滤器过滤后进入一级膜分离组件。有益效果(1)本发明公开一种水泥窑炉烟气余热制冷辅助回收制取高纯co2的装置,包括余热回收制冷系统、二氧化碳回收提纯系统和液化精馏系统几部分。其方步步骤包括,利用烟气和压缩机余热回收驱动制取-20~0℃之间的冷源(冷媒)。余热回收后的低浓度原料co2经气体缓冲罐、风机增压、过滤后进入一级膜提纯;一级膜渗透出来的co2粗气经风机二次增压进入二级膜提纯并获得98%以上的co2产品气;经压缩机增压、余热回收后的co2产品气与冷源(冷媒)在换热器中充分换热冷却成液态,经精馏塔精馏获得≥99.99%的高纯液态co2,尾气从精馏塔上部排空;冷媒经泵压缩循环使用。(2)本发明结合了烟气、压缩机余热回收和二氧化碳回收提纯技术,充分利用余热制冷来冷却(冷冻)co2产品气,并结合co2提纯技术,从而降低co2液化的分压,降低能耗和液态co2生产成本,达到节能和减排的双重目的。充分利用烟气和压缩机压缩余热制冷并获得冷源,并用于冷却二级膜分离组件提纯后的co2成品气,从而降低co2的液化分压,起到显著的节能作用。采用专利cn108148555b的实施案例可以提供-20度的低温,再结合co2的液化临界压力,可以说明本申请co2的液化分压显著降低,根据常温常压co2液化的压缩比和低温常压co2的压缩比对比,可以说明本申请的液化功率显著降低。(3)有效将烟气、压缩热等余热回收制冷技术和烟气低浓度co2回收提纯技术结合,降低能耗的同时,制取获得高纯液体co2,从而达到节能和co2减排的双重目的。适用于水泥窑、玻璃窑、石灰窑、燃煤电厂等领域的二氧化碳综合回收。附图说明图1为一种水泥窑炉烟气余热制冷辅助回收制取高纯co2的装置的结构示意图。图中:101、水泥窑;102、余热制冷设备;103、气体罐;104、风机;105、过滤器;106、一级膜分离组件;107、第一增压设备;108、二级膜分离组件;109、第二增压设备;110、换热器;111、泵;112、精馏塔。具体实施方式为了更好理解本发明的技术方案和优点,以下通过具体实施方式,并结合附图对本发明做进一步说明。在本发明的描述中,需要理解的是,术语“中心”、“纵向”、“横向”、“长度”、“宽度”、“厚度”、“上”、“下”、“前”、“后”、“左”、“右”、“竖直”、“水平”、“顶”、“底”“内”、“外”、“顺时针”、“逆时针”、“轴向”、“径向”、“周向”等指示的方位或位置关系为基于附图所示的方位或位置关系,仅是为了便于描述本发明和简化描述,而不是指示或暗示所指的装置或元件必须具有特定的方位、以特定的方位构造和操作,因此不能理解为对本发明的限制。实施例1如图1所示,本发明公开了一种水泥窑炉烟气余热制冷辅助回收制取高纯co2的装置,包括余热回收制冷、烟气co2回收提纯、co2加压及冷却液化精馏几部分,具体的水泥窑101和余热制冷设备102连接,余热制冷设备102一端和过滤组件连接,另一端和泵111连接,过滤组件包括烟气经气体罐103、风机104、过滤器105,所述余热制冷设备102和气体罐103、风机104、过滤器105依次连接。本申请中各个部件的连接均通过管路连接。余热制冷设备102包括发生器、冷凝器、蒸发器、吸收器及溶剂泵,余热制冷设备102内置换热器,余热制冷设备102所用的制冷工质为溴化锂和/或氨。余热制冷设备102的设置为本领域常用技术手段,具体可以参考专利申请号为cn110553420a一种基于溴化锂机组的氨吸收式制冷系统的具体设置。一级膜分离组件106的一端和过滤组件连接,另一端和风机107连接,二级膜分离组件108的一端和第一增压设备107连接,另一端和第二增压设备109连接,第二增压设备109进一步连接余热制冷设备102,换热器110的一端和泵111连接,另一端和精馏塔112连接。具体设置时,第一增压设备107为风机,第二增压设备109为压缩机。冷媒泵111和换热器110所用的冷媒介质为氨和/或乙二醇-水。一级膜分离组件106和二级膜分离组件108具体可以为基于聚酰胺所制的中空纤维膜。一级膜分离组件106和二级膜分离组件108尾气端均安装有用于尾气调节的自控阀门。充分利用烟气经压缩机109压缩余热制冷并获得冷源,并用于冷却二级膜分离组件108提纯后的co2成品气,从而降低co2的液化分压,起到显著的节能作用。实施例2一种采用实施例1的水泥窑炉烟气余热制冷辅助回收制取高纯co2装置的回收方法,包括以下步骤:步骤(1)、来自水泥窑101窑尾烟气及co2成品气压缩余热经过余热制冷设备102制冷,获得冷媒之后,冷媒经泵111循环;余热制冷设备102采用专利申请号为cn110553420a中的技术方案进行设置。步骤(2)、经余热回收后的烟气经气体罐103、风机104回收增压、过滤器105过滤后进入一级膜分离组件106;气体罐103设置压力100-110kpa之间,风机104设置出口压力≥150kpa,过滤器105过滤精度≤0.1μm。步骤(3)、一级膜分离组件106渗透出来的co2粗气经第一增压设备107增压至压力≥200kpa,后进入二级膜分离组件108,二级膜分离组件108渗透出来的纯净co2成品气经第二增压设备109增压至压力≥2.0mpa,后进入余热制冷设备102,具体设置时,第一增压设备107可以为风机,第二增压设备109可以为压缩机;第二增压设备109的出口压力能够根据经换热器110冷却的co2成品气温度实时调节,以确保co2被有效液化而不至于固化引起管路堵塞。co2液化的压力和温度数据,通常常温下(如20度)液化分压要求5.7mpa左右,而-20度时液化分压2.0mpa左右,0度时液化分压为3.5mpa左右。因为气体温度降低从而降低液化分压,越低的液化分压要求压缩机出口压力越低,从而电耗越低,从而达到节能的目的。步骤(3)中co2的液化压力变化受温度变化影响较大,温度(℃)-压力(mpa)数据具体如下:-20.000(℃),1.9696(mpa);-19.000(℃),2.0310(mpa);-18.000(℃),2.0938(mpa);-17.000(℃),2.1581(mpa);-16.000(℃),2.2237(mpa);-15.000(℃),2.2908(mpa);-14.000(℃),2.3593(mpa);-13.000(℃),2.4294(mpa);-12.000(℃),2.5010(mpa);-11.000(℃),2.5740(mpa);-10.000(℃),2.6487(mpa);-9.0000(℃),2.7249(mpa);-8.0000(℃),2.8027(mpa);-7.0000(℃),2.8821(mpa);-6.0000(℃),2.9632(mpa);-5.0000(℃),3.0459(mpa);-4.0000(℃),3.1303(mpa);-3.0000(℃),3.2164(mpa);-2.0000(℃),3.3042(mpa);-1.0000(℃),3.3938(mpa);0.0000(℃),3.4851(mpa);1.0000(℃),3.5783(mpa);2.0000(℃),3.6733(mpa);3.0000(℃),3.7701(mpa);4.0000(℃),3.8688(mpa);5.0000(℃),3.9695(mpa);6.0000(℃),4.0720(mpa);7.0000(℃),4.1765(mpa);8.0000(℃),4.2831(mpa);9.0000(℃),4.3916(mpa);10.000(℃),4.5022(mpa);11.000(℃),4.6149(mpa);12.000(℃),4.7297(mpa);13.000(℃),4.8466(mpa);14.000(℃),4.9658(mpa)。步骤(4)、co2成品气经充分余热回收后与冷媒在换热器110中冷却并液化,而后进入精馏塔112,经精馏后从精馏塔112底部流出并获得高纯液态co2,尾气从精馏塔112顶部排空。采用现有技术中专利cn108148555b的实施案例提供-20度的低温环境,再结合co2的液化临界压力,可以说明本申请co2的液化分压显著降低,根据常温常压co2液化的压缩比和低温常压co2的压缩比对比,可以说明本申请的液化功率显著降低。常温20度,co2的液化分压~5.7mpa,而-20度co2的液化分压只需要~1.97mpa,这也进一步说明本申请能够达到节能和co2减排的双重目的。-20度、0度、20度时co2的液化分压如下表1所示:表1温度液化分压20℃5.72mpa0℃3.48mpa-20℃1.97mpa需要说明的是,以上各实施例仅用以说明本发明的技术方案,而非对其限制;尽管参照前述各实施例对本发明进行了详细的说明,本领域的普通技术人员应当理解:其依然可以对前述各实施例所记载的技术方案进行修改,或者对其中部分或者全部技术特征进行等同替换;而这些修改或者替换,并不使相应技术方案的本质脱离本发明各实施例技术方案的范围。当前第1页12