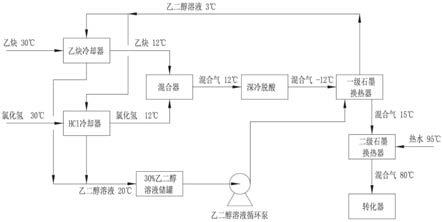
1.本公开涉及聚氯乙烯生产工艺,具体提供一种氯化氢、乙炔气体脱水工艺中冷量回收利用系统。
背景技术:2.这里的陈述仅提供与本公开有关的背景信息,而不必然构成现有技术。
3.聚氯乙烯是世界上产量最大的通用塑料,应用非常广泛。在建筑材料、工业制品、日用品、地板革、地板砖、人造革、管材、电线电缆、包装膜、瓶、发泡材料、密封材料、纤维等方面均有广泛应用。在现有技术中也常常加入其他成分来增强其耐热性,韧性,延展性等。它是当今世界上深受喜爱、颇为流行并且也被广泛应用的一种合成材料。它的全球使用量在各种合成材料中高居第二。
4.随着我国工业的发展,国内聚氯乙烯产量急剧增加,目前常用工艺为将乙炔与氯化氢气体初步冷却后混合,然后进入深冷脱酸系统冷却,经过酸雾捕集器脱酸处理后,送入热水预热器进行加热,在转化器中合成氯乙烯单体,单体经聚合生成聚氯乙烯。氯乙烯单体生产耗能量大,尤其是气体冷却过程中消耗大量的冷量,而加热过程中又消耗大量热量,为此,本公开利用深冷脱酸后混合气的冷量对乙炔和氯化氢气体进行初步冷却,现有技术中提供了一种聚氯乙烯生产中的乙炔与氯化氢混合气脱水节能装置,但发明人发现,一方面,因气体与气体换热总传热系数约10~50w/(m2·
℃),换热系数较低,现有技术中若采用气体与气体换热,则需要较大的换热器才能满足换热需求,且混合气管道较粗,投资较高,在原有装置上进行改造时,换热器及管道尺寸较大造成设备安装及配管困难,甚至无法安装。另一方面,混合气压力较低,需另外增加风机进行增压,增加电耗,且混合气中含有氯化氢及乙炔,需要耐酸及防爆风机,风机投资高,选型困难,无法适用于正常生产。
技术实现要素:5.针对现有技术中氯化氢和乙炔气体先用7℃冷水初步冷却,混合后经深冷脱酸后的混合气体再用热水加热升温,此过程没有进行换热网络优化,冷量和热量使用不合理,造成能量极大浪费。另一方面,深冷脱酸后的低温混合气直接送入热水预热器进行加热,由于设备遭受的温差变化较大,不利于设备的长周期运行。
6.本公开一个或一些实施方式中,提供一种氯化氢、乙炔气体脱水工艺中冷量回收利用系统,包括依次连接的混合单元、深冷脱酸单元和换热单元;
7.所述混合单元包括乙炔冷却器,氯化氢冷却器以及混合器,所述混合器将乙炔冷却器中的乙炔与氯化氢冷却器中的氯化氢混合,并将混合物输送至深冷脱酸单元,所述乙炔冷却器与氯化氢冷却器中的冷介质为乙二醇溶液;
8.所述深冷脱酸单元包括石墨冷却器及酸雾捕集器,所述酸雾捕集器用于去除混合物中的盐酸雾,所述石墨冷却器中的冷介质为冷冻盐水。
9.所述换热单元将深冷脱酸单元出口的气体混合物加热,所述换热单元分为一级换
热单元与二级换热单元,一级换热单元将混合物初步加热,二级换热单元将混合物加热至最终温度,一级换热单元中的热介质来自于乙炔冷却器和氯化氢冷却器中经过换热的冷介质。
10.本公开一个或一些实施方式中,提供一种氯化氢、乙炔气体脱水工艺中冷量回收利用工艺,包括如下步骤:将乙炔与氯化氢分别进行冷却,冷却后进入混合器中混合成混合物,混合后的混合物进入深冷脱酸单元中进行脱酸处理,深冷脱酸后的混合物进入换热单元换热,所述换热单元将混合物加热后出料,所述换热单元中的热介质来自于乙炔与氯化氢冷却换热后的冷介质。
11.上述技术方案中的一个或一些技术方案具有如下优点或有益效果:
12.1)本公开优化了换热工艺,将深冷脱酸后混合气与氯化氢、乙炔气体进行热交换,采用乙二醇水溶液作为换热介质,乙二醇水溶液与深冷脱酸后的混合气进行换热后,分别输送至乙炔冷却器和氯化氢冷却器用于冷却乙炔和氯化氢,降低了能耗。
13.2)本公开在改进工艺的同时,因工艺条件改变,重新规划了工艺的适用温度,规划后的温度使冷热介质恰好无需进行外部热交换,彻底实现自循环使用。改进工艺后,乙炔气体中含水量降低,从而降低了深冷脱酸系统中废酸产出量,节约废酸处理成本。
14.3)本公开可以降低一级石墨换热器遭受的温差变化,从而使设备可以长周期运行。
附图说明
15.构成本公开一部分的说明书附图用来提供对本公开的进一步理解,本公开的示意性实施例及其说明用于解释本公开,并不构成对本公开的不当限定。
16.图1为本公开改造前实施的生产工艺流程图。
17.图2为本公开实施例生产工艺流程图。
具体实施方式
18.下面将对本公开实施例中的技术方案进行清楚、完整地描述,显然,所描述的实施例仅是本公开的一部分实施例,而不是全部实施例。基于本公开的实施例,本领域技术人员在没有做出创造性劳动前提下所获得的所有其它实施例,都属于本公开保护的范围。
19.针对现有技术中将深冷脱酸后的低温混合气直接送入热水预热器进行加热时,不仅浪费冷量,而且需要大量的热能才能将低温混合气加热到设定温度,能耗较大。现有技术中采用气体与气体换热,由于气体与气体之间换热系数小,导致换热器过大,混合气管道较粗,投资较大,配管困难,且混合气压力低,需要风机增压,混合气腐蚀性高,对换热器器壁带来腐蚀。
20.本公开一个或一些实施方式中,提供一种氯化氢、乙炔气体脱水工艺中冷量回收利用系统,包括依次连接的混合单元、深冷脱酸单元和换热单元;
21.所述混合单元包括乙炔冷却器,氯化氢冷却器以及混合器,所述混合器将乙炔冷却器中的乙炔与氯化氢冷却器中的氯化氢混合,并将混合物输送至深冷脱酸单元,所述乙炔冷却器与氯化氢冷却器中的冷介质为乙二醇溶液;
22.所述深冷脱酸单元包括石墨冷却器及酸雾捕集器,所述酸雾捕集器用于去除混合
物中的盐酸雾,所述石墨冷却器中的冷介质为冷冻盐水。
23.所述换热单元将深冷脱酸单元出口的气体混合物加热,所述换热单元分为一级换热单元与二级换热单元,一级换热单元将混合物初步加热,二级换热单元将混合物加热至最终温度,一级换热单元中的热介质来自于乙炔冷却器和氯化氢冷却器中经过换热的冷介质。
24.本公开优化了换热工艺,将深冷脱酸后混合气与氯化氢、乙炔气体进行热交换,采用乙二醇水溶液作为换热介质,乙二醇水溶液与深冷脱酸后的混合气进行换热后,分别输送至乙炔冷却器和氯化氢冷却器用于冷却乙炔和氯化氢,降低了能耗。
25.优选的,所述乙炔冷却器与氯化氢冷却器中的冷介质均为乙二醇。气体与气体换热总传热系数约10~50w/(m2·
℃),气体与水换热总传热系数约20~300w/(m2·
℃),显然气液传热系数远大于气体之间的传热系数,本公开采用乙二醇水溶液与气体换热,与现有工艺中冷水与气体换热的总传热系数相近,换热器经计算复核后可以利用原换热器,管道也利用原有管道,无需更换设备及管道,改造简单,投资少。
26.且乙二醇溶液为工业中常用的防冻液,容易获得。
27.优选的,所述一级换热单元为一级石墨换热器和乙二醇溶液储罐,乙二醇溶液储罐为一级石墨换热器提供热介质,所述一级石墨换热器与深冷脱酸单元相连,所述乙二醇溶液储罐分别连接乙炔冷却器和氯化氢冷却器中冷介质出口。
28.本公开将现有工艺中的钢制预热器换成石墨预热器,防止深冷脱酸后的混合气夹带有微量氯化氢,对设备产生腐蚀。
29.一级石墨换热器与乙二醇溶液储罐之间增加两台循环泵,循环泵一开一备。来自储罐的乙二醇溶液与深冷脱酸后的混合气在一级石墨换热器进行换热。
30.优选的,所述一级石墨换热器热介质出口分别连接乙炔冷却器与氯化氢冷却器的冷介质入口。
31.优选的,所述二级换热单元为二级石墨换热器,初步预热后的混合物进入二级石墨换热器,所述二级石墨换热器中热介质为热水。
32.优选的,所述换热单元还与转化器相连。
33.本公开一个或一些实施方式中,提供一种氯化氢、乙炔气体脱水工艺中冷量回收利用工艺,包括如下步骤:将乙炔与氯化氢分别进行冷却,冷却后进入混合器中混合成混合物,混合后的混合物进入深冷脱酸单元中进行脱酸处理,深冷脱酸后的混合物进入换热单元换热,所述换热单元将混合物加热后出料,所述换热单元中的热介质来自于乙炔与氯化氢冷却换热后的冷介质。
34.优选的,所述冷介质为乙二醇溶液,所述乙二醇溶液进入乙炔冷却器和氯化氢冷却器时的温度为2
‑
5℃,优选为3℃;
35.优选的,所述乙二醇溶液从乙炔冷却器和氯化氢冷却器中换热后温度为18
‑
25℃,优选为20℃;
36.优选的,所述乙炔和氯化氢进入冷却器的初始温度为25
‑
35℃,优选为30℃。
37.优选的,所述乙炔和氯化氢冷却后温度为10
‑
15℃,优选为12℃;
38.所述乙炔与氯化氢混合物深冷脱酸后温度为
‑
20~
‑
8℃,优选为
‑
12℃。
39.优选的,还包括介质循环步骤:将换热单元中换热后的热介质用作乙炔和氯化氢
冷却过程中的冷介质。
40.优选的,所述换热分两步进行,第一步换热介质来自于乙炔与氯化氢冷却换热后的冷介质,换热后混合物温度为10
‑
20℃,优选为15℃,第二步换热介质为热水,换热后混合物温度为75
‑
90℃,进一步优选为80℃,优选的,热水温度为90
‑
100℃,进一步优选为95℃。
41.氯化氢及乙炔气体首先进行初步冷却,气体冷却温度越低,气体中水含量越低,这样就降低了深冷脱酸系统负荷,减少冷冻盐水用量。本公开对比例中的方案受限于冷水温度(7℃)及换热器换热面积,氯化氢及乙炔气体出口温度无法进一步降低。本公开使用乙二醇水溶液温度为3℃(若采用0℃以下,气体中的水可能结冰,堵塞管道;本技术采用3℃,避免氯化氢及乙炔气体中水结冰),可以进一步降低氯化氢及乙炔气体出口温度至12℃,这样可以充分回收利用系统中的冷量,降低能耗。另一方面,乙炔气体中含水量降低,降低了深冷脱酸系统中废酸产出量,节约废酸处理成本。
42.另外,对比例中一级石墨换热器采用95℃热水加热,混合气出口温度为70℃;本技术采用20℃乙二醇水溶液换热,混合气出口温度为15℃,因工艺条件改变,无法采用原来的温度。本公开可以降低一级石墨换热器遭受的温差变化,从而使设备可以长周期运行。
43.实施例1
44.本实施例提供一种氯化氢、乙炔气体脱水工艺中冷量回收利用系统,包括依次连接的混合单元、深冷脱酸单元、换热单元和转化器;
45.所述混合单元包括乙炔冷却器,氯化氢冷却器以及混合器,所述混合器将乙炔冷却器中的乙炔与氯化氢冷却器中的氯化氢混合,并将混合物输送至深冷脱酸单元,所述乙炔冷却器与氯化氢冷却器中的冷介质为乙二醇溶液;
46.所述深冷脱酸单元包括石墨冷却器及酸雾捕集器,所述酸雾捕集器用于去除混合物中的盐酸雾,所述石墨冷却器中的冷介质为冷冻盐水。
47.所述换热单元将深冷脱酸单元出口的气体混合物加热,所述换热单元包括一级石墨换热器与二级石墨换热器,一级石墨换热器将混合物初步加热,二级石墨换热器将混合物加热至最终温度,一级石墨换热器中的热介质来自于乙炔冷却器和氯化氢冷却器中经过换热的冷介质。所述二级石墨换热器中热介质为热水。
48.所述一级石墨换热器还与乙二醇溶液储罐相连,所述乙二醇溶液储罐分别连接乙炔冷却器和氯化氢冷却器中冷介质出口。
49.所述一级石墨换热器与深冷脱酸单元相连。
50.实施例2
51.如图2所示,本实施例提供一种氯化氢、乙炔气体脱水工艺中冷量回收利用工艺,所述工艺在实施例1所述的氯化氢、乙炔气体脱水工艺中冷量回收利用系统中进行,包括如下步骤:
52.将30℃的乙炔与氯化氢在冷却器中分别进行冷却,冷却器中介质为3℃的乙二醇,冷却后的乙炔与氯化氢均为12℃,冷却后进入混合器中混合成混合物,混合后的混合物进入深冷脱酸单元中进行脱酸处理,深冷脱酸后的混合物为
‑
12℃,然后进入换热单元换热,所述换热分两步进行,第一步换热在一级石墨换热器中进行,换热后混合物温度为15℃,第二步换热在二级石墨换热器中进行,换热后混合物温度为80℃,热水温度为95℃。
53.实施例3
54.如图2所示,本实施例提供一种氯化氢、乙炔气体脱水工艺中冷量回收利用工艺,所述工艺在实施例1所述的氯化氢、乙炔气体脱水工艺中冷量回收利用系统中进行,包括如下步骤:
55.将30℃的乙炔与氯化氢在冷却器中分别进行冷却,冷却器中介质为5℃的乙二醇,冷却后的乙炔与氯化氢均为10℃,冷却后进入混合器中混合成混合物,混合后的混合物进入深冷脱酸单元中进行脱酸处理,深冷脱酸后的混合物为
‑
15℃,然后进入换热单元换热,所述换热分两步进行,第一步换热在一级石墨换热器中进行,换热后混合物温度为10℃,第二步换热在二级石墨换热器中进行,换热后混合物温度为85℃,热水温度为95℃。
56.对比例1
57.如图1所示,在聚氯乙烯合成转化工艺中,来自界区外的乙炔和氯化氢气体温度均为30℃,使用7℃冷水分别将其冷却至18℃进行初步脱水,初步脱水后进入混合器混合,然后进入深冷脱酸系统与
‑
35℃冷冻盐水进行热交换,利用氯化氢吸水性强的性质,充分去除混合气中的水分。深冷后的混合气温度为
‑
12℃,进入一级石墨换热器与95℃热水进行换热至70℃,再进入钢制预热器与95℃热水进行换热至80℃以上,最后进入转化器进行转化反应。
58.从对比例1的工艺来看,进入界区的混合气体先用7℃冷水降温初步脱水,深冷脱酸后的混合气体(
‑
12℃)再用热水加热升温,此过程没有进行换热网络优化,冷量和热量使用不合理,造成能量极大浪费。
59.而通过实施例1
‑
3的改造,新工艺不再使用7℃冷水,同时降低了热水用量,公司每年可以节约电费100万元以上。
60.以上所揭露的仅为本公开的优选实施例而已,当然不能以此来限定本公开之权利范围,因此依本公开申请专利范围所作的等同变化,仍属本公开所涵盖的范围。