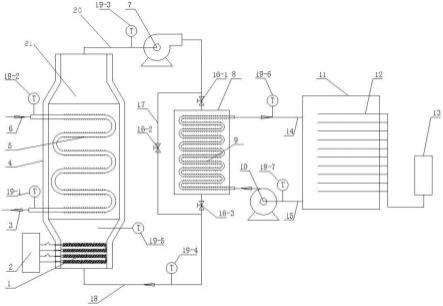
1.本实用新型涉及石油化工工艺加热炉领域,具体而言,涉及一种储能式电加热二氧化碳零排放的加热炉装置。
背景技术:2.石化产业是国民经济的重要支柱产业,也是资源型和能源型产业,目前生产石化产品的主要原料是石油、天然气、煤炭等化石资源,其石化产品的生产过程必然伴有二氧化碳的排放,这样的属性也决定了石化产业的碳排放量居工业领域的前列,特别是石油化工产业中的工艺加热炉,其目前仍是石化产业中的主要能耗装置。
3.现有技术中的工艺加热炉对工艺介质进行加热的过程,往往依靠燃烧器火焰加热工艺介质,不仅消耗大量的化石能源,而且对减碳排放形成巨大压力。随着“碳达峰,碳中和”政策的大力推进,石化产业也会尽可能地减少化石能源消耗,最终实现二氧化碳零排放。相应的,石化工艺加热炉也需要科学制定“碳达峰与碳中和”的实施方案及工艺技术突破。
4.为此,针对石油化工产业中现有的工艺加热炉,如何尽可能地降低工艺加热炉的化石能源消耗,最终实现工艺加热炉的零碳排放,便成了石化产业从业者应着手去解决的重要问题之一。
技术实现要素:5.有鉴于此,本实用新型旨在提出一种储能式电加热炉装置,以解决现有技术中工艺加热炉化石能源消耗较大,不利于实现二氧化碳零排放的问题。
6.为达到上述目的,本实用新型的技术方案是这样实现的:
7.一种储能式电加热炉装置,包括电加热熔盐储罐、熔盐换热器、工艺加热炉,所述熔盐换热器内设置第一换热通路、第二换热通路,所述工艺加热炉设置第三换热通路、第四换热通路,所述电加热熔盐储罐通过熔盐管路与第一换热通路连通,所述第三换热通路通过热风管路与第二换热通路连通;在熔盐换热器内,第一换热通路内的高温熔盐与第二换热通路内的热风进行换热;在工艺加热炉中,第三换热通路内的热风与第四换热通路内的工艺介质换热。
8.进一步的,所述热风管路包括热风旁路管线,所述热风旁路管线与熔盐换热器并联设置。
9.进一步的,所述第三换热通路的入口处设置电加热装置。
10.进一步的,所述熔盐换热器为管壳式换热器,第一换热通路为管程或壳程,第二换热通路为壳程或管程。
11.进一步的,所述熔盐换热器内设置换热管,所述换热管为第一换热通路,所述熔盐换热器的壳程为第二换热通路。
12.进一步的,所述熔盐管路包括低温熔盐管道、高温熔盐管道,所述低温熔盐管道分
别与换热管的出口、电加热熔盐储罐的入口连接,所述高温熔盐管道分别与电加热熔盐储罐的出口、换热管的入口连接,所述低温熔盐管道和/或高温熔盐管道中设置熔盐泵。
13.进一步的,所述工艺加热炉的内部具有炉腔,所述炉腔中设置炉管,所述炉管为第四换热通路,所述炉腔为第三换热通路。
14.进一步的,所述热风管路包括热风出炉管线、热风入炉管线,所述热风出炉管线分别与炉腔的出口、熔盐换热器的壳程入口连接,所述热风入炉管线分别与熔盐换热器的壳程出口、炉腔的入口连接,所述热风出炉管线和/或热风入炉管线中设置风机。
15.进一步的,所述热风出炉管线的出口处设置进风阀,所述热风入炉管线的入口处设置回风阀,所述热风旁路管线的入口与进风阀的入口端连接,所述热风旁路管线的出口与回风阀的出口端连接,所述热风出炉管线中设置旁路阀。
16.进一步的,所述电加热熔盐储罐内具有容纳腔,所述容纳腔中设置热电阻,用于对容纳腔中的熔盐进行电加热。
17.相对于现有技术,本实用新型所述的一种储能式电加热炉装置具有以下优势:
18.本实用新型所述的一种储能式电加热炉装置,与现有的燃烧加热工艺介质的工艺加热炉相比,本技术完全无需使用传统的化石燃料,仅通过利用电能便能够实现对工艺介质的加热,能够实现工艺加热炉的零碳排放。同时,也正是由于工艺加热炉摒弃了传统化石燃料的燃烧加热,使得工艺加热炉内不存在火焰,没有局部高温的产生,使得工艺介质受热更加均匀,避免了工艺介质因局部超温析碳、结焦等情况的发生,有利于提高工艺加热炉的使用寿命,降低工艺加热炉的维护成本。
19.此外,本技术采用储热技术,电加热熔盐储罐与熔盐换热器利用电力谷段将电能转化为热能进行储存,并根据实际生产需要通过熔盐换热器将储存的热量缓慢释放出来,能够有效降低装置的用电成本。同时,本技术中无论是熔盐、热风均在整个装置体系中实现了循环使用,使得整个装置体系没有污染物排放,加热炉可实现零污染、零排放的环保要求。
附图说明
20.构成本实用新型的一部分的附图用来提供对本实用新型的进一步理解,本实用新型的示意性实施例及其说明用于解释本实用新型,并不构成对本实用新型的不当限定。在附图中:
21.图1为本实用新型实施例所述的一种储能式电加热炉装置的结构示意图。
22.附图标记说明:
23.1、电加热装置;2、热风高压电源控制柜;3、工艺介质出口;4、工艺加热炉;5、炉管;6、工艺介质入口;7、风机;8、熔盐换热器;9、换热管;10、熔盐泵;11、电加热熔盐储罐;12、热电阻;13、熔盐罐高压电源控制柜;14、低温熔盐管道;15、高温熔盐管道;16-1、进风阀;16-2、旁路阀;16-3、回风阀;17、热风旁路管线;18、热风入炉管线;19-1、第一温度检测装置;19-2、第二温度检测装置;19-3、第三温度检测装置;19-4、第四温度检测装置;19-5、第五温度检测装置;19-6、第六温度检测装置;19-7、第七温度检测装置;20、热风出炉管线;21、炉腔。
具体实施方式
24.下文将使用本领域技术人员向本领域的其它技术人员传达他们工作的实质所通常使用的术语来描述本公开的实用新型概念。然而,这些实用新型概念可体现为许多不同的形式,因而不应视为限于本文中所述的实施例。
25.需要说明的是,在不冲突的情况下,本实用新型中的实施例及实施例中的特征可以相互组合。同时,本实用新型中“高温”、“低温”的用词,并非指绝对温度,而是用于表示同一个物质在加热前后的相对温度状态,例如被加热后称为“高温”,放热后称为“低温”。
26.下面将参考附图并结合实施例来详细说明本实用新型。
27.在现有技术中,石油化工产业中的工艺加热炉对工艺介质进行加热的过程,往往依靠燃烧器火焰加热工艺介质,不仅消耗大量的化石能源,而且对减碳排放形成巨大压力。
28.为了解决现有技术中工艺加热炉化石能源消耗较大,不利于实现二氧化碳零排放的问题,本实施例提出一种储能式电加热炉装置,如附图1所示,所述储能式电加热炉装置包括电加热熔盐储罐11、熔盐换热器8、工艺加热炉4,所述熔盐换热器8内设置第一换热通路、第二换热通路,所述工艺加热炉4设置第三换热通路、第四换热通路,所述电加热熔盐储罐11通过熔盐管路与第一换热通路连通,所述第三换热通路通过热风管路与第二换热通路连通,使得在熔盐换热器8内,第一换热通路内的高温熔盐与第二换热通路内的热风进行换热,以提高热风温度;在所述工艺加热炉4中,第三换热通路内的热风与第四换热通路内的工艺介质换热,以提高工艺介质的温度。
29.本技术利用电能对电加热熔盐储罐11中的熔盐进行加热升温,得到高温熔盐,高温熔盐进入第一换热通路之后,与第二换热通路内的热风进行换热,得到低温熔盐、高温热风,然后低温熔盐回到电加热熔盐储罐11中加热,高温热风进入第三换热通路与第四换热通路内的工艺介质进行换热,得到低温热风、高温工艺介质,低温热风回到熔盐换热器8继续与高温熔盐换热,高温工艺介质则从工艺加热炉4中输出,供下游工序的生产使用。从而与现有的燃烧加热工艺介质的工艺加热炉相比,本技术完全无需使用传统的化石燃料,仅通过利用电能便能够实现对工艺介质的加热,能够实现工艺加热炉的零碳排放。同时,也正是由于工艺加热炉4摒弃了传统化石燃料的燃烧加热,使得工艺加热炉4内不存在火焰,没有局部高温的产生,使得工艺介质受热更加均匀,避免了工艺介质因局部超温析碳、结焦等情况的发生,有利于提高工艺加热炉4的使用寿命,降低工艺加热炉4的维护成本。
30.此外,本技术采用储热技术,电加热熔盐储罐11与熔盐换热器8利用峰谷电的谷段,一般时间控制在22:00-次日8:00之间使用,利用电力谷段将电能转化为热能进行储存,并根据实际生产需要通过熔盐换热器8将储存的热量缓慢释放出来,能够有效降低装置的用电成本。同时,本技术中无论是熔盐、热风均在整个装置体系中实现了循环使用,使得整个装置体系没有污染物排放,加热炉可实现零污染、零排放的环保要求。
31.所述熔盐包括碳酸盐、氯化盐、硝酸盐中的至少一种,其具有热容量大、粘度低、热稳定性优良、使用温度范围宽、原料来源广成本低等优势。
32.所述热风包括二氧化碳、氮气、惰性气体中的至少一种气体,不仅比热容高,换热效率高,而且不含水,不含硫,无腐蚀,能够避免相关结构发生氧化、腐蚀等情况,有利于提高相关设备的使用寿命。
33.对于电加热熔盐储罐11而言,所述电加热熔盐储罐11内具有容纳腔,用于为熔盐
的存放、加热提供容纳空间,所述容纳腔中设置热电阻12,用于对容纳腔中的熔盐进行电加热。所述电加热熔盐储罐11外设置熔盐罐高压电源控制柜13,所述熔盐罐高压电源控制柜13与热电阻12连接,用于控制热电阻12的电加热功率。
34.对于熔盐换热器8而言,可以采用常规的换热器结构,使得第一换热通路与第二换热通路之间进行换热。在本技术中,所述熔盐换热器8优选为管壳式换热器,第一换热通路为管程或壳程,相应的,第二换热通路为壳程或管程。
35.考虑到本技术中熔盐、热风的物质性质,所述熔盐换热器8内设置换热管9,第一换热通路为管程,即第一换热通路为换热管9,第二换热通路为壳程,所述换热管9优选为翅片管结构,以提高换热效率。此外,在熔盐换热器8内,壳程中的热风流动方向与换热管9的延伸方向垂直。
36.所述熔盐管路包括低温熔盐管道14、高温熔盐管道15,所述低温熔盐管道14分别与换热管9的出口、电加热熔盐储罐11的入口连接,所述高温熔盐管道15分别与电加热熔盐储罐11的出口、换热管9的入口连接,所述低温熔盐管道14和/或高温熔盐管道15中设置熔盐泵10,用于为熔盐的移动提供动力支持。此外,所述低温熔盐管道14、高温熔盐管道15均设置高温蒸汽伴热管线,以防止熔盐在熔盐管路内凝固堵塞管道。
37.对于工艺加热炉4而言,所述工艺加热炉4同样可以为常规的换热器结构,使得第三换热通路、第四换热通路之间进行换热。但考虑到已建成设备的改造或更换成本,本技术建议仍以传统的工艺加热炉结构进行应用,即所述工艺加热炉4的内部具有炉腔21,所述炉腔21中设置炉管5,所述炉管5与工艺加热炉4外部的工艺介质管线连通,所述炉管5可以视为第四换热通路,所述炉腔21可以视为第三换热通路。所述工艺加热炉4的炉体外壁设置保温结构,使得外壁温度控制在60℃以下,有效降低热量损失。
38.优选的,炉管5按照卧式水平布置,包括多个卧式水平排列的管体,任意相邻的两个管体之间通过180度弯头连接。炉管5内的工艺介质采用上进下出的输送方式。炉管5可以为光管、翅片管、钉头管,优选采用翅片管结构,以提高换热效率。炉管5的材质采用cr5mo或碳钢管。热风由工艺加热炉4的底部进入,所述炉腔21内的热风流动方向为自下至上垂直于炉管5的方向。
39.此外,所述炉管5也可以采用竖管布置,优选为采用条状翅片结构,此时炉腔21内的热风流动方向与炉管5平行,
40.考虑到实际应用过程中电加热熔盐储罐11的停机检修、电加热熔盐储罐11能量不足、待加热工艺介质过多等情况,所述储能式电加热炉装置需要设置额外的热量补给设备。在本技术中,所述第三换热通路的入口处设置电加热装置1,通过利用电加热来对进入工艺加热炉4内的热风补充热量,一方面可以在开车阶段,通过电加热装置1的辅助加热作用,来使设备尽早达到平稳运行状态,另一方面可以在电加热熔盐储罐11停机或热量供给不足时,通过电加热装置1提供工艺加热炉4内的热量补充,以保障整套装置的正常运行。在电加热熔盐储罐11正常运行,热量供给充足的情况下,电加热装置1处于停机状态。所述工艺加热炉4外设置热风高压电源控制柜2,所述热风高压电源控制柜2与电加热装置1连接,用于控制电加热装置1的电加热功率。具体的,所述炉腔21的入口处设置电加热装置1,所述电加热装置1的电阻件采用0cr25a15材质,耐温1300℃,电阻件缠绕在纯刚玉或石英管外表面,纯刚玉或石英管热电阻丝起支撑作用,电阻件采用多组结构,高压电源采用10kv-66kv高压
电源。热电阻与炉体采用高压绝缘,保证安全性。从而本技术通过设置电加热装置1,使得整套装置操作更灵活,设备开车更为高效,也能够在个别设备检修时仍保持装置的正常运作,同时也能够有效地对加热工艺介质的实际流量波动进行热量补给。同时,在装置开车阶段,通过电加热装置1对热风加热,来对熔盐换热器8的换热管9预热,能够有效防止熔盐因温度偏低而堵塞管道。
41.对于工艺加热炉4与熔盐换热器8之间的连接而言,所述热风管路包括热风出炉管线20、热风入炉管线18,所述热风出炉管线20分别与炉腔21的出口、熔盐换热器8的壳程入口连接,所述热风入炉管线18分别与熔盐换热器8的壳程出口、炉腔21的入口连接,所述热风出炉管线20和/或热风入炉管线18中设置风机7,用于为热风的流动提供动力支持,使得热风能够在熔盐换热器8、工艺加热炉4之间进行循环换热。
42.考虑到设备开车、日常检修等情况,所述热风管路包括热风旁路管线17,所述热风旁路管线17与熔盐换热器8并联设置。具体的,所述热风出炉管线20的出口处设置进风阀16-1,所述热风入炉管线18的入口处设置回风阀16-3,所述热风旁路管线17的入口与进风阀16-1的入口端连接,所述热风旁路管线17的出口与回风阀16-3的出口端连接,所述热风出炉管线20中设置旁路阀16-2。从而通过与熔盐换热器8并联设置热风旁路管线17,使得热风可以流经热风旁路管线17和/或熔盐换热器8,在设备开车阶段、或熔盐换热器8、电加热熔盐储罐11等设备检修时,可以关闭进风阀16-1、回风阀16-3,打开旁路阀16-2,让热风走热风出炉管线20回到工艺加热炉4,并通过电加热装置1对热风进行加热。在正常情况下,电加热熔盐储罐11能够提供足够的热量支持,可以关闭旁路阀16-2,打开进风阀16-1、回风阀16-3,让热风正常经过熔盐换热器8与高温熔盐换热。从而本技术通过设置热风旁路管线17,使得整套装置操作更灵活,设备开车更为高效,也能够在个别设备检修时仍保持装置的正常运作,同时也能够有效地对加热工艺介质的实际流量波动进行热量补给或缓冲。
43.为了便于对相关物质的温度情况进行调控,所述储能式电加热炉装置中设置多个温度检测装置,例如:炉管5的出口设置第一温度检测装置19-1,用于检测流出炉管5的工艺介质温度;炉管5的入口设置第二温度检测装置19-2,用于检测进入炉管5的工艺介质温度;热风出炉管线20中设置第三温度检测装置19-3,用于检测流入熔盐换热器8的热风温度,所述第三温度检测装置19-3优选被设置在风机7的入口处,用于检测、调控进入风机7的温度,防止超温损坏风机7;热风入炉管线18中设置第四温度检测装置19-4,用于检测流出熔盐换热器8的热风温度,所述炉腔21内设置第五温度检测装置19-5,用于检测炉腔21内的热风温度,所述低温熔盐管道14中设置第六温度检测装置19-6,用于检测流出熔盐换热器8的熔盐温度,所述高温熔盐管道15中设置第七温度检测装置19-7,用于检测流入熔盐换热器8的熔盐温度。从而通过设置相应的温度检测装置,使得整套设备能够根据实际的相关物料温度,对物料流量、加热功率等工艺参数进行及时调控。
44.在本技术中,以申请人实际投产应用的原料油加热项目为一个实施例,所述工艺介质为原料油,工艺介质进入工艺加热炉4时的温度为270℃,在与高温热风换热后,工艺介质被加热至365℃后输送出工艺加热炉4。热风在工艺加热炉4中的入炉温度控制在500℃左右,出炉温度控制在340℃左右。熔盐温度控制在400℃~800℃之间,优选的,在熔盐换热器8中熔盐的进入温度为800℃,送出温度为400℃。
45.作为本技术的另一个实施例,所述工艺介质为重质油料,油料粘度高、易结焦、易
裂解。工艺介质进入工艺加热炉4时的温度为160℃,在与高温热风换热后,工艺介质被加热至500℃后输送出工艺加热炉4。热风在工艺加热炉4中的入炉温度控制在650℃左右,出炉温度控制在400℃左右。熔盐温度控制在420℃~900℃之间,优选的,在熔盐换热器8中熔盐的进入温度为900℃,送出温度为420℃。
46.以上所述仅为本实用新型的较佳实施例而已,并不用以限制本实用新型,凡在本实用新型的精神和原则之内,所作的任何修改、等同替换、改进等,均应包含在本实用新型的保护范围之内。