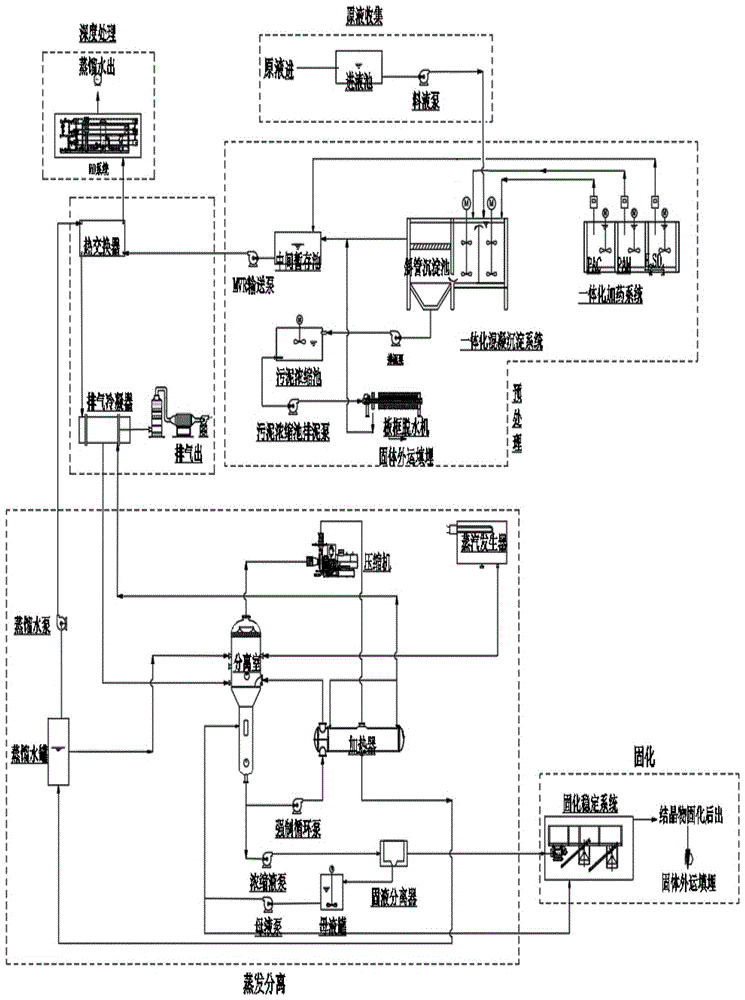
本发明属于垃圾废水处理
技术领域:
,特别涉及一种基于pmvr-zld的垃圾渗滤液处理工艺。
背景技术:
:垃圾渗滤液是垃圾填埋过程中在填埋库区范围内所产生的污水,此外还包括洗车废水及冲洗道路废水等;影响渗滤液产生量的因素是多方面的,其中垃圾渗滤液的主要来源为降雨渗入,此外还有垃圾本身所含的水分及厌氧分解所产生的废液,同时填埋年限、垃圾压实度、垃圾性状、垃圾堆体的孔隙含水率、大气蒸发、是否有地下水渗入等都会对渗滤液的水量产生一定的影响。垃圾渗滤液的水质相当复杂,一般含有高浓度的cod、重金属盐、ss及氨氮,具有高硬度等特点;垃圾渗滤液中的codcr、bod5浓度最高可达几万mg/l,与城市污水相比,浓度非常高。高浓度的垃圾渗滤液主要是在酸性发酵阶段产生,ph达到或略低于7,低分子脂肪酸的cod占cod总量的80%以上,bod5与cod比值为0.5~0.6。而填埋场垃圾渗滤液水质变化大,填埋场渗滤液的主要成份有下述四类:①常见元素和离子,如cd、mg、fe、na、nh3-n、碳酸根、氯离子等;②微量金属,如mn、cr、ni、pb等;③有机物,常用toc、cod来计量,酚等也可以单独计量;④微生物。渗滤液的性质与填埋废物的种类、性质及填埋方式等许多因素有关,化学成分变化较大,其浓度和性质随时间呈高度的动态变化关系,主要取决于填埋场的使用年限和取样时填埋场所处的阶段;在填埋的初期,渗滤液中的有机酸浓度较高,而挥发性有机酸含量不到1%,随着时间的推移,挥发性有机酸的比例将增加;在填埋场的酸性阶段,其ph值较低,而bod5、toc、cod、营养物和重金属的含量较高;在填埋场的产甲烷阶段,ph值介于6.5~7.5之间,而bod5、toc、cod、营养物的含量则明显降低,且重金属的含量也明显降低。对国内已建垃圾处理场渗滤液成分分析,渗滤液成分变化如下:ph值,填埋初期为6~7,呈弱酸性,随着时间推移,ph值可提高到7~8,呈弱碱性。bod随着时间和微生物活动的增加,渗滤液中的bod也逐渐增加,一般填埋6个月至2.5年,达到最高峰值,此时bod多以溶解性为主,随后此项指标开始下降,到6~15年填埋场稳定化为此;cod在填埋初期略低于bod,随着时间的推移,cod下降速率小于bod下降的速率,cod反而略高于bod。渗滤液的氨氮浓度随着填埋年数的增加而增加,可高达2000mg/l以上,渗滤液中的c/n比失调会降低生物处理的效果;对于生化处理,污水中适宜的营养元素比例是bod5:n:p=100:5:1,而一般的垃圾渗滤液中bod5/tp的比值相对较大,与微生物生长所需的磷元素相差较大,因此在渗滤液生化处理中往往缺乏磷元素,需要加以补给;若进场垃圾中混有大量的金属废物,则垃圾渗滤液中含有十多种金属离子,超过一般的排放标准,需进行处理;所以在垃圾进场时应严格禁止金属废物,使渗滤液中的金属含量极低,仅进行稀释处理或无需处理。为了克服上述垃圾渗滤液的水质特性,使得水质符合《生活垃圾填埋场污染物控制标准》(gb16889-2008)进行排放,从而需要垃圾渗滤液处理工艺对渗滤液进行处理,而目前的垃圾渗滤液处理工艺存在着许多问题,不能够对废水进行蒸发浓缩结晶出盐,从而不能够进行固化成砖,再填埋处理,进而影响了进水水质,另外,还存着能耗高、效率低、成本高、运行不安全、在线率低的问题,因此本发明提供了一种基于pmvr-zld的垃圾渗滤液处理工艺,具备了能够对废水进行蒸发浓缩结晶出盐,有效针对结垢及降低系统运行能耗,减少运行成本,运行安全可靠、高在线率,具有良好的操作性和操作灵活性的优点。技术实现要素:(一)要解决的技术问题为了克服垃圾渗滤液处理工艺存在着许多问题,如不能够对废水进行蒸发浓缩结晶出盐,从而不能够进行固化成砖,再填埋处理,进而影响了进水水质,另外,还存着能耗高、效率低、成本高、运行不安全、在线率低的问题,本发明提供了一种基于pmvr-zld的垃圾渗滤液处理工艺,具备了能够对废水进行蒸发浓缩结晶出盐,有效针对结垢及降低系统运行能耗,减少运行成本,运行安全可靠、高在线率,具有良好的操作性和操作灵活性的优点。(二)技术方案本发明通过如下技术方案实现:本发明提出了一种基于pmvr-zld的垃圾渗滤液处理工艺,包括下列步骤:a)原液收集:垃圾渗滤液为原液,进入到原液池进行收集;b)预处理:料液泵将原液池的原液抽取,并输送入一体化混凝沉淀系统进行处理,此时,一体化加药系统能够将混凝剂pac和pam投入一体化混凝沉淀系统中,一体化混凝沉淀系统能够搅拌混凝剂pac和pam、原液,使得发生混凝、化学反应,混凝剂pac和pam、原液互相吸附结合而成较大颗粒并沉淀,同时,经过混凝、化学反应后的原液直接进入后续的斜管沉淀池内进行沉淀,然后形成泥浆,泥浆过排泥泵输送入污泥浓缩池进行进一步浓缩,最后通过板框脱水机进行泥水分离,形成原液上清液、干泥,干泥直接外运填埋,原液上清液进入中间暂存池,再通过一体化加药系统将硫酸加入中间暂存池,调节ph到5,将原液上清液的nh3-n变为nh4+;原液预处理结束;c)预热:原液预处理结束后,由mvr输送泵从中间暂存池抽取,输送入热交换器,此时,蒸馏水罐中的蒸馏水通过蒸馏水泵的抽取进入到热交换器与原液进行换热,原液被预热,温度提升接近沸点温度;d)蒸发分离:采用mvr强制循环蒸发分离系统,经过预热后,略低于沸点温度的原液,呈不饱和状态,呈不饱和状态的原液切向进入结晶器的上层流床,与含有大量细小晶体过饱和循环液进行混合,经强制循环泵分流至每根换热管内,流速控制在1.5m/s~3.5m/s,当循环液从管子中高速流动时,循环液被换热管外部蒸汽冷凝所产生的热量加热升温,通过控制管内压力使其高于该温度下的饱和蒸汽压力,浓盐水在管内不会沸腾,使其不在管内蒸发,加热后的循环液从加热器流出到低压的分离室中,由于分离室压力骤然降低,高温浓盐水在此发生闪蒸,盐水浓缩,结晶析出,沿着结晶器中间的降液分配管直冲到器底,通过特殊设计的分配器,均匀转向上升,上升过程中过饱和溶液与悬浮的晶核充分接触,使其晶核生长,过饱和度消除,通过结晶器的处理,由下往上的颗粒直径大小层次分明,较大颗粒晶体由浓缩液泵抽出至后续离心分离系统处理,结晶器的上清液从由强制循环泵抽出至加热器继续循环蒸发;浓缩液泵抽送结晶器较大晶体颗粒的晶浆液在管道中进行输送,经过蒸发器浓缩结晶到设计值后,由浓缩液泵泵出的含晶体的浓盐水进入到固液分离器进行固液分离,部分母液回流到分离室与室内溶液混合,继续进行蒸发;部分母液去到固化系统进行处理;e)深度处理:经过mvr蒸发系统处理的蒸馏水,去除99%以上的盐分,残留少量的氨氮,需进入ro系统处理,进入ro系统前,先将蒸馏水进行调ph为酸性,氨氮以铵盐形式存在水里,提高ro系统出水水质,最终产水合格排放。f)固化:过循环蒸发分离后的浓缩液,随着浓度增高蒸发到一定程度,富集的杂质高cod影响正常蒸发分离时,结晶物以及少量高浓度母液经过污泥固化稳定化系统,采用水泥及螯合剂将母液固化,固化后送到填埋区填埋。进一步的,所述步骤b)中一体化加药系统:用于预处理加药,设有硫酸、pac、pam的储罐、搅拌器、加药泵;所述步骤b)中一体化混凝沉淀系统:用于预处理反应沉淀,设有2个反应池,1个斜管沉淀池,以及相应搅拌器。进一步的,所述步骤c)中mvr输送泵为vfd控制料液输送泵,频率为0~50hz;所述步骤c)中原液预热结束后,还经过排气冷凝器进行预热。进一步的,所述步骤d)中结晶器采用盐腿结晶器形式,盐腿结晶器设计是具有粒度分级的流化床结晶器。进一步的,所述步骤d)中的强制循环泵采用vfd控制,初始启动系统运行,系统溶液tds低,比重小,频率根据比重以及出口压力自动检测保持在0~50hz范围自动调节,满足循环流量需求;所述步骤d)中分离室产生的二次蒸汽,通过设有非常充分的液、汽分离面积和分离高度的高效除雾系统,高效除雾系统设有两层,一层采用折板式除雾器,二层采用丝网式除雾器,并设有plc自动控制定期产品水清洗除雾网设置,二次蒸汽经过高效除雾系统后,被压缩机抽出进行升温升压,提温后的蒸汽作为加热器的蒸发热源;加热器冷凝的蒸馏水,储存在蒸馏水罐,由蒸馏水泵输送与原液进行换热后,排出系统;系统设有bpe在线监测仪表,自动检测bpe变化;蒸馏水排除系统采用vfd控制蒸馏水泵的频率在0~50hz范围自动调节。进一步的,所述步骤d)中晶浆液的输送管道采用循环管路设计,管路采用多法兰设计,循环管路内设有自动冲洗系统。进一步的,所述步骤d中mvr强制循环蒸发分离系统,触晶浆的排空口,均设置有回流反冲设计。进一步的,所述步骤d)固化系统设有混合搅拌机及加药机。(三)有益效果本发明相对于现有技术,具有以下有益效果:本发明达到能够对废水进行蒸发浓缩结晶出盐,有效针对结垢及降低系统运行能耗,减少运行成本,运行安全可靠、高在线率,具有良好的操作性和操作灵活性的效果。1、为了最大限度回收热量,蒸发系统的进水板换均采用高效率的板式换热器,板式换热器优点是换热效率高、占地小,缺点是流道窄、易堵塞,适用于无ss、胶体水质,针对此问题,本发明采用混凝沉淀的预处理系统,去除废水中的ss及胶体,保持板式换热器的稳定,以免因堵塞造成装置运行不稳定。2、垃圾渗滤液中存在大量的该ca、mg、si等硬度离子以及含有大量不易挥发的cod,在蒸发系统中形成无机垢、有机垢,常规蒸发系统一般采用卧管喷淋降膜系统处理渗滤液浓缩,渗滤液均匀喷洒在换热管表面换热后蒸发,无机垢、有机垢易附在换热管表面结垢,导致传热系数降低、能耗上升等问题,严重造成整个蒸发器堵塞及停车,针对此问题,本发明采用mvr强制循环蒸发分离系统,对渗滤液进行废水蒸发。本系统采用强制循环蒸发分离系统为:抗垢性、适应性最强的蒸发工艺,可保证系统长时间在线运行,该工艺设备内的循环主要依靠外加动力所产生的强制流动。循环速度一般可达1.5-3.5米/秒,传热效率和生产能力较大,可连续运行3个月以上。3、为保证出水水质,后续系统采用膜深度处理系统对蒸发出水进行处理,蒸发出水的含盐量比较低,回收率可达96%以上。与常规采用硫酸洗涤蒸汽相比,造价低,无需耐高温稀硫酸的洗涤塔(一般需要用到锆材),而且需要考虑产水的硫酸铵溶液的后续处理。4、目前针对渗滤液的废水处理均采用浓缩回灌形式,如此恶性循环,造成填埋场渗滤液越来越差,难以处理,本发明采用垃圾渗滤液零排放处理系统,对渗滤液进行蒸发分离,产生的结晶进行固化成砖,再填埋处理,不影响进水水质。附图说明通过阅读参照以下附图对非限制性实施例所作的详细描述,本实用新型的其它特征、目的和优点将会变得更明显:图1为本发明的流程示意图。图2为本发明的mvr蒸发分离系统工艺流程图。图3为本发明的强制循环蒸发分离系统示意图。具体实施方式下面将结合实施例对本发明的技术方案进行清楚、完整地描述。显然,所述实施例仅仅是本发明一部分实施例,而不是全部的实施例。基于本发明中的实施例,本领域普通技术人员在没有作出创造性劳动前提下所获得的所有其他实施例,都属于本发明保护的范围。一种基于pmvr-zld的垃圾渗滤液处理工艺,包括下列步骤:a)原液收集:垃圾渗滤液为原液,进入到原液池进行收集;b)预处理:料液泵将原液池的原液抽取,并输送入一体化混凝沉淀系统进行处理,此时,一体化加药系统能够将混凝剂pac和pam投入一体化混凝沉淀系统中,一体化混凝沉淀系统能够搅拌混凝剂pac和pam、原液,使得发生混凝、化学反应,混凝剂pac和pam、原液互相吸附结合而成较大颗粒并沉淀,同时,经过混凝、化学反应后的原液直接进入后续的斜管沉淀池内进行沉淀,然后形成泥浆,泥浆过排泥泵输送入污泥浓缩池进行进一步浓缩,最后通过板框脱水机进行泥水分离,形成原液上清液、干泥,干泥直接外运填埋,原液上清液进入中间暂存池,再通过一体化加药系统将硫酸加入中间暂存池,调节ph到5,将原液上清液的nh3-n变为nh4+;原液预处理结束;c)预热:原液预处理结束后,由mvr输送泵从中间暂存池抽取,输送入热交换器,此时,蒸馏水罐中的蒸馏水通过蒸馏水泵的抽取进入到热交换器与原液进行换热,原液被预热,温度提升接近沸点温度;d)蒸发分离:采用mvr强制循环蒸发分离系统,经过预热后,略低于沸点温度的原液,呈不饱和状态,呈不饱和状态的原液切向进入结晶器的上层流床,与含有大量细小晶体过饱和循环液进行混合,经强制循环泵分流至每根换热管内,流速控制在1.5m/s~3.5m/s,当循环液从管子中高速流动时,循环液被换热管外部蒸汽冷凝所产生的热量加热升温,通过控制管内压力使其高于该温度下的饱和蒸汽压力,浓盐水在管内不会沸腾,使其不在管内蒸发,加热后的循环液从加热器流出到低压的分离室中,由于分离室压力骤然降低,高温浓盐水在此发生闪蒸,盐水浓缩,结晶析出,沿着结晶器中间的降液分配管直冲到器底,通过特殊设计的分配器,均匀转向上升,上升过程中过饱和溶液与悬浮的晶核充分接触,使其晶核生长,过饱和度消除,通过结晶器的处理,由下往上的颗粒直径大小层次分明,较大颗粒晶体由浓缩液泵抽出至后续离心分离系统处理,结晶器的上清液从由强制循环泵抽出至加热器继续循环蒸发;浓缩液泵抽送结晶器较大晶体颗粒的晶浆液在管道中进行输送,经过蒸发器浓缩结晶到设计值后,由浓缩液泵泵出的含晶体的浓盐水进入到固液分离器进行固液分离,部分母液回流到分离室与室内溶液混合,继续进行蒸发;部分母液去到固化系统进行处理;e)深度处理:经过mvr蒸发系统处理的蒸馏水,去除99%以上的盐分,残留少量的氨氮,需进入ro系统处理,进入ro系统前,先将蒸馏水进行调ph为酸性,氨氮以铵盐形式存在水里,提高ro系统出水水质,最终产水合格排放;f)固化:过循环蒸发分离后的浓缩液,随着浓度增高蒸发到一定程度,富集的杂质高cod影响正常蒸发分离时,结晶物以及少量高浓度母液经过污泥固化稳定化系统,采用水泥及螯合剂将母液固化,固化后送到填埋区填埋;所述步骤b)中一体化加药系统:用于预处理加药,设有硫酸、pac、pam的储罐、搅拌器、加药泵;所述步骤b)中一体化混凝沉淀系统:用于预处理反应沉淀,设有2个反应池,1个斜管沉淀池,以及相应搅拌器;所述步骤c)中mvr输送泵为vfd控制料液输送泵,频率为0~50hz;所述步骤c)中原液预热结束后,还经过排气冷凝器进行预热;该排气冷凝器回收随不可冷凝的气体一起排出系统的蒸汽的能量,以达到减少蒸汽损失和热损最小化的目的;所述步骤d)中结晶器采用盐腿结晶器形式,盐腿结晶器设计是具有粒度分级的流化床结晶器;所述步骤d)中的强制循环泵采用vfd控制,初始启动系统运行,系统溶液tds低,比重小,频率根据比重以及出口压力自动检测保持在0~50hz范围自动调节,满足循环流量需求;所述步骤d)中分离室产生的二次蒸汽,通过设有非常充分的液、汽分离面积和分离高度的高效除雾系统,高效除雾系统设有两层,一层采用折板式除雾器,二层采用丝网式除雾器,并设有plc自动控制定期产品水清洗除雾网设置,二次蒸汽经过高效除雾系统后,被压缩机抽出进行升温升压,提温后的蒸汽作为加热器的蒸发热源;加热器冷凝的蒸馏水,储存在蒸馏水罐,由蒸馏水泵输送与原液进行换热后,排出系统;系统设有bpe在线监测仪表,自动检测bpe变化;蒸馏水排除系统采用vfd控制蒸馏水泵的频率在0~50hz范围自动调节;采用vfd(变频)控制的特点是节省能耗,与采用调节阀控制的区别是不需要泵满频满负荷运行,减少泵的磨损损耗,降低备品备件更换成本;所述步骤d)中晶浆液的输送管道采用循环管路设计,管路采用多法兰设计,循环管路内设有自动冲洗系统;循环管路设计,管道流道大,流速高,弯头少,防止颗粒沉降在管道上,循环管道设有自动冲洗系统,停机是可稀释冲洗管路,防止沉降结块,造成堵塞;同时管路采用多法兰设计,易拆卸、易清理;所述步骤d)中mvr强制循环蒸发分离系统,触晶浆的排空口,均设置有回流反冲设计;所述步骤d)固化系统设有混合搅拌机及加药机。1、为了最大限度回收热量,蒸发系统的进水板换均采用高效率的板式换热器,板式换热器优点是换热效率高、占地小,缺点是流道窄、易堵塞,适用于无ss、胶体水质,针对此问题,本发明采用混凝沉淀的预处理系统,去除废水中的ss及胶体,保持板式换热器的稳定,以免因堵塞造成装置运行不稳定。2、垃圾渗滤液中存在大量的该ca、mg、si等硬度离子以及含有大量不易挥发的cod,在蒸发系统中形成无机垢、有机垢,常规蒸发系统一般采用卧管喷淋降膜系统处理渗滤液浓缩,渗滤液均匀喷洒在换热管表面换热后蒸发,无机垢、有机垢易附在换热管表面结垢,导致传热系数降低、能耗上升等问题,严重造成整个蒸发器堵塞及停车,针对此问题,本发明采用mvr强制循环蒸发分离系统,对渗滤液进行废水蒸发。本系统采用强制循环蒸发分离系统为:抗垢性、适应性最强的蒸发工艺,可保证系统长时间在线运行,该工艺设备内的循环主要依靠外加动力所产生的强制流动。循环速度一般可达1.5-3.5米/秒,传热效率和生产能力较大,可连续运行3个月以上。3、为保证出水水质,后续系统采用膜深度处理系统对蒸发出水进行处理,蒸发出水的含盐量比较低,回收率可达96%以上。与常规采用硫酸洗涤蒸汽相比,造价低,无需耐高温稀硫酸的洗涤塔(一般需要用到锆材),而且需要考虑产水的硫酸铵溶液的后续处理。4、目前针对渗滤液的废水处理均采用浓缩回灌形式,如此恶性循环,造成填埋场渗滤液越来越差,难以处理,本发明采用垃圾渗滤液零排放处理系统,对渗滤液进行蒸发分离,产生的结晶进行固化成砖,再填埋处理,不影响进水水质。渗滤液未处理和处理后的分析报告:取出垃圾渗滤液做出主要成分分析,下表为成分报告:序号指标单位数据备注1外观/黑色溶液2ph/8.243tdsmg/l527504codmg/l108955氨氮mg/l5367.36ssmg/l1000垃圾渗滤液经过本发明处理后主要成分分析,下表为成分报告:序号指标单位数据备注1外观/微浑浊溶液2ph/6.033tdsmg/l5634codmg/l855氨氮mg/l13.89通过上述两个表格比对,水质有较大的改善,且能够符合《生活垃圾填埋场污染物控制标准》(gb16889-2008)进行排放。此外,应当理解,虽然本说明书按照实施方式加以描述,但并非每个实施方式仅包含一个独立的技术方案,说明书的这种叙述方式仅仅是为清楚起见,本领域技术人员应当将说明书作为一个整体,各实施例中的技术方案也可以经适当组合,形成本领域技术人员可以理解的其他实施。当前第1页12