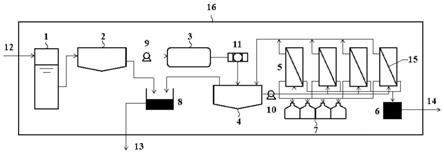
[0001]
本发明涉及一种乳化废液处理装置及工艺,尤其涉及一种基于有效组分回收的机加工乳化废液处理装置及工艺。
背景技术:[0002]
在机械加工和金属压延等行业中,都会使用乳化液(俗称切削液),起到冷却、润滑、清洗等作用。在循环使用多次后,乳化液会出现腐败变质和性能降低,然后被更换废弃,从而形成乳化废液,废液成分十分复杂,主要含有表面活性剂、机械油、矿物油、润滑剂、添加剂、可溶性的有机物、金属粉末和固体悬浮物等,具有乳化程度高、化学性质比较稳定,油含量、cod浓度高、可生化性比较差等特点。
[0003]
目前,乳化废液的处理还没有成熟的工艺,大多企业将其委外处理,处理费用3000-5000元/吨。高昂的乳化废液处理成本,已成为制约行业发展的主要因素之一。因此,开发一种高效、低能耗及资源回收的乳化废液处理技术已成为水污染治理的重要内容。
[0004]
乳化液失效更换,是由于其循环使用后腐败和杂质含量过高造成的。能否在处理过程中将杂质去除,而有效的成分和水继续使用?这样既可以回收有效成分,又可以对乳化废液处理,实现废液的再利用,减轻企业负担,实现节能减排的目的。
[0005]
传统乳化废液处理工艺采用生化法,存在着资源浪费,处理费用高昂,环境污染等问题。
技术实现要素:[0006]
发明目的:本发明目的是提供一种低能耗、高效率及资源回收的基于有效组分回收的机加工乳化废液处理装置及工艺。
[0007]
技术方案:本发明包括依次连接的原水水箱、沉淀池、氧化预处理池、循环池、多个膜分离组件和出水水箱,其中,每个膜分离组件内均设有陶瓷膜,所述的沉淀池和循环池与浓油池连接,所述的膜分离组件底部连接有浓油罐,所述的出水水箱与生产线连接。
[0008]
所述的原水水箱与乳化废液的入口连接。
[0009]
所述的沉淀池和氧化预处理池之间设有第一离心泵。
[0010]
所述的氧化预处理池和循环池之间设有过滤机。
[0011]
所述的循环池和膜分离组件之间设有第二离心泵。
[0012]
所述膜分离组件内未过滤的液体回流至循环池。
[0013]
一种基于有效组分回收的机加工乳化废液处理工艺,包括以下步骤:
[0014]
(1)乳化废液通过入口进入原水水箱储存,自流进入沉淀池,进行自然沉降;
[0015]
(2)初沉后的废液经过第一离心泵送水至氧化预处理池,完成破乳处理,使油水分离;
[0016]
(3)破乳后的液体通过过滤机进入循环池,由第二离心泵抽送至膜分离组件,截流废液中的大分子物质以及微生物,留下有效小分子乳化液成分,部分未过滤液体回流至循
环池进行二次过滤,由沉淀池和循环池产出的废油经浓油池收集后委外处理;
[0017]
(4)过滤后的液体进入出水水箱,复配后流入生产线,完成乳化废液中有效组分的回用。
[0018]
所述步骤(1)中乳化废液在原水水箱和沉淀池中停留的时间分别为2~3h和3~4h。
[0019]
有益效果:本发明在实现乳化废液经济处理的同时,能够对废液中有效组分进行回收利用;工艺成本低廉,一次性投资基建较少,膜材料成本低,且使用周期长(约为一年);工艺整体流程较短,处理耗时较少;可产水90%左右,减少企业90%左右乳化废液排放量,降低企业处理成本;产水中保留原废乳化液中40%左右的水性成分,回用配液时仅需补充原使用量60%左右的油性成分,因此,产水回用可以节约40%左右的化学品消耗量,节约资源,实现节能减排。
附图说明
[0020]
图1为本发明的结构示意图。
具体实施方式
[0021]
下面结合附图对本发明作进一步说明。
[0022]
如图1所示,本发明包括依次连接的原水水箱1、沉淀池2、氧化预处理池3,循环池4、多个并列分布的膜分离组件5和出水水箱6,每个膜分离组件5内均设有陶瓷膜15。其中,原水水箱1与乳化废液的入口12连接,沉淀池2和氧化预处理池3之间设有第一离心泵9,氧化预处理池3和循环池4之间设有过滤机11,循环池4和膜分离组件5之间设有第二离心泵10,膜分离组件5的出口通过出水水箱6与生产线14连接,膜分离组件5底部连接有浓油罐7,沉淀池2和循环池4与浓油池8连接,浓油池8与出口13连接。
[0023]
乳化废液通过入口12进入原水水箱1储存,自流进入沉淀池2,进行沉淀和物理截流,水力停留时间分别为2~3h和3~4h;初沉后的废液经过第一离心泵9送水至氧化预处理池3,完成破乳处理,使油水分离;破乳后的液体通过过滤机11进入循环池4,由第二离心泵10抽送至膜分离组件5,通过多级陶瓷膜15过滤后,截流废液中的大分子物质以及微生物,留下有效小分子乳化液成分,产水进入出水水箱6,其产水各项指标分别为折光度1.6%、ph值9.2、电导率4478us/cm、表面张力43.0、滴定减值ph=7消耗0.25nhcl量9.27,复配后流入生产线14,其产水复配乳化液各项指标分别为折光度5.9%、ph值9.6、电导率4671us/cm、表面张力38.1、滴定减值ph=7消耗0.25nhcl量16.55。浓缩废油经浓油罐7收集后委外处理,部分未过滤液体回流至循环池4;由沉淀池2和循环池4产出的废油经浓油池8收集后经出口13排出进行委外处理。
[0024]
膜分离组件5采用具有较高孔隙率和优异机械性能的多孔陶瓷膜,适用于乳化废液的经济处理;在出水水箱6内进行配乳,添加缺失成分,如环烷基、石蜡基、磺化脂肪、各种植物油等。
[0025]
一种基于有效组分回收的机加工乳化废液处理工艺主要包括以下步骤:
[0026]
(1)乳化废液通过入口12进入原水水箱1储存,自流进入沉淀池2,水力停留时间分别为2~3h和3~4h,进行自然沉降,用物理手段截流金属碎屑等物质;
[0027]
(2)初沉后的废液经过第一离心泵9送水至氧化预处理池3,完成破乳处理,使油水分离;
[0028]
(3)破乳后的液体通过过滤机11进入循环池4,由第二离心泵10抽送至膜分离组件5,截流废液中的大分子物质以及微生物,留下有效小分子乳化液成分,部分未过滤液体回流至循环池4进行二次过滤,由沉淀池2和循环池4产出的废油经浓油池8收集后委外处理;
[0029]
(4)过滤后的液体进入出水水箱6,复配后流入生产线14,完成乳化废液中有效组分的回用。
[0030]
以某机械加工厂乳化废液为原水,分别测定原水、产水、配乳后以及新鲜乳化液的各项指标,其实验见下表:
[0031][0032][0033]
实验结果表明:
[0034]
1)该工艺处理乳化废液后的产水与处理前现场乳液相比,ph、碱值、表面张力差别不大,说明陶瓷膜可有效去除废液中的油和杂质,而保留水溶性的有效成分,如表面活性剂和有机碱等。
[0035]
2)产水回用配置的乳液碱值比新鲜乳液高,是因为碱性物质在废液处理过程中作为有效成分被保留。
[0036]
该工艺解决了机械加工领域乳化废液处理成本高昂的问题,实现了企业乳化废液经济处理,实现了乳化废液中有效组分的回收再利用,在机械加工乳化废液处理领域中具有广阔应用前景。