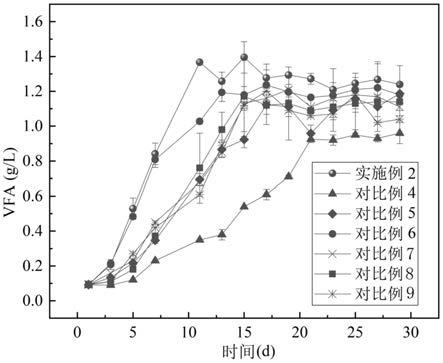
1.本发明属于有机固废处理技术领域,尤其涉及一种提高有机固废厌氧发 酵效率的制剂及其制备方法与应用。
背景技术:2.近年来,随着经济的发展,有机固废产量持续增加。有机固废成分相对 复杂,包括市政污泥、工业污泥、厨余垃圾、秸秆等,同时具有资源属性和 污染属性。若有机固废得到妥善处理,将变废为宝,反之将带来二次污染。
3.申请号为201010580486.2,发明名称为:亚临界水处理城乡有机固废生 产有机肥及设备的中国发明专利,采用亚临界水处理厨余垃圾和秸秆,制备 有机肥,该方法可调控肥料成分,肥料活性高。但是亚临界的反应条件在 180~230℃和1.55~3.0mpa,运行能耗较高,再加上亚临界水热过程中容易产 生有毒气体,造成二次污染或需要配备尾气处理设备,因此在市场上很难大 规模应用。
4.申请号为201811172817.1,发明名称为:一种提高有机废弃物高固厌氧 发酵产甲烷效率的方法的中国发明专利,其通过添加生物炭提高有机废弃物 高固厌氧发酵产甲烷的效率,生物炭的多孔结构和导电性有利于厌氧产酸并 提高产甲烷菌群落稳定性,从而提高厌氧发酵效率,然而生物炭的用量较大, 经济价值有待提升。
5.申请号为201410841735.7,发明名称为:利用餐厨垃圾生产短链挥发性 脂肪酸的方法及短链挥发性脂肪酸的中国发明专利公开了一种将活性污泥接 种到餐厨垃圾发酵系统中,并利用生物表面活性剂提高微生物的生命活动, 从而生产短链挥发性脂肪酸,实现餐厨垃圾的减量化、资源化和无害化处理, 具有运行成本低廉,收益高、短链挥发性脂肪酸产率高等优势。但是该方法 适应范围较窄。
技术实现要素:6.本发明的目的在于克服上述现有技术的缺点和不足,提供了一种提高有 机固废厌氧发酵效率的制剂。本发明的具体原理为采用固定生物酶和共代谢 营养激发有机固废本土微生物的快速繁殖,通过有机高分子的絮凝架桥,提 高厌氧颗粒污泥群落稳定性,从而实现有机固废无害化、资源化和减量化。
7.本发明的另一个目的在于提供上述提高有机固废厌氧发酵效率的制剂的 制备方法。
8.本发明的再一目的在于提供上述提高有机固废厌氧发酵效率的制剂的应 用。
9.本发明的上述目的通过如下技术方案实现:
10.一种提高有机固废厌氧发酵效率的制剂,包括固定生物酶与共代谢营养 物质和有机高分子。
11.所述的共代谢营养物质包括但不限于葡萄糖、乙醇、蔗糖和乙酸钠中的 至少一种;更优选为葡萄糖和乙酸钠中的至少一种。
12.所述的有机高分子包括但不限于聚丙烯酰胺(pam)、壳聚糖、环糊精 和支链淀粉中的至少一种;优选为:分子量为800万~2000万的聚丙烯酰胺 (pam)和粘度为200~600mpa.s的壳聚糖中的至少一种;更优选为分子量为 1400万的聚丙烯酰胺和粘度为400mpa.s的壳聚糖中的至少一种。
13.所述的固定生物酶与共代谢营养物质和有机高分子优选按质量比 0.05~0.40:0.5~1:0.001计算。
14.所述的固定生物酶通过如下制备方法制备得到:
15.s1.将fe3o4@sio2‑
nh2分散于溶液1中,超声分散,得到分散的混合物, 然后向其中加入戊二醛,洗涤磁选出固体;
16.s2.将上述固体用溶液2溶解,然后加入生物酶反应,洗涤磁选后,冷冻 干燥即得固定生物酶。
17.步骤s1中,所述的fe3o4@sio2‑
nh2的制备方法包括如下步骤:
18.1)fe3o4nps的制备:fecl3分散于乙二醇中,超声分散至呈砖红色后向 其中加入二水合柠檬酸钠和乙酸钠,搅拌混匀至黄褐色后进行水热反应,磁 分离,然后用1/10磁分离所得固体体积的0.1m稀硝酸快速清洗,超声,再 依次用乙醇、水洗涤,所得固体经冷冻干燥即得粉末状fe3o4nps;
19.2)fe3o4@sio2‑
nh2的制备:将fe3o4nps分散到乙醇和水的混合液中, 水浴搅拌均匀,向其中滴加氨水和teos,继续反应、磁分离后冷冻干燥,即 得粉末状fe3o4@sio2;
20.3)fe3o4@sio2‑
nh2的制备:向fe3o4@sio2中加入乙醇,超声处理、水 浴条件下混匀后,分别滴加氨水和3
‑
氨丙基三乙氧基硅烷,反应,洗涤至中 性,冷冻干燥即得fe3o4@sio2‑
nh2。
21.具体地,所述的fe3o4@sio2‑
nh2的制备方法包括如下步骤:
22.1)fe3o4nps的制备:将1.3g fecl3分散于40.0ml乙二醇中,超声分散 10~60min,使其充分溶解成砖红色,加入0.48g二水合柠檬酸钠和2.40g乙 酸钠,300~600r/min机械搅拌20~60min,充分溶解成黄褐色,然后倒入高 压反应釜中的聚四氟乙烯内衬中,200℃高温反应10h后,磁分离,然后按体 积比磁分离固体:0.1m稀硝酸=10:1的比例加入0.1m稀硝酸,超声10min后 依次用乙醇和去离子水洗涤,然后分散于去离子水中,
‑
70℃冷冻12h,冷冻 干燥后即为粉末状fe3o4nps;
23.2)fe3o4@sio2‑
nh2的制备:取0.05g fe3o4nps分散到100ml乙醇和水 的混合液(体积比乙醇:水=4:1)中,在40℃水浴,300~600r/min搅拌下,依 次滴速加入1ml 28%(v/v)氨水和2.0ml正硅酸乙酯(teos),连续反应 6h,磁分离清洗,
‑
70℃冷冻12h,冷冻干燥即得粉末状fe3o4@sio2;
24.3)在圆底烧瓶中加入1g fe3o4@sio2和60ml无水乙醇,超声处理 10~30min,在50~90℃水浴,300~600r/min搅拌下,分别滴速加入6.0ml 28% (v/v)氨水和4ml 3
‑
氨丙基三乙氧基硅烷(aptes),连续反应8h,洗涤 至中性,冷冻干燥即得fe3o4@sio2‑
nh2。
25.步骤s1中所述的溶液1优选为磷酸盐缓冲液;进一步优选为:ph为 7.5~8.5的磷酸盐缓冲液;更优选为:ph为7.8的磷酸盐缓冲液。
26.步骤s1中所述的fe3o4@sio2‑
nh2与溶液1按质量g体积ml比1:50~150 计算;更优选按质量g体积ml比1:90计算。
27.步骤s1中所述的超声处理的条件优选为:时间5~30分钟,功率100~300 w;更优选为:时间10分钟,功率200w。
28.步骤s1中所述的戊二醛优选为50%(v/v)的戊二醛。
29.步骤s1中所述的溶液1与戊二醛优选按体积比7~11:1计算;更优选按 9:1计算。
30.步骤s1中所述的洗涤磁选出固体中,洗涤的条件优选为25℃、200rpm 震荡洗涤2h。
31.步骤s2中所述的溶液2优选为磷酸盐缓冲液;进一步优选为:ph为 4.5~6.5的磷酸盐缓冲液;更优选为:ph为5.2的磷酸盐缓冲液。
32.步骤s2中所述的fe3o4@sio2‑
nh2与溶液2按质量g体积ml比1:100~300 计算;更优选按质量g体积ml比1:200计算。
33.步骤s2中所述的生物酶与步骤s1中的fe3o4@sio2‑
nh2优选按质量比 0.5~4:1;更优选按质量比1.5~4:1计算。
34.步骤s2中所述的生物酶优选包括酸性蛋白酶、果胶酶、漆酶、纤维素酶、 脂肪酶、淀粉酶、溶菌酶和脱氢酶中的至少一种;更优选为酸性蛋白酶、果 胶酶、漆酶和纤维素酶中的至少三种。
35.步骤s2中所述的反应的条件为:2~8℃、50~300rpm反应1~4h;更优选 为4℃、200rpm反应2h。
36.步骤s2中所述的干燥优选为冷冻干燥。
37.所述的提高有机固废厌氧发酵效率的制剂的制备方法,包括如下步骤: 将固定生物酶与共代谢营养物质和有机高分子按照常规方法混匀即得。
38.具体地,所述的提高有机固废厌氧发酵效率的制剂的制备方法,包括如 下步骤:
39.(1)固定生物酶的制备:将fe3o4@sio2‑
nh2分散于溶液1中,超声分 散,得到分散的混合物,然后向其中加入戊二醛,洗涤磁选出固体;
40.将上述固体用溶液2溶解,然后加入生物酶反应,洗涤磁选后,冷冻干 燥即得固定生物酶;
41.(2)将步骤(1)得到的固定生物酶与共代谢营养物质和有机高分子混 匀,即得提高有机固废厌氧发酵效率的制剂。
42.所述的提高有机固废厌氧发酵效率的制剂在有机固废厌氧发酵中的应 用。
43.一种将提高有机固废厌氧发酵效率的制剂应用于有机固废厌氧发酵生产 挥发性脂肪酸的方法,包括如下步骤:将上述提高有机固废厌氧发酵效率的 制剂加入有机固废中进行厌氧发酵,并在挥发性脂肪酸(vfa)出现峰值后 补加有机固废。
44.所述的有机固废的ph为3~11、含水率为70%~98%;更优选ph为7.2、 含水率为75.30%~92.3%。
45.所述的有机固废包括但不限于餐厨垃圾、市政污泥和工业污泥中的至少 一种;更优选为餐厨垃圾调浆液、市政污泥和有机物含量大于30%的工业污 泥中的至少一种。
46.所述的提高有机固废厌氧发酵效率的制剂与有机固废优选按质量(mg) 体积(l)比10~500:1计算;优选按质量(mg)体积(l)比100:1。
47.所述的厌氧发酵的条件优选为:通入氮气10~180s、20~300rpm、ph 7.0~ 7.8、10~50℃恒温培养;更优选为:通入氮气30~180s、100~300rpm、ph 7.0~ 7.8、35~50℃
恒温培养。
48.所述的达到峰值的时间优选为3~11天。
49.所述的补加有机固废的量优选按水力停留时间5~20d计算;更优选按水 力停留时间10d计算。
50.本发明相对于现有技术,具有如下的优点及效果:
51.(1)利用有机固废组成和结构特点,采用固定酶的形式提高酶的活性及 稳定性,将污泥中的大分子转变化为小分子,再通过共代谢营养,促进污泥 中的厌氧微生物的生命活动,降解难分解的有机物,最后通过有机高分子的 絮凝架桥,提高污泥群落稳定性及反应体系污泥的稳定性,从而实现有机固 废资源化和减量化的目标。
52.(2)本发明提高有机固废厌氧发酵效率的制剂合成工艺简单,成本低, 使用方便,应用范围广。
附图说明
53.图1为实施例1的各酶在固定前后的红外光谱图。
54.图2为实施例1三种固定酶的zeta电位图;其中,图a)为酶的固定化过 程图;图b)为酸性蛋白酶固定前后的zeta电位图;图c)为果胶酶固定前后 的zeta电位图;图d)为漆酶固定前后的zeta电位图。
55.图3为实施例2和对比例4
‑
9中每升混合液中含有的vfa随时间的变化 结果图。
具体实施方式
56.下面结合具体实施例对本发明作进一步具体详细描述。
57.实施例中,fe3o4@sio2‑
nh2的制备方法包括如下步骤:
58.1)fe3o4nps的制备:将1.3g fecl3分散于40.0ml乙二醇中,超声分散 10~60min,使其充分溶解成砖红色,加入0.48g二水合柠檬酸钠和2.40g乙 酸钠,300~600r/min机械搅拌20~60min,充分溶解成黄褐色,然后倒入高 压反应釜中的聚四氟乙烯内衬中,200℃高温反应10h后,磁分离,然后按体 积比磁分离固体:0.1m稀硝酸=10:1的比例加入0.1m稀硝酸,超声10min后 依次用乙醇和去离子水洗涤,然后分散于去离子水中,
‑
70℃冷冻12h,冷冻 干燥后即为粉末状fe3o4nps;
59.2)fe3o4@sio2‑
nh2的制备:取0.05g fe3o4nps分散到100ml乙醇和水 的混合液(体积比乙醇:水=4:1)中,在40℃水浴,300~600r/min搅拌下,依 次滴速加入1ml 28%(v/v)氨水和2.0ml正硅酸乙酯(teos),连续反应 6h,磁分离清洗,
‑
70℃冷冻12h,冷冻干燥即得粉末状fe3o4@sio2;
60.3)在圆底烧瓶中加入1g fe3o4@sio2和60ml无水乙醇,超声处理 10~30min,在50~90℃水浴,300~600r/min搅拌下,分别滴速加入6.0ml 28% (v/v)氨水和4ml 3
‑
氨丙基三乙氧基硅烷(aptes),连续反应8h,洗涤 至中性,冷冻干燥即得fe3o4@sio2‑
nh2。
61.实施例1:
62.一种提高有机固废厌氧发酵效率的制剂的制备方法,包括如下步骤:
63.(1)固定酶的制备:
64.a1:固定酸性蛋白酶的制备:将0.1g粒径约500nm的fe3o4@sio2‑
nh2分散在9ml磷酸
盐缓冲溶液(ph为7.8)中,并超声处理10分钟、超声功 率200w,得到分散的混合物;将1ml 50%(v/v)戊二醛溶液加入到上述分 散的混合物中,25℃、200rpm震荡洗涤2h,磁选出固体;
65.a2:将步骤a1筛选得到的固体用20ml、ph 5.2的磷酸盐缓冲液重新溶 解,然后加入酸性蛋白酶(50u/mg)0.05g,4℃、200rpm反应2h,用ph为 5.2的磷酸缓冲液洗涤3~5遍,然后用磁铁吸取固体,再冷冻干燥得到固定酸 性蛋白酶(42.51u/mg)。
66.b1:固定果胶酶的制备:将0.1g粒径约500nm的fe3o4@sio2‑
nh2分散 在9ml磷酸盐缓冲溶液(ph为7.8)中,并超声处理10分钟、超声功率200 w,得到分散的混合物;将1ml 50%(v/v)戊二醛溶液加入到上述分散的混 合物中,25℃、200rpm震荡洗涤2h,磁选出固体;
67.b2:将步骤b1筛选得到的固体用20ml、ph 5.2的磷酸缓冲液重新溶解, 然后加入果胶酶(500u/mg)0.05g,4℃、200rpm反应2h,用ph 5.2的磷 酸缓冲液洗涤3~5遍,然后用磁铁吸取固体,再冷冻干燥得到固定果胶酶 (42.51u/mg)。
68.c1:固定漆酶的制备:将0.1g粒径约500nm的fe3o4@sio2‑
nh2,分散 在9ml磷酸盐缓冲溶液(ph为7.8)中,并超声处理10分钟、超声功率200 w,得到分散的混合物;将1ml 50%(v/v)戊二醛溶液加入到上述分散的混 合物中,25℃、200rpm震荡洗涤2h,磁选出固体;
69.c2:将步骤b1筛选得到的固体用20ml、ph 5.2的磷酸缓冲液重新溶解, 然后加入漆酶(500u/mg)0.05g,4℃、200rpm反应2h,用ph 5.2的磷酸 缓冲液洗涤3~5遍,然后用磁铁吸取固体,再冷冻干燥得到固定漆酶(42.51 u/mg);
70.酸性蛋白酶、果胶酶、漆酶在固定前后的红外光谱图如图1所示。
71.从图1可以看出,相比游离酶,固定酶在1230cm
‑1产生了新的化学键, 说明游离酶可通过共价键的形式固定在fe3o4@sio2‑
nh2上。
72.酸性蛋白酶、果胶酶、漆酶的固定化过程如图2中的a)图所示。
73.酸性蛋白酶、果胶酶、漆酶、固定酸性蛋白酶、固定果胶酶、固定漆酶 和fe3o4@sio2‑
nh2的zeta电位如下表1和图2中的图b)
‑
d)所示:
74.表1:
[0075][0076]
从表1和图2可以看出:酶经过固定,固定酸性蛋白酶、固定果胶酶和 固定漆酶的zeta电位得到提高,游离酶也可通过静电结合的方式固定在 fe3o4@sio2‑
nh2上。
[0077]
(2)将上述步骤(1)制备得到的固定酸性蛋白酶、固定果胶酶和固定 漆酶各0.05g与1g葡萄糖和0.001g,分子量为1400万的聚丙烯酰胺(pam, 购于上海麦克林生化科技有限
公司;下同)混合均匀,即得提高有机固废厌 氧发酵效率的制剂。
[0078]
一种将提高有机固废厌氧发酵效率的制剂应用于有机固废厌氧发酵生产 挥发性脂肪酸的方法,包括如下步骤:
[0079]
取佛山市平洲污水处理厂浓缩池污泥1l,放入锥形瓶中,其含水率为92.3%,有机物含量(即原始vss)43.2%,调节ph为7.2,得到混合液,并 按100mg/l的量向混合液中加入提高有机固废厌氧发酵效率的制剂;再向厌 氧发酵罐中通入氮气30s,100rpm、35℃、ph 7.0~7.8避光恒温培养,连续 测vfa含量。第3d vfa出现峰值68.43
±
1.29mg/l,然后第4d开始按0.1l/d (水力停留时间10d)加入有机固废,并连续检测vss和vfa,整个周期为 30天。
[0080]
对比例1:
[0081]
本对比例与实施例1基本相同,不同之处在于,本对比例提高有机固废 厌氧发酵效率的制剂中不含固定酶,仅含葡萄糖和聚丙烯酰胺;第3d vfa 出现峰值47.80
±
2.23mg/l,然后第4d开始按0.1l/d(水力停留时间10d) 加入有机固废,并连续检测vss和vfa。
[0082]
对比例2:
[0083]
本对比例与实施例1基本相同,不同之处在于,本对比例提高有机固废 厌氧发酵效率的制剂中只含有固定酶酸性蛋白酶、固定果胶酶和固定漆酶, 不含有葡萄糖和聚丙烯酰胺;第5d,vfa出现峰值39.73
±
1.57mg/l,然后 第6d开始按0.1l/d(水力停留时间10d)加入有机固废,并连续检测vss和 vfa。
[0084]
对比例3:
[0085]
本对比例与实施例1基本相同,不同之处在于,本对比例向浓缩池污泥 中不添加提高有机固废厌氧发酵效率的制剂;第15d,vfa出现峰值4.09
±ꢀ
0.45mg/l,然后第16d开始按0.1l/d(水力停留时间10d)加入有机固废, 并连续检测vss和vfa。
[0086]
实施例2:
[0087]
本实施例与实施例1基本相同,不同之处在于,本实施例2步骤(1)中 选用的酶分别为0.05g酸性蛋白酶(50u/mg)、0.05g果胶酶(500u/mg)、 0.05g纤维素酶(500u/mg)和0.05g漆酶(500u/mg),最终制备得到固定酸 性蛋白酶(48.19u/mg)、固定果胶酶(459.23u/mg)、固定纤维素酶(468.39 u/mg)和固定漆酶(467.77u/mg);
[0088]
其中,固定酸性蛋白酶(48.19u/mg)、固定果胶酶(459.23u/mg)和固 定漆酶(467.77u/mg)的制备方法同实施例1;
[0089]
固定纤维素酶的制备方法如下:d1:固定纤维素酶(468.39u/mg)的制 备:将0.1g粒径约500nm的fe3o4@sio2‑
nh2,分散在9ml磷酸盐缓冲溶 液(ph为7.8)中,并超声处理10分钟、超声功率200w,得到分散的混合 物;将1ml 50%(v/v)戊二醛溶液加入到上述分散的混合物中,25℃、200rpm 震荡洗涤2h,磁选出固体;
[0090]
d2:将步骤b1筛选得到的固体用20ml、ph 5.2的磷酸缓冲液重新溶解, 然后加入纤维素酶(468.39u/mg)0.05g,4℃、200rpm反应2h,用ph 5.2、 0.5mol/l的磷酸缓冲液洗涤3~5遍,然后用磁铁吸取固体,再冷冻干燥得到 固定纤维素酶(468.39u/mg);
[0091]
步骤(2)中,将固定酸性蛋白酶(48.19u/mg)、固定果胶酶(459.23u/mg)、 固定纤维素酶(468.39u/mg)和固定漆酶(467.77u/mg)各0.1g和乙酸钠各 0.5g与粘度为400mpa.s壳聚糖(购于上海麦克林生化科技有限公司;下同) 0.001g混合均匀得到提高有机固废厌
vfa出现峰值0.89
±
0.03g/l,其它操作与实施例2相同。
[0109]
第30天后,实施例2和对比例4
‑
9每升混合液中含有的vfa随时间的变 化结果如图3所示。
[0110]
从图3可以看出,与对比例4
‑
9相比,实施例2加入了提高有机固废厌氧 发酵效率的制剂,厌氧发酵体系产生vfa的速度和产量显著提高。
[0111]
本发明的实施方式并不受上述实施例的限制,其他任何未背离本发明的 精神实质与原理下所作的改变、修饰、替代、组合、简化,均应为等效的置 换方式,都包含在本发明的保护范围之内。