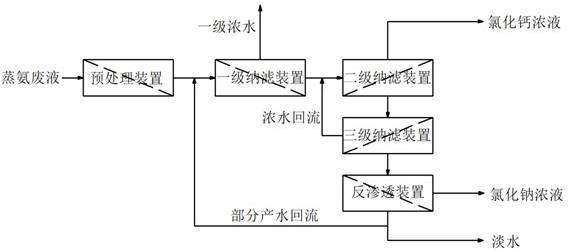
1.本发明涉及一种蒸氨废水制取氯化钙浓液的方法,尤其是氨碱法纯碱工艺产生的蒸氨废水利用膜法分离浓缩制取氯化钙浓液的方法。
背景技术:2.纯碱作为一种重要的无机化工原料,国内年产能已超3000万吨,其中氨碱法工艺在国内的产能占比为45%。利用氨碱法工艺每生产1吨纯碱,会产生约10m3的蒸氨废水,国内每年蒸氨废水排放量超过1亿立方米。蒸氨废水的排放不仅会造成环境污染,更是一种资源的浪费,因其清液主要成分为cacl2(8~10%)和nacl(4~6%),具有可回收利用价值。蒸氨废清液的典型组成:成分ca
2+
mg
2+
na
+
cl-so
42-含量(mg/l)372191.21931395564418目前,国内外对蒸氨废水进行资源利用的主流工艺,一是通过蒸发结晶工艺制备氯化钙,二是以硫酸钠为原料制备硫酸钙。第一种工艺先对蒸氨废水进行固液分离,然后清液经蒸发结晶生产固体氯化钙,为了节约蒸汽消耗,国内企业的传统做法是将清液送到盐田中自然蒸发,提高清液浓度到20
°bé
左右后,用于生产氯化钙,这种工艺生产效率低,周期长,占地面积大,且自然蒸发的方式存在不稳定性,无法保证氯化钙浓液的品质和供应量,造成氯化钙生产成本波动较大。第二种工艺是化学法工艺,用硫酸钠和清液反应生产硫酸钙,需要消耗大量的原料硫酸钠,而且剩余母液中仍含有较多杂质。中国专利cn111559753a公开了“一种纯碱厂蒸氨废液的利用方法及装置”,该方法在蒸氨废液中加入硫酸钠,利用废液中的ca
2+
制取caso4,再加碳酸钠进一步除钙,最后用膜法进一步去除杂质,得到较纯净的氯化钠溶液,该方法的本质还是用化学法除钙,达到蒸氨废水中钙钠分离的目的,工艺过程中需要消耗大量的硫酸钠和碳酸钠,原料成本高。
技术实现要素:3.本发明要解决的技术问题是提供一种蒸氨废水制取氯化钙浓液的方法,可以为蒸发结晶法生产固体氯化钙提供高浓度的原料液,克服了传统摊晒方法占地面积大、原料消耗高、产出效率低、质量和产量不稳定的问题,克服了直接蒸发浓缩工艺能耗高、装置易结垢、经济效益差的问题,可实现蒸氨废水全膜法资源高效利用。
4.为解决上述技术问题,本发明包括如下步骤:(1) 蒸氨废水经预沉淀后,取上层清液,经过微滤和/或超滤装置,去除其中的固体大颗粒及不溶物,除杂后的蒸氨废水用盐酸调节ph值至5.0~7.0,得到浊度小于2ntu的蒸氨废清液;(2) 步骤(1)得到的蒸氨废清液加入淡水稀释,稀释比例按照淡水占蒸氨废清液体积的0~50%,然后加压进入一级纳滤装置,得到一级纳滤产水和一级纳滤浓水;一级纳滤对so
42-的截留率81~92%,对ca
2+
的截留率8~46%,对na
+
的截留率-12~8%,操作压力2.0~
5.5 mpa,回收率控制在45~85%;(3) 步骤(2)得到的一级纳滤产水加压进入二级纳滤装置,得到二级纳滤产水和二级纳滤浓水,二级纳滤浓水即为18~20wt%的氯化钙浓液;二级纳滤对ca
2+
的截留率63~91%,对na
+
的截留率-21~-5%,操作压力5.5~8.8 mpa,回收率控制在55~85%;(4) 步骤(3)得到的二级纳滤产水加压进入三级纳滤装置,得到三级纳滤产水和三级纳滤浓水;三级纳滤对ca
2+
的截留率72~89%,对na
+
的截留率15~32%,操作压力2.0~5.8 mpa,回收率控制在55~85%;(5)步骤(4)得到的三级纳滤产水加压进入反渗透装置,得到反渗透产水和反渗透浓水,反渗透产水部分回流至一级纳滤进水作为稀释水,部分作为产品淡水,反渗透浓水为6~14wt%的氯化钠浓液;反渗透脱盐率92~98%,操作压力4.5~7.9 mpa,回收率控制在32~65%。
5.所述的步骤(2)中用于稀释蒸氨废清液的淡水为步骤(5)反渗透产水的回流水,回流比例控制在反渗透产水的0~80%,稀释比例优选淡水占蒸氨废清液体积的10%~30%;一级纳滤对so
42-的截留率83~88%,对ca
2+
的截留率9~20%,对na
+
的截留率-8~0%,操作压力2.5~4.5 mpa,回收率控制在60~75%;一级纳滤浓水由于硫酸根浓度高,外排另作他用。
6.所述的步骤(3)中的二级纳滤装置,对ca
2+
的截留率78~89%,对na
+
的截留率-12~-8%,操作压力7.0~8.5 mpa,回收率控制在66~78%;根据最终氯化钙浓液浓度要求,二级纳滤采用分段式设计,段间设有增压泵,以保证分离浓缩效果。
7.所述的步骤(4)中的三级纳滤装置,对ca
2+
的截留率80~89%,对na
+
的截留率22~30%,操作压力3.5~5.5 mpa,回收率控制在62~78%;三级纳滤浓水加压后回到二级纳滤装置再次分离浓缩。
8.所述的步骤(5)中的反渗透装置,脱盐率95~98%,操作压力4.9~7.5 mpa,回收率控制在40~58%。
9.上述步骤(2)~(5)中所述的各级装置,运行温度为15~40℃,ph为5.0~7.0;所述的各级装置浓水出口均设有能量回收装置,以达到节能之目的。
10.上述步骤(1)中所述的微滤和/或超滤装置,可以采用陶瓷膜、中空纤维超滤膜、有机管式膜的一种或几种组合。
11.通过本发明,可实现蒸氨废水中cacl2和nacl的有效分离,最终得到的18~20wt%氯化钙浓液中na
+
浓度≤17g/l,得到的6~14wt%氯化钠浓液中ca
2+
浓度≤1.5g/l,氯化钙浓液可直接用于蒸发结晶生产氯化钙,氯化钠浓液可用于纯碱/氯碱化盐,另外还有部分淡水产出。
12.通过反渗透产水回流可有效降低一级纳滤装置结垢风险,减少甚至无需阻垢剂添加;通过不同性能膜的排列组合,控制各装置回收率以及对离子的截留率,可有效控制cacl2和nacl的分离浓缩;通过三级纳滤浓水回流,可进一步提高蒸氨废清液的利用率,综合利用率可达65%以上。
13.与现有技术相比,本发明创新性的采用全膜法工艺,使蒸氨废水中的cacl2和nacl实现了高效分离浓缩,且无其它成分的引入,最终得到高浓度的氯化钙和氯化钠浓液以及淡水,从而提高了蒸氨废水的利用率,实现了蒸氨废水高效绿色清洁回收,相较于传统的氯化钙蒸发结晶生产工艺,减少浓缩用地,提高浓缩效率,保证了氯化钙浓液的品质和供应量
的稳定性,具有良好的环保和经济效益。
附图说明
14.下面结合附图和实施例对本发明进一步说明:图1是本发明的工艺流程示意图。
具体实施方式
15.实施例1参照图1,本发明采用的装置包括:依次以管线相连的预处理装置、一级纳滤装置、二级纳滤装置、三级纳滤装置和反渗透装置,预处理装置、一级纳滤装置、二级纳滤装置、三级纳滤装置和反渗透装置的自身结构为公知技术。一级纳滤装置设有浓水出口,二级纳滤装置设有氯化钙浓液出口,三级纳滤装置设有浓水回流管线,返回至二级纳滤装置入口,反渗透装置设有产水出口和氯化钠浓液出口,产水一部分作为产品淡水,另一部分通过产水回流管线,返回至一级纳滤装置入口。
16.本实施例所采用主要装置如上所述,其中二级纳滤装置设计为三段、段间设置增压泵,以保证系统运行压力,一级纳滤装置、二级纳滤装置和反渗透装置浓水管线均设有px能量回收装置。
17.采用上述装置,以日产1000 m3氯化钙浓液系统为例,具体步骤如下:蒸氨废水先在沉淀池中预沉淀,所得上层清液典型成分如下成分ca
2+
mg
2+
na
+
cl-so
42-含量(mg/l)372191.21931395564418取上层清液159m3/h,经陶瓷膜过滤,产水用盐酸调节ph至6.5,得到浊度1.6ntu的蒸氨废清液;对蒸氨废清液进行稀释,稀释比例为淡水占蒸氨废清液体积的13%,然后加压进入一级纳滤装置,得到一级纳滤产水和一级纳滤浓水,一级纳滤对so
42-的截留率84%,对ca
2+
的截留率10.3%,对na
+
的截留率-3%,操作压力3.8 mpa,回收率71%,一级纳滤未添加阻垢剂,浓水侧无结垢现象,一级纳滤浓水外排另作他用;一级纳滤产水加压进入二级纳滤装置,得到二级纳滤产水和二级纳滤浓水,二级纳滤浓水即为产品氯化钙浓液,二级纳滤对ca
2+
的截留率81%,对na
+
的截留率-9%,操作压力7.8 mpa,回收率74%;二级纳滤产水加压进入三级纳滤装置,得到三级纳滤产水和三级纳滤浓水,三级纳滤浓水回流与一级纳滤产水混合,再次进入二级纳滤装置,三级纳滤对ca
2+
的截留率89%,对na
+
的截留率30%,操作压力4.4mpa,回收率70%;三级纳滤产水加压进入反渗透装置,得到反渗透产水和反渗透浓水,所得反渗透产水的50%回流至一级纳滤进水作为稀释水,回流量为20.5m3/h,以保证蒸氨废清液与淡水的混合比例,剩余反渗透产水为产品淡水,反渗透浓水为产品氯化钠浓液,反渗透脱盐率98%,回收率52%,操作压力5.6 mpa。
18.最终得到42 m3/h浓度为240g/l(20wt%)的氯化钙浓液,其中na
+
浓度16g/l,得到41 m3/h浓度为89.5g/l(8.5wt%)的氯化钠浓液,其中ca
2+
浓度为1g/l,另外得到20.5 m3/h的淡
水,蒸氨废清液的综合利用率65%。
19.实施例2本实施例所采用主要装置如实施例1所述,其中二级纳滤装置设计为二段、段间设置增压泵,以保证系统运行压力,一级纳滤装置、二级纳滤装置和反渗透装置浓水管线均设有透平式能量回收装置。
20.采用上述装置,以日产1000 m3氯化钙浓液系统为例,具体步骤如下:蒸氨废水先在沉淀池中预沉淀,所得上层清液典型成分如下成分ca
2+
mg
2+
na
+
cl-so
42-含量(mg/l)362080.71833692476205取上层清液186 m3/h,经中空纤维超滤膜过滤,产水用盐酸调节ph至6.0,得到浊度1.5ntu的蒸氨废清液;本实施例不对蒸氨废清液进行稀释,直接加压进入一级纳滤装置,得到一级纳滤产水和一级纳滤浓水,一级纳滤对so
42-的截留率88%,对ca
2+
的截留率20%,对na
+
的截留率-8%,操作压力4.9 mpa,回收率62%,由于原水中硫酸根浓度低,一级纳滤未添加阻垢剂,浓水侧无结垢现象,一级纳滤浓水外排另作他用;一级纳滤产水加压进入二级纳滤装置,得到二级纳滤产水和二级纳滤浓水,二级纳滤浓水即为产品氯化钙浓液,二级纳滤对ca
2+
的截留率79%,对na
+
的截留率-11%,操作压力7.2 mpa,回收率71%;二级纳滤产水加压进入三级纳滤装置,得到三级纳滤产水和三级纳滤浓水,三级纳滤浓水回流与一级纳滤产水混合,再次进入二级纳滤装置,三级纳滤对ca
2+
的截留率88%,对na
+
的截留率23%,操作压力3.6mpa,回收率64%;三级纳滤产水加压进入反渗透装置,得到反渗透产水和反渗透浓水,反渗透产水不回流,全部作为产品淡水,反渗透浓水为产品氯化钠浓液,反渗透脱盐率95%,回收率45%,操作压力5.2 mpa。
21.最终得到42 m3/h浓度为208.9g/l(18wt%)的氯化钙浓液,其中na
+
浓度17g/l,得到37 m3/h浓度为87.2g/l(8.3wt%)的氯化钠浓液,其中ca
2+
浓度为0.9g/l,另外得到30 m3/h的淡水,蒸氨废清液的综合利用率59%。
22.实施例3本实施例所采用主要装置如实施例1所述,其中二级纳滤装置设计为三段、段间设置增压泵,以保证系统运行压力,一级纳滤装置、二级纳滤装置和反渗透装置浓水管线均设有px能量回收装置。
23.采用上述装置,以日产1000 m3氯化钙浓液系统为例,具体步骤如下:蒸氨废水先在沉淀池中预沉淀,所得上层清液典型成分如下成分ca
2+
mg
2+
na
+
cl-so
42-含量(mg/l)3819813.21998698163523取上层清液154 m3/h,经有机管式膜过滤,产水用盐酸调节ph至5.5,得到浊度1.8ntu的蒸氨废清液;对蒸氨废清液进行稀释,稀释比例为淡水占蒸氨废清液体积的30%,然后加压进入一级纳滤装置,得到一级纳滤产水和一级纳滤浓水,一级纳滤对so
42-的截留率83%,对ca
2+
的
截留率9%,对na
+
的截留率-3%,操作压力3.9 mpa,回收率75%,一级纳滤按照3mg/l添加羟基乙叉二膦酸阻垢剂(hedp),浓水侧无结垢现象,一级纳滤浓水外排另作他用;一级纳滤产水加压进入二级纳滤装置,得到二级纳滤产水和二级纳滤浓水,二级纳滤浓水即为产品氯化钙浓液,二级纳滤对ca
2+
的截留率87%,对na
+
的截留率-8%,操作压力8.1 mpa,回收率77%;二级纳滤产水加压进入三级纳滤装置,得到三级纳滤产水和三级纳滤浓水,三级纳滤浓水回流与一级纳滤产水混合,再次进入二级纳滤装置,三级纳滤对ca
2+
的截留率87%,对na
+
的截留率26%,操作压力4.2mpa,回收率75%;三级纳滤产水加压进入反渗透装置,得到反渗透产水和反渗透浓水,反渗透产水的60%回流至一级纳滤进水作为稀释水,回流量为43.9 m3/h,以保证蒸氨废清液与淡水的混合比例,剩余反渗透产水为产品淡水,反渗透浓水为产品氯化钠浓液,反渗透脱盐率96%,回收率70%,操作压力6.9 mpa。
24.最终得到42 m3/h浓度为243g/l(20wt%)的氯化钙浓液,其中na
+
浓度15g/l,得到31 m3/h浓度为129g/l(12wt%)的氯化钠浓液,其中ca
2+
浓度为1.4g/l,另外得到29.3 m3/h的淡水,蒸氨废清液的综合利用率67%。
25.实施例4本实施例所采用主要装置如实施例1所述,其中二级纳滤装置设计为三段、段间设置增压泵,以保证系统运行压力,一级纳滤装置、二级纳滤装置和反渗透装置浓水管线均设有透平式能量回收装置。
26.采用上述装置,以日产1000 m3氯化钙浓液系统为例,具体步骤如下:蒸氨废水先在沉淀池中预沉淀,所得上层清液典型成分如下成分ca
2+
mg
2+
na
+
cl-so
42-含量(mg/l)3687510.51875794066457取上层清液135 m3/h,经陶瓷膜过滤,产水用盐酸调节ph至6.0,得到浊度1.7ntu的蒸氨废清液;对蒸氨废清液进行稀释,稀释比例为淡水占蒸氨废清液体积的50%,然后加压进入一级纳滤装置,得到一级纳滤产水和一级纳滤浓水,一级纳滤对so
42-的截留率81%,对ca
2+
的截留率8%,对na
+
的截留率-2%,操作压力3.5 mpa,回收率80%,一级纳滤未添加阻垢剂,浓水侧无结垢现象,一级纳滤浓水外排另作他用;一级纳滤产水加压进入二级纳滤装置,得到二级纳滤产水和二级纳滤浓水,二级纳滤浓水即为产品氯化钙浓液,二级纳滤对ca
2+
的截留率82%,对na
+
的截留率-7%,操作压力7.5 mpa,回收率79%;二级纳滤产水加压进入三级纳滤装置,得到三级纳滤产水和三级纳滤浓水,三级纳滤浓水回流与一级纳滤产水混合,再次进入二级纳滤装置,三级纳滤对ca
2+
的截留率84%,对na
+
的截留率29%,操作压力3.4mpa,回收率74%;三级纳滤产水加压进入反渗透装置,得到反渗透产水和反渗透浓水,反渗透产水的80%回流至一级纳滤进水作为稀释水,回流量为65.1 m3/h,以保证蒸氨废清液与淡水的混合比例,剩余反渗透产水为产品淡水,反渗透浓水为产品氯化钠浓液,反渗透脱盐率97%,回收率71%,操作压力6.2 mpa。
27.最终得到42 m3/h浓度为235g/l(20wt%)的氯化钙浓液,其中na
+
浓度13g/l,得到35 m3/h浓度为108g/l(10wt%)的氯化钠浓液,其中ca
2+
浓度为1.5g/l,另外得到16.3 m3/h的淡水,蒸氨废清液的综合利用率69%。