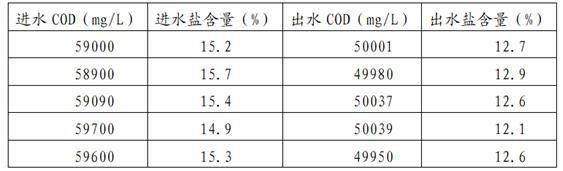
橡胶促进剂dcbs母液废水深度处理并回收bt工艺
技术领域
1.本发明属于废水处理领域,具体涉及一种橡胶促进剂dcbs母液废水深度处理并回收bt工艺。
背景技术:2.橡胶促进剂dcbs合成过程中会产生一些副产物,此副产物是一些化学组成和结构比较稳定,难降解的杂环类化合物,此副产物溶解到水中,导致废水成分复杂,难降解,生物毒性大,严重抑制微生物对已生化有机物的降解,此废水经过蒸发浓缩后母液更难于处理,主要此废水含盐量到,含盐量高达20%以上,有机物含量cod高达50000mg/l以上,此废水经过处理去除有机物后也难以生化,对菌种要求比较高,故此废水处理难度大,高cod,高盐,采用一种工艺方法很难实现完全降解。
3.针对以上废水目前的处理方案有以下3种:一)絮凝沉降+活性炭吸附+多效蒸发:在絮凝剂的条件下先沉降,沉降去除一部分树脂,再经过活性炭吸附后,再去蒸发浓缩,凝水返回到车间生产系统循环使用。
4.二)mvr蒸发+芬顿氧化法:采用mvr直接蒸发此废水,凝水再经过芬顿氧化后返回到生产系统循环使用,母液返到原水再次进行处理。
5.三)萃取法+mvr蒸发:此废水首先进行预处理,采用萃取剂把部分有机物先回收,萃取剂重复使用,再进行mvr蒸发浓缩,凝水直接返回到生产系统循环使用,母液返到原水再次进行处理。
6.针对方案一)因此废水盐含量高、cod高有机物含量高,仅仅通过沉降絮凝吸附很难彻底降解有机物,循环一定周期后,凝水cod会上升,验证影响车间产品质量。
7.针对方案二)原水未经过预处理直接mvr蒸发浓缩,废水cod高,有机物多,沸点提升,mvr系统运行负荷大,对设备损耗大,凝水中低挥发有机物含量高,有机物多,芬顿氧化,成本高。
8.针对方案三)因废水cod高,含盐高,有机物成分复杂,对萃取剂要求高,并且引入新的化学成分,一旦萃取过程中分离不彻底,萃取剂带入mvr蒸发系统,很容易进到凝水中,凝水再返回车间使用将影响产品质量,同时萃取剂损耗也比较高,成本高。
9.综上所述,因橡胶促进剂废水成分复杂,含盐量高,单一方案很难完全处理,多家厂家采用综合治理方案,已见报道的有“蒸发+吸附”,“氧化+蒸发”、“高级氧化+混凝沉淀+过滤+活性炭吸附”等。但纵观诸多处理方案,尽管可以解决目前短期排放问题,但仍然存在设备投资大,运行成本高,处理过程很难长期稳定运行等众多问题。
技术实现要素:10.本发明的目的在于克服现有技术中的缺点,提供一种橡胶促进剂dcbs母液废水深度处理并回收bt工艺。
11.为实现上述目的,本发明采用的技术方案为:
一种橡胶促进剂dcbs母液废水深度处理并回收bt工艺,包括下述步骤:1)橡胶助剂dcbs母液废水,cod>50000mg/l,经过-10℃降温,去除一部分盐和有机物,使其cod稳定在50000mg/l;2)再经过催化氧化,析出大部分有机物后cod降到5000mg/l以下,再进行过滤,取滤液去mvr蒸发系统;3)滤液经过mvr蒸发浓缩,母液返回到原水系统再处理;凝水经活性炭吸附后cod<500mg/l,返回到生产系统循环使用;4)饱和后的活性炭经过蒸汽反洗后,可以回收bt原材料。
12.具体的,步骤2)中催化氧化的催化剂为硫酸铜,催化剂含量为5wt
‰
;反应温度为150-280℃,反应压力为2-5mpa。
13.具体的,步骤3)中mvr蒸发浓缩比控制在80%。
14.具体的,步骤4)中活性炭反洗的温度为100-130℃,蒸汽压力0.1-0.4mpa,时间为0.5-2h。
15.优选的,步骤2)中的反应为温度250℃,反应压力为5mpa。
16.优选的,步骤3)中活性炭的加入量与凝水的体积质量比1:100。
17.优选的,步骤4)中活性炭反洗的温度为120-130℃,蒸汽压力0.24mpa,时间为1h。
18.与现有技术相比,本发明的有益效果是:本发明开发了一种橡胶促进剂dcbs母液废水处理工艺方法,因dcbs在合成过程中有大量的副产物,主要是一些苯环类的复杂的有机物的混合物,很难彻底降解,并且此有机物生物毒性大,难于生化,同时dcbs氧化合成过程中容易生成磺酸盐导致回收的氯化钠中有大量的磺酸盐,盐纯度不够,针对以上高盐、高cod的废水,采取如下工艺:该工艺采用先降温沉降后去除废水中的磺酸盐,把磺酸盐单独从废水中收集,降低了后续催化氧化的难度,同时提升了回收工业盐的纯度。
19.再催化氧化,在催化剂存在的条件下,压力5mpa,温度250℃的条件下,可以把大分子有机物氧化成二氧化碳和水,有机物物彻底的降解,可以去除大部分的cod。
20.再经过mvr蒸发浓缩,采用mvr蒸发可以节约蒸汽,同时经过前面的预处理,回收的氯化钠盐纯度高,可以达到工业盐要求,mvr母液再次返回到原水系统,凝水进行下一步处理。
21.凝水经过活性炭吸附后,返回到生产系统循环使用,活性炭吸附能力强,可以有效去除剩余的有机物,出水达到外排要求。同时活性炭通过蒸汽再生可以达到循环利用的要求,蒸汽再生条件简单容易操作,同时蒸汽凝水经过静止分层的就可以从中把油相分离出来,分离的油相为回收的bt,回收bt纯度高,回收bt作为合成橡胶促进剂mbt的原料,蒸汽凝水再次返回到原水系统处理。
22.该工艺采用降温沉降把母液中磺酸盐进行回收,降低了废水的盐浓度,再催化氧化去除大部分有机物,提高了进mvr系统的水质,降低了mvr蒸发的负荷,凝水再经过活性炭吸附后提高了生产回用水的质量,同时还可以回收废水中的bt,作为mbt的原料使用,以上工艺的有效结合,彻底解决了此母液高盐高cod废水的难题,可以完全降解有机物大分子,提升了回用水质量,同时提升了盐的质量,并且还可以把废水中有机物有效回收,处理成本低,同时还解决了环保问题。
具体实施方式
23.为了使本技术领域的技术人员更好地理解本发明的技术方案,下面结合实施例对本发明作进一步的详细说明。
24.实施例1:本实施例提供了一种处理橡胶促进剂废水方法,所述方法包括如下步骤:(1)将橡胶促进剂dcbs母液废水(cod》50000mg/l)低温沉降条件下,可以有效去除cod,并降低盐含量; 表1示出降温沉降下处理效果。此废水通过降温可以有效的把磺酸钠盐去除,并同时cod也降低,可以有效地降低催化氧化的难度;表1 (2)将废水(cod≈50000mg/l)中先加入大约5wt
‰
铜类的催化剂硫酸铜,催化氧化降解有机物(cod<5000mg/l)温度250℃条件下;分别考察在2mpa/3mpa/4mpa/5mpa条件下氧化效果;表2示出不同压力条件下氧化效果;表2不同压条件下氧化效果有所区别,5mpa条件下cod去除率最高达到96%效果最佳。
25.(3)将废水(cod≈50000mg/l)中先加入大约5
‰
铜类的催化剂,催化氧化降解有机物(cod<5000mg/l),压力5mpa条件下,分别考察在150℃/180℃/200℃/250℃/280℃条件下氧化效果;表3示出不同温度条件下氧化效果。
26.表3
通过以上数据可以看出此氧化过程,在温度180~280℃,压力2~5mpa条件,均可达到效果,最优条件是温度250℃,压力5mpa。
27.(4)氧化后的滤液经过mvr进行蒸发浓缩,浓缩比例80%,进水cod不同,凝水cod以及母液cod有所不同;表4示出不同废水蒸发凝水cod。
28.表4mvr蒸发过程中,浓缩比例控制在80%,对凝水和母液cod有一定的影响,浓缩比例控制在80%时,氧化后不同cod水经过,凝水cod均能控制在1000mg/l,母液cod小于原水,返回到原水系统,不影响处理效果。
29.(5)mvr蒸发的cod<1000mg/l凝水经过活性炭吸附后出水cod<500mg/l,活性炭吸附罐大约10m3活性炭,吸附水量不同出水cod不同。表5示出附水量不同对出水效果影响。
30.表5同一批活性炭当吸附水量超过1000m3时,出水cod开始上升,lm3活性炭最优处理水量小于活性炭量的100倍。
31.(6)活性炭饱和后,采用蒸汽反洗再生活性炭,使活性炭具备再次吸附能力,反洗后通过进出水cod考察吸附能力,并从蒸汽凝水中回收bt,蒸汽压力0.2mpa,再生1h条件下;
分别考察在100℃/110℃/120℃/130℃/条件下反洗效果;表6示出不同温度条件下反洗效果。
32.表6通过以上数据可以看出活性炭反洗再生过程,压力0.2mpa条件下,在温度100~130℃,均可达到效果,最优条件是温度120~130℃,每次反洗再生回收bt可以达到55l,纯度可以达到98%以上。
33.(7)活性炭饱和后,采用蒸汽反洗再生活性炭,使活性炭具备再次吸附能力,反洗后通过进出水cod考察吸附能力,并从蒸汽凝水中回收bt,蒸汽温度120℃,再生1.5h条件下,分别考察在0.1mpa/0.2mpa/0.3mpa/0.4mpa/条件下反洗效果;表7示出不同压力条件下反洗效果。
34.表7通过以上数据可以看出活性炭反洗再生过程,温度120℃条件下,在压力0.1~0.4mpa下,均可达到效果,最优条件是温度0.2mpa,当蒸汽压力低于0.2mpa时升温时间比较长,当高于0.2mpa时升温快,再生1.5小时,能源浪费,最优压力0.2mpa,每次反洗再生回收bt可以达到55l,纯度可以达到98%以上。
35.(8)活性炭饱和后,采用蒸汽反洗再生活性炭,使活性炭具备再次吸附能力,反洗后通过进出水cod考察吸附能力,并从蒸汽凝水中回收bt,蒸汽温度120℃,蒸汽压力2mpa条件下,分别考察在0.5h/1h/1.5h/2h/条件下反洗效果;表7示出不同再生时间反洗效果。
36.表8
通过以上数据可以看出活性炭反洗再生过程,压力2mpa条件下,在温度120℃,再生1.5h以上均可达到效果,为节约能源同时还可以达到效果,现最优再生时间1.5h,每次反洗再生回收bt可以达到55l,纯度可以达到98%以上。
37.本发明将四种工艺方案的有效结合,解决了以往水处理的难题,处理工艺经济可行,降低了原处理手段的环保风险。
38.以上所述仅是本发明的优选实施方式,应当指出,对于本技术领域的普通技术人员来说,在不脱离本发明原理的前提下,还可以做出若干改进和润饰,这些改进和润饰也应视为本发明的保护范围。