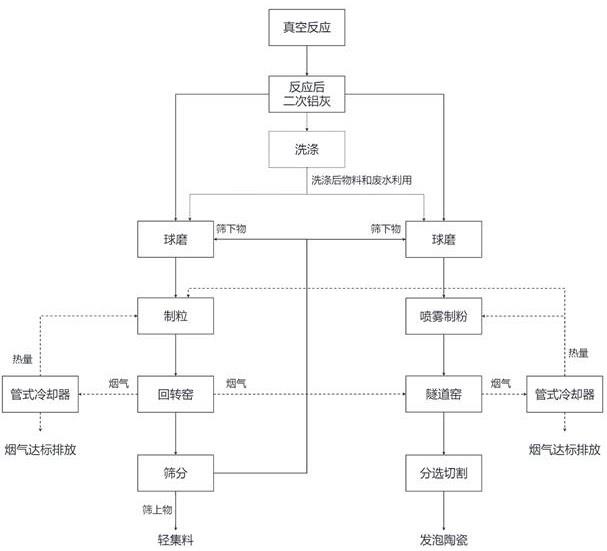
1.本发明属于危险废物处理领域,涉及二次铝灰处理方法,具体涉及一种二次铝灰安全控制系统及资源化工艺。
技术背景
2.我国是全世界最大的金属铝生产国和消费国,每年生产能力为6000万吨,实际生产能力每年也达4000余万吨。铝灰产生于金属铝发生熔融的生产工序,含铝量10%~80%不等,其中的铝约占铝生产过程中总损失量的1%~12%。
3.铝灰渣中存在着大量的有毒元素,如果将铝灰填埋,对当地土壤及水资源会造成严重污染,造成周边牲畜、居民和植物重金属中毒;铝灰渣中还含有大量的可溶性盐,填埋会导致周边土壤盐碱化,农作物大量死亡。传统处置方式基本是填埋或露天堆放,这样的处置措施不仅占用了大量土地,而且其中所含的可溶性氟化物会通过风吹、日晒、雨淋的作用转移或挥发进入大气,或随雨水混入江河、渗入地下污染土壤和地下水,对动植物生长及人体产生很大损害,破坏生态环境,影响生态平衡。
4.2020年11月5日,生态环境部审议并原则通过制修订的《国家危险废物名录》,已明确铝灰渣为危险固体废弃物,铝灰渣尤其是二次铝灰(铝灰提铝后的剩余部分)的问题已经到了非处理不可的地步,其紧迫性可谓迫在眉睫。铝灰渣含有铝及多种有价元素,是一种可再生资源。如果不加以回收利用,不仅浪费资源,而且污染环境。从铝灰中回收铝及其他有价元素,充分合理利用,对提高企业的经济效益,保护生态环境具有重要的现实意义和实用价值。
5.中国专利cn113735611a公开了一种铝灰渣高温自发泡制备低收缩多孔陶瓷的方法,但该工艺烧结温度高,且需用到粘结剂,原料成本高,能耗高。专利cn113788623a中公开了一种二次铝灰渣无需预处理制备泡沫微晶玻璃的方法,同样该专利烧成温度较高,需使用粘结剂,都难以实现产业化。且该工艺以二次铝灰渣中的氮化铝作为发泡剂,氮化铝遇水会反应放出氨气,不仅造成环境污染,还存在爆炸风险。
6.二次铝灰中除了氮化铝,还有碳化铝和活性铝,其中氮化铝和氮化铝遇水极易反应生成氨气和甲烷,大量的氨气和甲烷对环境有很大的伤害,且氨气的爆炸极限为16~25%,甲烷的爆炸极限5~15%;活性铝遇水反应生成氢气,氢气无色无味,氢气的爆炸极限为4~75.6%,一旦引起燃烧和爆炸,在工业生产中将是极大的危害,因此在对二次铝灰资源化处理时,如何在脱氨固氟过程中避免爆炸以保证安全高效的工业化生产,同时降低生产能耗,并将二次铝灰转化为具有高经济价值的产品是亟待解决的问题。
技术实现要素:7.针对上述问题,本发明提供一种二次铝灰安全控制系统及资源化工艺,不仅可以安全高效地对二次铝灰进行脱氨固氟处理,降低生产能耗,还可以将其制备成高强度的轻集料或发泡陶瓷等产品。
8.本发明的技术方案是:先提供一种二次铝灰安全控制系统,用于对二次铝灰进行脱氨固氟处理,即对二次铝灰进行真空反应。
9.所述的二次铝灰安全控制系统包括检测模块、给料模块、下料模块、真空模块,其中各模块的具体功能如下,检测模块:用于对待处理二次铝灰进行成分检测,并记录结果,或将已有样品检测结果进行整理,记录备用;至少得到物料中aln的质量分数,al的质量分数,al4c3的质量分数的具体数值;给料模块:用于对经过检测模块处理后的二次铝灰进行称重,并送入真空反应设备,记物料总重量为 ,给料模块还可以用于将水或助剂送入真空反应设备,以便进行反应,其中助剂包括固氟剂,固氟剂可采用生石灰。
10.下料模块:用于将反应后的物料排出真空反应设备,下料模块主要包括输料管道;通过输料管道将物料从真空反应设备中转移出来,便于在后续处理工艺中使用。
11.真空模块:用于提供真空反应场所并控制反应条件,包括真空反应设备及其控制软件。真空反应设备主要包括真空罐。
12.控制软件包括参数设置单元、定时单元、空气量计算单元和真空处理单元,其中参数设置单元用于输入当前生产批次的物料中的具体数值;定时单元用于设定当前生产批次的二次铝灰在真空反应设备中的反应时间t;空气量计算单元用于根据参数设置单元和定时单元的具体输入值来计算反应过程中反应设备允许通入的最大空气进入量;真空处理单元用于根据的计算结果来控制真空反应设备的真空度,在反应过程中控制进入真空反应设备的氮气通入量,通过控制氮气的通入量使真空反应设备的真空度保持动态恒定,同时使氧气值含量低于5.4%,防止爆炸。
13.空气量计算单元采用的函数关系式如下:其中表示时间微分,a、b、c为相应组份的权重参数,可通过相应物料的爆炸极限值计算或通过实验测量得出,a∈[2.000,4.000]、b∈[25.000,30.000]、c∈[5.000,10.000]。
[0014]
优选的,函数关系式中的a=2.869,b=29.867,c=8.867。
[0015]
进一步的,反应时间为30~120min。
[0016]
由于反应过程保持真空度恒定,单位时间内通入空气量也恒定,随着反应进行中氨气、氢气和甲烷的生成和排出,使空气和气体生成量始终保持在爆炸极限量以下,确保整个反应过程的安全。同时可将氨气、氢气和甲烷等气体进行收集储存,以便作为燃料使用。
[0017]
在现有技术中,处理二次铝灰的真空设备大都不能精确计算出空气量,所以其为了避免爆炸,其真空度的数值总是设置为远远超过实际生产所需的真空度,从而使得真空设备的运行成本较高,而本发明通过计算出精确的通入空气量的临界值,可以根据每批次
物料的真实情况来确定真空设备在生产过程中所需保持的真空度,从而大大节省了真空设备运行时的生产成本。
[0018]
本发明还提供一种二次铝灰资源化工艺,将经过上述控制系统脱氨固氟后的二次铝灰按如下步骤处理:s1:二次铝灰过筛提铝后与粘土、烧结助剂定量混合后送入球磨机进行球磨;混合时使用的配方为:二次铝灰60~80%、粘土10~30%、烧结助剂1~10%,其中烧结助剂为硫酸亚铁、生石灰、氟化钙中的一种或多种。
[0019]
优选的,本步骤s1中,混合时使用的配方也可以为:(二次铝灰+筛下物)60~80%、粘土10~30%、烧结助剂1~10%,其中烧结助剂为硫酸亚铁、生石灰、氟化钙中的一种或多种。
[0020]
进一步的,在步骤s1中,球磨机中添加水的比例为:混料:水=1:0.5~1。进一步的,在步骤s1中,球磨时间为0.5~2h,浆料细度≤80目。
[0021]
s2:将磨料放入造粒机进行制粒;优选的,球料粒径为5~25mm。
[0022]
s3:将球料放入烧成窑内高温烧制,得到初步产品;优选的,控制烧成窑中烧成段最高温度为900~1000℃,烧成时间为20min-100min。
[0023]
s4:对产品进行筛选,筛分直径为5~25mm,分成筛上物和筛下物,其中筛上物作为轻集料产品,筛下物作为生产原料,集中存放备用;s5:将提铝后的二次铝灰和/或筛下物不经洗涤,直接与粘土、矿渣、发泡剂、抑制剂定量混合后送入球磨机球磨;进一步的,在本步骤s5中混合时使用的配方为:(二次铝灰+筛下物)30~60%、粘土20~30%、矿渣10~30%、发泡剂1~5%、抑制剂1~5%,其中发泡剂为碳酸钙、碳粉、石墨、氯化镁等其中一种或多种。
[0024]
进一步的,在步骤s5中,球磨机中添加水的比例为:混料:水=1:0.5~1。
[0025]
进一步的,在步骤s5中,球磨时间为0.5~2h,浆料细度≤80目。
[0026]
s6:通过喷雾制粉后得到粉料,再装入窑车模具内;进一步的,本步骤s6中,喷雾制粉所得粉料粒径分布控制为:30-50目(10%-25%),50-70目(40%-65%),70-100目(20%-35%),100目以上(2%)。
[0027]
进一步的,粉料含水率控制在6%-10%。
[0028]
s7:将窑车放入烧成窑中进行烧制,得到发泡陶瓷半成品;进一步的,先将烧成窑中的温度从室温升至850℃,升温速率为150~300℃/h;从850℃升至烧成温度1000℃~1150℃,升温速率为300~450℃/h;然后,在烧成温度保温0.5~1h之后;从烧成温度降温至500℃,降温速率为600~800℃/h;最后,从500℃降至室温,降温速率为300~500℃/h,得到发泡陶瓷板半成品。
[0029]
s8:对半成品进行拣选、切边,最终制得成品。
[0030]
进一步的,可以在s1步骤中对提铝后的二次铝灰先进行洗涤,从洗涤水中回收可溶性氯盐,剩余废水送入s1或s5步骤进行回用;或者在s4步骤对筛上物进行洗涤,回收可溶性氯盐以使产品含氯量不超标,剩余废水送入s1或s5步骤进行回用。
[0031]
进一步的,在步骤s3或步骤s7中,烧成窑使用的燃料是来自前述的二次铝灰安全控制系统在处理二次铝灰的过程中产生的nh3、h2、ch4等可燃气体,或者是上述气体与其他燃料的混合物。
[0032]
进一步的,在处理二次铝灰时,也可以仅使用上述二次铝灰资源化工艺中的部分工艺步骤,例如可以仅使用其中的s1-s4步骤来生产轻集料,也可以直接从s5步骤开始来生产发泡陶瓷。
[0033]
本发明相对于现有技术的优势体现在:(1)通过控制系统,可以有组织地根据物料的实际情况,通过对反应设备的真空度进行调整,从而使密闭容器内的空气量始终低于氢气、甲烷、氨气的爆炸极限量,保证二次铝灰资源化处理过程中的安全;同时,根据物料的实际情况来调节真空度,可以在避免爆炸的同时尽可能的降低真空反应设备的能耗。
[0034]
(2)本发明中通过将二次铝灰烧制为陶粒及发泡陶瓷,将危废转变为具有更高价值的产品。
[0035]
(3)二次铝灰脱氨固氟使用的固氟剂为生石灰,生成caf2沉淀,氟化钙可降低难熔金属的熔点,降低烧结温度,本身可作为一种助熔剂,还能增强烧结时熟料液相粘度,促进硅酸三钙的形成,增强熟料的强度。
[0036]
(4)二次铝灰中含有少量氯离子,在高温环境下可以与部分金属发生反应,形成氯盐随烟气挥发,可通过水洗回收。
[0037]
(5)先将二次铝灰进行陶粒烧制,再将已经玻璃化的筛下熟料烧制成发泡陶瓷,降低能耗,最大程度将二次铝灰资源化。
[0038]
(6)真空反应过程产生的nh3、h2、ch4均可燃烧放出热量,其中nh3和h2更是优质的环保气体, 通过混燃技术将前端工艺产物燃烧为后端工艺提供热量,无须对气体产物进行单独处理,优化工艺、提高协同性的同时大大降低了能耗。
附图说明
[0039]
图1是本发明的二次铝灰资源化工艺的流程图。
具体实施方式
[0040]
将结合具体实施例对本发明做进一步详细说明,本实施例中未具体说明的方法或工艺,均为现有技术。
[0041]
实施例1本实施例中利用二次铝灰生产轻集料陶粒,先要利用安全控制系统对二次铝灰进行脱氨固氟预处理,具体过程如下:第一步,利用检测模块对物料进行成分检测,检测模块中使用的仪器为包括液相色普仪、质普仪在内的检测设备产品,最终得到的检测结果为:第二步,将经过检测后的当前批次二次铝灰进行称重,记录重量为:,并送入1l的真空反应设备(真空罐)中。
[0042]
第三步,在控制软件中输入相关参数,设定的反应时间为 30min,控制软件通过函
数关系式(1)计算最大空气通入量,在本实施例中,函数关系式中的a=2.869,b=29.867,c=8.867,算得第四步,向设备中加0.5l水;同时,真空反应设备按控制软件的计算结果开始工作,以保证内部的空气不超过上一步的数值;并且收集好反应过程中生产的氨气、氢气和甲烷等气体,便于在烧制工艺中作为燃料使用。
[0043]
第五步, 在反应结束后,通过下料模块排出物料,即得到脱氨固氟预处理的二次铝灰。
[0044]
对经过上述预处理后得到二次铝灰进行过筛提铝,剩下的二次铝灰再进行轻集料烧制工艺,烧制工艺的具体过程如下:第一步:按二次铝灰60%、红泥30%、生石灰10%的比例进行均匀混合后,放入球磨机进行球磨。球磨机中添加水的比例为:混料:水=1: 0.5,球磨时间为0.5h,浆料细度为80目。具体的物料配方如下表1:第二步:将干燥后粉料放入造粒机进行制粒,球料粒径为5~25mm。
[0045]
第三步:将球料放入窑内高温烧制,以300℃/h的升温速度从室温升至900℃,烧成时间为45min,后降温至室温,得到产品。
[0046]
第四步:对产品进行筛选,筛分直径为5mm,筛上物为轻集料,筛下物集中回收。
[0047]
所得产品的技术参数如下表2:产品符合轻集料国家标准gb/t17431.1-2010要求,产品经质检部门检测,其产品质量达到优等品。
[0048]
实施例2本实施例中利用二次铝灰生产轻集料发泡陶瓷,先利用安全控制系统对二次铝灰进行脱氨固氟预处理,脱氨固氟预处理过程与实旋例1相同。
[0049]
对经过预处理后得到的物料进行过筛提铝,剩下的二次铝灰再进行发泡陶瓷烧制工艺,烧制工艺的具体过程如下:第一步:按二次铝灰40%、红泥20%、萤石尾矿30%、碳酸钙 5%、抑制剂5%定量混合后送入球磨机球磨,球磨机中添加水的比例为:混料:水=1: 1,球磨时间为2h,浆料细度为80
目。具体物料配方如下表3:第二步:将浆料进行干燥后得到粉料,再装入窑车模具内,喷雾制粉所得粉料粒径分布控制为:30-50目(10%-25%),50-70目(40%-65%),70-100目(20%-35%),100目以上(2%),粉料含水率控制在6%-10%。
[0050]
第三步:将窑车放入窑中进行烧制,先将烧成窑中的温度从室温升至850℃,升温速率为150~300℃/h;从850℃升至烧成温度1000℃~1150℃,升温速率为300~450℃/h;然后,在烧成温度保温0.5~1h之后;从烧成温度降温至500℃,降温速率为600~800℃/h;最后,从500℃降至室温,降温速率为300~500℃/h,得到发泡陶瓷板半成品。
[0051]
第四步:对半成品进行拣选、切边,最终制得成品。
[0052]
将实施例的最终产品做检测,其中吸水率的测试参见gb/t3810.3(真空法),防火等级的测试参见gb/t8624,抗压强度、体积密度的测试参见gb/t5486,导热系数参见gb/t10295,测试结果如下表4所示:由检测结果可以看出,本发明的发泡陶瓷气孔均匀、气泡形状一致;且导热系数、抗压强度等理化性能良好。
[0053]
实施例3本实施例中利用二次铝灰生产轻集料陶粒,先要利用安全控制系统对二次铝灰进行脱氨固氟预处理,具体的脱氨固氟处理过程与实旋例1相同。
[0054]
对经过脱氨固氟预处理后得到物料进行过筛提铝,剩下的二次铝灰再进行陶瓷化工艺,烧制工艺的具体过程如下:第一步:按二次铝灰80%、红泥10%、生石灰10%的比例进行均匀混合后,放入球磨机进行球磨。球磨机中添加水的比例为:混料:水=1: 0.5,球磨时间为0.5h,浆料细度为80目。具体物料配方如下表5:
第二步:将干燥后粉料放入造粒机进行制粒,球料粒径为5~25mm。
[0055]
第三步:将球料放入窑内高温烧制,以300℃/h的升温速度从室温升至900℃,烧成时间为45min,后降温至室温,得到产品。
[0056]
第四步:对产品进行筛选,筛分直径为5mm,筛上物为轻集料,筛下物集中回收。
[0057]
第五步:按筛下物60%、红泥25%、萤石尾矿10%、碳粉 3%、抑制剂2%定量混合后送入球磨机球磨,球磨机中添加水的比例为:混料:水=1: 1,球磨时间为1h,浆料细度为80目;具体如下表6:第六步:将浆料进行干燥后得到粉料,再装入窑车模具内,喷雾制粉所得粉料粒径分布控制为:30-50目(10%-25%),50-70目(40%-65%),70-100目(20%-35%),100目以上(2%),粉料含水率控制在6%-10%。
[0058]
第七步:将窑车放入窑中进行烧制,先将烧成窑中的温度从室温升至850℃,升温速率为150~300℃/h;从850℃升至烧成温度1000℃~1150℃,升温速率为300~450℃/h;然后,在烧成温度保温0.5~1h之后;从烧成温度降温至500℃,降温速率为600~800℃/h;最后,从500℃降至室温,降温速率为300~500℃/h,得到发泡陶瓷板半成品。
[0059]
第八步:对半成品进行拣选、切边,最终制得成品。
[0060]
将实施例的最终产品分别做检测,测试结果如下表7和表8所示:产品符合轻集料国家标准gb/t17431.1-2010要求,产品经质检部门检测,其产品质量达到优等品。
[0061]
由检测结果可以看出,本发明的发泡陶瓷气孔均匀、气泡形状一致;且导热系数、抗压强度等理化性能良好。
[0062]
以上仅为本发明的部分实施例而已,并不用于限制本发明,对于本领域的技术人员来说,本发明可以有前述各种技术特征的组合和变型,本领域的技术人员在不脱离本发明的精神和范围的前提下,对本发明的改进、变型、等同替换,或者将本发明的结构或方法用于其它领域以取得同样的效果,都属于本发明包括的保护范围。