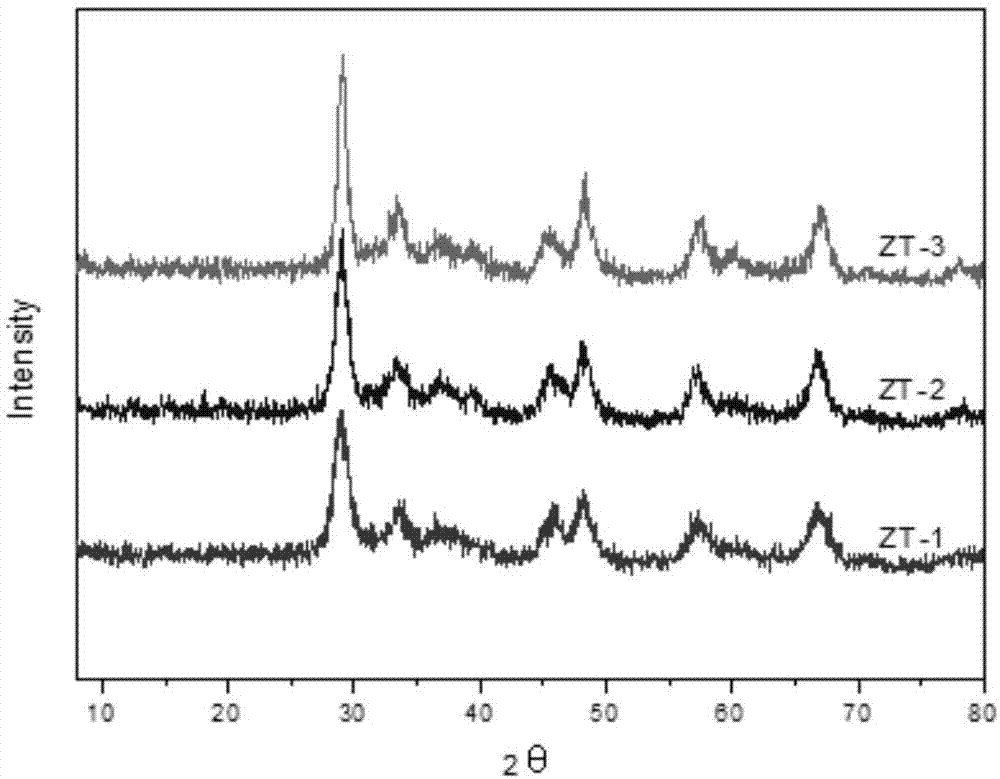
本发明涉及一种铈锆铝复合金属氧化物及其制备方法,还涉及一种以铈锆铝复合金属氧化物为载体的镍基催化剂及其制备方法。
背景技术:
:由于镍的廉价易得及其良好的催化性能,镍基催化剂是目前催化工业中应用最广泛的催化剂之一,广泛应用于催化加氢、催化重整、甲烷部分氧化及甲烷催化裂解反应中。其所参与的这些反应均涉及高温反应条件,具体的如催化加氢领域中大规模煤制天然气、甲烷催化重整制氢、甲烷部分氧化、甲烷裂解等,均需要镍基催化剂在高温条件下使用且具有好的高温稳定性、活性及抗积碳性能,而目前催化剂的耐高温性能仍是制约镍基催化剂应用的关键。铈锆铝复合氧化物以其优异的耐高温性能、高氧容性及助活性金属分散性能常被作为载体应用于制备汽车尾气净化催化剂,所负载的活性金属多为贵金属,而以铈锆铝复合氧化物为载体制备具有较好高温稳定性的镍基催化剂尚少见报道。另外,一般情况下,因贵金属负载量较小,对催化剂比表面积及吸水等物理性质要求较低,如专利cn106732578a所公开的铈锆铝复合氧化物比表面积为50-90m2/g,而专利cn104226295b所公开的铈锆铝复合氧化物比表面积仅为50.7m2/g。而载体比表面积、孔结构、吸水率等物理性质对于高活性金属负载量的镍基催化剂尤为重要。cn103706370a公开了一种煤制天然气高温甲烷化催化剂及其制备方法。在该专利中用共沉淀法制备铈锆铝复合氧化物,然后将铈锆铝复合氧化物粉体与含镍及助剂的浸渍液浸渍,然后干燥、造粒然后成型得到适用于煤制天然气的甲烷化催化剂,该催化剂具有较好的高温活性及热稳定性。但专利公开的沉淀法制备铈锆铝复合氧化物,需要经过多次的洗涤过程步骤较为繁复。cn102784639a公开了一种煤层气脱氧催化剂及其制备方法和应用,其中所述催化剂包括铂(pt)氧化物作为活性成分,以及载体,其中所述载体包括铈锆复合氧化物(ce-zr-o)、拟薄水铝石(al2o3·nh2o)和氢氧化铝(yh),而所述制备方法包括载体制备和浸渍活性组分两个部分,得到所述煤层气脱氧催化剂。该发明的催化剂起活温度为300-360℃,高温稳定性好,产品气中氧含量可降到5ppm以下,表现出良好的反应精度,而且无需预还原,简化了开车流程。技术实现要素:基于以上现状及问题,本发明提供一种具有高比表面积的铈锆铝复合金属氧化物及以该氧化物为载体的一种耐高温的镍基催化剂及制备方法。本发明提供的一种铈锆铝复合金属氧化物载体,其包括氧化铝、铈锆复合氧化物、氧化硅及氧化钛,以铈锆铝复合金属氧化物载体的总质量为基准,其中,氧化铝占50-90wt%,优选65-80wt%,更优选70-75wt%,铈锆复合氧化物为9-49wt%,优选15-30wt%,更优选17-22wt%,氧化硅0.5-5wt%,优选1-4wt%,更优选1.5-3.5wt%,氧化钛为0.5-5wt%,优选1-4wt%,更优选1.5-3.5wt%,铈锆复合氧化物中氧化铈与氧化锆质量百分含量比为1-2.5:1,优选1.5-2:1。进一步地,以铈锆铝复合金属氧化物载体的总质量为基准,铈锆复合氧化物除了氧化铈与氧化锆以外还可掺杂0.5-1.8wt%的氧化钇,优选0.8-1.5wt%。所述铈锆铝复合金属氧化物载体为柱状颗粒,强度为18-52n/mm,bet比表面积90-220m2/g,吸水率40-70%,孔径为9-14nm,优选地,强度为30-45n/mm,bet比表面积120-180m2/g,吸水率50-60%。其通过以下步骤制备(方法一):(1)将硅溶胶(优选酸性硅溶胶或硅酸水溶胶,例如30wt%的酸性硅溶胶)加入到稀硝酸(例如0.5-5.0wt%)的稀硝酸中搅拌均匀,使得液固质量比为1:0.5-3,优选1:0.8-1.3;(2)将铈锆复合氧化物粉、大孔氢氧化铝粉、氧化钛、田菁粉、sb粉在捏合机中混合均匀后,加入步骤(1)所得的稀硝酸混合物,继续捏合均匀后研磨过筛(例如研磨后过50-500目筛,优选100-250目筛);(3)向步骤(2)制得的含湿固体物料中加入适量脱模剂(例如固体物料的1.5-3wt%的硬脂酸镁和/或硬脂酸钙),打片成柱状颗粒,焙烧获得铈锆铝复合氧化物载体,其中,铈锆复合氧化物粉为8-30重量份,优选10-25重量份;大孔氢氧化铝粉占45-70重量份,优选55-65重量份;sb粉为15-25重量份,优选18-22重量份;田菁粉1.5-5重量份,优选2-4重量份;硅溶胶为1.2-11.7重量份,优选2-10重量份;氧化钛为0.35-3.5重量份,优选0.8-2重量份。或通过以下步骤制备(方法二):(1)将第一部分sb粉(拟薄水铝石粉)及硅溶胶(优选酸性硅溶胶或硅酸水溶胶)加入到稀硝酸(例如0.5-5wt%的稀硝酸)中搅拌制备得到铝胶,使得液固质量比为1:0.5-3,优选1:0.8-1.3;(2)将铈锆复合氧化物粉、大孔氢氧化铝粉、田菁粉、第二部分sb粉、氧化钛在捏合机中混合均匀后,加入步骤(1)制备的铝胶,继续捏合,混合均匀后,研磨过筛(例如研磨后过50-500目筛,优选100-250目筛);(3)向步骤(2)制得的含湿固体物料中加入适量脱模剂(例如基于固体物料质量的1.5-3%的硬脂酸镁和/或硬脂酸钙)打片成柱状颗粒,焙烧获得铈锆铝复合氧化物载体,其中,以原料固体粉总质量为基准,各原料使用比例与第一种方法相同(即其中,铈锆复合氧化物粉为8-30重量份,优选10-25重量份;大孔氢氧化铝粉占45-70重量份,优选55-65重量份;sb粉为15-25重量份,优选18-22重量份;田菁粉1.5-5重量份,优选2-4重量份;硅溶胶为1.2-11.7重量份,优选2-10重量份;氧化钛为0.35-3.5重量份,优选0.8-2重量份),此方法中液固质量比为稀硝酸及硅溶胶中液体的质量和与总固体粉料(包括硅溶胶中的二氧化硅颗粒和第一部分的sb粉)之比,第一部分sb粉与第二部分sb粉的质量比为1:0.5-5。其中,上述铈锆复合氧化物可以市购或按照以下方法制备:(1)配制五水硝酸锆、六水硝酸钇、六水硝酸铈的总金属离子浓度为1mol/l的混合盐溶液,五水硝酸锆、六水硝酸钇、六水硝酸铈的摩尔比为(2.9-3.4):1:(4.9-5.3),50-75℃水浴加热,并在不断搅拌的条件下向混合盐溶液中滴加25wt%的浓氨水,控制滴定终点的ph值为7.5-9.5,然后升温至80-90℃,老化1-5h,过滤得沉淀,(2)或向混合盐溶液中滴加碳酸氢铵饱和溶液,室温下操作并控制终点ph值为6.0-7.5,升温至70-90℃,老化1-5h,过滤得沉淀,(3)将步骤(1)或(2)得到的沉淀洗涤至中性,100-130℃烘干、450-550℃焙烧2-5h、研磨,例如过100-250目筛(优选150-200目筛,更优选过180目筛),得铈锆复合氧化物粉。其中,铈锆复合氧化物中氧化铈、氧化锆、氧化钇的质量百分含量比为60-65:25-30:1。所述铈锆铝复合氧化物的焙烧条件为,在空气气氛中,以2.8℃/min的升温至450℃,在450℃保持2小试,然后再以2.5℃/min的升温速率升至700-950℃,在终点温度下保持2-5h,自然降温。本发明另外提供了上述铈锆铝复合金属氧化物载体的制备方法,包括以下步骤:(1)将硅溶胶、任选的第一部分sb粉(可为0)加入到稀硝酸中搅拌制备得到胶状物,(2)将铈锆复合氧化物粉、大孔氢氧化铝粉、田菁粉、第二部分sb粉、氧化钛粉在捏合机中混合均匀后,加入步骤(1)制备的胶状物,继续捏合,混合均匀后,研磨过筛;(3)向步骤(2)制得的含湿固体物料中加入适量脱模剂打片成柱状颗粒,焙烧,获得铈锆铝复合氧化物载体。上述方法中,铈锆复合氧化物粉为8-30重量份,优选10-25重量份;大孔氢氧化铝粉占45-70重量份,优选55-65重量份;sb粉为15-25重量份,优选18-22重量份;田菁粉1.5-5重量份,优选2-4重量份;硅溶胶为1.2-11.7重量份,优选2-10重量份;氧化钛为0.35-3.5重量份,优选0.8-2重量份。第一部分sb粉与第二部分sb粉的质量比为1:0.5-5。本发明还提供了一种以铈锆铝复合氧化物为载体的镍基催化剂,其包括10-30wt%的活性组分nio,0-5wt%的助剂la2o3及65-85wt%的铈锆铝复合氧化物载体,优选15-25wt%的活性组分nio,1-4wt%的助剂la2o3及70-80wt%的铈锆铝复合氧化物载体。本发明进一步提供了一种制备以铈锆铝复合氧化物为载体的镍基催化剂的方法,该方法包括:在质量分数为10-20%(优选12-18%)的硝酸镍溶液中任选进一步溶解硝酸镧,并加入铈锆铝复合氧化物载体浸渍,过滤、烘干后焙烧,制得镍基催化剂。该催化剂可经一次或两次浸渍获得。优选浸渍温度为40-70℃,浸渍时间0.5-10h,优选约1-3h,烘干是在100-120℃烘干1-5h,焙烧是在400-650℃(优选450-580℃)焙烧1-6h,优选2-4h。进一步地,镧与镍原子的摩尔比为0-0.15:1,优选0.03-0.1:1,硝酸镍的用量使得最终制备的镍基催化剂具有以上组成。本发明的有益效果:本发明制备铈锆铝复合氧化物所用铝源为大孔氢氧化铝粉及sb粉,铝含量高,原子经济性好,铈锆复合氧化物可用常规方法生产也可外购商业化产品,获得方法简单方便,整个铈锆铝复合载体制备过程中操作工艺简单、排放少、环境友好,特别适用于铈锆铝复合氧化物的规模化工业化生产。先用沉淀法制备铈锆复合氧化物前驱体,经400-550℃焙烧,两者形成不完全的固溶体,之后再加入铝,经进一步700-950℃焙烧后可使部分铝与铈锆形成固溶体结构,而另一部分铝起分散支撑的作用,从而保留较高的比表面积及较适宜的介孔结构。用沉淀法制备铈锆复合氧化物时掺杂的助剂钇以提高载体的稳定性。本发明先制备铈锆铝复合氧化物为载体,然后用浸渍法制备nio含量为15-30%的催化剂,加入少量的la促进ni的分散,经适宜的温度焙烧后,制得适用于高温反应条件的镍基催化剂。以铈锆铝复合氧化物为载体制备镍基催化剂,首先载体本身具有很好的高温稳定性、强度、吸水率、表面孔结构,有助于催化剂具有很好的高温稳定性及机械稳定性,而且锆能够促进ni的分散,提高催化剂的稳定性及活性,铈能够提高催化剂的可还原性能,降低催化剂还原温度。本发明所制备的镍基催化剂特别适用于500-650℃的高温甲烷合成反应及600-900℃的甲烷水蒸气重整反应。附图说明图1为zt-1、zt-2、zt-3三种铈锆铝复合氧化物载体的xrd图。图2为zt-1、zt-2、zt-3三种铈锆铝复合氧化物载体的孔分布。图3为催化剂cat-1的xrd图。图4催化剂耐高温烧结测试装置图。具体实施方式下面通过实施例进一步说明本发明。催化剂的分析表征方法有:采用美国麦克公司asap2460装置用n2低温物理吸附法测定催化剂的孔大小及孔结构;采用大连智能试验机厂的zqj-ⅱ智能颗粒强度试验机测定单颗载体压裂强度;采用美国麦克公司chemautoⅱ2920型化学吸附仪进行催化剂程序升温还原及co吸附量的测定;采用日本理学d/max-2200pcx射线衍射仪分析催化剂物相;采用美国pe公司optima2100dv电感耦合等离子光谱发射分析仪分析催化剂金属含量;采用美国安捷伦公司6890n气相色谱分析产物组成。实施例1铈锆铝复合金属氧化物的制备:配制一定量3.0wt%的稀硝酸(v),将一定量的sb粉(第一部分sb粉,sb1)及一定量30wt%的酸性硅溶胶(si)在搅拌的条件下加入稀硝酸中制胶(使用方法一时sb1为0),将一定量的ceo2:zro2=2:1的商品铈锆复合氧化物(cz)、氢氧化铝粉(al)、田菁粉(s)、sb粉(sb2)、氧化钛粉(ti)在捏合机中混合均匀,将铝胶缓慢加入上述混合均匀的复合粉料中,继续捏合30min,在鼓风干燥机中100℃烘干2h后(在此只是给出在实施例原料用量下的一般捏合、烘干条件,需根据原料用量进行调整),研磨造粒,24目标准筛过筛,加入物料总量2%的硬脂酸镁打片成型,成片尺寸φ5*5-7mm,经一定温度(t)焙烧约5h后制得铈锆铝复合氧化物载体,此组实验成品复合金属氧化物理论量为300g。具体制备参数及物理吸附数据如下表所示:其中载体吸水率测量方法为,取20g(w1)载体,在去离子水中常温浸泡2h,将过量去离子水滤出,然后将载体表面水擦干,称重(w2),(w2-w1)/w1*100%即为载体的吸水率。强度为侧压强度。所制备的铈锆铝复合氧化物中各氧化物的组成见下表:载体编号ceo2/%zro2/%al2o3/%sio2tio2zt-1到zt-26.673.33852.52.5zt-3到zt-413.346.667532zt-5到zt-620.8310.4272.9231以上述的铈锆铝复合金属氧化物为载体的催化剂制备:分别称取载体50g,根据载体吸水率及理论nio、la2o3负载量,计算所需的六水硝酸镍及六水硝酸镧的质量,配制成40ml的浸渍液,将浸渍液水浴加热至温度t1℃,将载体倒入浸渍液中,浸渍t小时。催化剂过滤,于鼓风干燥箱中110℃、5h烘干,在马弗炉中t2℃焙烧4h,获得催化剂成品或半成品,载体经一次或两次浸渍、烘干、焙烧过程制得催化剂成品。催化剂具体原料用量及制备参数如下表所示:催化剂编号于载体编号一一对应。(如cat-1为使用zt-1制备的催化剂)从图1得出,三种组分均以氧化物的形式存在。图2可以看出三种载体均为典型的介孔材料,平均孔径为8-15nm。图3为650℃焙烧的nio含量为30%的镍基催化剂,在这么高的nio含量及焙烧温度条件下,仅有少量的镍铝尖晶石形成,且nio晶粒尺寸较小分散效果好,说明载体有助于nio较好的分散,使得催化剂具有较好的还原性及耐高温烧结性。对比例1称取铈锆复合氧化物25g,氢氧化铝150g,田菁粉3g,混捏得到粉体。称取sb粉75g放入烧杯1中,加入200ml蒸馏水持续搅拌。向烧杯2中加入浓度为3.4mol/l的稀硝酸40ml和3g柠檬酸搅拌至柠檬酸溶解,将烧杯2中的液体倒入烧杯1中搅拌至悬浊液形成胶体。将胶体移至混捏机中与混好的粉体混捏,混捏均匀后出料,然后于鼓风干燥机中120℃、2小时除湿,之后研磨,24目标准筛过筛,加入所得过筛物料总量2%的硬脂酸镁打片成型。成片尺寸φ5*5-7mm,经800℃焙烧约5h后制得铈锆铝复合氧化物载体。该载体吸水率为42%,bet表面积108m3/g。通过实施对比例发现,上述载体在捏合造粒过程中由于胶性过强而成团,物料偏硬,在除湿后更是如此,手工不易破碎,另外在打片时出现层裂不易成型的现象,且吸水率及比表面积明显低于本发明该焙烧条件下的结果。这均与原料种类、比例及制备方法直接相关。实施例2钇掺杂的铈锆复合氧化物的制备:将47.04g五水硝酸锆、9.16g六水硝酸钇、72.6g六水硝酸铈加适量水溶解于烧杯中,待金属盐完全溶解后定容至294ml,配置制成1mol/l金属离子浓度的盐溶液,将盐溶液75℃水浴加热。以浓氨水为沉淀剂,在不断搅拌的条件下将氨水滴加到盐溶液中,控制滴定终点ph值为8.2±0.05,沉淀结束后,升温至85℃老化2h,将沉淀过滤,去离子水洗涤至滤液呈中性,110℃、5h烘干,450℃焙烧4h,研磨,180目标准筛过筛,得到铈锆复合氧化物粉42.5g。该铈锆复合氧化物中ceo2占64%、zro2占30%、y2o3占6%。铈锆铝复合氧化物的制备:按实施例1中zt-1的方法制备铈锆铝复合氧化物,具体原料用量为,铈锆复合氧化物28g、氢氧化铝粉150.5g、sb粉66.1g、田菁粉8g、硅溶胶26.7g、氧化钛4g,2%的稀硝酸235ml。100℃、1.5h烘干,研磨造粒,24目标准筛过筛,打片成型,900℃、3h焙烧后制得189g铈锆铝复合氧化物载体。该氧化物吸水率为60%,强度为41.2n/mm,bet比表面积为142.28m2/g。该铈锆铝复合氧化物中ceo2占8.96%、zro2占4.2%、y2o3占0.84%、al2o3占80%、sio2占4%、tio2占2%。镍基催化剂的制备:称取载体50g,称取六水硝酸镍32.5g、六水硝酸镧2.23g,配制成40ml的浸渍液,将浸渍液水浴加热至67℃,将载体倒入浸渍液中,浸渍2小时。催化剂过滤,于鼓风干燥箱中110℃、3h烘干,在马弗炉中500℃焙烧3h,获得催化剂半成品,将该半成品再经与上述条件相同的浸渍、烘干、焙烧过程制得催化剂成品。该催化剂中nio含量为25%、la2o3占2%、铈锆铝复合氧化物占73%。该催化剂记为cat-7。实施例3铈锆复合氧化物的制备:将34.84g五水硝酸锆、50.4g六水硝酸铈加适量水溶解于烧杯中,待金属盐完全溶解后定容至210ml,配置制成1mol/l金属离子浓度的盐溶液,将盐溶液72℃水浴加热。以常温下的饱和碳酸氢铵溶液为沉淀剂,在不断搅拌的条件下将碳酸氢铵溶液滴加到盐溶液中,控制滴定终点ph值为6.5±0.05,在沉淀温度下老化2h,将沉淀过滤,去离子水洗涤至滤液呈中性,110℃、5h烘干,450℃焙烧4h,研磨,180目标准筛过筛,得到铈锆复合氧化物粉28.6g。该铈锆复合氧化物中包括60%的zro2及40%的ceo2。铈锆铝复合氧化物的制备:按实施例1中zt-5物料配比制备铈锆铝复合氧化物,具体物料用量及方法为:铈锆复合氧化物28.6g、氢氧化铝粉116g、sb粉38.6g、田菁粉6.7g、1.5%的稀硝酸177ml。110℃、1.5h烘干,研磨造粒,24目标准筛过筛,打片成型,900℃、3h焙烧后制得140g,该氧化物载体吸水率为52%,强度为48.9n/mm,bet比表面积为116.28m2/g。该铈锆铝复合氧化物载体包含12%的ceo2、8%的zro2、80%的al2o3。镍基催化剂的制备:称取铈锆铝复合氧化物载体50g,称取六水硝酸镍37.4g、六水硝酸镧2.55g,配制成40ml的浸渍液,将浸渍液水浴加热至67℃,将载体倒入浸渍液中,浸渍2小时。催化剂过滤,于鼓风干燥箱中110℃、4h烘干,在马弗炉中480℃焙烧3h,获得催化剂半成品,将该半成品再经与上述条件相同的浸渍、烘干、焙烧过程制得催化剂成品。该催化剂中nio含量为22%、la2o3含量为2%、铈锆铝复合氧化物含量为76%。该催化剂记为cat-8。对比例2沉淀法制备ce-zr-al复合载体:将2l含16.83g六水硝酸铈、294.22g九水硝酸铝、11.65g五水硝酸锆的混合水溶液加入恒温反应釜中,控制反应温度为70℃,电动搅拌下加入8wt%的碳酸钠水溶液,调节ph值至8.5,恒温老化2h,然后将浆液过滤洗涤,80℃干燥8h,450℃下煅烧6h制得载体。该载体包含13.34wt%的氧化铈、6.66wt%的氧化锆及80wt%的氧化铝。镍基催化剂的制备:将上述铈锆铝复合载体分散于0.5l含44.81g六水硝酸镍、5.1g六水硝酸镧的水溶液中,于50℃下浸渍6h,然后升温至80℃蒸干浆液。催化剂成型:蒸干后的物料在100℃下干燥6h,然后于350℃下煅烧6h。将煅烧后的物料磨细,过200目筛,添加2%的石墨和5%的去离子水,混合均匀压制成片。该催化剂包含18.15wt%的nio及3.02wt%的氧化镧及78.83wt%的铈锆铝复合氧化物载体。催化剂记为cat-9。实施例4镍基催化剂耐高温烧结性能评价:该性能评价在管式炉上进行,装置如图4所示,具体测试方法为,装填原颗粒催化剂30ml于石英管反应器恒温段,25%h2-75%n2混合气置换系统,进气空速300h-1并保持不变,开始升温,升温程序为:以2.5℃/min的升温速率升至300℃,在300℃保持2h,然后以2℃/min的升温速率升至500℃并保持5h,还原结束。然后n2吹扫降温拆卸催化剂完成催化剂的还原。同样在该装置中,装填已还原的原粒度催化剂5ml,可装填多个催化剂,不同催化剂之间用石英棉隔开,在n2保护下升温至650℃,并在该温度下保持72h,进行耐高温烧结测试。用xrd检测测试前后的ni(111)晶面的晶粒尺寸,用化学吸附仪检测催化剂的co脉冲吸附量,以此表示催化剂的活性金属集团数量。测试结果如下表所示:由以上结果可以看出,上述催化剂在该耐高温烧结测试条件下,除cat-9外,均未发生明显的ni晶粒长大的现象,催化剂具有很好的耐高温烧结性能。实施例5催化剂在煤基甲烷合成条件下的性能评价:将催化剂cat-4、cat-6、cat-7、cat-8、cat-9在四气一液高压微型固定床反应器上进行活性及高温稳定性测试,测试条件均为:将已经管式炉还原的催化剂破碎成40-60目颗粒,称取5ml装入催化剂在反应器恒温段,上下均用石英棉及石英砂隔开,催化剂首先在还原气氛h2/n2=75,还原空速2040h-1,480℃、1.0mpa的条件下还原1h,再转入合成条件压力3.0mpa,空速60000h-1,进气组成h2/co/co2/ch4/h2o=36.8/7.6/3.7/36.7/15.2,调节反应温度为650℃,在线色谱分析产物组成,从进合成气开始持续测试48h,然后停止进气,通入n2/h2=99混合气(加入少量氢气是防止催化剂因n2中携带的微量氧而被氧化),流量340ml/min,吹扫至系统检测不到co、co2时,保持通入氢氮混合气并以3℃/min的升温速率升温至800℃,并在该条件下维持48h进行高温老化处理,待处理结束后降温重新转入合成条件进行催化剂活性检测,同样持续测试48h停止实验,待装置降温至50℃以下拆出催化剂并对催化剂进行积碳含量的测定。测试结果表1所示。其中:总碳转化率计算公式:ch4选择性计算公式:从测试结果可以看出,按发明方法所制备催化剂具有很好的甲烷化反应活性、选择性,并且经高温老化处理后仍具有与处理前相当的活性、选择性及反应温升,说明催化剂具有很好的高温稳定性,测试后催化剂的积碳量很低且未出现明显的粉化现象,具有很好的抗积碳性及机械稳定性。当前第1页12