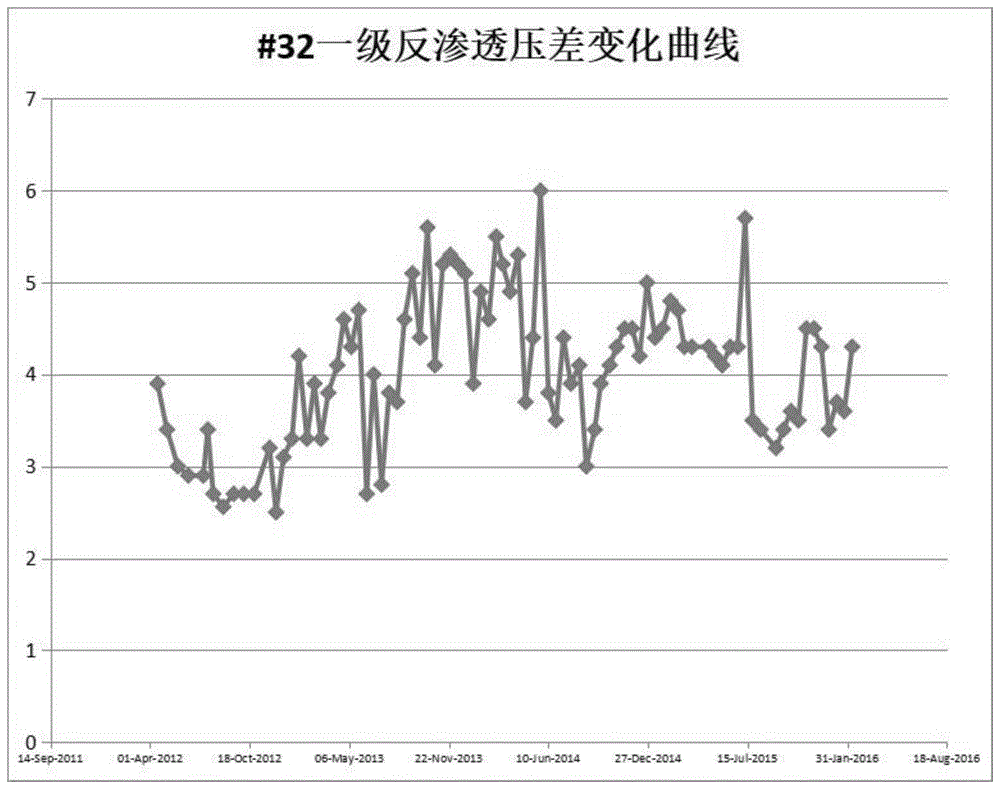
本实用新型涉及一种水处理系统,特别涉及一种防止反渗透污堵的系统。
背景技术:
:目前现有的很多电厂的采用全膜法工艺制取锅炉补给水,采用长江水为水源,水处理工艺流程为地表水→平流斜板沉淀池→净化水池→超滤→一级反渗透→二级反渗透→电除盐系统,该系统设计在平流斜板沉淀池前加二氧化氯对原水进行杀菌处理,但该系统曾发生过一段时间一级反渗透一段频繁污堵的的情况,经分析为微生物污染,后在超滤进水增加二次次氯酸钠杀菌后,膜污染情况得到一定的控制,在一段时间的使用后,系统因膜氧化问题把原水杀菌剂改为次氯酸钠。自原水杀菌剂改为次氯酸钠杀菌后,一级反渗透膜污堵情况开始逐渐显露,成为制约设备经济稳定运行的主要问题。图1是该厂#32一级反渗透压差曲线图,从图上可以看出该厂在一段时间内,压差有12次高峰值,这说明至少进行了12次清洗,实际情况比曲线图显示的更加严重,大部分清洗并不能有效地降低压差,往往需要重复多次清洗,压差才能降低下来。甚至在线清洗无效,要把膜拆下来委托专门的清洗机构对膜进行单只清洗。保安过滤器滤芯更换频繁,最短运行周期只有1周左右。13年10月份一个月内两套保安过滤器总更换10次滤芯。失效的保安过滤器的滤芯表面有明显的黏性物质。闻起来有鱼腥味。可以初步判断膜元件和保安过滤器为微生物或有机物污染。最初的分析认为杀菌剂从二氧化氯变成次氯酸钠后就发生膜污堵现象,应该是杀菌效果出了问题,用二氧化氯作为预处理杀菌剂,控制超滤出水的余二氧化氯在0.1ppm以下即可以保证杀菌效果。使用次氯酸钠杀菌,一般要维持超滤出水余氯含量为0.2ppm以上。这使得预处理沉淀池入口次钠的加药量大幅度增加。最初从节省药剂方面考虑,通过在超滤进口二次添加次氯酸钠,控制超滤出水余氯含量为0.2ppm以上。图2为超滤出水余氯定期查定的数据,从查定数据看,初期余氯的控制虽然不够稳定,总的余氯浓度平均控制在0.2ppm以上,反渗透污堵的情况并没有得到明显改善。增加非氧化性杀菌剂的冲击剂量及加药频次,反渗透污堵情况也没有得到有效控制。当超滤出水水质变差,反渗透更容易发生污堵。反渗透进水COD和浊度的变化曲线如图3,从图3可以看出在反渗透污堵比较严重的的期间,COD和浊度都没有明显的恶化趋势。这说明反渗透预处理系统(超滤出水)的水质是稳定的。污堵指数(SDI)是衡量反渗透进水污染指标的重要参数,实际监测超滤系统的出水SDI没有明显变化,变化曲线如图4。对超滤膜单只压力容器进行的进行完整性的气密性检测,超滤的完整性检测数据见表1,表1说明部分膜有断丝现象。对膜丝修补前后出水SDI的值进行对比,整套超滤系统出水的SDI变化并不大;压力容器编号总断丝数O圈情况接头情况SDI测量值#11根有变形痕迹无裂纹4.02#3一根无变形痕迹无裂纹2.89#55根有变形痕迹一个裂纹2.25#81根无变形痕迹无裂纹3.85#93根无变形痕迹无裂纹2.95表1:#33超滤的完整性检测数据超滤膜的EDX分析结果(见表2)表明膜的超滤膜污染情况并不严重,膜表面也没有明显堵塞现象。膜强度检测见表3,表3表明,膜强度有减弱现象,但仍在合格范围内,荷兰方面的专家建议膜可考虑随后一年内更换。超滤膜进行整体更换。从图5、图6看更换后,反渗透污堵情况有所改善,清洗周期有所延长。保安过滤器滤芯更换周期略延长,但效果并不明显。这说明超滤膜的断丝泄漏并不是反渗透膜污堵的主要原因;检测项目检测膜内表面检测膜外表面新膜C(%)515767O(%)332214K(%)///Al(%)2//Si(%)21/S(%)131719CL(%)11/Ca(%)///Ti(%)///Fe(%)23/Mn(%)1//表2:超滤膜的EDX分析结果项目使用过的膜新膜目前的性能(%)过滤性能(lmbh711131954拉伸强度(N)2.33.860拉断前伸缩度(%)31.46846表3:膜强度检测安排对保安过滤器滤芯和连接部件进行检查。污染的保安过滤器滤芯表面多次检查颜色不尽相同,主要为浅黄、暗黑色,表面手摸略有滑腻感觉,塑料接头和保安过滤器内壁从进水处约1/3内表面处有明显滑腻的污染物,燃烧后有明显烧焦头发的味道,初步判断主要污染物为微生物。滤芯的污染物EDX分析表明,污染物碳氧元素比列在2:1,而新的保安过滤器滤材的碳氧元素比列是30:1,这进一步说明污染主要为微生物污染。该厂四期有一套400m3/h制水系统,水源也同样取自为长江水,水处理工艺流程为地表水→平流斜板沉淀池→V型滤池→超滤→一级反渗透→二级反渗透→电除盐系统,系统也在平流沉淀池前设计加次氯酸钠对原水进行杀菌处理。三、四期制水的超滤进水余氯的控制也按同一值进行控制,四期制水系统的反渗透可以保证3个月左右清洗一次,保安过滤器的滤芯的更换周期在90天左右。从预处理方面对比分析,两者唯一的差别在于四期设计了滤池,而三期并没有设计过滤器系统。这很容易得出滤池在保证反渗透污堵有着重要作用的结果。COD可以在一定程度上反映反渗透进水中有机物含量。图7是三、四期超滤进水COD的对比分析,三、四期制水系统的超滤出水COD基本相同,工艺上增加过滤系统并没有表现出更好的去除有机物的优势。也就是说三期制水系统反渗透的污堵并不是没有设计过滤器系统造成。三期制水与四期制水另一个不同点在于三期制水的沉淀池出水不仅用来为除盐水制水系统提供水源,还为全厂提供工业冷却水,由于在净化水池内停留时间过长,余氯消耗量大,净化水池进口必须加入更大剂量的次氯酸钠,最初从经济性考虑,三期制水在沉淀池进水加入一定量的次氯酸钠,保证沉淀池出水余氯。当次氯酸钠因长时间停留在净化水池内消耗完毕之后,在超滤进水二次添加次氯酸钠,保证反渗透预处理管线的次氯酸钠含量。四期制水只在沉淀池入口加药,维持预处理管线一直保证余氯的含量在0.2ppm以上。经计算,四期反渗透预处理次氯酸钠持续作用时间约为5小时,而三期制水反渗透预处理次氯酸钠持续作用时间分为两部分,预处理部分为2小时,超滤部分约为2小时,总计4小时。三期次氯酸钠持续作用时间与四期相比,相差并不大,为何杀菌效果却相差很大呢,一般认为反渗透的整个预处理管线都应维持足够的杀菌剂浓度,以防微生物产生抗药性。次氯酸钠的杀菌效果和药剂浓度和药剂的持续作用时间有关,三期加药系统二次加药前,次氯酸钠的浓度已经降低为0ppm,再次加药,持续时间无法保证。杀菌效果必然下降。后来三期制水系统改变次氯酸钠加药方式,仅在沉淀池入口加药,保证整个反渗透预处理管线的次氯酸钠都在0.3ppm以上。加药方式改变后,保安过滤器更换滤芯周期延长到3-6个月,有时压差还不增高。反渗透清洗周期延长到3-6个月。从图1可以明显看出,自2015年9月后,反渗透压差变化基本保持稳定,只进行过2次清洗。综上所述,不难看出一级反渗透压差升高原因主要是受到微生物污染。而微生物污染的主要原因是次氯酸钠加药方式的不对。技术实现要素:本实用新型的目的是提供一种可保证反渗透预处理杀菌效果使反渗透系统预处理管线始终维持一定的余氯浓度从而防止反渗透污堵的系统。本实用新型的上述技术目的是通过以下技术方案得以实现的:一种防止反渗透污堵的系统,包括斜板沉淀池、V型滤池、过滤水池、超滤系统、超滤水箱、反渗透增压泵和反渗透系统,所述斜板沉淀池、V型滤池、过滤水池、超滤系统、超滤水箱、反渗透增压泵和反渗透系统依次连通,在斜板沉淀池的进水口处设有加药口一,在斜板沉淀池与V型滤池之间设有余氯检测仪一,所述超滤系统与超滤水箱之间存在余氯检测仪二,所述反渗透给泵与反渗透泵之间设有加药口二。作为优选,还包括反渗透给泵,所述反渗透给泵串接在超滤水箱和反渗透增压泵之间。作为优选,所述加药口一包括次氯酸钠加药口和混凝剂加药口。作为优选,所述加药口二包括还原剂加药口。作为优选,所述加药口二还包括非氧杀菌剂加药口。通过采用上述技术方案,本实用新型的防止反渗透污堵的系统具有如下优点:本实用新型的防止反渗透污堵的系统一方面可以实现长江水或者河水直接取用并分别通过沉淀、过滤、超滤和反渗透后进行直接进行工业用水用;另一方面克服了传统的长江水或河水直接进行过滤时一定时间后会对反渗透膜组件造成淤堵的问题;再者,对于整个过滤系统的管道进行长时间的余氯控制防止了整个管道内的微生物繁殖并且不易产生抗药性的问题,其次,当管道内的余氯量降低至指定值或者降为0时,通过加入非氧杀菌剂对微生物和细菌进行杀灭和抑菌操作,进而实现整个管道内细菌的含量以及防止反渗透膜组件的淤堵。附图说明图1是现有技术的#32一级反渗透压差变化曲线图;图2是现有技术的超滤出水余氯变化曲线图;图3是现有技术的反渗透进水COD和浊度的变化曲线图;图4是现有技术的#33超滤断丝修补前后出水SDI变化曲线图;图5是现有技术的超滤膜更换前后标准化产水量的变化图;图6是现有技术的超滤膜更换前后反渗透脱盐率和压差的变化图;图7是现有技术的三、四期超滤进水COD的对比分析;图8是本实用新型的防止反渗透污堵的系统示意图。图中,1、斜板沉淀池,2、V型滤池,3、过滤水池,4、超滤系统,5、超滤水箱,6、反渗透给泵,7、反渗透增压泵,8、反渗透系统,9、加药口一,91、次氯酸钠加药口,92、混凝剂加药口,10、余氯检测仪一,11、余氯检测仪二,12、加药口二,121、还原剂加药口,122、非氧杀菌剂加药口。具体实施方式以下结合附图对本实用新型作进一步详细说明。一种防止反渗透污堵的系统,包括斜板沉淀池1、V型滤池2、过滤水池3、超滤系统4、超滤水箱5、反渗透增压泵7和反渗透系统8,所述斜板沉淀池1、V型滤池2、过滤水池3、超滤系统4、超滤水箱5、反渗透增压泵7和反渗透系统8依次连通,在斜板沉淀池1的进水口处设有加药口一9,在斜板沉淀池1与V型滤池2之间设有余氯检测仪一10,所述超滤系统4与超滤水箱5之间存在余氯检测仪二11,所述反渗透给泵6与反渗透泵7之间设有加药口二12;还包括反渗透给泵6,所述反渗透给泵6串接在超滤水箱5和反渗透增压泵7之间;所述加药口一9包括次氯酸钠加药口91和混凝剂加药口92;所述加药口二12包括还原剂加药口11和非氧杀菌剂加药口12。在具体实施时,直接将长江水通入斜板沉淀池1中并在次氯酸加药口91中加入次氯酸钠溶液,在混凝剂加药口92中进行加入混凝剂;在斜板沉淀池1中进行进水预沉降,对预沉降后的上清液通入V型滤池2中,同时余氯检测仪一10对上清液中的余氯浓度进行检测并将该余氯浓度进行反馈,若上清液中的余氯浓度低于1.0ppm,则对次氯酸加药口91中继续加次氯酸钠溶液,直至余氯检测仪一10对上清液中的余氯浓度保持在1.0ppm;V型滤池2对上清液进行继续过滤并通入过滤水池中,对过滤水池中的过滤水再次通入超滤系统,并对超滤系统中的水继续通入超滤水箱,余氯检测仪二11对超滤系统中的出水余氯进行检测,当余氯检测仪二11检测出的余氯浓度低于0.3-0.5ppm,若降低V型滤池2中的过滤时间或缩短过滤水池的过滤时间,从而保证余氯检测仪二11检测出的余氯浓度范围在0.3-0.5ppm;对保持余氯浓度的过滤水继续经过超滤水箱5、反渗透给泵6和反渗透增压泵7,对加药口二12中的还原剂加药口11进行还原剂加药;步骤五:所述反渗透增压泵7将经过加药后的过滤水通入反渗透增压泵7再流入反渗透系统,经过反渗透系统流出过滤水和浓水。所述若余氯检测仪二11检测出的余氯浓度为0,则对加药口二12中的非氧杀菌剂加药口12进行添加非氧杀菌剂。所述非氧杀菌剂具体为DPNPA。添加非氧杀菌剂的加药方式为浓度控制在100ppm以内且加药时间为1-2小时。本具体实施例仅仅是对本实用新型的解释,其并不是对本实用新型的限制,本领域技术人员在阅读完本说明书后可以根据需要对本实施例做出没有创造性贡献的修改,但只要在本实用新型的权利要求范围内都受到专利法的保护。当前第1页1 2 3