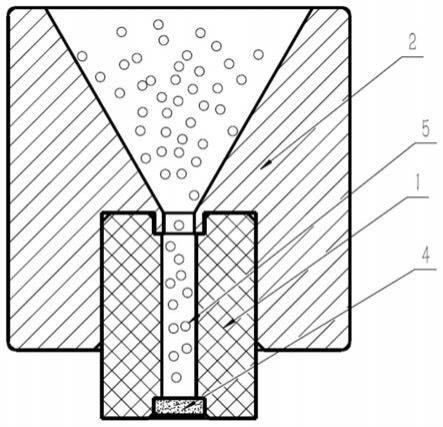
1.本发明专利涉及分析仪器技术领域,更具体地说涉及一种固相萃取柱的填料装填装置及应用,用于固相萃取柱填料的装填,确保固相萃取柱的耐压符合要求,提高固相萃取柱装填的合格率,为自动化装填固相萃取柱提供一种方案。
背景技术:2.固相萃取(spe)主要用于样品的分离、纯化和浓缩,与传统的液液萃取法相比较可以提高分析物的回收率,更有效的将分析物与干扰组分分离,减少样品预处理过程。随着技术的发展,为提高样品分析效率,需要能够实现spe过程的全自动化、高通量处理和与液相色谱的在线联用。近年来发展出耐高压(≥15mpa)淋洗和洗脱的小型spe柱,给液相色谱直接进样,免去了氮吹浓缩和定容过程。这项技术需要在固相萃取仪器上放置多个耐高压固相萃取柱,每个固相萃取柱可以重复高压密封,且具有良好的富集、分离效果。这就要求装填的填料要尽量填实,避免较大的空隙,以保证较高的富集、分离效率。现有技术一般采用移液枪,将分散有填料的溶剂分多次加入到填料装填腔中。这种方法虽然能将填料填实,但很容易在安装筛板时挤压填料导致筛板堵塞,进而导致固相萃取柱压力超标,无法使用。同时,现有技术的装填方式不利于自动化。
技术实现要素:3.针对上述技术难题,本发明提供一种固相萃取微型柱的填料装填装置,该装置可以避免筛板安装过程对填料的过分挤压,确保填料填实,从而提高固相萃取微型柱装填的合格率,提升装填效率,节约成本。同时,也为自动化装填固相萃取柱提供了一种方案。
4.本发明的技术方案是:
5.一种固相萃取柱的填料装填装置,包括包括填料漏斗和填料塞;
6.所述固相萃取柱为一圆柱体,其上下二个端面均分别设有相对应的用于放置筛板的圆形凹槽a,二圆形凹槽之间设有一圆形通孔a,圆形凹槽a直径大于圆形通孔a直径;
7.所述填料漏斗顶部设有一漏斗状凹槽,底部设有一圆形凹槽b,圆形凹槽b直径大于固相萃取柱外径;于圆形凹槽底部设有一圆柱形突起,圆柱形突起直径小于圆形凹槽a直径、大于圆形通孔a直径,于圆柱形突起端面上开设有与漏斗状凹槽相连通的通孔;
8.所述填料塞底部设有一圆形凹槽c,圆形凹槽c直径大于固相萃取柱外径;于圆形凹槽底部设有一圆柱形突起,圆柱形突起直径小于圆形凹槽a直径、大于圆形通孔a直径。
9.所述填料漏斗和填料塞为圆柱形块体,填料漏斗上端为一倒圆锥台形孔,下端为内部带同轴圆柱的圆柱形槽孔,槽孔直径d满足d0<d≤d0+0.2mm,d0为固相萃取柱外圆直径;槽孔的深度h满足l
×
1/3<h<l,l为固相萃取柱的高度;倒圆锥台形孔和槽孔内圆柱端面相互间有一个圆柱形贯穿孔,贯穿孔直径d’满足0.5mm<d’≤d2,d2为圆形通孔a的内径;圆柱的直径d满足d’<d≤d
1-0.2mm,高度h1满足h1≥l1,d1为圆形凹槽a的直径,l1为圆形凹槽a的深度;
10.所述填料塞底部设有一圆形凹槽c,圆形凹槽c直径d3满足d0<d3≤d0+0.2mm,圆形凹槽c的深度l2为l
×
1/3<l2<l,于圆形凹槽c底部设有一圆柱形突起,突起直径d4满足d’<d4≤d
1-0.2mm,突起的高度h2≥l1。
11.所述填料漏斗的倒圆锥台形孔锥角为30~120
°
。
12.所述填料漏斗和填料塞为金属材质,优选黄铜、不锈钢或钛合金。
13.一种固相萃取柱的填料装填装置的应用,将下端安装筛板的待装填的固相萃取柱开口朝上安装到填料漏斗的圆柱形槽孔内,且保证圆柱安装到固相萃取柱放置筛板的圆形凹槽a内;将准备好的填料通过填料漏斗的倒圆锥台形孔和圆柱形贯穿孔装填到固相萃取柱内;然后轻微振动,使填料紧密地填充到固相萃取柱内;填满填料后取下填料漏斗,将填料塞的圆形凹槽c套在萃取微型柱上,且保证突起位于萃取微型柱放置筛板的圆形凹槽a内,再次轻微振动,使填料紧密地填充到固相萃取柱内;之后取下填料塞,将固相萃取柱的上端安装上筛板。
14.所述轻微振动方式为敲击填料塞或将萃取微型柱敲击桌面或用超声波振动。
15.本发明固相萃取柱填料的装填装置及方法具有如下优点:
16.1、该装置能避免填料在装填过程中遗留在固相萃取柱放置筛板的平台上,通过填料漏斗和填料塞的配合使用,能确保填料在安装筛板时不被过分挤压,从而避免了筛板堵塞导致的装填失败。
17.2、所述装填装置的应用方法不仅可以避免筛板堵塞,还能保证填料填实,从而装填出富集、分离效率高的固相萃取柱。
18.3、装置结构及装填方法简单,结构设计合理、成本低廉,该装置和方法也为自动化装填固相萃取柱提供了一种方案。
19.4、该装置和方法提高了固相萃取柱的装填合格率,节省填料成本,同时可以获得优良的批间重复性。
附图说明
20.图1——填料漏斗用于装填过程示意图,图中:1-固相萃取柱,2-填料漏斗,4-筛板,5-填料。
21.图2——填料塞用于装填过程示意图,图中:1-固相萃取柱,3-填料塞,4-筛板,5-填料。
22.图3——填料漏斗示意图。图中:21-倒圆锥台形孔,22-槽孔,23-圆柱,24-圆柱形贯穿孔。
23.图4——填料塞示意图。图中:31-圆形凹槽c,32-圆柱形突起。
具体实施方式
24.下面接合实施例来说明本发明。
25.实施例1
26.一种固相萃取微型柱的填料装填装置,如附图1至图4所示,由填料漏斗2和一个填料塞3组成;
27.固相萃取柱为一圆柱体,其上下二个端面均分别设有相对应的用于放置筛板的圆
形凹槽a,二圆形凹槽之间设有一圆形通孔a,圆形凹槽a直径大于圆形通孔a直径;
28.所述填料漏斗2顶部设有一漏斗状凹槽,底部设有一圆形凹槽b,圆形凹槽b直径大于固相萃取柱外径;于圆形凹槽底部设有一圆柱形突起,圆柱形突起直径小于圆形凹槽a直径、大于圆形通孔a直径,于圆柱形突起端面上开设有与漏斗状凹槽相连通的通孔;
29.所述填料塞3底部设有一圆形凹槽c,圆形凹槽c直径大于固相萃取柱外径;于圆形凹槽底部设有一圆柱形突起,圆柱形突起直径小于圆形凹槽a直径、大于圆形通孔a直径。
30.所述填料漏斗2和填料塞3为圆柱形块体,填料漏斗2上端为倒圆锥台形孔21,锥角为90
°
;下端为内部带同轴圆柱23的圆柱形槽孔22,槽孔22直径为9.05mm,高度为8mm;倒圆锥台形孔21和槽孔22内圆柱端面相互间有一个圆柱形贯穿孔24,贯穿孔24直径为1.9mm;圆柱23的直径为2.7mm,高度为1.3mm。填料塞3底部设有一圆形凹槽c 31,其直径为9.05mm,深度为8mm,于圆形凹槽c 31底端有一圆柱形突起32,其直径为2.7mm,高度为1.3mm;所述固相萃取柱1的外圆直径为9mm、高度为12mm,圆形凹槽a的直径为3mm、深度为1.2mm,圆形通孔a的直径径为2mm。
31.填料漏斗2和填料塞3材质为黄铜。
32.实施例2
33.一种固相萃取微型柱的填料装填装置的应用
34.一种固相萃取微型柱的填料装填方法,如实施例1所述的装置,将下端安装筛板的待填装的固相萃取柱1开口朝上安装到填料漏斗2的圆柱形槽孔22内,且保证圆柱23安装到固相萃取柱1放置筛板的圆形凹槽a内;将适量的c18填料通过填料漏斗22的倒圆锥台形孔21和圆柱形贯穿孔24装填到固相萃取柱1内,然后将固相萃取柱轻微敲击桌面,使填料紧密地填充到固相萃取柱内;填满填料后取下填料漏斗2,将填料塞3的圆形凹槽c 31套在固相萃取柱1上,且保证突起32位于固相萃取柱1放置筛板的圆形凹槽a内,通过轻微敲击填料塞3,使得填料紧密地填充到固相萃取柱内,之后取下填料塞3,将固相萃取柱1的上端安装上筛板。
35.实施例3
36.如实施例1所述的装填装置,区别在于:填料漏斗2的圆柱形槽孔22的直径9.10mm,圆柱23的直径为2.4mm,高度为1.2mm;填料塞3的圆形凹槽c 31的直径为9.10mm,突起32的直径为2.4mm;所述填料漏斗2和填料塞3为不锈钢材质。
37.实施例4
38.如实施例1所述的装填装置,区别在于:所述填料漏斗2和填料塞3为钛合金材质;所述填料漏斗2的倒圆锥台形孔21锥角为120
°
。