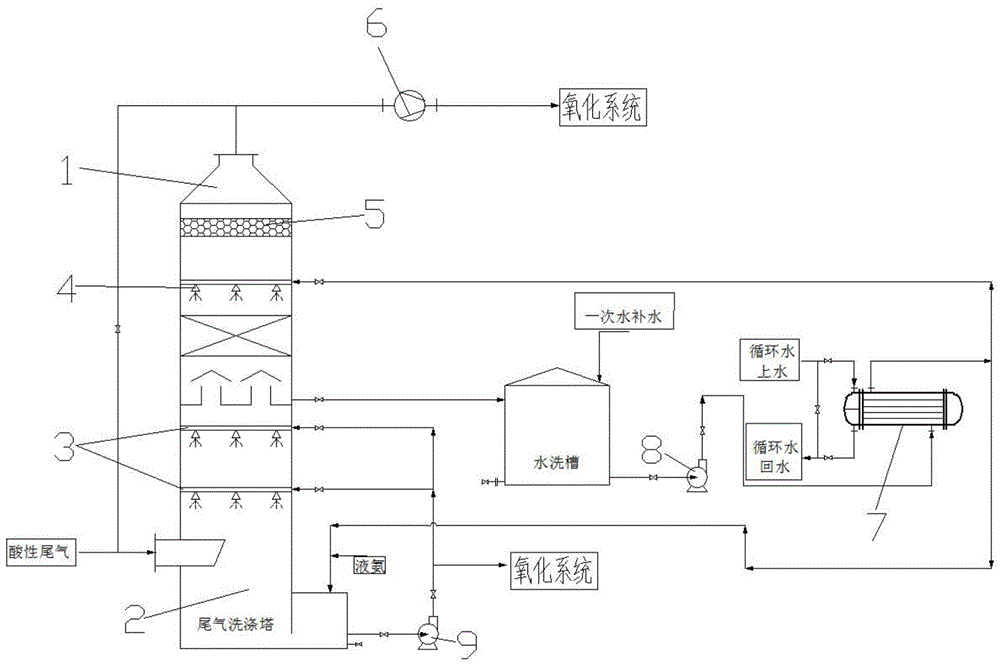
本实用新型属于废弃的回收装置
技术领域:
,具体涉及一种含有so2以及h2so4的混合气体的回收装置。
背景技术:
:现有技术中,通过湿法硫回收工艺回收硫时,反应过程中未被完全氧化的so2和空气中的氮气及过量氧气等组份混合而成成的酸性尾气自硫回收装置冷凝器顶部排出,经高度为40米的尾气烟囱直排大气,设计so2排放浓度<550mg/m3。而这一排放量无法满足现有环保排放标准,且排放到空气中的so2以及h2so4还会对人体健康造成困扰。如果直接利用锅炉烟气脱硫系统对混合气体进行处理,则其氧化生成硫酸铵,部分气体排放后发现吸收该股尾气的脱硫浆液颜色呈鹅黄色,而未吸收该股尾气的脱硫浆液颜色呈正常灰白色,同时排放时,烟囱高空排放呈喷涌式,视觉效果不好。怀疑尾气中夹带的硫酸酸雾组份影响了脱硫系统的运行,造成脱硫吸收运行效果差,导致烟气外观呈浓雾云喷状,必须对该等废气进行预处理后方可进入烟气脱硫系统。技术实现要素:为了解决现有技术中不经预处理的含硫混合气体排放造成的空气污染,本实用新型提供一种装置简单、处理效果好、排放量减少的含有so2以及h2so4的混合气体的回收装置。为了达到上述技术效果,本实用新型通过以下技术方案实现:一种含有so2以及h2so4的混合气体的回收装置,包括:洗涤塔,所述洗涤塔用于对混合气体的洗涤,使得so2以及h2so4转化成同一类的含硫化合物;所述洗涤塔从下至上依次设置有:循环浆液储槽、氨洗层、水洗层以及除雾器,所述循环浆液储槽设置于洗涤塔塔底,放经氨洗层氨洗后的溶液;所述氨洗层用于转换形成的同类含硫化合物溶液,所述水洗层用于吸收同类含硫化合物溶液中的氨,所述除雾器用于除去烟气中夹带的水气;氧化系统,所述氧化系统用于对同类含硫化合物溶液进行氧化,使其形成硫酸铵产品,所述氧化系统与所述洗涤塔顶部连接。进一步地,还包括增压风机,所述增压风机所述增压风机设置于洗涤塔与氧化系统之间。所述增压风机用于将通过洗涤塔处理后的混合尾气送至锅炉烟气脱硫系统。由于硫化合物压力较大,需要抗压实现,故选用增压风机进行输送。进一步地,所述增压风机工作时,进口风压为0kpa,出口风压为7kpa-9kpa,风量为15000nm3/h-20000nm3/h。通过这一压差,能够实现处理后混合液的输送,且这一风量,能够实现硫回收装置酸性尾气的全部回收。本申请中,选用结构简单、维修方便的离心式增压风机,配备防爆变频风机,可根据硫回收系统负荷调整风机风量。进一步地,所述洗涤塔顶部以及洗涤塔底部分别通过pph管道连接至氧化系统中。由于混合气体温度高,呈酸性,腐蚀性强,通过试验研究以及对比,pph即均聚聚丙烯材料,在120℃以内,耐酸碱腐蚀效果显著,符合使用工况要求;且该材质导热系数小,具有较好的保温性能,可有效减少尾气冷凝液的产生,并在很大的温度范围内承受ph=1~14的高浓度酸和碱的腐蚀,且产品质轻,焊接工艺简单,施工方便,工程综合造价低,能满足复杂的工艺管道需要。进一步地,还包括水洗冷却装置,所述水洗冷却装置用于对水洗层以及氨洗层进行低温补水。水洗冷却装置的目的是对水洗层以及氨洗层提供低温的水,实现低温预处理。进一步地,还包括用于补氨的液氨管道,所述水洗冷却装置通过所述液氨管道对氨洗层进行低温补水以及补氨。由于反应中氨气消耗多,故需要增加液氨管道,实现补氨。进一步地,所述水洗冷却装置为卧式列管换热器,其换热面积为300m2。卧式列管换热器安装及检修方便,换热面积大而占地面积小,尤其是对于管路较多的化工厂,卧式列管换热器能够更好地发挥换热效果。进一步地,所述液氨层设有两层喷头,两层所述喷头之间的距离为2.5m-3m,所述喷头用于将氨水喷向混合气体。两喷淋层间距优选2.7m,能使尾气与氨水充分接触,并延长尾气在塔内的停留时间。进一步地,所述喷头为pph喷头。因为氨水具有弱碱性,而尾气具有强酸性,pph喷头可在一定温度下,具有显著的同时耐酸、耐碱腐蚀性。进一步地,所述循环浆液储槽一体设置于洗涤塔底部。通过一体化的结构设置,不仅方便生产加工,而且占地面积小,管道流程短,便于实现浆液的循环使用。本实用新型的有益效果:本实用新型中,通过增加水洗以及氨洗等预处理,极大地吸收了混合气体中的so2以及h2so4,减少了其排放量,且将其用于生产硫酸铵,变废为宝,有利于环保。本实用新型中,通过一个洗涤塔,实现了整个预处理,且整个洗涤塔,结构简单,参数容易调节,使用方便。本实用新型中,通过氨洗+水洗的预处理装置,实现湿法硫回收装置和锅炉烟气脱硫装置的相结合,用于分步处理湿法硫回收装置酸性放空尾气。附图说明图1是本实用新型提供的一种含有so2以及h2so4的混合气体的回收装置的结构示意图;图2是本实用新型提高的实施例2的结构示意图;图中:1、洗涤塔;2、循环浆液储槽;3、氨洗层;4、水洗层;5、除雾器;6、增压风机;7、水洗冷却装置;8、水洗泵;9、氨洗泵。具体实施方式为进一步阐述本实用新型达成预定目的所采取的技术手段及功效,以下结合附图及实施例对本实用新型的具体实施方式、结构特征及其功效,详细说明如下。以下将结合附图及实施例对本实用新型做进一步详细说明。实施例1参照附图1所示,本实用新型提供一种含有so2以及h2so4的混合气体的回收装置,具体用于回收湿法回收硫装置中含有so2以及h2so4的混合气体,减少空气中s物质的排放量。具体地,参照附图1所示,本实施例具体包括预处理用的洗涤塔1以及氧化用的氧化系统。所述氧化系统可以为锅炉脱硫装置。连接时,洗涤塔1底部与硫回收装置玻璃冷凝器出口连接,实现混合气体的通入;而洗涤塔1顶部则与氧化系统连接,经氧化系统氧化后,一部分含有so2以及h2so4的混合气体形成硫酸铵产品,一部分经管道排入大气。参照附图1所示,本实施例中,洗涤塔1从下至上依次设置有:洗涤塔1、氨洗层3、水洗层4以及除雾器5,所述洗涤塔1设置于洗涤塔1塔底,放经氨洗层3氨洗后的溶液;所述氨洗层3用于转换形成的同类含硫化合物溶液,水洗层4用于吸收同类含硫化合物溶液中的氨,所述除雾器5用于除去烟气中夹带的水气,防止洗涤液被带出塔外。实际使用中,氨洗层3氨水浓度为5%,消耗新鲜液氨150kg/d。氧化系统,所述氧化系统用于对同类含硫化合物溶液进行氧化,使其形成硫酸铵产品,所述氧化系统与所述洗涤塔1顶部连接。使用本实用新型时,混合气体直接或者通过储存罐以及管道进入洗涤塔1,依次进行氨洗和水洗,然后进入氧化系统,进行氧化形成硫酸铵产品以及混合气体的排放。本实用新型利用so2以及h2so4与过量的稀氨水充分接触,发生化学反应生成亚硫酸铵(nh4hso3)和硫酸铵((nh4)2so4)的原理,发生如下化学反应:so2+nh3·h2o=nh4hso32nh3·h2o+h2so4=(nh4)2so4+2h2o同时利用常温下氨极易溶于水的原理,在水洗层4内尾气中夹带的氨被水充分吸收,避免游离态的氨被带出塔外,从而减少装置补氨量,降低了装置运行成本。实施例2作为上述实施例的进一步改进,本实施例中,还包括增压风机6,所述增压风机6用于将洗涤后的硫回收尾气送至氧化系统中。由于硫化合物压力较低,需要抗压实现,故选用增压风机6进行输送。为了能够成功的将洗涤后的硫回收尾气送至氧化系统(或锅炉系统脱硫装置),需新增一台风量18000nm3/h、风压8kpa的离心式增压风机6,该风机叶轮和蜗壳的材质既要能满足在正常工况下尾气ph=6~8时长周期使用,也要能满足极端工况下尾气ph=1~3时间断使用的要求。为了进行材料的选取,故在实验室中,分别选取双相不锈钢2205、双向不锈钢2507、超级奥氏不锈钢904l和钛材ta2,尺寸约为100mm×50mm,厚度为8mm的4块钢板,放置在ph=1的硫酸中,水浴加热30~40℃,并每5天观测和记录钢板腐蚀情况(实验观测记录见表1)。表1实验观测记录表经30天后试验观测,904l和ta2钢板经目测检查无明显腐蚀现象,其他材质钢板均出现严重腐蚀。本实施例中还包括,钢板腐蚀情况的检测对比将在硫酸中浸泡30天的904l和ta2材实验样品取出,对这两种研试验样品进行称重;再按照《金属和合金的腐蚀试样上腐蚀产物的清除》(gb/t16545-2015)中的方法,在流水中用软毛刷进行轻微清洗,以便去除附着不牢固或疏松的腐蚀产物;经反复清洗后,再对以上2个样品进行称重,并与清洗前样品重量进行对比,清洗前后样品重量无明显差异。清洗前称重对比见表2。表2904l钢板较ta2钢板清洗前后称重对比钢板材质清洗前重量(g)清洗后重量(g)前后重量差(g)904l310.359309.0861.273ta2175.691174.9560.735然后在按照《金属和合金的点蚀评定方法》(gb/t18590-2001),在流水中用硬毛刷对904l和ta2材实验样品进行机械清洗,再将清洗过的样品放置于20倍显微镜下进行细致观察。两块样品表面仅存个别宽浅型蚀坑,无摘窄深型和皮下型等其它类型蚀坑存在。经试验分析对比,904l钢板和ta2钢板在该等工况下,耐腐蚀情况较好。因904l钢板较ta2钢板价格较低,因此本装置增压风机6的叶轮和蜗壳选用904l钢板作为母材。进一步地,所述增压风机6工作时,进口风压为0kpa,出口风压为7kpa-9kpa,风量为15000nm3/h-20000nm3/h。通过这一压差,能够实现处理后尾气的输送,且这一风量,能够实现硫回收装置酸性尾气的全部回收。本实施例中,选用结构简单、维修方便的离心式增压风机6,配备防爆变频风机,可根据硫回收系统负荷调整风机风量。参照附图2所示,本实施例中,氧化系统选用锅炉烟气脱硫系统。实施例3参照附图1所示,本实施例中,洗涤塔1上部通过水洗槽、水洗泵8、循环水、水洗冷却装置7(即水洗冷却器)以及管道形成循环水洗装置;而下部增通过氨洗泵9连接循环浆液储槽2以及氨洗层3;工作时,选取洗涤塔1空速为选取1.6-1.8m/s,塔内停留时间选取5-6s,经计算得尾气洗涤塔1φ2000×15000mm,采用塔体及塔内喷头、填料、支撑件等均采用pph材质,塔下部为2层喷淋洗涤,洗涤液采用适量稀氨水,洗涤后的硫铵浆液送至锅炉烟气脱硫装置;上部为填料层+1层喷淋洗涤,洗涤液采用一次水,洗涤后的浆液送至下层洗涤水箱,作为下层洗涤液再次利用;塔顶为1层填料除雾器5。实际工作中,因硫回收尾气中含有so2/h2so4,温度约100℃,在长距离输送过程中,尾气会因外界环境温度的降低而产生冷凝液,经多次采样分析,未经洗涤塔1洗涤的尾气其冷凝液为强酸性(ph为1~3之间),腐蚀性极强,而经氨水洗涤后的尾气其冷凝液为中性或弱碱性(ph为6~8之间)。因此,尾气洗涤塔1和尾气风管的材质选择极为关键,需在该工况下同时适应强酸性和弱碱性环境。通过对现有材质的物性分析并结合运行经验,现有钢材均存在一定的腐蚀,材质选择受限。研究考虑选用改性塑料材质作为尾气风管和洗涤塔1母材,经对现有新型材料硬质聚氯乙烯(upvc)管、氯化聚氯乙烯(cpvc)管、聚乙烯(pe)管、交联聚乙烯(pe-x)管、三型聚丙烯(pp-r)管、聚丁烯(pb)管、工程塑料(abs)管、玻璃钢夹砂(rpm)管、铝塑料复合(pap)管、钢塑复合(sp)管等等的特性分析,其耐酸碱腐蚀性和耐温情况也有所不同。经过查阅资料,在本项目研究中期大胆采用了新型材料均聚聚丙烯(pph)。聚丙烯pp的均聚物简称pph,是单一丙烯单体的聚合物。pph是一种高分子量,低熔流率的均聚聚丙烯,它经过β改性具有细腻的结晶结构,使其具有优良的耐化学性、耐高温性以及良好的抗蠕变性,而且在低温下还具有优异的抗冲击性。进行实验室小样试验,发现pph材料其在120℃以内,耐酸碱腐蚀效果显著,符合使用工况要求。因此本装置尾气洗涤塔1(包括塔内喷头、填料、支撑件等内件)和尾气风管均采用了新型材料均聚聚丙烯(pph)。该材质导热系数小,具有较好的保温性能,可有效减少尾气冷凝液的产生,并在很大的温度范围内承受ph=1~14的高浓度酸和碱的腐蚀,且产品质轻,焊接工艺简单,施工方便,工程综合造价低,能满足复杂的工艺管道需要。本实施例中,水洗槽规格为φ2000×2500mm,材质采用cs+玻璃鳞片,槽体上设有就地和远传液位计。氨洗泵9和水洗泵8泵体和叶轮均采用cs+f46材质,出口压力0.3mpa,氨洗泵9循环量为60m3/h,水洗泵8循环量为40m3/h。水洗冷却器为卧式列管换热器,材质为316l,换热面积300m2,用来降低水洗层4浆液温度,降低氨逃逸。参照附图1,本实施例中,所述洗涤塔1顶部以及洗涤塔1底部分别通过pph管道连接至氧化系统以及混合气体储存罐。由于混合气体温度高,呈酸性,腐蚀性强,通过试验研究以及对比,pph即均聚聚丙烯材料,在120℃以内,耐酸碱腐蚀效果显著,符合使用工况要求;且该材质导热系数小,具有较好的保温性能,可有效减少尾气冷凝液的产生,并在很大的温度范围内承受ph=1~14的高浓度酸和碱的腐蚀,且产品质轻,焊接工艺简单,施工方便,工程综合造价低,能满足复杂的工艺管道需要。进一步地,还包括用于补氨的液氨管道,所述水洗冷却装置7通过所述液氨管道对氨洗层3进行低温补水以及补氨。由于反应中氨气消耗多,故需要增加液氨管道,实现补氨。进一步地,所述氨洗层3设有两层喷头,两层所述喷头之间的距离为2.5m-3m,所述喷头用于将氨水喷向混合气体。两喷淋层间距优选2.7m,能使尾气与氨水充分接触,并延长尾气在塔内的停留时间。所述喷头用于将氨水喷向混合气体。进一步地,所述循环浆液储槽2一体设置于洗涤塔1底部。通过一体化的结构设置,不仅方便生产加工,而且便于实现浆液的循环使用。本实施例中的操作歩序:(1)尾气洗涤系统开车前准备a)确认尾气洗涤系统所有设备管线及仪表附件安装完成。b)系统吹扫、气密都已合格。c)系统所有公用介质都已具备条件:仪表空气压力:0.7mpa循环水:0.4mpa一次水:0.4mpa液氨:1.6mpad)所有仪表都已调试完毕,且正常投运。(2)尾气洗涤系统水循环建立a)投运水洗冷却器循环水(开循环回水排气阀排气)。b)打开水洗槽一次水补水阀,给水洗槽建立液位至50%-60%(900-1000mm)。c)开启p1902(即水洗泵),开前需排气,为上塔水洗段建立液位,同时打开lv19002给下塔建立液位50%(≤500mm)。d)开启p1903(即氨洗泵),开前需排气,为下塔建立水循环,同时使用hv19003、lv19002稳定水洗槽和上下塔液位。e)当水洗槽和上下塔液位稳定后此时水循环建立完毕。(3)尾气洗涤系统配氨,并开启洗涤塔1入口尾气蝶阀并入酸性尾气。a)打开hv19004前后切断及自调阀给洗涤塔1配氨,要求初次氨水浓度达到5%。b)缓慢打开洗涤塔1底阀,待此阀全开后逐渐打开洗涤塔1出口阀,洗涤塔1底出口阀打开后逐渐关闭联通阀,关阀过程要缓慢,中控注意pi-19066压力,压力如果较高,可适当增加3号风机转速(电流不能超过82.7a)。c)给动力分厂水洗槽送浆液,通知调度,逐渐打开lv19001前后切断及自调阀逐渐给动力分厂送硫酸氨浆液,将浆液密度控制1.05~1.2g/cm2。d)根据补水量和酸雾含量配相应的液氨,将洗涤塔1下塔浆液ph控制在5-6.5之间。并控制尾气洗涤塔1下塔浆液温度≤60℃(即氨洗泵9的出口温度),水洗段温度控制≤40℃(水洗槽的温度)。2.6.2操作参数硫回收酸性尾气洗涤装置参照参数见表3。表3回收装置操作参数本实施例中,为了实现密闭循环,不产生二次污染,各组分在预处理后将进入下一工序进行二次利用,最终实现达标排放。该工艺的基本物料平衡见下表4。表4酸性尾气预洗工序物料平衡表物流名称入塔尾气去锅炉尾气新鲜液氨新鲜补水去锅炉浆液物流序号12345单位nm3/hnm3/hkg/dt/dt/d流量1800018000150(间断)3(间断)5(间断)洗涤塔1选择:风量、风速、及管经计算公式。根据设计规范要,塔内流速:≦2m/s,填充层停留时间>0.9s。泵流量的选择:依据润湿因子>0.1m2/hr进行泵流量的选择。使用本实用新型对原有的设计进行改造后,年减排酸性尾气89吨,原有硫回收装置40m烟囱不再排放酸性尾气气体,洗涤后的净烟气经锅炉系统150m烟囱达标排放,经烟囱上安装的污染物在线数据分析仪监测,混合烟气排放数据经第三方检测对比监测so2排放浓度为20.7mg/m3,cems在线监测so2排放浓度为17.3mg/m3,完全满足《石油化学工业污染物排放标准》(gb31571-2015)、《锅炉大气污染物排放标准》(gb13271-2014)和《关中地区重点行业大气污染物排放标准》(db61/941-2014),达到了污染物超低排放技术要求。硫回收酸性尾气经洗涤装置后,将洗涤塔1底密度为1.05~1.2g/cm3的nh4hso3和(nh4)2so4浆液,送至锅炉系统烟气脱硫装置作为硫酸铵原料,经氧化、干燥、结晶和包装后,作为硫酸铵产品销售,每小时硫酸铵约增产25kg,按照年运行时间8000小时,硫酸铵产品售价600元/吨计算,年增产硫酸铵200吨,则可年新增销售收入12万元。虽然经济效益不是很高,但其带来的环保效益是不可估量的,减少了酸性尾气的排放量,节约了环境容量,改善了当地的区域环境质量。本实施例中的硫回收尾气洗涤装置投运以来,原有硫回收装置40m烟囱不再排放含有污染物气体,洗涤后的净烟气经锅炉系统150m烟囱达标排放,经烟囱上安装的污染物在线数据分析仪监测,混合烟气排放数据满足《石油化学工业污染物排放标准》(gb31571-2015)、《锅炉大气污染物排放标准》(gb13271-2014)和《关中地区重点行业大气污染物排放标准》(db61/941-2014),达到了污染物超低排放技术要求,完善了系统的工艺流程,环保效益显著。以上内容是结合具体的优选实施方式对本实用新型所作的进一步详细说明,不能认定本实用新型的具体实施只局限于这些说明。对于本实用新型所属
技术领域:
的普通技术人员来说,在不脱离本实用新型构思的前提下,还可以做出若干简单推演或替换,都应当视为属于本实用新型的保护范围。当前第1页12