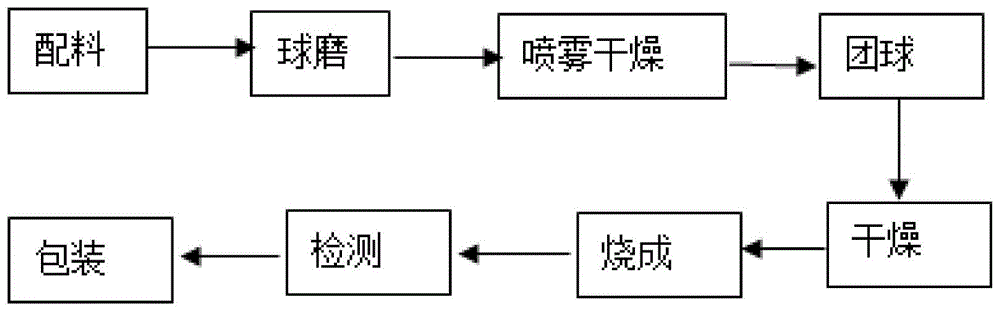
本发明涉及一种建筑材料研磨工艺,具体涉及一种蒸压加气混凝土料浆的研磨工艺。
背景技术:
:蒸压加气混凝土砌块是以粉煤灰,石灰,水泥,石膏,矿渣等为主要原料,加入适量发气剂,调节剂,气泡稳定剂,经配料搅拌,浇注,静停,切割和高压蒸养等工艺过程而制成的一种多孔混凝土制品。在蒸压加气混凝土的生产过程中,需要对混凝土料浆进行研磨,使其细度达到一定要求,再进行浇注、静停等工艺过程;具体地,要将占投料量约70%的硅质材料(大多用硅质砂)通过研磨设备进行粉磨后,使其细度达到能够通过200目筛的筛余小于20%,且颗粒级配分布和料浆温度满足生产工艺要求。在现有技术的研磨过程中,采用的研磨体是含铬钢锻研磨体,其优点是研磨效率高,设备结构简单。但是,采用含铬钢锻研磨体存在以下缺点:1、含铬钢锻研磨体的质量重,研磨过程中与材料进行摩擦与碰撞时产生较大噪音,产生环境噪音污染;同时,研磨过程中由于研磨体质量重,会导致料浆温度升高,从而导致稠化速度大于发气速度,容易造成憋气,破坏材料的气孔结构的均匀性,使坯体上下层容重不均匀、产品强度下降,干缩值增大;2、研磨体质量过重还会增大球磨机负荷,对设备磨损大,导致设备故障率高,影响粉磨效率和生产的正常进行,并且耗能高,增加生产成本。技术实现要素:本发明目的在于克服现有技术的不足,提供一种蒸压加气混凝土料浆的研磨工艺,该研磨工艺能提高研磨质量,对研磨设备磨损小,能降低料浆的温度,并且环保。本发明的目的通过以下技术方案实现:一种蒸压加气混凝土料浆的研磨工艺,其特征在于,在球磨机静态时,向磨机装进球状的陶瓷研磨体,控制总填充率为25%-50%;采用四级配置模式,其中,φ30的陶瓷研磨体为1.9吨-2.5吨,φ25的陶瓷研磨体为2.85吨-3.75吨,φ20的陶瓷研磨体为2.49吨-4.4吨,φ17的陶瓷研磨体为0-2.5吨;设置料浆磨后参数,其中含水量为39%-40%,料浆细度≤20%(即200目筛余量);配置完成后,开始研磨,直至研磨后的料浆符合所设置的磨后参数。优选地,控制总填充率为43.6%;采用四级配置模式具体为:φ30的陶瓷研磨体为2.2吨,φ25的陶瓷研磨体为3.05吨,φ20的陶瓷研磨体为4.4吨,φ17的陶瓷研磨体为2.25吨。优选地,所述球磨机为φ1.83×7m管磨机。优选地,所述陶瓷研磨体由92锆铝陶瓷制成。这样相比于普通的氧化铝陶瓷增加了其中的锆元素,使得研磨体变成多晶结构,提高耐磨性,利用锆的相变增韧,强度和韧性都得到提高,从而使得研磨体的抗冲击韧性能力大幅度提高,碎球率低。优选地,所述陶瓷研磨体的体积密度为3.6g/cm3,不含铬离子,莫氏硬度为9。本发明与现有技术相比具有以下有益效果:1、本发明的研磨工艺绿色环保,降低环境污染;其中,采用不含铬元素的陶瓷研磨体,降低对环境污染同时能提高研磨质量,同时由于陶瓷研磨体的质量轻,在研磨时能够有效降低噪声,避免噪音污染,保障生产员工的健康。2、本发明的研磨工艺能够有效提高料浆质量;其中,由于陶瓷研磨体质量轻,减轻摩擦力度,有效降低料浆的温升,能够保持后续生产过程中材料内部的气孔结构稳定性和均匀性;另外,采用球状的陶瓷研磨体,既可以保证研磨体的硬度,又能对料浆中的硅质材料均匀研磨,使得硅质材料的颗粒形状更佳,有利于产品质量和产量的提升。3、本发明的研磨工艺采用球状的陶瓷研磨体,相比于棒状的铬钢锻研磨体,硬度大,强度高,研磨时与料浆相互滚动,对物料的研磨为点接触(铬钢锻研磨体为线接触),除了具有均匀研磨的特点外,还能长时间保持研磨体自身结构,对研磨体的磨损小,有利于延长使用寿命;同时,对磨机的磨损小,减少设备维护次数,保证生产的连续进行;陶瓷研磨体的质量轻,磨机填充率高,抬高了磨机的重心,能降低磨机能耗,提高设备可靠性等。附图说明图1为本发明的蒸压加气混凝土料浆的研磨工艺中采用的锆铝陶瓷研磨体的生产工艺的流程图。图2为本发明的蒸压加气混凝土料浆的研磨工艺中采用不同陶瓷研磨体配置方案的实验对比表。图3为锆铝陶瓷研磨体的微观结构分析图。图4为高铝陶瓷研磨体的微观结构分析图。图5-图7为采用不用研磨体和磨机对研磨后的料浆的硅质材料进行粒度分布分析的曲线图,其中,图5为1号磨机采用锆铝陶瓷研磨体磨制后的粒度分布分析图,图6为2号磨机采用含铬钢锻研磨体磨制后的粒度分布分析图,图7为3号磨机采用含铬钢锻研磨体磨制后的粒度分布分析图。图8-图13为从不同放大倍数的电镜扫描磨制后产品的图片,其中,图8为锆铝陶瓷研磨体磨制的硅质材料浆液0.5k电镜图片,图9为陶瓷研磨体磨制的硅质材料浆液1.0k电镜图片,图10为陶瓷研磨体磨制的硅质材料浆液2.0k电镜图片;图11为铬钢锻研磨体磨制的硅质材料浆液0.5k电镜图片,图12为铬钢锻研磨体磨制的硅质材料浆液1.0k电镜图片,图13为铬钢锻研磨体磨制的硅质材料浆液2.0k电镜图片。具体实施方式下面结合实施例和附图对本发明作进一步描述,但本发明的实施方式不仅限于此。本实施例的蒸压加气混凝土料浆的研磨工艺,在球磨机静态时,向磨机装进所述陶瓷研磨体,控制总填充率为25%-50%;采用四级配置模式,其中,φ30的陶瓷研磨体为1.9吨-2.5吨,φ25的陶瓷研磨体为2.85吨-3.75吨,φ20的陶瓷研磨体为2.49吨-4.4吨,φ17的陶瓷研磨体为0-2.5吨;设置料浆磨后参数,其中含水量为39%-40%,料浆细度≤20%(即200目筛余量);配置完成后,开始研磨,直至研磨后的料浆符合所设置的磨后参数。具体地,本实施例的研磨工艺中,控制总填充率为43.6%;采用四级配置模式具体为:φ30的陶瓷研磨体为2.2吨,φ25的陶瓷研磨体为3.05吨,φ20的陶瓷研磨体为4.4吨,φ17的陶瓷研磨体为2.25吨。本实施例中,所述陶瓷研磨体由92锆铝陶瓷制成,且呈球状;其中,陶瓷研磨体的直径为φ15mm-φ50mm,体积密度约为3.6g/cm3,不含铬离子,莫氏硬度为9。采用92锆铝陶瓷作为研磨体,相比于普通的氧化铝陶瓷增加了其中的锆元素,使得研磨体变成多晶结构,提高耐磨性,利用锆的相变增韧,强度和韧性都得到提高,从而使得研磨体的抗冲击韧性能力大幅度提高,碎球率低。参见图3和图4,根据高铝陶瓷研磨体与锆铝陶瓷研磨体的微观结构分析(通过扫描电镜sem同倍率(2k)扫描分析)可知,高铝陶瓷材质晶相单一,耐磨性好,较稳定,通过少量熔剂结合刚玉相,但相对较脆;而锆铝陶瓷材质是多晶结构,耐磨性好,利用锆的相变增韧,强度和韧性较高。因此本实施例采用的锆铝陶瓷研磨体的耐磨性更佳,具有耐磨、损耗低、使用寿命长、研磨效果好等优点。另外,其中氧化锆陶瓷硬度大,强度高,常用来做高性能研磨介质,但成本高;氧化铝陶瓷也常用作研磨介质,其成本低,但硬度低;本实例中的陶瓷研磨体将上述两者复合,生产锆铝陶瓷研磨体(锆铝陶瓷球),既可以保证研磨体的硬度,又可以降低成本,同时将研磨体由锻状改为球状,对研磨后硅质材料的颗粒形状更佳,有利于产品质量提升。参见图1,本实施例的蒸压加气混凝土料浆的研磨工艺中采用的球状的锆铝陶瓷研磨体的生产工艺一般包括以下步骤:(1)配料;将高纯氧化铝粉末及其他原料按比例进行配置;(2)球磨;(3)喷雾干燥;(4)团球;(5)干燥;(6)烧成;(7)检测;(8)包装。具体可参见现有技术,也可由萍乡市金刚科技工业园有限公司提供。将蒸压加气混凝土硅质砂料浆分别用铬钢锻研磨体和锆铝陶瓷研磨体进行研磨测试。本次测试采用球磨机(也可采用管磨机)完成,在研磨测试前,先确定球磨机的设备参数,具体如下表:同时,确定磨后料浆的工艺控制参数,具体如下表:含水率(%)200目标准筛余砂浆比重(g/ml)39~41<20%1.55~1.57完成上述相关参数的设定后,使用同一批次的料浆物料,开始进行研磨测试,并检查和记录装载量、填充率、噪音、料浆温度以及台时产量;同时对比两者在研磨时产生的电耗、研磨体耗、衬板损耗、料浆比表面积、砌块出釜抗压强度、研磨成本以及产品综合成本。得出下表对比结果:其中,研磨成本计算具体为:当期厂用电综合电价为0.8元/kwh,锆铝陶瓷研磨体价格为7900元/吨,铬钢锻研磨体价格为7280元/吨;产品综合成本计算具体为:浇注17.25万/方,用砂65528/吨。球磨机的损耗主要为衬板损耗,因此用衬板损耗作为球磨机损耗的参考。通过分析上表可以得出结论:锆铝陶瓷研磨体与铬钢锻研磨体相比,其中的装载量降低、填充率增大、噪音降低、料浆温度下降、台时产量增大、研磨体消耗降低、衬板损耗更换周期变长、料浆比表面积增大、砌块出釜抗压强度增大,研磨成本和产品综合成本降低。由此可见,采用本实施例的研磨工艺,在经济效益、环境保护以及研磨质量三个方面均得到明显提高。参见图2,为了测试出最佳的研磨工艺的研磨体配置方案,在测试过程中分别采用不同的陶瓷研磨体配置方案,具体为:方案一,控制总填充率为27.4%;采用三级配置模式具体为:φ30的陶瓷研磨体为2.49吨,φ25的陶瓷研磨体为3.32吨,φ20的陶瓷研磨体为2.49吨。方案二,控制总填充率为31.4%;采用四级配置模式具体为:φ30的陶瓷研磨体为1.9吨,φ25的陶瓷研磨体为2.85吨,φ20的陶瓷研磨体为2.85吨,φ17的陶瓷研磨体为1.9吨。方案三,控制总填充率为36.4%;采用四级配置模式具体为:φ30的陶瓷研磨体为2.2吨,φ25的陶瓷研磨体为3.3吨,φ20的陶瓷研磨体为3.3吨,φ17的陶瓷研磨体为2.2吨。方案四,控制总填充率为41.4%;采用四级配置模式具体为:φ30的陶瓷研磨体为2.5吨,φ25的陶瓷研磨体为3.75吨,φ20的陶瓷研磨体为3.75吨,φ17的陶瓷研磨体为2.5吨。方案五,控制总填充率为43.6%;采用四级配置模式具体为:φ30的陶瓷研磨体为2.2吨,φ25的陶瓷研磨体为3.05吨,φ20的陶瓷研磨体为4.4吨,φ17的陶瓷研磨体为2.25吨。方案六,控制总填充率为50%;采用四级配置模式具体为:φ30的陶瓷研磨体为3.04吨,φ25的陶瓷研磨体为4.56吨,φ20的陶瓷研磨体为4.56吨,φ17的陶瓷研磨体为3.04吨。参见图2,测试后检测并记录磨机产量、台时电耗和研磨体损耗,并计算研磨成本,可见陶瓷研磨体在与铬钢锻研磨体同样的磨机填充率下,磨机产量较低,电耗、研磨体损耗较高,陶瓷研磨体的研磨成本高于钢锻的研磨成本。随着增加陶瓷研磨体提高磨机的填充率,磨机的产量增加、电耗降低、研磨体损耗降低,陶瓷研磨体的研磨成本逐渐降低;但当陶瓷研磨体堆积到磨机中空轴孔的下缘(方案五)后,再增加陶瓷研磨体提高填充率(方案六),磨机的产量增加很小,电耗、研磨体损耗反而加大,研磨成本增加;因此方案五为采用上述型号规格的球磨机的最佳级配方案。参见图5-图7,通过采用不用研磨体对研磨后的料浆的硅质材料的粒度分布进行对比可知,在d10指标中(d10是指一个样品的累计粒度分布百分数达到10%时所对应的粒径),1号磨机数值为3.096,2号磨机数值为3.9.4,3号磨机数值为4.028;在d50指标中(d50是指一个样品的累计粒度分布百分数达到50%时所对应的粒径),1号磨机数值为31.66μm,2号磨机数值为47.47μm,3号磨机数值为50.07μm;在d90指标中(d90是指一个样品的累计粒度分布百分数达到90%时所对应的粒径),1号磨机数值为114.8μm,2号磨机为159.6μm,3号磨机为163.6μm。由此可见,1号磨机中采用锆铝陶瓷研磨体的研磨效果更佳,磨后的料浆硅质材料的粒度更细。另外,从区间分布曲线上看,1号磨机相比2号磨机和3号磨机分布更加连续、均匀,且中值和最频值分布曲线重叠,2号磨机和3号磨机两曲线峰值均偏离左侧,1号磨机的产品颗粒分布更加连续均匀,即用锆铝陶瓷研磨体磨制成的产品颗粒分布相比铬钢锻研磨体制成的产品颗粒分布更加连续均匀。综上所述,1号磨机产品多为球形颗粒,在球形度整形效果上优于另外两台磨机的产品(与锆铝陶瓷研磨体做功机理是点接触,产品多为球形颗粒;含铬钢锻的做功机理是线接触,产品多为片状和长条状吻合)。参见图8-图10,样品有大小不同的颗粒,从几微米至100微米,有较多标准的圆球,球直径从1微米至30微米。参见图11-图13,产品主要为棱角分明的较大的颗粒,从几十微米至200微米,有少量粉末,有一些小球珠直径大约1-2μm,有少量的大球状物,直径数十微米。可见,从不同放大倍数的电镜扫描图片比较分析,可以直观地看出,使用锆铝陶瓷研磨体磨制的产品和使用含铬钢锻研磨体磨制的产品相比,陶瓷研磨体磨制的产品的球形度更好,且产品的粒径更细。上述为本发明较佳的实施方式,但本发明的实施方式并不受上述内容的限制,其他的任何未背离本发明的精神实质与原理下所做的改变、修饰、替代、组合、简化,均应为等效的置换方式,都包含在本发明的保护范围之内。当前第1页12