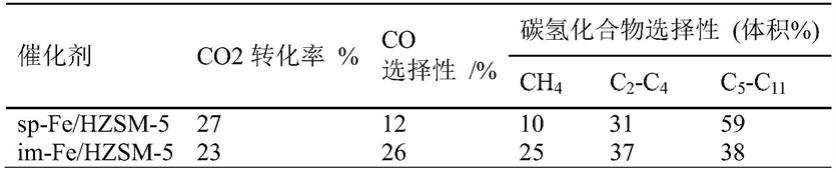
1.本技术涉及一种负载型铁基催化剂的制备方法及其应用,属于催化剂制备领域。
背景技术:2.在自然界中,植物从空气中吸收二氧化碳,经光合作用转化为有机物和氧气,该过程缓慢,所以一直以来化学家们努力想通过化学方式回收利用二氧化碳。如果以二氧化碳作为原料生产烃类化合物,特别是长链烃类燃料,将是一种潜在替代化石燃料的清洁能源策略,不仅可有效降低二氧化碳造成的温室效应,还可减轻对传统化石能源的依赖。但二氧化碳的活化与选择性转化仍面临巨大挑战。相比于更活泼的孪生兄弟一氧化碳,二氧化碳分子非常稳定,难以活化,与经典的费托合成路线相比,二氧化碳与氢分子的催化反应更易生成甲烷、甲醇、甲酸等小分子化合物,而很难生成长链的液态烃燃料。
3.目前报道的可用于生成c
2+
烃类化合物的二氧化碳加氢催化剂,多为金属氧化物催化剂或其与分子筛耦合的复合催化剂,而传统负载型的金属催化剂在二氧化碳加氢这一新型串联催化反应中并不常见,且普遍存在活性较差,难以稳定生成长链液态烃燃料的问题。主要原因在于,负载型金属催化剂中的活性金属分散较差,难以与载体或酸性位进行良好的协同匹配,制备过程不易控制,且在长期高温反应条件下易长大烧结而使反应失活的问题。
技术实现要素:4.根据本技术的一个方面,提供了一种负载型铁基催化剂的制备方法,本技术通过多角旋转桶的旋转,实现铁粒子的均匀分散。本发明的目的是解决二氧化碳加氢催化剂,活性金属分散较差,且在长期高温反应条件下易长大烧结而使反应失活的问题。
5.本发明设计将铁组分通过物理溅射的方法负载于活性炭、碳纳米管、石墨烯、二氧化硅、分子筛等多孔材料载体上,包括以下步骤:首先,将载体进行真空干燥处理,将处理后的载体进行造粒;然后,将颗粒置于物理溅射腔室的载体台上;最后,在真空条件下,通过磁控溅射的方法,将活性铁纳米粒子附着于载体台上的载体表面,通过多角旋转桶的旋转,实现铁粒子的均匀分散。本发明的目的是解决二氧化碳加氢催化剂,活性金属分散较差,且在长期高温反应条件下易长大烧结而使反应失活的问题。
6.本技术采用磁控溅射法直接制备得到负载型铁基催化剂。
7.根据本技术的第一方面,提供了一种负载型铁基催化剂的制备方法,所述方法至少包括:以铁为活性组分,多孔材料为载体,采用物理溅射法制备得到所述负载型铁基催化剂。
8.可选地,所述多孔材料选自活性炭、碳纳米管、石墨烯、二氧化硅、分子筛、氧化铝中的至少一种。
9.具体地,当使用分子筛为载体时,c
5-c
11
为主要产物;当使用不含有分子筛的物质为载体时,c
2-c4为主要产物。
10.可选地,采用多角滚筒溅射装置制备所述负载型铁基催化剂;
11.所述多角滚筒溅射装置包括多角旋转桶和等离子体发生器。
12.可选地,所述方法至少包括:
13.(1)使用等离子体发生器产生的ar离子轰击铁靶材1~30min;
14.(2)将载体置于所述多角旋转桶内,多角旋转桶内抽真空;
15.(3)向多角旋转桶内通入氩气,调节多角旋转桶转速,使ar离子轰击铁靶材所产生的金属铁离子沉积至载体表面,即可得到所述负载型铁基催化剂。
16.可选地,本技术中的多角旋转桶为六棱柱状,在使用时,平躺放置。
17.可选地,本技术中的多角旋转桶在旋转时,为“钟摆式”旋转,载体放置于底面,在多角旋转桶的带动下,载体上下移动,但是由于多角旋转桶棱的限制,不会移动至多角旋转桶外。
18.可选地,本技术中的多角旋转桶上还设置有压力计、真空室、机械振动单元、真空泵。
19.可选地,所述多角滚筒溅射装置包括等离子体发生器、金属靶材和多角旋转桶;
20.所述等离子体发生器用于产生ar离子;
21.所述ar离子用于轰击金属靶材;
22.所述多角旋转桶外壁上设置有压力计、真空室、机械振动单元和真空泵;所述多角旋转桶平躺设置;
23.溅射时,载体设于所述多角旋转桶底面;所述金属靶材进入所述多角旋转桶内;所述金属靶材竖直向下溅射至所述载体上;
24.溅射时,多角旋转桶呈“钟摆式”摇摆。
25.可选地,在所述多角旋转桶外壁外还设有保护罩。
26.可选地,在所述步骤(1)之前,还需要对铁靶材进行清洁处理。
27.优选地,使用等离子体发生器产生的ar离子轰击铁靶材10~30min。
28.可选地,载体在使用前,需要进行造粒处理。因为载体一般是粉末,粉末置于桶内旋转时易悬浮,因此需要造粒处理。
29.可选地,在所述步骤(2)中,多角旋转桶内抽真空至压力达到9.9
×
10-4
pa以下;
30.优选地,在所述步骤(2)中,多角旋转桶内抽真空至压力达到9.9
×
10-6-9.9
×
10-4
pa以下。
31.可选地,在所述步骤(3)中,向多角旋转桶内通入氩气的流量为10~50ml/min,始终维持多角旋转桶内压力为1.0~3.0pa;
32.可选地,在所述步骤(3)中,向多角旋转桶内通入氩气的流量上限独立地选自50ml/min、40ml/min、30ml/min、20ml/min,下限独立地选自10ml/min、40ml/min、30ml/min、20ml/min。
33.可选地,在所述步骤(3)中,维持多角旋转桶内压力上限独立地选自3pa、2.5pa、2pa、1.5pa,下限独立地选自1pa、2.5pa、2pa、1.5pa。
34.优选地,在所述步骤(3)中,向多角旋转桶内通入氩气的流量为12~30ml/min,始终维持多角旋转桶内压力为1.0~1.5pa。
35.可选地,所述多角旋转桶转速为1~20rpm。
36.可选地,所述多角旋转桶转速上限独立地选自20rpm、15rpm、10rpm、5rpm,下限独立地选自1rpm、15rpm、10rpm、5rpm。
37.优选地,所述多角旋转桶转速为5~10rpm。
38.可选地,在所述步骤(3)后,还包括如下步骤:溅射结束后,桶内通入o2/ar混合气至压力达到常压,其中o2体积含量为0.5~5%,优选1~3%。
39.优选地,所述载体选自分子筛。
40.优选地,所述分子筛选自hzsm-5。
41.可选地,所述分子筛的硅铝比为20-200。
42.可选地,所述分子筛的硅铝比上限独立地选自200、150、100、50,下限独立地选自20、150、100、50。
43.具体地,本技术需要通过多角旋转桶的旋转才可得到均匀分散的铁纳米颗粒,多角旋转桶的旋转使得载体可以充分的接触溅射下来的金属颗粒。
44.具体地,本技术中的磁控溅射设备,可以通过多角旋转桶的旋转以及桶棱角的限制,使载体始终保持在多角旋转桶的底层接受溅射下来的纳米粒子;同时辅以桶外壁的机械振动系统,振动速率保持在20-40次/min,保证沉积过程中的粉末不会因过热而聚集。最终,使ar离子轰击铁靶材所产生的纳米金属铁粒子均匀沉积在载体的表面。
45.具体地,若要实现高度分散的fe纳米颗粒,采用磁控溅射法是很好的选择,中间不涉及任何化学试剂,无废弃化学试剂带来的环境污染,属于“干法”制备过程;其他用湿式化学沉积的办法制备高分散的fe较难,不易控制,而且易产生环境二次污染。
46.根据本技术的第二方面,还提供了一种负载型铁基催化剂,包括根据上述方法制备得到的负载型铁基催化剂中的任一种。
47.可选地,活性组分在负载型铁基催化剂中的质量含量为10~30%;
48.可选地,活性组分在负载型铁基催化剂中的质量含量上限独立地选自30%、25%、20%、15%,下限独立地选自10%、25%、20%、15%。
49.优选地,在负载型铁基催化剂中,所述活性组分的粒径为3~20nm。
50.根据本技术的第三方面,还提供了一种二氧化碳加氢制备烃类化合物的方法,将含有二氧化碳和氢气的原料气,在催化剂的存在下反应,制备得到烃类化合物;
51.所述催化剂选自根据上述方法制备得到的负载型铁基催化剂、上述负载型铁基催化剂中的任一种。
52.可选地,在所述原料气中,二氧化碳和氢气的体积比为1:1~1:6。
53.可选地,所述反应的条件为:反应温度为280~320℃;原料气的体积空速为2000~10000h-1
;反应压力为1~4mpa。
54.可选地,所述原料气的体积空速上限独立地选自10000h-1
、8000h-1
、6000h-1
、4000h-1
,下限独立地选自2000h-1
、8000h-1
、6000h-1
、4000h-1
。
55.本技术能够产生的有益效果包括:
56.1)本技术提供的催化剂制备方法采用磁控溅射,中间不涉及任何化学试剂,无废弃化学试剂带来的环境污染,属于“干法”制备过程;其他用湿式化学沉积的办法制备高分散的fe较难,不易控制,而且易产生环境二次污染;
57.2)本发明可解决二氧化碳加氢催化剂,活性金属分散较差,且在长期高温反应条
件下易长大烧结而使反应失活的问题。
附图说明
58.图1为多角滚筒溅射装置结构示意图;
59.图2为实施例1制备的fe/hzsm-5催化剂的透射电镜图。
具体实施方式
60.下面结合实施例详述本技术,但本技术并不局限于这些实施例。
61.如无特别说明,本技术的实施例中的原料和试剂均通过商业途径购买。
62.本技术实施例中使用的hzsm-5分子筛来源于南开催化剂厂。
63.本技术实施例中使用的im-fe/hzsm-5为浸渍法制备的铁催化剂,具体的,在室温搅拌条件下,通过控制铁的负载量为15%,将26.8ml的硝酸铁(1m)的溶液浸渍到10g粉末载体hzsm-5(硅铝比160)上,直至载体完全湿润,停止搅拌,并保持老化时间12h,将得到的混合物进行120℃干燥12h处理,然后进行500℃焙烧3h,即得im-fe/hzsm-5。
64.本发明所采用的测试分析方法如下:
65.利用高分辨透射电镜(tem)观察制备催化剂样品的形貌,金属粒子大小及分布等。
66.本发明所采用的催化剂评价过程如下:
67.采用流动的固定床反应器进行二氧化碳催化加氢的反应过程,并以在线及离线的气相色谱仪分析产物组成。反应前,将新鲜催化剂在400℃氢气或合成气条件下原位活化10小时以上。还原后将温度降至催化反应温度280~320℃。反应中原料气配比为co2/h2=1:3,体积空速控制为2000~10000h-1
,压力控制在1~4mpa。冷阱中加入辛烷做溶剂,用来捕捉重质烃。气相产物中co、co2及ch4组分由装有tcd检测器的在线气相色谱进行含量分析,而轻烃组分(c
1-c7)的含量可由另一台装有fid检测器的在线气相色谱分析。反应结束后,收集辛烷冷阱中的重质烃组分,并加入十二烷作为内标。液体组分由装有fid检测器的离线气相色谱进行分析。将气液相分析后的结果进行归一化,得到产物co选择性s(co)、烃组分选择性s(i)以及转化率x(co2)。
68.本技术中,“sp”代表磁控溅射方法,“im”代表浸渍方法。
69.图1为多角滚筒溅射装置结构示意图,包括等离子体发生器和多角旋转桶,多角旋转桶上还设置有压力计、真空室、机械振动单元、真空泵。多角旋转桶为六棱柱状,在使用时,平躺放置。在旋转时,为“钟摆式”旋转,载体放置于底面,在多角旋转桶的带动下,载体上下移动,但是由于多角旋转桶棱的限制,不会移动至多角旋转桶外。
70.实施例1
71.sp-fe/hzsm-5催化剂制备过程如下:
72.采用多角滚筒溅射装置制备催化剂,制备前对靶材表面进行清洁处理,用等离子体发生器产生的ar离子轰击铁靶(质量纯度99.9%以上)靶材30分钟;
73.将载体粉末hzsm-5分子筛(硅铝比50)至于多角旋转桶中,桶内抽真空至压力达到9.9x10-4
pa以下;
74.桶中通入ar气(体积纯度99.9%以上),流量为15ml/min,维持桶内压力为2.0pa;
75.将多角滚筒转速加至10rpm,桶外振动速率保持在20次/min,使ar离子轰击铜靶材
所产生的纳米金属铁粒子均匀沉积在载体表面;
76.溅射结束后,桶内通入o2/ar混合气至压力达到常压,其中o2体积浓度为1%。
77.制备得到的fe负载量为15%(质量比)的fe/hzsm-5催化剂的透射电镜图如图2所示,由图可见,采用磁控溅射法制备的fe/hzsm-5催化剂,铁的分散非常均匀,粒径集中分布于2-3nm之间。
78.sp-fe/hzsm-5催化剂反应性能评价过程如下:
79.以sp-fe/hzsm-5和传统的浸渍法im-fe/hzsm-5(铁含量均为15%)进行二氧化碳加氢反应,进料条件为二氧化碳与氢气体积比为1:3,反应条件为:反应温度300℃,压力3.0mpa,空速4000h-1
。
80.表1制备的铁催化剂与传统催化剂对比的二氧化碳反应结果
[0081][0082]
二氧化碳加氢反应评价实验说明,相对传统浸渍法制得的fe/hzsm-5催化剂相比,通过磁控溅射法制得的sp-fe/hzsm-5铁催化剂,其二氧化碳反应中c
5-c
11
汽油馏分段(包含c
5-c
11
馏分段的烷烃、烯烃、异构烃、芳烃、环烷烃等)的选择性得到明显提升,突破了asf(费托合成的产物分布规律)(最高约45%)的理论限制。二氧化碳的转化率选择性也得到增加,同时副产物一氧化碳选择性明显降低。说明高度分散的sp-fe/hzsm-5铁催化剂在二氧化碳加氢反应中反应性能提升明显,提出的合成路线简单有效。
[0083]
实施例2
[0084]
sp-fe/sio2催化剂制备过程如下:
[0085]
采用多角滚筒溅射装置制备催化剂,制备前对靶材表面进行、清洁处理,用等离子体发生器产生的ar离子轰击铁靶(质量纯度99.9%以上)靶材20分钟;
[0086]
将载体粉末二氧化硅(比表面积约200m2/g)至于多角旋转桶中,桶内抽真空至压力达到9.9x10-4
pa以下;
[0087]
桶中通入ar气(体积纯度99.9%以上),流量为30ml/min,维持桶内压力为1.0pa;
[0088]
将多角滚筒转速加至20rpm,桶外振动速率保持在30次/min,使ar离子轰击铜靶材所产生的纳米金属铁粒子均匀沉积在载体表面;
[0089]
溅射结束后,桶内通入o2/ar混合气至压力达到常压,其中o2体积浓度为5%。
[0090]
表2制备的铁催化剂与传统催化剂对比的二氧化碳反应结果
[0091][0092]
二氧化碳加氢反应评价实验说明,相对传统浸渍法制得的fe/sio2催化剂相比,通过磁控溅射法制得的sp-fe/sio2铁催化剂,其二氧化碳反应中c
2-c4馏分段的烯烃和烷烃选
择性得到明显提升。二氧化碳的转化率也得到增加,同时副产物一氧化碳选择性明显降低。说明高度分散的sp-fe/sio2铁催化剂在二氧化碳加氢反应中反应性能提升明显,提出的合成路线简单有效。
[0093]
实施例3
[0094]
将上述实施例2中的二氧化硅载体(比表面积约200m2/g)替换为碳纳米管(cnt,多壁,比表面积约400m2/g),其余制备过程同上,催化剂记为sp-fe/cnt。
[0095]
表3制备的铁催化剂与传统催化剂对比的二氧化碳反应结果
[0096][0097]
二氧化碳加氢反应评价实验说明,相对传统浸渍法制得的im-fe/cnt催化剂相比,通过磁控溅射法制得的sp-fe/cnt铁催化剂,其二氧化碳反应中c
2-c4馏分段的烯烃和烷烃选择性得到明显提升,其中烯烃比例可提升在c2-c4中占到75%。二氧化碳的转化率也得到增加,同时副产物一氧化碳选择性明显降低。说明高度分散的sp-fe/cnt铁催化剂在二氧化碳加氢反应中反应性能提升明显,利于生成低碳烯烃,提出的合成路线简单有效。
[0098]
实施例4
[0099]
将上述实施例2中的二氧化硅载体(比表面积约200m2/g)替换为石墨烯粉末(graphene,单层,比表面积约500m2/g),其余制备过程同上,催化剂记为sp-fe/graphene。
[0100]
表4制备的铁催化剂与传统催化剂对比的二氧化碳反应结果
[0101][0102]
二氧化碳加氢反应评价实验说明,相对传统浸渍法制得的im-fe/graphene催化剂相比,通过磁控溅射法制得的sp-fe/cnt铁催化剂,其二氧化碳反应中c
2-c4馏分段的烯烃和烷烃选择性得到明显提升,其中烯烃比例可提升在c2-c4中占到70%。二氧化碳的转化率也得到增加,同时副产物一氧化碳选择性明显降低。说明高度分散的sp-fe/graphene铁催化剂在二氧化碳加氢反应中反应性能提升明显,利于生成低碳烯烃,提出的合成路线简单有效。
[0103]
实施例5
[0104]
sp-fe/hzsm-5催化剂制备过程如下:
[0105]
采用多角滚筒溅射装置制备催化剂,制备前对靶材表面进行清洁处理,用等离子体发生器产生的ar离子轰击铁靶(质量纯度99.9%以上)靶材15分钟;
[0106]
将载体粉末hzsm-5分子筛(硅铝比50)至于多角旋转桶中,桶内抽真空至压力达到9.9x10-5
pa;
[0107]
桶中通入ar气(体积纯度99.9%以上),流量为30ml/min,维持桶内压力为1.5pa;
[0108]
将多角滚筒转速加至10rpm,桶外振动速率保持在20次/min,使ar离子轰击铜靶材所产生的纳米金属铁粒子均匀沉积在载体表面;
[0109]
溅射结束后,桶内通入o2/ar混合气至压力达到常压,其中o2体积浓度为1%。
[0110]
制备得到的fe负载量为18%(质量比)的sp-fe/hzsm-5催化剂。
[0111]
sp-fe/hzsm-5催化剂反应性能评价过程如下:
[0112]
以sp-fe/hzsm-5和传统的浸渍法im-fe/hzsm-5(铁含量均为18%)进行二氧化碳加氢反应,进料条件为二氧化碳与氢气体积比为1:3,反应条件为:反应温度300℃,压力3.0mpa,空速4000h-1
。
[0113]
表5制备的铁催化剂与传统催化剂对比的二氧化碳反应结果
[0114][0115]
二氧化碳加氢反应评价实验说明,相对传统浸渍法制得的fe/hzsm-5催化剂相比,通过磁控溅射法制得的sp-fe/hzsm-5铁催化剂,其二氧化碳反应中c
5-c
11
汽油馏分段(包含c
5-c
11
馏分段的烷烃、烯烃、异构烃、芳烃、环烷烃等)的选择性得到明显提升,突破了asf(费托合成的产物分布规律)(最高约45%)的理论限制。二氧化碳的转化率选择性也得到增加,同时副产物一氧化碳选择性明显降低。说明高度分散的sp-fe/hzsm-5铁催化剂在二氧化碳加氢反应中反应性能提升明显,提出的合成路线简单有效。
[0116]
实施例6
[0117]
将上述实施例1中制备得到的fe负载量为12%(质量比)fe/hzsm-5催化剂替换为fe负载量为25%(质量比)fe/hzsm-5催化剂,其余制备及反应评价过程同实施例1中所述。
[0118]
表6制备的铁催化剂与传统催化剂对比的二氧化碳反应结果
[0119][0120][0121]
二氧化碳加氢反应评价实验说明,相对传统浸渍法制得的im-fe/hzsm-5催化剂相比,通过磁控溅射法制得的sp-fe/hzsm-5铁催化剂,其二氧化碳反应中c
5-c
11
汽油馏分段(包含c
5-c
11
馏分段的烷烃、烯烃、异构烃、芳烃、环烷烃等)的选择性得到明显提升,突破了asf(费托合成的产物分布规律)(最高约45%)的理论限制。二氧化碳的转化率选择性也得到增加,同时副产物一氧化碳选择性明显降低。说明高度分散的sp-fe/hzsm-5铁催化剂在二氧化碳加氢反应中反应性能提升明显,提出的合成路线简单有效。
[0122]
实施例7
[0123]
将上述实施例1中以sp-fe/hzsm-5和传统的浸渍法im-fe/hzsm-5(铁含量均为15%)进行二氧化碳加氢反应,进料条件为二氧化碳与氢气体积比为1:3,反应条件为:反应
温度320℃,压力2.0mpa,空速8000h-1
。
[0124]
表7制备的铁催化剂与传统催化剂对比的二氧化碳反应结果
[0125][0126]
二氧化碳加氢反应评价实验说明,相对传统浸渍法制得的fe/hzsm-5催化剂相比,通过磁控溅射法制得的sp-fe/hzsm-5铁催化剂,其二氧化碳反应中c
5-c
11
汽油馏分段(包含c
5-c
11
馏分段的烷烃、烯烃、异构烃、芳烃、环烷烃等)的选择性得到明显提升,突破了asf(费托合成的产物分布规律)(最高约45%)的理论限制。二氧化碳的转化率选择性也得到增加,同时副产物一氧化碳选择性明显降低。说明高度分散的sp-fe/hzsm-5铁催化剂在二氧化碳加氢反应中反应性能提升明显,提出的合成路线简单有效。
[0127]
实施例8
[0128]
将上述实施例1中以sp-fe/hzsm-5和传统的浸渍法im-fe/hzsm-5(铁含量均为15%)进行二氧化碳加氢反应,进料条件为二氧化碳与氢气体积比为1:3,反应条件为:反应温度280℃,压力4.0mpa,空速3000h-1
。
[0129]
表8制备的铁催化剂与传统催化剂对比的二氧化碳反应结果
[0130][0131]
二氧化碳加氢反应评价实验说明,相对传统浸渍法制得的fe/hzsm-5催化剂相比,通过磁控溅射法制得的sp-fe/hzsm-5铁催化剂,其二氧化碳反应中c
5-c
11
汽油馏分段(包含c
5-c
11
馏分段的烷烃、烯烃、异构烃、芳烃、环烷烃等)的选择性得到明显提升,突破了asf(费托合成的产物分布规律)(最高约45%)的理论限制。二氧化碳的转化率选择性也得到增加,同时副产物一氧化碳选择性明显降低。说明高度分散的sp-fe/hzsm-5铁催化剂在二氧化碳加氢反应中反应性能提升明显,提出的合成路线简单有效。
[0132]
实施例9
[0133]
将上述实施例1中以sp-fe/hzsm-5和传统的浸渍法im-fe/hzsm-5(铁含量均为15%)进行二氧化碳加氢反应,进料条件为二氧化碳与氢气体积比为1:3,反应条件为:反应温度400℃,压力3.0mpa,空速9000h-1
。
[0134]
表9制备的铁催化剂与传统催化剂对比的二氧化碳反应结果
[0135][0136]
二氧化碳加氢反应评价实验说明,相对传统浸渍法制得的im-fe/hzsm-5催化剂相比,通过磁控溅射法制得的sp-fe/hzsm-5铁催化剂,其二氧化碳反应中c
5-c
11
汽油馏分段(包含c
5-c
11
馏分段的烷烃、烯烃、异构烃、芳烃、环烷烃等)的选择性得到明显提升,突破了asf(费托合成的产物分布规律)(最高约45%)的理论限制。二氧化碳的转化率选择性也得到增加,同时副产物一氧化碳选择性明显降低。说明高度分散的sp-fe/hzsm-5铁催化剂在二氧化碳加氢反应中反应性能提升明显,提出的合成路线简单有效。
[0137]
更为重要的是,sp-fe/hzsm-5铁催化剂在高温400度,100小时长时间连续反应过程中基本无失活现象,转化率和c
5-c
11
汽油烃选择性几乎保持不变,而同条件下的im-fe/hzsm-5催化剂,其二氧化碳转化的活性下降了40%,c
5-c
11
产物的选择性也下降了12.5%。说明sp-fe/hzsm-5铁催化剂在二氧化碳加氢反应中不仅反应性能提升明显,而且可在高温下保持长时间的稳定性,解决了传统催化剂易失活的问题。
[0138]
以上所述,仅是本发明的几个实施例,并非对本发明做任何形式的限制,虽然本发明以较佳实施例揭示如上,然而并非用以限制本发明,任何熟悉本专业的技术人员,在不脱离本发明技术方案的范围内,利用上述揭示的技术内容做出些许的变动或修饰均等同于等效实施案例,均属于技术方案范围内。