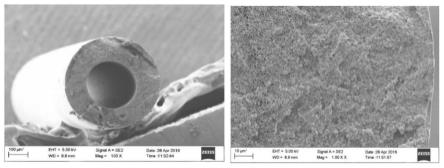
:
1.本发明涉及一种用于液压油脱气的中空纤维膜制备及改性方法,属于功能膜和航空安全技术领域。
背景技术:2.液压传动由于功率体积比大、容易实现自动化等特点在航空航天领域得到广泛应用。液压系统是飞机重要的二次能源系统,以油液为工作介质,靠油压驱动执行机构完成起落架收放、刹车、转弯、飞行控制、反推装置和舱门操纵等特定操纵动作。现代客机的液压系统工作介质为阻燃磷酸酯基液压油。有关资料表明,在液压系统的使用过程中50~70%的故障是由液压系统的污染引起的。飞机液压系统控制精度要求的提高对工作介质的污染控制水平也提出了更高的要求。整体而言,目前对液压油内固体颗粒污染物及液体污染的控制技术已较为成熟,但是对空气污染的控制研究尚有欠缺。
3.事实上液压系统中空气污染对其性能的影响非常严重,主要表现在以下几个方面:(1)降低油液容积模数:油液中游离气体的存在会大幅降低油液的弹性模量,造成系统响应迟缓,工作不稳定,从而出现飞机操纵跟随性不好;(2)产生气蚀:当油液从低压进入高压时气泡会瞬间被压缩破灭而产生局部高温和高压冲击,对液压元件造成损害;(3)引起系统压力不稳定:油液中气体的存在影响系统操纵力的稳定,气泡析出会使系统压力发生波动,从而产生操纵不到位的情况;(4)增加系统温升:大量游离气体被急剧压缩时会产生局部高温,甚至产生火花,可能引起油液燃烧碳化;(5)促进油液氧化变质:油液中空气含量增多必然对油液产生氧化腐蚀,增加油液的酸值,缩短油液的使用寿命;(6)产生噪声和振动:油液所含空气随压力的高低变化频繁出现溶解析出现象,将在系统中形成难以消除的噪声和振动。
4.液压油中的空气污染主要由两种原因造成:外界气体与液压油接触直接溶解于其中(开式油箱)以及系统运行过程中产生的空气污染。尽管在液压系统设计中采取了各种预防措施,但是空气污染仍然难以完全避免,有证据表明即使是闭式系统,其中仍含有~25%的溶解空气需要被脱除,因此在运行过程中不断排除空气对于液压系统的正常运行非常重要。目前采用的的排气手段主要包括排气阀排气、离心式排气以及真空排气等。
5.中国专利cn92108634.2提供了一种从油液中脱气、脱水的方法,包括待处理的油液的输入、真空脱气、脱水和处理后的油液的输出,其特征在于在油液进入真空罐前要经过一节流步骤。
6.中国专利cn202010532953.8提供了一种消泡装置,包括油箱本体,其特征在于,所述油箱本体内置隔板,所述隔板将油箱本体分隔为油箱上腔体和油箱下腔体,所述隔板上设置有导通油箱上腔体和油箱下腔体的旋流口,所述油箱本体内的液压油的液面高度高于所述隔板的高度;所述油箱下腔体内通过弧形旋流板形成旋流腔,注入油箱下腔体的液压油通过旋流腔形成旋流并分离出含有气泡的轻质液压油,所述轻质液压油通过旋流口汇集至油箱上腔体。
7.上述方法操作繁琐,且排气的规律性、均匀性、可靠性等不能保证,针对民航客机存在的液压油脱气需求,本发明提出了一种采用所制备的中空纤维膜对液压系统中的溶解空气进行脱除的方法。膜技术广泛应用于气体分离领域,已经被证明是高效、可靠的过程。气体在压差推动力作用下,以“溶解扩散”方式渗透通过聚合物,而液压油则因为较大的分子体积/膜表面亲水性排斥作用等无法渗透通过膜。依此技术背景,在液压系统回流管道中加入中空纤维膜组件,液压油通过组件壳层流动,膜内管为真空状态故在膜两侧形成分压差,在此推动力作用下,液压油中溶解的空气便渗透通过膜,随着脱气过程的进行,在中空纤维膜轴向液压油流动方向上其所含溶解空气的量逐渐减低,最终实现液压系统中溶解空气的高效脱除。
8.基于以上背景,本发明提供了一种可用于航空液压油中溶解空气脱除的中空纤维膜制备及改性方法。
技术实现要素:9.本发明针对航空液压油中存在大量溶解空气,其对飞机的安全飞行构成重大挑战,急需开发出安全、可靠、稳定地实现液压油脱气过程的客观要求,从提高膜在液压油脱气过程的稳定性及高效性出发,提供了一种可对液压油具有优异的耐受性,在高压液压油中性能稳定,在液压油中无明显溶胀及液压油膜内渗透现象的中空纤维膜制备及改性方法。
10.本发明首先在液压油中性能稳定的特定高分子材料,采用混合溶剂溶解制得均一膜液,通过改变纺丝过程参数对相转化过程进行精细调控,制备出具有致密无缺陷皮层结构的中空纤维膜底膜或者存在表皮缺陷孔的中空纤维膜;前者致密皮层厚故气体通量小但可直接应用于液压油脱气过程;后者致密皮层薄且有缺陷孔故气体通量大,但是因为高压液压油会渗透通过此膜所以无法直接应用,需要采用特定材料进行表面缺陷孔密封改性处理后才可应用于液压油脱气过程。
11.本发明的具体步骤如下:
12.a.铸膜液制备:在50~90℃温度下,以一定比例将聚合物/溶剂/非溶剂混合搅拌,形成均一溶液并真空脱泡,制成聚合物含量25~35wt%的透明铸膜液;
13.所用的膜材料可以是聚酰亚胺、聚醚酰亚胺、聚砜、聚醚砜、聚苯砜、聚偏氟乙烯、纤维素、聚醋酸纤维素等;所用的溶剂可以是n-甲基吡咯烷酮、二甲基乙酰胺、二甲基亚砜、二氧六环、环己酮、四氢呋喃等;所用的非溶剂可以是甲醇、乙醇、丙酮、水、丁内酯等;
14.b.采用沉浸相转化法干湿纺制备具有中空纤维膜,纺丝工艺参数为:纺丝温度50~110℃,干纺距离为0~500mm,外凝胶浴为0~50℃的自来水,内管芯液为含有0~90wt%溶剂的水溶液,通过向膜液料罐施加100~500kpa的n2推动膜液进入齿轮泵,并由齿轮泵精确控制流量,通过喷头挤压进入凝胶浴池,在内外凝胶浴的共同作用下形成中空纤维底膜;
15.c.用流动自来水冲洗中空纤维膜48小时以上以充分洗去膜内残留溶剂,然后采用溶剂置换方法(乙醇置换膜内水,正己烷置换乙醇)对膜内水进行充分去除,正己烷挥发后将底膜放入温度50~120℃的真空烘箱中进行干燥,根据膜液初始浓度不同,可得到具有致密无缺陷皮层结构的中空纤维膜底膜或者存在表皮缺陷孔的中空纤维膜;
16.以上具体纺丝工艺流程为:用压缩氮气把纺丝溶液压出纺丝液罐,经计量泵计量
后进入过滤器,然后进入插管式纺丝喷头内外管间的空腔中,压出后经过一定高度的空气层干纺阶段后进入凝胶浴中。芯液由平流泵控制从贮存容器中压入喷头的内管,与纺丝溶液同时挤出喷头,这样纺丝液通过干纺阶段后进入凝胶浴固化为初生纤维,用流动自来水冲洗中空纤维膜48小时以上以充分洗去膜内残留溶剂,然后采用溶剂置换方法(乙醇置换膜内水,正己烷置换乙醇)对膜内水进行充分去除;正己烷挥发后将底膜放入温度50~120℃的真空烘箱中进行干燥,干燥2~5小时后得到干态的中空纤维膜;
17.d.对中空纤维膜表面孔缺陷进行封堵及改性的方法,其特征在于首先将中空纤维膜制备为适用规格的膜组件,并配置浓度为1~10wt%的涂层液,涂层所采用的聚合物可以是醋酸纤维素、聚乙二醇、壳聚糖、聚乙烯醇、聚乳酸等,根据聚合物不同向涂层液中加入一定的交联剂,交联剂一般是戊二醛、硼酸;将所制备的涂层液置于膜组件内中空纤维膜外侧,通过膜内侧抽真空的方式形成动力,使得涂层液进入膜孔,并通过调控真空度以避免涂层液透过缺陷孔进入膜的中空孔;在中空侧保持真空情况下对膜外侧的多余涂层液进行去除处理,方法可以是水洗、乙醇洗、甲醇洗等;然后将组件置入温度设置为50~100℃的真空烘箱进行高温交联改性处理;经此过程处理的膜组件表面孔缺陷可被有效去除,可以应用于液压油脱气过程。
18.本发明所制备的中空纤维膜对液压油具有优异的耐受性,在高压液压油中性能稳定,无液压油膜内渗透及膜被溶胀现象。在进行液压油膜法脱气过程中,液压油在膜外侧流动,膜内侧通过抽真空形成渗透动力,使得液压油中溶解的空气渗透通过膜而被有效脱除。本发明所提供的中空纤维膜制备及改性方法,可有效提高液压油中溶解空气的脱除效率及过程可靠性,同时通过控制中空纤维膜尺寸,以中空纤维膜组件的形式进行工作,可以大幅度提高液压油与脱气膜的接触面积,具有脱气效率高、能耗低以及对航空系统至关重要的体积要求小等优点。
19.与常用的液压油脱气装置及过程相比,本发明具有以下优点:
20.(1)采用膜法对液压油脱气过程简单且稳定可靠;
21.(2)膜法脱气原理基于气体在膜内的渗透速率,脱气均匀效率高;
22.(3)中空纤维膜尺寸小,比表面高,可为液压油脱气提供超高的脱气面积;
23.(4)中空纤维膜组件体积小,不会对航空液压油脱气体系造成体积负担;
24.(5)膜组件规格可变,可依据具体脱气要求选择合适的膜组件,适应性强。
25.基于以上总结,本发明所提供的一种可用于航空液压油中溶解空气脱除的中空纤维膜制备及改性方法,对实现我国航空系统液压油高效脱气过程具有重要价值。
附图说明
26.图1中空纤维膜电镜照片
27.图2用于液压油脱气过程的中空纤维膜组件,图中:1环氧封头;2中空纤维膜;3液压油入口(未脱气);4/6脱除的空气出口(负压);5液压油出口(脱气后),该组件整体尺寸为直径~8.0cm,长度~20.0cm的圆柱体,其中密封有中空纤维膜共计~33000根。该组件安装在液压系统的回流管道,可以在1hr内,将140l液压油中所含溶解空气量从25%脱除到5%的水平。
具体实施方式
28.实施例1
29.把36克聚酰亚胺加入64克nmp/四氢呋喃(重量比例为6:1)混合溶剂中,在90℃与氮气保护下搅拌24hr完全溶解,真空脱泡后,得到浓度为36wt.%的铸膜液,然后放入纺丝料罐进行湿纺。纺丝温度70℃,芯液为95wt%nmp的水溶液,流量0.4ml/min,凝胶浴为水,水浴温度为室温。所纺的中空纤维膜在流动去离子水中清洗24小时后采用溶剂置换法进行干燥(先用乙醇置换膜内水,再用正己烷置换乙醇,正己烷挥发后将底膜放入温度80℃的真空烘箱中进行干燥6小时)。扫描电子显微镜显示该中空纤维膜具有致密无缺陷皮层结构(如图1)。
30.该底膜内/外径为0.36mm/0.18mm。测定了所制备底膜的气体渗透速率。在25℃,0.5mpa压力下,该聚酰亚胺膜的o2渗透速率为12.0gpu(1gpu=10-6
cm3(stp)/(cm2·s·
cmhg)),n2的渗透速率为2.0gpu。氧氮分离系数为6.0,与聚酰亚胺材料的本征氧氮分离系数相当,表明所制备的中空纤维膜皮层无缺陷孔,可直接应用于液压油脱气过程。
31.实施例2
32.将实施例1所描述的中空纤维膜浸泡于液压油中,经过60天浸泡,膜无溶胀现象;将中空纤维膜制备成组件,在膜外侧通入液压油,并升高其压力至3.0mpa,连续施压30天,膜内无液压油渗透现象,表明所制备的聚酰亚胺中空纤维膜具有优异的液压油耐受性。
33.实施例3
34.将实施例1中所描述的中空纤维膜集束制备为图2所示的脱气膜组件,在进行液压油脱气处理时,液压油通过膜丝的外侧,内侧进行抽真空处理(真空度90kpa)。
35.脱气膜组件包括一密闭的中空筒体,筒体的左右二端分别设有气体出口,于筒体内靠近左右二端分别设有气体出口处分别设有二个隔板,隔板的四周边缘与筒体内壁面密闭连接;隔板将筒体内部分隔成左、中、右三个互不连通的腔室,中空纤维膜置于筒体的中部腔室内、二端穿过隔板分别伸出至左、右二个腔室中,于中部腔室的壁面上设有物料进口和出口。