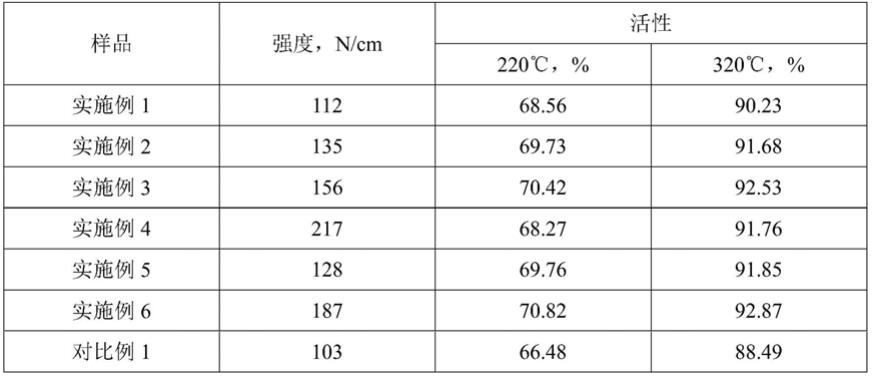
1.本发明涉及工业一氧化碳合成气水汽变换催化剂制氢领域,具体涉及一种节能环保的耐硫变换催化剂制备方法。
背景技术:2.生产生活中使用的大宗化学品、原材料等都来源于基础能源——石油、煤炭和天然气,而利用它们来合成一系列的产品或原料,包括现代兴起的氢能源行业,首先必须要得到氢气,而得到氢气就要用到一氧化碳耐硫变换催化剂。因此,一氧化碳耐硫变换催化剂是现代煤化工工艺技术的核心之一。我国煤化工经过多年的发展,不断涌现大型加压煤气化技术,如大型煤制甲醇、煤制油、煤制天然气、煤制乙二醇、煤制烯烃、煤制乙二醇、煤制芳烃等,形成了我国特有的现代煤化工技术。因此,能试用于中大型设备的一氧化碳耐硫变换催化剂的需求也不断增加。
3.高压耐硫变换催化剂实现工业化应用以来已广泛用于煤化工行业。其活性组分主要为钴、钼,载体主要为铝酸镁或铝酸钛结构。目前,国内外已开发成功的钴-钼系耐硫变换催化剂,按其性能可分为两大类:一类为适用于高压(约8.0mpa)耐硫变换催化剂(co-mo/mgo-al2o3);另一类为适用于低压(≦3.0mpa)的耐硫变换催化剂(co-mo-k/al2o3)。前者主要用于大型煤化工、石化厂,后者主要用于中、小型煤化工、石化厂。国外在耐硫变换催化剂研制方面起步较早,而且各国竞相研究开发。目前己报道的耐硫变换催化剂的品种和型号较多,但应用较多、影响较广泛的工业耐硫变换催化剂主要有四种。(1)德国巴斯夫(basf)公司1969年开发成功的耐硫变换催化剂——kb11型号;(2)丹麦托普索(topsφe)公司开发的ssk耐硫变换催化剂;(3)日本宇部兴产株式会社研制的c113耐硫变换催化剂;(4)美国uci公司开发的新一代c25-2-02耐硫变换催化剂。早期,国外公司产品在国内使用广泛,尤其是前两者;但近年来随着国内耐硫变换催化剂及应用工艺技术的不断发展,加上技术服务和价格上的优势逐渐取代了国外产品。国内于20世纪70年代开始进行耐硫变换催化剂的研制工作经过多年的努力,我国耐硫变换催化剂的开发已取得了较大成就,其主要品牌的催化剂具有活性高、寿命长、强度高、变换炉阻力小、起活温度低等优点,不但成功替代国外同类产品,而且部分产品已进入国际市场。
4.但是,目前耐硫变换催化剂制备方法中有三个方面需要注意,一是采用沉淀法的会产生大量废水排放,对环保日益严格的政策下会增加企业运营成本和环境保压力;二是采用氧化铝载体浸渍镁、钛等改性工艺时由于载体吸水率及改性盐溶解度问题使浸渍上镁含量较低,而且容易排放有害的no
x
等;三是采用捏合法制备时采用多次焙烧或一次的高温焙烧导致能耗较高,不论是电热源还是天然气热源都会增加碳排放,不符合今后碳减排政策。
5.中国专利cn103596682a公开了一种用碱沉淀法制备耐硫变换催化剂,其制备过程复杂,有大量废水排放。中国专利cn105251512 a公开了一种以钴镁铝类水滑石为前驱物的变换催化剂及其制备方法,其先采用可溶性钴盐、铝盐、镁盐与碱共沉淀制备钴镁铝类水滑
石为载体,过程较为复杂,要洗涤产生废水,且载体要高温600℃~750℃焙烧,之后制备催化剂还要400℃~500℃焙烧。中国专利cn101342491a公开了一种球形高压耐硫变换催化剂的制备,该催化剂载体采用α-氧化铝浸渍硝酸镁再经600℃~900℃高温焙烧,能耗高、有害废气排放大。中国专利cn1205114c公开的一种不含钾的一氧化碳变换催化剂的制备方法,采用镁、铝粉体原料捏合后经过高温700℃~900℃焙烧制得载体,再过量浸渍活性组分不但浸渍时间长还要分离回收效率低。中国专利cn107362806b公开了一种等温耐硫变换催化剂及其制备方法,该催化剂采用镁、铝粉体捏合法先制备载体,再浸渍活性组分,但制备过程经过了三次干燥和焙烧,增加了工序和能耗。中国专利cn101695662a公开了一种co耐硫变换催化剂及其制备方法,该法是将天然菱镁矿作为镁源,将其高温(750-800℃)焙烧处理,再将载体(铝源)和菱镁矿分散剂混合处理后再加入钼钴及助剂捏合、挤条成型焙烧(450~600℃)。天然镁源处理为高温焙烧,后续催化剂焙烧温度也较高。中国专利cn110841652a公开了一种孔隙率高的耐硫变换催化剂及其制备方法,该法首先将镁、铝等粉体与造孔物质捏合后于500~650℃焙烧后再加入载体混捏后于500~600℃焙烧成型,最后浸渍活性组分干燥或焙烧。因此,该法虽用捏合法但较高温度下焙烧至少2次,能耗也是偏高。
技术实现要素:6.为了克服上述问题,避免高能耗、高排放,本发明的目的在于提供一种节能环保的制备耐硫变换催化剂的方法,全过程只需要经一步较高温度焙烧即可得到含铝酸镁载体的一氧化碳耐硫变换催化剂,节能环保,且制备所得催化剂机械强度好,同时在中、高压环境下低温、高温活性较好。
7.为了解决上述技术问题,本发明采用以下技术方案:
8.提供一种节能环保的制备耐硫变换催化剂的方法,具体包括以下步骤:
9.1)将一定量的镁化合物粉体和铝化合物粉体混合均匀得混合粉体;
10.2)分别将一定量酸溶液和钼盐溶液加入步骤1)所得混合粉体中,充分捏合;然后在120~200℃温度下低温热处理,得到含钼载体前驱物;
11.3)将步骤2)载体前驱物进行粉碎,加入助剂、钴盐溶液进行捏合,挤条成型,干燥后在300~500℃温度下焙烧得到耐硫变换催化剂。
12.按上述方案,所述步骤1)中,镁化合物粉体为活性mg(oh)2、mgo中的至少一种,所述的铝化合物粉体为拟薄水铝石或氢氧化铝干胶粉。
13.按上述方案,所述步骤1)中,镁化合物中镁、铝化合物中铝的质量比以氧化物计,mgo:al2o3为1:5~1:2。
14.按上述方案,所述步骤2)中,在160-200℃温度下低温热处理,优选为170-190℃。
15.按上述方案,所述步骤2)中,酸溶液为硝酸、乙酸、柠檬酸或其中两者的混合物配成水溶液,酸总质量为步骤1)所得混合粉体质量的2~8%。
16.按上述方案,所述步骤2)中,钼盐为钼酸铵;所述步骤3)中,钴盐为硝酸钴、草酸钴或醋酸钴。
17.按上述方案,所述步骤2)中,钼盐以moo3计质量占所得催化剂质量的7~12%;所述步骤3)中,钴盐以coo计质量占所得催化剂质量的1~5%。
18.按上述方案,所述步骤2)中,低温处理时间为3~4小时。
19.按上述方案,所述步骤3)中,粉碎是将含钼载体前驱物粉碎至粒度为(d50)为8-30μm,优选为8~18μm。
20.按上述方案,所述步骤3)中,助剂为甲基纤维素或聚丙烯酰胺,质量为步骤1)所得混合粉体质量的3~6%。
21.按上述方案,所述步骤3)中,焙烧温度为400-500℃。
22.按上述方案,所述步骤3)中,焙烧时间为2~4小时。
23.本发明的有益效果为:
24.1.本发明提供一种节能环保的制备耐硫变换催化剂的方法,以mo、co为活性组分,首先将钼盐加入镁、铝化合物粉体中捏合后经低温热处理,促进镁、铝固相反应,形成钼促进的mg-al-o化合物前驱体,使后续加入钴盐捏合焙烧后更易形成铝酸镁,所得催化剂具有更好的机械强度和变换活性;全过程只需要经过一步较高温度(300~500℃)焙烧即可得到含铝酸镁载体的一氧化碳耐硫变换催化剂,该催化剂机械强度好,且在中、高压环境下低温、高温活性较好。
25.2.本发明制备催化剂全过程工艺简单,只用一次焙烧,节约能耗减少碳排放,没有废水排放,绿色环保,并且所制备的催化剂机械强度好、一氧化碳变换活性好,具有广泛的应用前景。
具体实施方式
26.以下通过具体实施例对本发明做进一步的解释说明。
27.实施例1
28.提供一种节能环保的制备耐硫变换催化剂的方法,包括以下步骤:
29.取23g氧化镁,70g拟薄水铝石混合均匀后分别加入33g质量百分含量为6%的硝酸溶液、含7克钼酸铵的溶液及适量水在捏合机上进行充分捏合,然后再140℃低温热处理4小时得到含钼的镁铝前驱物,然后将其粉碎到d50为10~14μm,再加入甲基纤维素4.5g,含5g硝酸钴的溶液捏合挤条成型,最后烘干,于440℃焙烧3小时得到中高压耐硫变换催化剂。
30.实施例2
31.方法同实施例1,不同的是将得到的含钼的镁铝前驱物在160℃低温热处理4小时。
32.实施例3
33.方法同实施例1,不同的是将得到的含钼的镁铝前驱物在180℃低温热处理4小时。
34.实施例4
35.方法同实施例3,不同的是将硝酸钴的质量调整为8g。
36.实施例5
37.方法同实施例3,不同的是将180℃低温热处理的含钼的镁铝前驱物粉碎至粒度为(d50):25~30μm。
38.实施例6
39.方法同实施列3,不同的是将180℃低温热处理的含钼的镁铝前驱物粉碎至粒度为(d50):8~10μm。
40.对比例1
41.提供一种耐硫变换催化剂的制备方法,包括以下步骤:
42.取23g氧化镁,70g拟薄水铝石混合均匀后分别加入33g质量百分含量为6%的硝酸溶液及适量水在捏合机上进行充分捏合,再将得到的镁、铝混合物180℃低温热处理4小时,然后将其粉碎到d50为10~14μm,再加入甲基纤维素4.5g、含7克钼酸铵的溶液、含5g硝酸钴的溶液捏合挤条成型,最后烘干于440℃焙烧3小时得到耐硫变换催化剂。
43.与实施例3进行对比,考察钼先后加入镁、铝粉体捏合的影响。
44.将实施例1-6和对比例1制备所得耐硫变换催化剂经机械强度测试后进行一氧化碳水气变换活性测试,测试前经强制快速硫化对催化剂进行4h硫化。其中活性测试条件为:低温(220℃)测试气源:co:2.5%、co2:41%、h2:56%、h2s:200ppm,余n2,水气比0.45,压力4.0mpa,空速3000h-1
。高温(320℃)测试气源为:co:45%、co2:5%、h2:40%、h2s:200ppm其余n2,水气比1.0,压力4.0mpa,空速3000h-1
。活性以原料气中一氧化碳转化率计算。
45.实施例1-6和对比例1制备所得耐硫变换催化剂的机械强度和活性测试结果见表1。
46.表1.实施例1-6和对比例1制备所得催化剂的机械强度及活性
[0047][0048]
表1中可知,与对比例1相比,实施例1-6所得催化剂的机械强度和变换活性均较好,其中前驱体低温热处理的温度高些时,性能更佳,同时前驱物的粉碎粒度较小时有利于催化剂的机械强度与活性。
[0049]
以上仅为本发明的较佳实施例而已,并不用以限制本发明,凡在本发明的精神和原则之内,所作的任何修改、等同替换、改进等,均应包含在本发明的保护范围之内。