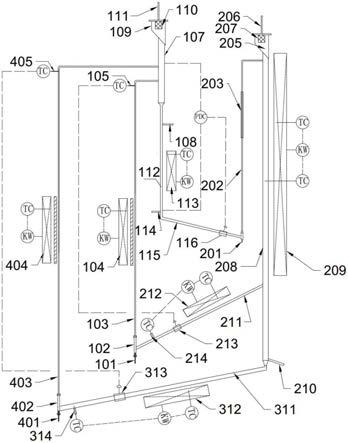
1.本实用新型涉及石油化工领域的一种催化剂连续循环的气固催化反应实验装置,特别是一种双反应器的催化剂连续循环反应实验装置。
背景技术:2.催化裂化是重质油轻质化的一个重要手段。催化裂化工艺是影响催化裂化装置产品分布的一个重要因素。目前实验室的小型提升管装置基本都是常规提升管型式,其主要作用是催化裂化催化剂的性能评价和原料油的评价,基本不具有工艺实验的能力。已有实验室提升管装置不具备催化剂循环量的测量功能,只能根据反应热平衡计算,误差大。工业催化裂化装置是绝热反应,现在的实验室提升管装置,加热炉直接给提升管反应器加热,做不到绝热反应,这使得催化剂循环量的计算误差更大;由于实验装置进料量很小,装置散热量大,仅仅通过保温很难实现真实反应热过程,导致实验数据偏差。
技术实现要素:3.本实用新型的目的在于克服常规提升管实验装置存在的不足之处,提供一种双反应器的催化剂连续循环反应实验装置。
4.本实用新型提出了一种双反应器的催化剂连续循环反应实验装置,
5.设有反应器a、反应器b、汽提器、再生器a和一个或多个再生催化剂供剂管;所述汽提器顶部设置汽提沉降器,底部设置待生催化剂供剂管a;所述再生器a顶部设置再生沉降器a,底部设置再生催化剂供剂管a;所述再生催化剂供剂管a与反应器a下部连通,反应器a出口与汽提器或汽提沉降器连通,反应器b出口与汽提器或汽提沉降器连通;
6.装置设置有待生催化剂输送管a(或称输送管a),所述待生催化剂输送管a入口与待生催化剂供剂管a连通,出口与再生器a或再生沉降器a连通,汽提器汽提后的待生催化剂经待生催化剂输送管a输送到再生器a;反应器b下部通过再生催化剂供剂管b连通再生器a底部,相互连通实现催化剂分别在反应器、反应器b和再生器a间的连续循环;在待生催化剂输送管a上设置催化剂循环量计量单元a;
7.在反应器a、反应器b、汽提器、待生催化剂供剂管a、再生器a和各个再生催化剂供剂管外部(外壁或外侧)设置有加热炉、隔热和补热加热炉或保温层。本实用新型所述再生催化剂是指来自实验装置称为“再生器”的催化剂,其离开再生器的催化剂的含碳量和/或温度可以不同。本实用新型通过控制再生器a内的再生温度和进入再生器a的空气量或进入再生器a的气体含氧量控制进入反应器的催化剂或流出再生器a的催化剂含碳量;通过控制再生催化剂供剂管内催化剂的温度控制进入反应器的催化剂的温度。在具体实施时,本实用新型在各反应器入口安装进料喷嘴;进料喷嘴设反应物进料管和雾化蒸汽进料管,在汽提沉降器顶部设油气出口,反应产物和汽提介质从该出口流出;再生器底部设烧焦气体入口管,再生器顶部设烟气出口。在具体的一个实施例中,反应器a和反应器b采用提升管形式。
8.上述的双反应器的催化剂连续循环反应实验装置,优选地,所述加热炉设置有加热炉丝和外部保温层;
9.所述隔热和补热加热炉,设置有内部隔热层、加热炉丝和外部保温层;
10.所述温度控制器包括温度热电偶(或称温度测量热电偶)和加热炉丝功率控制器;所述功率控制器设置于加热炉丝线路上,所述温度热电偶信号反馈到功率控制器,功率控制器调节加热炉丝的功率实现温度控制。本实用新型在具体实施时,在再生催化剂供剂管和待生催化剂供剂管上设置阀门,或塞阀或滑阀,控制催化剂的循环量;反应器温度热电偶的反应温度信号进入到控制器,控制器控制再生催化剂供剂管上的阀门调节催化剂循环量实现反应温度控制。
11.上述的双反应器的催化剂连续循环反应实验装置,优选地,在再生器a和各再生催化剂供剂管外部设置或分段设置加热炉,分别向再生器a和再生催化剂供剂管内的催化剂供热;分别在再生器a和再生催化剂供剂管的内、外侧设置或分段设置温度热电偶。本实用新型在实施时,由于实验装置进料量小,散热热损失大,反应生焦氧化再生提供的热量不能满足反应对热量要求,通过再生器外补热的方法实现对再生器补热,实现对再生温度的控制。具体实施时,在再生器a外侧分段设加热炉,供电后转化成热量向再生器a内的催化剂供热;同时在加热炉丝供电线路设置功率控制器,调节供电功率实现加热炉丝的供热量,控制再生器a内的温度;在加热炉丝在再生器a外形成的高温区和再生器a内设温度热电偶;所述再生器a外加热炉丝供电功率按加热炉丝在再生器a外形成的高温区温度调节或按设定功率调节。同样地,具体实施时,在再生催化剂供剂管外侧设加热炉或分段设加热炉,加热炉丝供电实现催化剂供剂管外升温,控制再生催化剂供剂管内催化剂的温度;在再生催化剂供剂管内、外设温度热电偶,再生催化剂供剂管外加热炉丝供电功率按加热炉丝在再生催化剂供剂管外形成的高温区温度调节或按设定功率调节。本实用新型中,还可在汽提器外分段设加热炉,供电后转化成热量向汽提器内的催化剂供热;加热炉丝供电线路设置功率控制器,调节供电功率实现加热炉丝的供热量,控制汽提器内的温度;在所述加热炉丝在汽提器外形成的高温区和汽提器内设温度热电偶;所述汽提器外加热炉丝供电功率按加热炉丝在汽提器外形成的高温区温度调节或按设定功率调节。
12.上述的双反应器的催化剂连续循环反应实验装置,优选地,所述反应器a或/和反应器b设计成可分段拆卸结构,各反应段通过法兰或螺纹实现反应器分段拆分和更换;各反应段直径相同或不同。
13.上述的双反应器的催化剂连续循环反应实验装置,优选地,在反应器a和反应器b外壁外侧设置或分段设置隔热和补热加热炉,同时在相应反应器内和反应器外侧加热炉丝区域设置或分段设置温度热电偶。本实用新型中,在反应器壁外设隔热和补热加热炉,给加热炉丝供电后转化成热量提高反应器外的温度,实现反应器外和反应器内温度差的控制;通过反应器外补热使反应器外温度和反应器内温度相同或接近,限制反应器向外散热或向内传热,实现真实的反应和催化剂供热的热平衡或实现反应器外壁绝热;具体实施时,在加热炉丝供电线路设置功率控制器,调节供电功率实现加热炉丝的供热量,控制反应器外的温度;反应器内和反应器外加热炉丝区设温度热电偶。
14.上述的双反应器的催化剂连续循环反应实验装置,优选地,设置再生器b和待生催化剂输送管b(或称输送管b),再生器b设有再生沉降器b,汽提器底部设置待生催化剂供剂
管b;
15.所述反应器b下部通过再生催化剂供剂管b311连通再生器b底部;所述待生催化剂输送管b入口与待生催化剂供剂管b连通,出口与再生器b或再生沉降器b连通,相互连通实现催化剂分别在反应器a、反应器b和再生器a、再生器b间的连续循环,再生催化剂供剂管a向反应器a提供催化剂,再生催化剂供剂管b向反应器b提供催化剂,在待生催化剂输送管b上设置催化剂循环量计量单元b;
16.在再生器b和待生催化剂供剂管b外侧设置保温层或加热炉。在具体实施时,装置设置两个再生器,分别与两个再生催化剂供剂管连通,向两个反应器提供催化剂;实验装置在汽提器和两个再生器间各设置一个待生催化剂输送管,汽提器设有两个待生催化剂供剂管,分别与两个待生催化剂输送管连通,实现待生催化剂向两个再生器输送,进而实现两个再生器和两个反应器、一个汽提器间的催化剂循环,在两个待生催化剂输送管上各设置催化剂循环量计量单元进行催化剂循环量控制。
17.上述的双反应器的催化剂连续循环反应实验装置,优选地,所述催化剂循环量计量单元a或催化剂循环量计量单元b,包括对应设置于待生催化剂输送管a或待生催化剂输送管b外部的冷却管,所述冷却管和待生催化剂输送管a或待生催化剂输送管b形成内外套管或环管结构,冷却管和待生催化剂输送管a或待生催化剂输送管b间的环隙构成冷却介质通道;冷却管两端分别设置冷却介质入口管和冷却介质出口管;所述冷却管外设保温层;
18.在待生催化剂输送管a或待生催化剂输送管b上设置下部入口催化剂温度热电偶和上部出口催化剂温度热电偶,入口催化剂温度热电偶和出口催化剂温度热电偶分别位于冷却管的底端和顶端;在冷却管的底端或冷却介质出口管上设置冷却介质出口温度热电偶,在冷却管的顶端或冷却介质入口管上设置冷却介质入口温度热电偶。
19.上述的双反应器的催化剂连续循环反应实验装置,优选地,所述反应器a和/或反应器b,设置有一个或多个催化剂入口,所述再生器a和/或再生器b设置与上述催化剂入口对应的再生催化剂供剂管,实现再生器a和/或再生器b通过再生催化剂供剂管经催化剂入口向反应器a和/或反应器b提供催化剂。本实用新型,在具体实施时,反应器可按位置上下为两种不同流态化形式串联,上部分设直径扩大段。本实用新型的实验装置中,需要说明的是,再生器可设置一个或多个催化剂出口,分别与再生催化剂供剂管连通,向两个反应器提供催化剂,在具体的实施过程中,再生催化剂供剂管优选设置1~4个,这些再生催化剂供剂管可同时连通一个再生器,或者其中一个连通再生器a,其余的连通再生器b,形成催化剂在反应器和再生器间的一路或多路循环。
20.上述的双反应器的催化剂连续循环反应实验装置,优选地,控制再生器a或再生器b的再生温度和进入空气量或气体含氧量控制进入反应器a和/或反应器b的催化剂含碳量,控制再生催化剂供剂管a和再生催化剂供剂管b内催化剂的温度控制进入反应器a和/或反应器b的催化剂的温度。
21.实用新型效果
22.本实用新型的两个反应器可以实现不同原料的分别反应;本实用新型具有催化剂循环量计量单元,可以更为准确的测量出催化剂的循环量,增加实验的可靠性和对工业催化裂化操作的指导性;本实用新型通过对反应区加热炉的特殊设计,可以实现绝热反应,使得反应结果更可靠。通过对再生催化剂供剂管加热炉功率的控制灵活调整进入反应区域的
再生催化剂的温度。
附图说明
23.图1:本实用新型的设置单再生器的实验装置结构示意图;
24.图2:本实用新型的设置两个再生器的实验装置结构示意图;
25.图3:图1中再生器a设置的加热炉结构示意图;
26.图4:图1中反应器a设置的隔热和补热加热炉具体结构示意图;
27.图5:图1中催化剂循环量计量单元a结构示意图。
28.附图符号说明:
29.101
‑
进料喷嘴,102
‑
预提升段,103
‑
反应器a,104
‑
提升管a隔热和补热加热炉,105
‑
提升管a出口温度热电偶,107汽提器扩径区,108汽提器温度热电偶,109
‑
汽提沉降器,110
‑
汽提沉降器过滤器,111
‑
油气出口,112
‑
汽提器,113汽提器加热炉,114
‑
汽提蒸汽入口,115
‑
待生催化剂供剂管a,116
‑
待生催化剂供剂管a塞阀或滑阀,117
‑
待生催化剂供剂管b,118
‑
待生催化剂供剂管b塞阀或滑阀,201
‑
输送风入口a,202
‑
待生催化剂输送管a,203
‑
催化剂循环量计量单元a,205
‑
再生沉降器a,206
‑
再生沉降器a气体出口,207
‑
再生沉降器a过滤器,208
‑
再生器a,209
‑
再生器a加热炉,210
‑
再生器a空气入口,211
‑
再生催化剂供剂管a,212
‑
再生催化剂供剂管a加热炉,213
‑
再生催化剂供剂管a塞阀或滑阀,214
‑
再生催化剂供剂管a返剂温度热电偶,301
‑
输送风入口b,302
‑
待生催化剂输送管b,303
‑
催化剂循环量计量单元b,305
‑
再生沉降器b,306
‑
再生沉降器b出口,307
‑
再生沉降器b过滤器,308
‑
再生器b,309
‑
再生器b加热炉,310
‑
再生器b空气入口,311
‑
再生催化剂供剂管b,312
‑
再生催化剂供剂管b加热炉,313
‑
再生催化剂供剂管b塞阀或滑阀,314
‑
再生催化剂供剂管b返剂温度热电偶,401
‑
进料喷嘴,402
‑
预提升段,403
‑
反应器b,404
‑
提升管b隔热和补热加热炉,405
‑
提升管b出口温度热电偶,502
‑
入口催化剂温度热电偶,503
‑
出口催化剂温度热电偶,504
‑
冷却介质入口,505
‑
冷却介质出口,506
‑
冷却介质入口温度热电偶,507
‑
冷却介质出口温度热电偶,508
‑
冷却管,509
‑
保温层,601
‑
设备管壁,602
‑
隔热层,603
‑
加热炉丝或电加炉丝,604
‑
绝缘碗珠,605
‑
保温层,606
‑
炉子隔热外壳,tc温度控制信号(温度显示),kw功率控制信号,ti温度显示。
具体实施方式
30.下面结合附图和具体实施方式对本实用新型作进一步详细说明。附图和具体实施方式并不限制本实用新型要求保护的范围。
31.如图1所示,一种双反应器的催化剂连续循环反应实验装置,设有反应器a103、反应器b403、汽提器112和再生器a208;在汽提器112上部的汽提器扩径区107顶部设置汽提沉降器109,底部设置待生催化剂供剂管a115,待生催化剂供剂管a115设置待生催化剂供剂管a塞阀或滑阀116,汽提沉降器109设置有汽提沉降器过滤器110和油气出口111,汽提器112下部设汽提蒸汽入口114,反应器的反应产物和汽提介质(如蒸汽)经汽提沉降器过滤器110从油气出口111流出;在再生器a208顶部设置再生沉降器a205,底部设置再生催化剂供剂管a211、再生催化剂供剂管b311和再生器a空气入口210,再生沉降器a205设有再生沉降器a过滤器207和再生沉降器a气体出口206,含氧空气进入再生器a208进行烧焦实现催化剂再生,
再生烟气经再生沉降器a过滤器207从再生沉降器a气体出口206流出,在再生催化剂供剂管a211上设置再生催化剂供剂管a塞阀或滑阀213,在再生催化剂供剂管b311上设置再生催化剂供剂管b塞阀或滑阀313;再生催化剂供剂管a211与反应器a103底部的预提升段a102连通,在预提升段a102入口安装进料喷嘴a101,在反应器a103出口设置反应器a出口温度热电偶105,再生催化剂供剂管b311与反应器b403底部的预提升段b402连通,在预提升段b402入口安装进料喷嘴b401,在反应器b403出口设置反应器b出口温度热电偶405,反应器a103出口和反应器b403出口均与汽提器112的汽提器扩径区107连通;再生器a208与待生催化剂供剂管a115通过待生催化剂输送管a202连通,待生催化剂输送管a202底部设有输送风入口a201,待生催化剂输送管a202出口连通再生器a208上部,汽提器112汽提后的待生催化剂进入待生催化剂输送管a202,由输送风入口a201引入的输送风输送到再生器a208,从而相互连通实现催化剂分别在反应器a103、反应器b403和再生器a208间的连续循环;
32.具体实施时,在待生催化剂输送管a202上设置催化剂循环量计量单元a203,如图5所示,催化剂循环量计量单元a203,包括设置于待生催化剂输送管a202外部的冷却管508,冷却管508和待生催化剂输送管a202形成内外套管或环管结构,冷却管508和待生催化剂输送管a202间的环隙构成冷却介质通道;冷却管508两端分别设置冷却介质入口504和冷却介质出口505;在冷却管508外设保温层509;在待生催化剂输送管a202上设置下部的入口催化剂温度热电偶502和上部的出口催化剂温度热电偶503,入口催化剂温度热电偶502和出口催化剂温度热电偶503分别位于冷却管508的底端和顶端;在冷却介质出口505上设置冷却介质出口温度热电偶507,在冷却介质入口504上设置冷却介质入口温度热电偶506;关于催化剂循环量计量单元的具体结构,以下实施方式类同,不再赘述;
33.具体实施时,本实用新型的实验装置中,分别在汽提器112、再生器a208、再生催化剂供剂管a211和再生催化剂供剂管b311外侧设置加热炉,即分别设置汽提器加热炉113、再生器a加热炉209、再生催化剂供剂管a加热炉212和再生催化剂供剂管b加热炉312。再生器a加热炉209的结构如图3所示,再生器a加热炉209设置于再生器a208的设备管壁601外侧,由加热炉丝603和外部保温层605组成,加热炉丝603外套装绝缘碗珠604,保温层605在加热炉丝603外围,保温层605套装炉子隔热外壳606;汽提器加热炉113、再生催化剂供剂管a加热炉212和再生催化剂供剂管b加热炉312,结构同再生器a加热炉209,关于加热炉的具体构造,其他实施例方式类同,不再赘述;
34.在反应器a103外侧设置提升管a隔热和补热加热炉104,在反应器b403外侧设置提升管b隔热和补热加热炉404,提升管a隔热和补热加热炉104结构如图4所示,反应器a隔热和补热加热炉104设置于反应器a103的设备管壁601外侧,由内部隔热层602、加热炉丝603和外部保温层605组成,加热炉丝603外套装绝缘碗珠604,保温层605在加热炉丝603外围,保温层605套装炉子隔热外壳606;反应器b4隔热和补热加热炉404,结构同提升管a隔热和补热加热炉104,关于隔热和补热加热炉,其他实施例方式类同,不再赘述;
35.具体实施时,如图1所示,前述的加热炉或隔热和补热加热炉,在加热炉丝线路上设置功率控制器,在再生器a208壁外加热炉丝形成的高温区和再生器a208内设温度热电偶,在再生催化剂供剂管a211内、外侧设置再生催化剂供剂管a返剂温度热电偶214,在再生催化剂供剂管b311内、外侧设置再生催化剂供剂管b返剂温度热电偶314,在反应器a103壁外加热炉丝形成的高温区和反应器a103内设温度热电偶,在反应器b403壁外加热炉丝形成
的高温区和反应器b403内设温度热电偶,在汽提器113壁外加热炉丝形成的高温区和汽提器113内设温度热电偶,以及反应器a出口温度热电偶105、反应器b出口温度热电偶405和催化剂循环量计量单元a203的各温度热电偶,每个温度热电偶均与功率控制器连接,构成对实验装置的温度控制系统;装置工作时,各温度热电偶的温度信号反馈或输送到功率控制器,功率控制器调节加热炉丝的加热功率,实现对进入装置反应再生部分各部件的催化剂的温度控制,譬如对进入再生器a208、再生催化剂供剂管a211、再生催化剂供剂管b311及在催化剂循环量计量单元内催化剂的温度控制。
36.图2所示的双反应器的催化剂连续循环反应实验装置,还设置有再生器b308和待生催化剂输送管b302,再生器b308设有再生沉降器b305,汽提器112底部设有两个待生催化剂供剂管即待生催化剂供剂管a115和待生催化剂供剂管b117,反应器b403下部的预提升段b402通过再生催化剂供剂管b311连通再生器b308底部;待生催化剂输送管b302入口与待生催化剂供剂管b117连通,出口与再生器b308连通,其他部分装置结构同图1,装置各部分相互连通实现催化剂分别在反应器a103、反应器b403和再生器a208、再生器b308间的连续循环,再生催化剂供剂管a211向反应器a103提供催化剂,再生催化剂供剂管b311向反应器b403提供催化剂,在待生催化剂输送管b302上设置催化剂循环量计量单元b303;在再生器b308外侧设置再生器a加热炉309。本实验装置具体工作时,汽提器112底部设有两个待生催化剂供剂管,一部分待生催化剂通过待生催化剂供剂管a115经待生催化剂供剂管a塞阀或滑阀116进入待生催化剂输送管a202底部,输送到再生器a208,再生催化剂通过再生催化剂供剂管a211经再生催化剂供剂管a塞阀或滑阀a213进入到反应器a103的预提升段a102,与从喷嘴a101进入的原料油接触,一起向上输送反应;另一部分待生催化剂通过待生催化剂供剂管b117经待生催化剂供剂管b塞阀或滑阀118进入待生催化剂输送管b302底部,输送到再生器b308,再生催化剂通过再生催化剂供剂管b311经再生催化剂供剂管b塞阀或滑阀a313进入到反应器b403的预提升段b402参与反应,反应结束后,催化剂与反应产物等进入汽提器112,完成油气与催化剂的分离,油气向上进入汽提沉降器109,经汽提器过滤器110过滤掉大于10
‑
30微米的催化剂后,从汽提沉降器109顶部的油气出口111离开进入后面的油气处理单元。待生催化剂则经过两个待生催化剂供剂管分别进入再生器a208和再生器b308,完成烧焦再生,继续经相应的再生催化剂供剂管进入各反应器,参与反应,实现连续循环反应。
37.实施例:
38.反应物进料量1.3kg/h,反应器a和反应器b采用提升管反应器,两反应器为等径形式,设一个再生器a;反应沉降器操作压力130kpa(表压);再生温度700℃;进入反应器a的再生催化剂温度680℃,进入反应器b的再生催化剂温度700℃;
39.反应器a内径15mm,长5000mm;反应器b内径10mm,长3000mm,再生器a内径60mm,高度3000mm;汽提器内径60mm,高3000mm;再生催化剂供剂管a内径15mm;再生催化剂供剂管b内径12mm;待生催化剂供剂管a内径15mm;待生催化剂输送管a内径10mm,外径14mm,冷却管内径20mm;
40.两提升管外侧全部设厚度10mm的隔热层,隔热层材料导热系数0.1;隔热层外分三段设外侧隔热和补热加热炉丝,每段最大功率1.8kw,使用功率可调;
41.再生器a外设三段加热炉丝,每段最大功率2.0kw,使用功率可调;汽提器设两段加
热炉丝,每段最大功率2.0kw,实际使用功率可调;两个再生催化剂供剂管分别设一段加热炉丝,功率2.0kw,实际使用功率可调;
42.加热炉丝采用220伏特电压供电。
43.各设备外设80mm厚保温层。
44.汽提蒸汽温度350℃,蒸汽量8g/min;再生器烧焦空气20l/min;
45.本实施例中,反应器的整体材质为316l,设计温度700℃;再生器材质310s,设计温度800℃;装置设计压力0.6mpa。