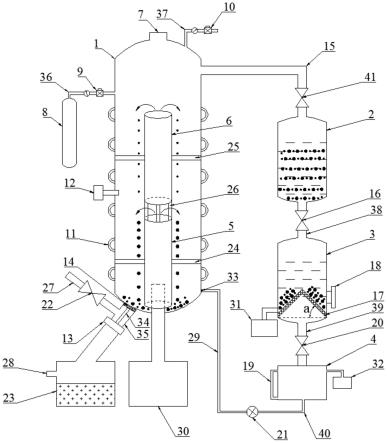
1.本发明涉及催化剂再生技术领域,尤其涉及一种重油加氢裂化催化剂再生装置及方法。
背景技术:2.重油加氢裂化催化剂经过使用后,除了携带少量油分之外,其表面和空隙内部还会沉积附着较多的焦碳类物质,焦碳类物质中含有使得催化剂中毒的重金属,导致催化剂性能下降甚至失活。
3.将使用后的重油加氢裂化催化剂上的油分和焦碳类物质去除,实现重油加氢裂化催化剂的再生,能够提高经济效益。由于焦碳类物质覆盖致密,难以去除,现有的重油加氢裂化催化剂再生方式一般是采用通入空气或贫氧空气进行焦碳类物质的烧焦、采用某些溶剂洗涤等方法,然而,现有的重油加氢裂化催化剂再生方式对焦碳类物质的处理效果不好,处理后的催化剂上残留较多的焦炭中的金属成分。
技术实现要素:4.本发明提供一种重油加氢裂化催化剂再生装置及方法,以解决现有重油加氢裂化催化剂再生方式对焦碳类物质的处理效果不好,处理后的催化剂上残留较多的焦炭中的金属成分的问题。
5.为了实现上述目的,本发明提供一种重油加氢裂化催化剂再生装置,包括超声处理塔,超声处理塔的底部中央固定安装超声波发生器,超声处理塔的底部一侧固定安装过渡管,过渡管的上端安装催化剂筛网,过渡管的中部连接外排水汽管,外排水汽管上安装外排水汽阀,过渡管的下端与催化剂卸料盖螺纹连接,催化剂卸料盖的上端通过连杆与催化剂筛网连接,催化剂卸料盖的下端盖在催化剂活化塔上,催化剂活化塔上设置氢气入口,超声处理塔的内部由下到上依次安装一级导流筒、第三支撑杆和二级导流筒,一级导流筒的上端与第三支撑杆固定连接,第三支撑杆的上端与二级导流筒固定连接,超声处理塔上固定安装热电偶,超声处理塔的外壁上安装电磁加热线圈,超声处理塔的顶部中央设置废催化剂进料斗,超声处理塔的上端通过氮气管与高压氮气罐连接,氮气管上安装减压阀和压力表,超声处理塔的上端连接外排气管,外排气管上安装背压阀和压力表,超声处理塔通过油焦水溢出管与油焦储罐连接,油焦水溢出管上设置截止阀。
6.在上述的重油加氢裂化催化剂再生装置中,可选的是,油焦储罐的下端通过第一连接管与固液分离罐连接,固液分离罐的下端通过第二连接管与油水分离罐连接,固液分离罐的底部安装焦碳过滤筛网,第一连接管上设置第二减压阀,第二连接管上设置排水阀。
7.在上述的重油加氢裂化催化剂再生装置中,可选的是,油水分离罐的上部连接储油罐。
8.在上述的重油加氢裂化催化剂再生装置中,可选的是,油水分离罐的底部连接出水管,出水管连接水泵,水泵连接进水管,进水管连接超声处理塔的底部入水口,超声处理
塔的底部入水口处设置进水管筛网。
9.在上述的重油加氢裂化催化剂再生装置中,可选的是,油水分离罐的一侧设置液位计。
10.在上述的重油加氢裂化催化剂再生装置中,可选的是,固液分离罐上设置储槽。
11.在上述的重油加氢裂化催化剂再生装置中,可选的是,固液分离罐上设置水力清焦孔。
12.在上述的重油加氢裂化催化剂再生装置中,可选的是,一级导流筒通过第一支撑杆固定在超声处理塔内,一级导流筒的外壁圆周设置第一支撑杆,第一支撑杆的一端固定在超声处理塔的内壁上;二级导流筒通过第二支撑杆固定在超声处理塔内,二级导流筒的外壁圆周设置第二支撑杆,第二支撑杆的一端固定在超声处理塔的内壁上。
13.在上述的重油加氢裂化催化剂再生装置中,可选的是,一级导流筒与二级导流筒之间圆周均布四个第三支撑杆。
14.一种重油加氢裂化催化剂再生方法,包括:
15.步骤一:废催化剂进料,将废催化剂通过废催化剂进料斗加入超声处理塔,通过超声处理塔的底部入水口通入新鲜来水;
16.步骤二:系统压力维持,密闭超声处理塔,通过高压氮气罐和减压阀为超声处理塔提供减压后的惰性气体(氮气)气氛,电磁加热线圈为超声处理塔提供适宜的处理温度(260℃-320℃),热电偶用于测定超声处理塔的温度,利用背压阀维持12mpa左右的高压p1,使超声处理塔中的水处于超临界状态;
17.步骤三:废催化剂超声波处理,废催化剂在超声处理塔底部通过超声波震荡处理,通过超声波震荡将废催化剂颗粒表面及空隙内部附着的焦碳及油分脱除;
18.步骤四:焦碳及油分溢出,经步骤三处理的已经脱除油分和焦碳的催化剂颗粒、不同处理程度的催化剂颗粒以及催化剂分离出来的油相和焦碳等,通过一级导流筒和二级导流筒逐渐向上移动;其中,废催化剂分离出来的油相以及焦碳等通过油焦水溢出管溢出至油焦储罐;较大的催化剂颗粒或没有脱除干净的较重催化剂颗粒在一级导流筒上缘处溢出后逐渐沉降落入超声处理塔底部,再进行进一步超声处理;较小催化剂颗粒通过一级导流筒后进入二级导流筒,最终从二级导流筒的上边缘溢出回落到超声处理塔底部;
19.步骤五:焦碳与油水分离,在关闭截止阀后,油焦储罐中含油含焦碳的液相,经第一连接管上的第二减压阀进入固液分离罐,固液分离罐内保持1mpa-2mpa的压力p2,利用压力p2的作用经过焦碳过滤筛网分离出固体焦碳等,实现液相和固相分离,液相部分通过第二连接管上的排水阀进入油水分离罐;
20.步骤六:油水分离,通过液位计判断油水分离罐内的油水界面,将油水分离罐上部的油相外排至储油罐,将油水分离罐底部的水通过水泵抽入超声处理塔中进行循环使用;
21.步骤七:催化剂排出,废催化剂处理完毕后需要卸料时,停止电磁加热线圈对超声处理塔加热,关闭高压氮气罐防止氮气进入超声处理塔,停止水泵的工作,通过背压阀逐渐降低超声处理塔内的压力;打开外排水汽管上的外排水汽阀,通过外排水汽管排出超声处理塔内的水至废水管道;将催化剂卸料盖从过渡管和催化剂活化塔上取下,通过连杆带动催化剂筛网从过渡管上取下,然后将过渡管的下端对准催化剂活化塔的上方入口,将超声处理塔中处理后的废催化剂卸入催化剂活化塔中;
22.步骤八:催化剂活化还原,通过催化剂卸料盖封堵催化剂活化塔的上方入口,通过氢气入口为卸入催化剂活化塔内的脱除油焦等附着物的催化剂颗粒通入氢气在设定的温度和压力条件下进行加氢还原,使得催化剂颗粒上的被氧化的活性金属还原,重新具备加氢活性。
23.本发明提供的重油加氢裂化催化剂再生装置及方法,利用超临界水的优异特性,将废催化剂表面及孔道内沉积的焦碳及含有的部分油分,进行充分的剥离,在超声波震荡条件下,通过一级导流筒和二级导流筒的引流作用,将废催化剂表面的焦碳及含有的部分油分脱除分离,大大减少处理后的催化剂上残留的金属成分,提高对焦碳类物质的处理效果,对脱除油焦等附着物的废催化剂颗粒进行加氢还原,使得催化剂颗粒上的被氧化的活性金属还原,重新具备加氢活性,实现催化剂的再生。
24.本发明的构造以及它的其他发明目的及有益效果将会通过结合附图而对优选实施例的描述而更加明显易懂。
附图说明
25.为了更清楚地说明本发明实施例或现有技术中的技术方案,下面将对实施例或现有技术描述中所需要使用的附图作以简单地介绍,显而易见地,下面描述中的附图是本发明的一些实施例,对于本领域普通技术人员来讲,在不付出创造性劳动的前提下,还可以根据这些附图获得其他的附图。
26.图1为本发明实施例提供的重油加氢裂化催化剂再生装置的结构示意图。
27.附图标记说明:
28.1-超声处理塔;2-油焦储罐;3-固液分离罐;4-油水分离罐;5-一级导流筒;6-二级导流筒;7-废催化剂进料斗;8-高压氮气罐;9-减压阀;10-背压阀;11-电磁加热线圈;12-热电偶;13-催化剂卸料盖;14-催化剂筛网;15-油焦水溢出管;16-第二减压阀;17-焦碳过滤筛网;18-水力清焦孔;19-液位计;20-排水阀;21-水泵;22-外排水汽阀;23-催化剂活化塔;24-第一支撑杆;25-第二支撑杆;26-第三支撑杆;27-外排水汽管;28-氢气入口;29-进水管;30-超声波发生器;31-储槽;32-储油罐;33-进水管筛网;34-连杆;35-过渡管;36-氮气管;37-外排气管;38-第一连接管;39-第二连接管;40-出水管;41-截止阀。
具体实施方式
29.为使本发明的目的、技术方案和优点更加清楚,下面将结合本发明的优选实施例中的附图,对本发明实施例中的技术方案进行更加详细的描述。在附图中,自始至终相同或类似的标号表示相同或类似的部件或具有相同或类似功能的部件。所描述的实施例是本发明一部分实施例,而不是全部的实施例。下面通过参考附图描述的实施例是示例性的,旨在用于解释本发明,而不能理解为对本发明的限制。基于本发明中的实施例,本领域普通技术人员在没有作出创造性劳动前提下所获得的所有其他实施例,都属于本发明保护的范围。下面结合附图对本发明的实施例进行详细说明。
30.如图1所示,本发明提供一种重油加氢裂化催化剂再生装置,包括超声处理塔1,超声处理塔1的底部中央固定安装超声波发生器30,超声处理塔1的底部一侧固定安装过渡管35,过渡管35的上端安装催化剂筛网14,过渡管35的中部连接外排水汽管27,外排水汽管27
上安装外排水汽阀22,过渡管35的下端与催化剂卸料盖13螺纹连接,催化剂卸料盖13的上端通过连杆34与催化剂筛网14连接,催化剂卸料盖13的下端盖在催化剂活化塔23上,催化剂活化塔23上设置氢气入口28,超声处理塔1的内部由下到上依次安装一级导流筒5、第三支撑杆26和二级导流筒6,一级导流筒5的上端与第三支撑杆26固定连接,第三支撑杆26的上端与二级导流筒6固定连接,超声处理塔1上固定安装热电偶12,超声处理塔1的外壁上安装电磁加热线圈11,超声处理塔1的顶部中央设置废催化剂进料斗7,超声处理塔1的上端通过氮气管36与高压氮气罐8连接,氮气管36上安装减压阀9和压力表,超声处理塔1的上端连接外排气管37,外排气管37上安装背压阀10和压力表,超声处理塔1通过油焦水溢出管15与油焦储罐2连接,油焦水溢出管15上设置截止阀41。
31.需要说明的是,高压氮气罐8为系统提供高压惰性气体(氮气)气氛,成为超临界水处理催化剂;减压阀9将高压氮气减至超声处理塔1所需的压力p1(12mpa左右);电磁加热线圈11为超声处理塔1提供适宜的处理温度(260℃-320℃);热电偶12用于测定超声处理塔1的温度;背压阀10的作用是维持超声处理塔1的压力,具体的,由于加热等原因导致系统压力上升超过设定值p1后,开启背压阀10将多余气体通过外排气管37排出,待系统压力降至设定值p1时关闭背压阀10,高压p1的存在是为了使超声处理塔1中的水处于超临界状态,形成超临界水,利用超临界水的类似于有机溶剂的性质,将废催化剂表面及催化剂孔道内沉积的焦碳及含有的部分油分,进行充分的剥离;超声波发生器30的超声波探头上端深入超声处理塔1的一级导流筒5内,超声波震荡形成的向上的升力以及产生的空泡效应,使得已经脱除油分和焦碳的催化剂颗粒、不同处理程度的催化剂颗粒以及催化剂分离出来的油相和焦碳等通过一级导流筒5和二级导流筒6逐渐向上移动,其中,从废催化剂分离出来的油相以及焦碳等通过油焦水溢出管15上的截止阀41溢出至油焦储罐2;一级导流筒5后和二级导流筒6均为上下两端开口的圆筒状结构,较大的催化剂颗粒或没有脱除干净的较重催化剂颗粒在一级导流筒5上缘处溢出后逐渐沉降落入超声处理塔1底部,再进行进一步超声处理;较小催化剂颗粒通过一级导流筒5后进入二级导流筒6,最终从二级导流筒6的上边缘溢出回落到超声处理塔1底部,由于催化剂颗粒与脱除的焦碳及油分存在着较大的密度差,只有较大体积和密度的少量焦碳会沉降到超声处理塔1底部,并且在超声波处理下破碎成较小颗粒,随导流筒内上升的液流再次上浮,最终从油焦水溢出管15溢出超声处理塔1;催化剂筛网14用于分离催化剂和水分,在卸出催化剂时,将催化剂筛网14从过渡管35内取出。
32.油焦储罐2的下端通过第一连接管38与固液分离罐3连接,固液分离罐3的下端通过第二连接管39与油水分离罐4连接,固液分离罐3的底部安装焦碳过滤筛网17,第一连接管38上设置第二减压阀16,第二连接管39上设置排水阀20。
33.需要说明的是,油焦储罐2中含油含焦碳的液相,经第一连接管38上的第二减压阀16进入固液分离罐3,固液分离罐3内保持1mpa-2mpa的压力p2,利用压力p2的作用经过焦碳过滤筛网17分离出固体焦碳等,实现液相和固相分离,需要说明的是,焦碳过滤筛网17的中心位置向上隆起呈圆锥状,焦碳过滤筛网17的圆锥母线与圆锥底面之间的夹角a为30
°
~60
°
,优选45
°
,圆锥状的焦碳过滤筛网17有利于焦碳先从四周累积形成密实层,导致液相部分难以从焦碳过滤筛网17的四周通过,使得液相部分从焦碳过滤筛网17中心的锥体尖部向下排出,液相部分最终通过第二连接管39上的排水阀20进入油水分离罐4。
34.油水分离罐4的上部连接储油罐32。
35.需要说明的是,油水分离罐4上部的油相外排至储油罐32进行储存。
36.油水分离罐4的底部连接出水管40,出水管40连接水泵21,水泵21连接进水管29,进水管29连接超声处理塔1的底部入水口,超声处理塔1的底部入水口处设置进水管筛网33。
37.需要说明的是,油水分离罐4下部的水通过水泵21吸入超声处理塔1内进行二次利用,提高水资源利用率;超声处理塔1的底部入水口处设置的进水管筛网33有效防止超声处理塔1内的催化剂及焦碳类物质进入进水管29。
38.油水分离罐4的一侧设置液位计19。
39.需要说明的是,通过液位计19判断油水分离罐4内的油水界面。
40.固液分离罐3上设置储槽31。
41.需要说明的是,储槽31用于储存固液分离罐3内排出的物料。
42.固液分离罐3上设置水力清焦孔18。
43.需要说明的是,由于废催化剂脱除的焦碳及某些催化剂粉尘沉积在焦碳过滤筛网17上,经过固液分离罐3内带压过滤处理,本身性状较为坚硬和密实,排出固液分离罐3需要采用高压的水力除焦水枪进行切割和粉碎,处理后的物料随水流至储槽31。
44.一级导流筒5通过第一支撑杆24固定在超声处理塔1内,一级导流筒5的外壁圆周设置第一支撑杆24,第一支撑杆24的一端固定在超声处理塔1的内壁上;二级导流筒6通过第二支撑杆25固定在超声处理塔1内,二级导流筒6的外壁圆周设置第二支撑杆25,第二支撑杆25的一端固定在超声处理塔1的内壁上。
45.需要说明的是,圆周设置的第一支撑杆24增加一级导流筒5的稳定性,圆周设置的第二支撑杆25增加二级导流筒6的稳定性。
46.一级导流筒5与二级导流筒6之间圆周均布四个第三支撑杆26。
47.需要说明的是,一级导流筒5和二级导流筒6之间通过四个第三支撑杆26连接,增加一级导流筒5和二级导流筒6的稳定性,从一级导流筒5上缘溢出的催化剂颗粒通过相邻的第三支撑杆26之间的空隙后进行沉降。
48.一种重油加氢裂化催化剂再生方法,包括:
49.步骤一:废催化剂进料,将废催化剂通过废催化剂进料斗7加入超声处理塔1,通过超声处理塔1的底部入水口通入新鲜来水;
50.步骤二:系统压力维持,密闭超声处理塔1,通过高压氮气罐8和减压阀9为超声处理塔1提供减压后的惰性气体(氮气)气氛,电磁加热线圈11为超声处理塔1提供适宜的处理温度(260℃-320℃),热电偶12用于测定超声处理塔1的温度,利用背压阀10维持12mpa左右的高压p1,使超声处理塔1中的水处于超临界状态;
51.步骤三:废催化剂超声波处理,废催化剂在超声处理塔1底部通过超声波震荡处理,通过超声波震荡将废催化剂颗粒表面及空隙内部附着的焦碳及油分脱除;
52.步骤四:焦碳及油分溢出,经步骤三处理的已经脱除油分和焦碳的催化剂颗粒、不同处理程度的催化剂颗粒以及催化剂分离出来的油相和焦碳等,通过一级导流筒5和二级导流筒6逐渐向上移动;其中,废催化剂分离出来的油相以及焦碳等通过油焦水溢出管15上的截止阀41溢出至油焦储罐2;较大的催化剂颗粒或没有脱除干净的较重催化剂颗粒在一级导流筒5上缘处溢出后逐渐沉降落入超声处理塔1底部,再进行进一步超声处理;较小催
化剂颗粒通过一级导流筒5后进入二级导流筒6,最终从二级导流筒6的上边缘溢出回落到超声处理塔1底部;
53.步骤五:焦碳与油水分离,在关闭截止阀41后,油焦储罐2中含油含焦碳的液相,经第一连接管38上的第二减压阀16进入固液分离罐3,固液分离罐3内保持1mpa-2mpa的压力p2,利用压力p2的作用经过焦碳过滤筛网17分离出固体焦碳等,实现液相和固相分离,液相部分通过第二连接管39上的排水阀20进入油水分离罐4;
54.步骤六:油水分离,通过液位计19判断油水分离罐4内的油水界面,将油水分离罐4上部的油相外排至储油罐32,将油水分离罐4底部的水通过水泵21抽入超声处理塔1中进行循环使用;
55.步骤七:催化剂排出,废催化剂处理完毕后需要卸料时,停止电磁加热线圈11对超声处理塔1加热,关闭高压氮气罐8防止氮气进入超声处理塔1,停止水泵21的工作,通过背压阀10逐渐降低超声处理塔1内的压力;打开外排水汽管27上的外排水汽阀22,通过外排水汽管27排出超声处理塔1内的水至废水管道;将催化剂卸料盖13从过渡管35和催化剂活化塔23上取下,通过连杆34带动催化剂筛网14从过渡管35上取下,然后将过渡管35的下端对准催化剂活化塔23的上方入口,将超声处理塔1中处理后的废催化剂卸入催化剂活化塔23中;
56.步骤八:催化剂活化还原,通过催化剂卸料盖13封堵催化剂活化塔23的上方入口,通过氢气入口28为卸入催化剂活化塔23内的脱除油焦等附着物的催化剂颗粒通入氢气在设定的温度和压力条件下进行加氢还原,使得催化剂颗粒上的被氧化的活性金属还原,重新具备加氢活性。
57.本发明提供的重油加氢裂化催化剂再生装置及方法,利用超临界水的优异特性,将废催化剂表面及孔道内沉积的焦碳及含有的部分油分,进行充分的剥离,在超声波震荡条件下,通过一级导流筒5和二级导流筒6的引流作用,将废催化剂表面的焦碳及含有的部分油分脱除分离,大大减少处理后的催化剂上残留的金属成分,提高对焦碳类物质的处理效果,对脱除油焦等附着物的废催化剂颗粒进行加氢还原,使得催化剂颗粒上的被氧化的活性金属还原,重新具备加氢活性,实现催化剂的再生。
58.在本发明的描述中,需要说明的是,除非另有明确的规定和限定,术语“安装”、“相连”、“连接”应作广义理解,例如,可以使固定连接,也可以是通过中间媒介间接相连,可以是两个元件内部的连通或者两个元件的相互作用关系。对于本领域的普通技术人员而言,可以根据具体情况理解上述术语在本发明中的具体含义。术语“上”、“下”、“前”、“后”、“竖直”、“水平”、“顶”、“底”、“内”、“外”等指示的方位或者位置关系为基于附图所示的方位或位置关系,仅是为了便于描述本发明和简化描述,而不是指示或者暗示所指的装置或者元件必须具有特定的方位、以特定的方位构造和操作,因此不能理解为对本发明的限制。在本发明的描述中,“多个”的含义是两个或两个以上,除非是另有精确具体地规定。
59.本技术的说明书和权利要求书及上述附图中的术语“第一”、“第二”、“第三”、“第四”等(如果存在)是用于区别类似的对象,而不必用于描述特定的顺序或先后次序。应该理解这样使用的数据在适当情况下可以互换,以便这里描述的本技术的实施例例如能够以除了在这里图示或描述的那些以外的顺序实施。此外,术语“包括”和“具有”以及他们的任何变形,意图在于覆盖不排他的包含,例如,包含了一系列步骤或单元的过程、方法、系统、产
品或设备不必限于清楚地列出的那些步骤或单元,而是可包括没有清楚地列出的或对于这些过程、方法、产品或设备固有的其它步骤或单元。
60.最后应说明的是:以上各实施例仅用以说明本发明的技术方案,而非对其限制;尽管参照前述各实施例对本发明进行了详细的说明,本领域的普通技术人员应当理解:其依然可以对前述各实施例所记载的技术方案进行修改,或者对其中部分或者全部技术特征进行等同替换;而这些修改或者替换,并不使相应技术方案的本质脱离本发明各实施例技术方案的范围。