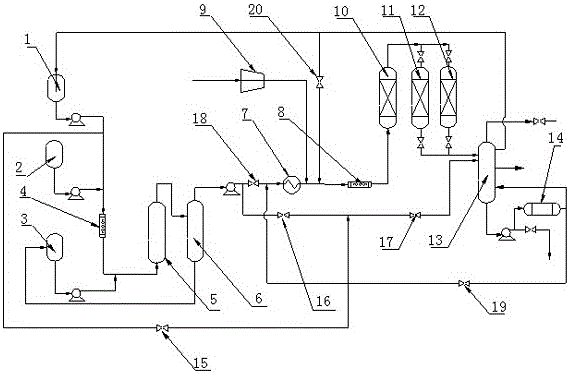
本发明涉及一种烷基化油的脱氯方法,具体地说是将高含氯量的烷基化油通过加氢及脱氯处理进行脱氯,特别适宜于离子液烷基化工艺的生成油。
背景技术:
:烷基化油是一种常见的高辛烷值汽油调和组分,具有辛烷值高、抗爆性能好、蒸气压低、含硫低以及不含烯烃和芳烃等特点,是理想的清洁汽油调合组分。烷基化油一般通过异丁烷与烯烃在酸催化剂的作用下反应生成。烷基化油的技术种类较多,按催化剂的相态划分,可分为液体酸烷基化和固体酸烷基化两大类。液体酸烷基化技术包括氢氟酸、硫酸和离子酸三种;固体酸主要是专用沸石催化剂。目前,液体酸烷基化工艺是最常见的方法,其中离子液烷基化是近年来最新开发的烷基化工艺技术。离子液体具有不挥发、蒸气压接近零、不燃、热稳定性高及液态存在的温度范围宽等优点,被公认为是一种环境友好的体系;因同时具有液体酸高密度的反应活性和固体酸的不挥发性,近年来受到广泛关注。chevron、shell和石油大学等公司和高校对离子液烷基化技术开展了大量研究工作。石油大学开发的离子液烷基化技术于2013年9月在山东德阳化工有限公司建成投产。离子液催化烷基化过程包括原料预处理、烷基化反应及产品分离、离子液再生三个部分。离子液的主要活性成分为氯化铝,同时阳离子部分含cu等金属化合物,因此烷基化生成油中含有氯离子或氯代烃,由于氯离子腐蚀性较强,对汽车油箱、发动机等部件安全使用存在重大隐患,必须将其脱除才能作为车用汽油调和组分。目前,针对以异丁烷与烯烃通过链式反应生产的烷基化油的脱氯研究较少,主要采用吸附脱除法。例如,cn204918487u公开了一种烷基化油脱氯设备,该设备包括脱氯装置a和脱氯装置b。从反应装置输送过来的含氯烷基化油,通过原料管线经脱氯装置物料入口进入装填有脱氯剂的脱氯装置,从脱氯装置内的脱氯剂中通过时,含氯烷基化油携带的残留有机氯就会被吸附到脱氯剂中。脱除有机氯后的合格烷基化油从脱氯装置物料出口排出,进入烷基化油产品罐。经脱氯后,烷基化油中的总氯含量降低至1ppm以下,满足市场对油品质量的要求。但是受固体吸附剂的有机氯吸附容量的限制,需要频繁再生,增加了工艺的操作的难度和成本。除吸附脱除法外,还有可以采用加氢脱除法。例如cn106995720a公开了一种含氯烷基化油的液相脱氯方法,该方法包括以下步骤:(1)液相加氢:在加氢条件下,将含氯烷基化油在液相状态下与氢气和加氢催化剂反应生成含hcl的加氢产物;(2)液相吸附:将所述含hcl的加氢产物在液相状态下与吸附剂接触,吸附hcl后,得到脱除hcl后的加氢产物:(3)油气分离:将所述脱除hcl后的加氢产物和氢分离,得到脱氯烷基化油。该液相脱氯方法采用液相加氢,其操作条件温和,氢油比低,不必设置加氢进料加加热炉等设备,可以实现有机氯的完全转化。但是,由于含hcl的加氢产物在液相状态下与吸附剂接触,hcl在液相中扩散速率较慢,而且加氢产物中hcl含量少(不大于500ppm),造成需要非常长的吸附停留时间才能将大部分hcl脱除,从而影响烷基化油的脱氯效率。cn103025687a公开了一种离子液体衍生的烃产物的加氢脱氯。该方法将得自离子液体催化烃转化反应的一种或多种烃产物加氢脱氯,从而提供了脱氯产物和含hcl的废气,所得脱氯产物的氯化物含量小于50ppm,典型地小于10ppm。该方法虽然也可以达到脱氯的目的,但该工艺需要气液分离,分离后产生含hcl、h2、c1-c5烃的废气,还有需要进一步回收或分离hcl。整个工艺流程比较复杂,投资和操作费用也相对较高。此外,加氢脱氯装置的开工过程中,由于反应条件和催化剂性能未达到反应所需的状态,因此加氢脱氯产物一般达不到质量指标。技术实现要素:针对现有技术的不足,本发明提供了一种烷基化油的脱氯方法。该方法不但可以满足烷基化生成油氯含量满足车用汽油调和组分的要求,而且提高了脱氯效率,同时解决了加氢脱氯装置开工初期引起的产品质量不达标问题,有效解决跨线阀门内漏造成的产品不合格或装置运转周期缩短的问题。本发明提供了一种烷基化油的脱氯方法,包括如下内容:烷基化反应结束后分离出离子液催化剂,得到烷基化混合产物,其特征在于:烷基化混合产物直接进入加氢脱氯反应器,然后加氢脱氯生成含hcl的加氢产物,再进入吸附脱氯装置对加氢产物中的hcl进行吸附,吸附完成后通入精馏塔进行精馏;设置跨线用于将加氢脱氯反应、吸附脱氯装置与烷基化系统隔离时,将烷基化混合产物直接引入精馏塔,跨线即设置在加氢脱氯反应器入口前的管线与精馏塔进口管线之间的连通管线;设置防漏管线,防漏管线一端与跨线连通,另一端与异丁烷原料输送泵出口管线连通,防漏管线上设置第一阀门;跨线与防漏管线连通位置的跨线两侧分别设置有第二阀门、第三阀门;正常运转时,将第二阀门、第三阀门中的至少一道阀门关闭,优选地将第二阀门、第三阀门均关闭,第一阀门处于打开状态,防漏管线内液相压力高于跨线内压力,优选地高于跨线内液相0.1mpa~0.3mpa。本发明方法中,在加氢脱氯反应器开工时,烷基化混合产物先进入精馏塔进行精馏,然后将精馏塔的塔底物料引入到加氢脱氯反应器并进行加氢脱氯,然后经过吸附脱氯装置进行吸附,吸附完成后通入精馏塔5分钟~24小时时,优选1~10小时,停止将烷基化混合产物直接通入精馏塔和停止将精馏塔的塔底物料引入加氢脱氯反应器,将烷基化混合产物直接引入到加氢脱氯反应器,进行正常的加氢脱氯反应过程。本发明方法中,加氢脱氯采用液相反应状态,即在反应条件下,至少部分烷基化混合产物(烷基化油)为液相状态。本发明方法中,精馏塔设置的塔底再沸器为精馏塔提供热源,引入加氢脱氯反应器的精馏塔底物料在塔底再沸器之后引出,优选地,在塔底再沸器之后引出的精馏塔底物料的温度为100℃~200℃。本发明方法中,精馏塔的塔底设置物料输送装置,通过物料输送装置将精馏塔塔底出口的物料输送至加氢脱氯反应器入口前的管路。本发明方法中,在进入加氢脱氯反应器前的管路上依次设置有换热器和气液混合器,换热器用于加热烷基化混合产物,气液混合器用于将氢气和烷基化混合产物进行充分混合,气液混合器优选为静态混合器或动态混合器,静态混合器选自sv型静态混合器、sk型静态混合器、sx型静态混合器、sh型静态混合器、sl型静态混合器中的一种或者几种组合,动态混合器可以选自混合泵、超临界混合器、搅拌混合器中一种或者几种组合。本发明方法中,在气液混合器前的管路上设置有第四阀门。本发明方法中,设置有连接精馏塔的塔底物料与换热器进口的第一管路,第一管路上安装有第五阀门。本发明方法中,跨线连接在第四阀门前的管路。本发明方法中,设置有连接精馏塔的异丁烷出口与气液混合器入口的第二管路,第二管路上安装有第六阀门。本发明方法中,加氢脱氯的反应条件如下:反应压力为0.5mpa~6.0mpa,优选为1.2mpa~3.0mpa;反应温度为100℃~200℃,优选为120℃~170℃;体积空速为1.0h-1~10.0h-1,优选为2.0h-1~6.0h-1;氢油体积比为50:1以下,优选为2:1~10:1。本发明方法中,使用的加氢脱氯催化剂可以是商品加氢脱氯催化剂,优选采用以贵金属为活性组分的加氢脱氯催化剂,加氢脱氯催化剂一般以氧化铝为载体,如抚顺石油化工研究院研制生产的fhda-10催化剂。优选地,以pt和/或pd为活性组分,活性组分以重量计在催化剂中的含量不小于0.1%,一般为0.1%~1.5%。对烷基化油原料来说,使用该加氢脱氯催化剂可以使烷基化生成油中的有机氯化物降低至1ppm以下,满足优质车用汽油调和组分的要求。本发明方法中,吸附脱氯装置装填常规工业用脱氯剂即可,为碱土金属的氧化物,优选为氧化钙和/或氧化镁。本发明方法中,吸附脱氯装置的操作条件如下:吸附压力可与加氢脱氯反应器温度、压力可以相同或不同,吸附脱氯装置的吸附温度为100℃~200℃,吸附压力为0.5~6.0mpa,优选为1.2mpa~3.0mpa。本发明方法中,在开工初期,部分外甩精馏塔的塔底物料,得到脱氯后的烷基化油。本发明方法中,加氢脱氯反应器采用上流式操作方式,即反应物料自加氢脱氯反应器下部进入反应器内进行加氢脱氯反应,精制油通过分离器后,可直接进入汽油池。加氢脱氯反应器也可以采用下流式操作方式,即反应物料自加氢脱氯反应器顶部进入反应器内进行加氢脱氯反应。本发明方法中,对于烷基化反应为采用离子液催化剂的烷基化反应,异丁烷在反应过程中通常过量,其异丁烷与丁烯的摩尔比优选为(2~40):1,进一步优选为(5~20):1。反应温度可以确定在-20~100℃,一般为0~50℃;反应压力的选取应该以保证反应条件下反应原料保持液体状态为下限,一般可以为0.1~1.6mpa。与现有技术相比,本发明的有益技术效果如下:(1)如果跨线阀门稍有内漏,精馏塔的塔底物料氯含量就会明显上升,而阀门内漏是较普遍、较难发现、难以完全根治的难题,如果欲彻底解决阀门内漏,需付出较高代价。本发明中,巧妙采用防漏管线设计,结合该装置的实际特点,即异丁烷原料输送泵出口压力比跨线压力稍高,引入防漏管线后,防漏管线内液相压力稍高于跨线内压力,在这种状态下,即使跨线上阀门稍有内漏,也是防漏管线内物料(异丁烷)泄漏进入加氢脱氯反应器或泄漏进入精馏塔,而异丁烷不影响加氢脱氯反应,也不影响精馏塔的烷基化油的精馏过程,因此不管哪种内漏均不影响最终产品性质和氯含量,巧妙解决了阀门内漏引起的物料氯含量就会明显上升的问题。本发明方法构思巧妙,易于实现,维护成本低,有利于装置长周期稳定运转。(2)本发明方法,烷基化混合产物不经分离直接进行加氢脱氯,生成含hcl的加氢产物,含hcl的加氢产物通过吸附脱氯装置进行吸附,吸附后通入精馏塔进行精馏;这样烷基化混合产物中未反应的过量异丁烷气体能够从液相中汽提出来hcl,从而在与吸附脱氯装置中的吸附剂吸附时,能够很快地进行扩散、吸附,从而提高加氢产物的hcl脱除效率。此外,通过对烷基化混合产物进行加氢脱氯和吸附脱氯,然后通过精馏分离出异丁烷、正丁烷和氢气等气体,从而脱氯后不会产生含hcl、h2、c1-c5烃的废气。在开工初期,烷基化混合产物先进入精馏塔进行精馏,然后将精馏塔的塔底物料引入到加氢脱氯反应器,进行加氢脱氯,然后经过吸附脱氯装置重新进入精馏塔,这样既可以保证初期产品质量要求,避免产品不合格稳定期,又可以利用精馏塔的塔底再沸器快速升温烷基化混合产物,达到加氢脱氯的温度要求,从而不需要增加额外的加热器,并克服换热器在开工初期换热不稳定性、升温慢的缺点,而且不影响后续的正常加氢反应过程。(3)本发明方法,充分利用了贵金属加氢催化剂的低温高加氢活性的特点,采用液相下进料加氢脱氯工艺流程,降低了投资成本,可以实现高氯烷基化直接作为车用汽油调和组分的要求,脱氯后的生成油无需进一步处理,直接进入车用汽油池作为合格产品出厂。(4)对于炼油企业的烷基化装置,只需在烷基化装置的沉降塔和精馏塔之间增加一个加氢脱氯反应器和一个吸附脱氯装置即可,不必单独新建一套加氢脱氯装置,工艺流程简单,操作条件较为缓和,可实施性强,可以大幅度降低投资和操作费用。附图说明图1为本发明的烷基化油的脱氯的示意图;其中:1-异丁烷罐,2-丁烯罐,3-离子液罐,4-第一气液混合器,5-烷基化反应器,6-沉降罐,7-换热器,8-第二气液混合器,9-补充氢压缩机,10-加氢脱氯反应器,11-第一吸附脱氯装置,12-第二吸附脱氯装置,13-精馏塔,14-再沸器,15-第一阀门,16-第二阀门,17-第三阀门,18-第四阀门,19-第五阀门,20-第六阀门。具体实施方式下面结合附图和具体实施例对本发明方法进行详细的描述。对于采用本发明方法的新建装置,如图1所示:设置跨线用于将加氢脱氯反应器10、第一吸附脱氯装置11与烷基化系统隔离时,将烷基化混合产物直接引入精馏塔13,跨线为设置在加氢脱氯反应器10入口前的管线与精馏塔13进口之间的连通管线;设置防漏管线,防漏管线一端与跨线连通,另一端与精馏塔13底循环泵出口管线连通,防漏管线上设置第一阀门15;跨线与防漏管线连通位置的跨线两侧分别设置有第二阀门16、第三阀门17;正常运转时,将第二阀门16、第三阀门17中的至少一道阀门关闭,优选地将第二阀门16、第三阀门17均关闭,第一阀门15处于打开状态,防漏管线内液相压力高于跨线内压力,优选地高于跨线内液相压力0.1mpa~0.3mpa。这样由于精馏塔13底循环泵出口压力比跨线压力稍高,引入防漏管线后,防漏管线内液相压力稍高于跨线内压力,在这种状态下,即使跨线上阀门稍有内漏,也是防漏管线内物料通过发生泄漏的阀门进入加氢脱氯反应器或进入精馏塔,因为防漏管线内物料是经过加氢处理的,物料中的氯含量是非常低的,因此哪种内漏均不影响最终产品性质和氯含量,巧妙解决了阀门内漏引起的物料氯含量就会明显上升的问题。烷基化装置开工和加氢装置开工后,异丁烷罐1中的异丁烷与丁烯罐2的丁烯通入第一气液混合器4,然后再与离子液罐3中的离子液混合进入烷基化反应器5,反应结束后进入沉降罐6,沉降分离出离子液和烷基化混合产物,关闭第一阀门15、第四阀门18,打开第三阀门16、第三阀门17,烷基化混合产物直接进入精馏塔13,经过精馏塔13的底泵进入再沸器14加热至反应所需温度,打开第五阀门19,同时可选择性地打开第六阀门20,经过加热的物料返回换热器7,然后在第二气液混合器8内与异丁烷、补充氢压缩机9输送来的富氢气体5进行充分混合,混合后自加氢脱氯反应器10的底部进入,与贵金属加氢催化剂接触,在加氢脱氯的条件下进行加氢脱氯反应,使烷基化油中的有机氯化物转化为无机氯化物,反应结束后,含有异丁烷、氢气、hcl的产物进入第一吸附脱氯装置11,吸附脱除无机氯化物(hcl),然后脱氯产物再次进入精馏塔13进行精馏,塔底得到脱氯的烷基化油、中部得到正丁烷、上部得到异丁烷、顶部得到其它气体。塔底得到脱氯的烷基化油可全部或部分通入加氢脱氯反应器10,塔底部分外排烷基化油时,可以得到开工初期的脱氯烷基化油,可以直接用于汽油调和组分,或者进一步脱氯处理。当加氢脱氯反应器10进入正常工况后,关闭第二阀门16、第三阀门17、第五阀门19和第六阀门20,打开第一阀门15、第四阀门18,加氢脱氯部分进入正常生产工艺流程,这种灵活的工艺流程避免了开工初期产品不合格稳定期。同时,在开工初期,选择性地通入精馏后的异丁烷,可以使加氢脱氯生成的hcl进入异丁烷气体,而异丁烷可以再次精馏塔进行精馏,不需要额外装置进行分离,也不影响后继的正常开工。防漏管线内液相压力高于跨线内压力0.1mpa~0.3mpa,巧妙解决了阀门内漏引起的物料氯含量就会明显上升的问题。当第一吸附脱氯装置11中脱氯剂达到饱和后,关闭第一吸附脱氯装置11的阀门,打开阀门第二吸附脱氯装置12的阀门,进入第二吸附脱氯装置12,同时对第一吸附脱氯装置11中脱氯剂进行更换或再生,可以保证本脱氯单元实现连续稳定运行。该脱氯单元工艺流程简单,解决了烷基化油不能直接作为车用汽油调和组分的问题。经过本发明方法处理的烷基化生成油,产品可以达到如下性质:精制油氯含量小于1ppm。其他性质满足优质车用汽油调和组分的要求。下面的实施例将对本发明作进一步说明。实验使用催化剂为工业应用的加氢脱氯催化剂,为抚顺石油化工研究院研制生产的fhda-10加氢催化剂,其理化性质指标见表1。表1催化剂的理化性质指标催化剂编号fhda-10金属组成pt-pd物理性质孔容,ml/g≮0.45比表面积,m2/g≮170耐压强度,n/cm≮90形状圆柱条形实施例1按本发明方案新建烷基化装置。烷基化反应结束后,经沉降罐6分离离子液,然后经过进料泵、换热器7与氢气在sx型静态混合器中充分混合溶解后,进入加氢脱氯反应器10,反应条件为:反应压力1.5mpa﹑液时体积空速3.8h-1、反应温度143℃。反应结束后,反应结束后进入第一吸附脱氯装置11,吸附脱除无机氯化物。第一吸附脱氯装置11内装填常规工业用脱氯剂即可,其主要组分包括氧化钙。吸附脱氯装置的吸附温度为142℃,吸附压力1.4mpa。然后吸附脱氯产物进入精馏塔13进行精馏,塔底得到脱氯的烷基化油、中部得到正丁烷、上部得到异丁烷、顶部得到其它气体。加氢脱氯前烷基化混合产物中的烷基化油的性质及精馏塔得到的最终产品-烷基化油性质列于表2。采用本发明方法对加氢装置进行开工处理,开工时,先将烷基化混合产物先进入精馏塔13进行精馏,精馏塔13的塔底物料(在塔底再沸器之后引出的精馏塔底物料的温度为143℃)引入加氢脱氯反应器10,同时,可以选择性地通过第二气液混合器8向加氢脱氯反应器10引入循环的异丁烷,进行加氢脱氯,然后经过第一吸附脱氯装置11或第二吸附脱氯装置12进行吸附,在吸附完成的物料进入精馏塔5小时后,停止引入精馏塔13的塔底物料和异丁烷,以及停止直接向精馏塔13通入烷基化混合产物,切换为正常的操作流程。正常加氢操作时,防漏管线内液相压力高于跨线内压力0.2mpa,可巧妙解决了阀门内漏引起的物料氯含量就会明显上升的问题。由表2可见,采用该工艺技术可以使烷基化生成油的氯含量降低至1ppm以下,并且整个开工过程产品质量也保持稳定。实施例2按本发明方案新建烷基化装置。烷基化反应结束后,经沉降罐分离离子液,然后经过进料泵、换热器与氢气在sx型静态混合器中充分混合溶解后,进入加氢脱氯反应器,反应条件为:反应压力1.6mpa﹑液时体积空速4.2h-1、反应温度157℃。反应结束后,进入第一吸附脱氯装置11,吸附脱除无机氯化物。第一吸附脱氯装置11装填常规工业用脱氯剂即可,其主要组分包括氧化镁等。吸附脱氯装置的吸附温度为156℃,吸附压力1.5mpa。然后吸附脱氯产物进入精馏塔13进行精馏,塔底得到脱氯的烷基化油、中部得到正丁烷、上部得到异丁烷、顶部得到其它气体。加氢脱氯前的烷基化油的性质及最终产品性质列于表2。采用本发明方法对加氢装置进行开工处理,开工时,先将烷基化混合产物先进入精馏塔进行精馏,精馏塔的塔底物料(在塔底再沸器之后引出的精馏塔底物料的温度为157℃)引入加氢脱氯反应器10,同时,可以选择性地通过第二气液混合器8向加氢脱氯反应器10引入循环的异丁烷,进行加氢脱氯,然后经过第一吸附脱氯装置11或第二吸附脱氯装置12进行吸附,在吸附完成的物料进入精馏塔4小时后,停止引入精馏塔13的塔底物料和异丁烷,以及停止直接向精馏塔13通入烷基化混合产物,切换为正常的操作流程。正常加氢操作时,防漏管线内液相压力高于跨线内压力0.2mpa,可巧妙解决了阀门内漏引起的物料氯含量就会明显上升的问题。由表2可见,采用该工艺技术可以使烷基化生成油的氯含量降低至1ppm以下,并且整个开工过程产品质量也保持稳定。对比例1按照实施例1的方案,只是在开工时,将烷基化混合产物直接进入加氢反应器,直接进行正常操作。在开工过程中,加氢反应生成物有约30小时达不到质量指标(超过10ppm),而且开工初期5小时内超过50ppm。表2脱氯原料的性质及试验结果项目实施例1实施例2工艺条件反应温度,℃143157反应压力,mpa1.51.6液时体积空速,h-13.84.2油品性质加氢脱氯前的烷基化油氯含量,ppm750579开工初期,脱氯后烷基化油氯含量,ppm<10<10正常操作,脱氯后烷基化油氯含量,ppm<1.0<1.0实施例3试验运转过程中,打开跨线上的第二阀门16、第三阀门17,且使第二阀门16、第三阀门17保持很小开度,模拟阀门内漏工况,在不启用防漏管线(不打开第一阀门15)时,脱氯后烷基化油的氯含量大于10ppm,而启用防漏管线(打开第一阀门15)后,脱氯后烷基化油的氯含量稳定,低至1.0ppm。经过计算,在某些工况下,当催化剂性能良好时(产品指标远低于控制指标),如果有1.7wt%的内漏,脱氯后烷基化油的氯含量大于10ppm;在催化剂使用后期(脱氯后烷基化油的氯含量接近质量指标),稍有内漏,就会造成产品氯含量不达标。当前第1页12