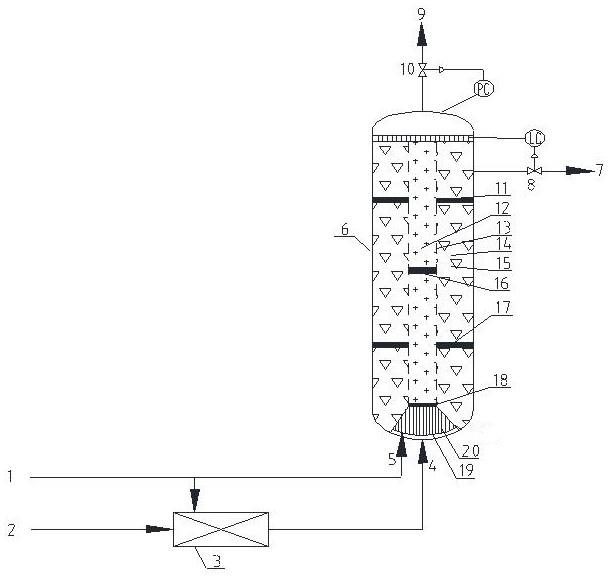
1.本发明属于石油化工领域,具体涉及一种重油加氢工艺。
背景技术:2.重质油的加氢反应过程一般采用固定床、悬浮床、沸腾床等加氢工艺,其中以固定床加氢工艺的应用最为广泛,能够用于多种类型的重油加氢过程。目前普遍采用的反应形式为气/液/固三相加氢工艺。
3.液相加氢工艺过程相比于传统的固定床气/液/固三相加氢工艺而言,具有加氢反应速率快、反应效率高、能耗低、投资少等诸多优势,得到广泛认可和应用,因此,上流式液相加氢反应过程综合了上流式加氢反应器和液相加氢反应工艺过程二者的优势,应用于加氢过程已经显示出了一定的优势。但是,重油液相加氢工艺中仍然存在如下问题:(1)重油黏度大,氢油传质速率低,导致反应速率低;(2)重油加氢过程的反应停留时间不易控制,停留短达不到反应要求的深度,而反应停留时间长副反应或裂解及催化剂结焦严重的问题。
4.cn 108659882 a提出了一种重油加氢方法及其加氢系统,其中,所述重油加氢方法包括:将重油、循环油、硫化剂和催化剂混合,与氢气在第一反应器中进行加氢裂化,得到第一反应产物;将第一反应产物的部分物料返回第一反应器中,将其余物料在第二反应器中进行加氢裂化,得到第二反应产物;将第二反应产物分离为轻组分和重组分,将部分重组分返回第二反应器中,将其余重组分分离得到馏分油做为循环油;将轻组分在第三反应器中进行加氢精制得到轻油产品。该发明方法主要是为了提高传热、传质效率,保证物料在反应器内足够的停留时间,提高重油转化率和轻质油收率,但只是通过常规的加氢反应器结构,更不能有效的控制催化剂与原料的接触时间,也不能保证重油转化率和轻质油收率。
5.因此,对于重油加氢反应过程来说,采用有效的手段,如开发新的加氢工艺,提高加氢过程中各个阶段的加氢反应速率和反应转化深度,解决集中放热、温升不均匀的问题,减少副反应或裂解反应,提高液体收率,具有重要意义。
技术实现要素:6.针对现有技术的不足,本发明提供一种重油加氢工艺。本发明通过对重油原料与氢气混合溶解,同时控制进料在反应器内流动路径,解决了重油液相加氢过程反应前期温升高、反应器径向温差大的问题,保证反应中期较高转化率,减少后期深度裂化反应,提高液收。
7.本发明的重油加氢工艺,包括如下内容:(1)氢气和重油原料在氢油混合设备进行混合得到第一混合进料;(2)第一混合进料自固定床反应器底部进入下筒内沿反应器轴向延伸的无机膜管的壳侧,补充氢气进入无机膜管管侧,补充氢气由无机膜管管壁上的孔道由管侧扩散至壳侧,均匀分散在壳侧的第一混合进料中,形成第二混合进料;所述下筒横截面积由下至上逐渐减小;
(3)第二混合进料向上流动进入与下筒连通的上筒,经上筒壁上开孔进入上、下筒和反应器外筒体之间的环形区域,上筒内装填第一加氢催化剂,环形区域内装填第二加氢催化剂,第二混合进料由下而上与第二加氢催化剂发生加氢反应,经过一段停留时间后在环形区域内的第一块隔板的阻挡下,反应物流经上筒壁上开孔返回上筒,在第一加氢催化剂上发生加氢反应,经过一定的停留时间后,在上筒的第一块隔板的阻挡下,再进入环形区域在第二加氢催化剂上继续发生加氢反应,反应物料按照上述方式在上筒和环形区域轴向设置的若干隔板的作用下,在上筒和环形区域交替进行加氢反应,最后加氢产物经环形区域上部流出。
8.本发明工艺中,所述的重油原料选自减压渣油、蜡油、煤焦油、润滑油、蒽油、脱沥青油、生物柴油、动物油或植物油等中的一种或多种。
9.本发明工艺中,所述的氢油混合设备选自静态混合器、溶气泵、胶体磨、微孔板分散组件、无机膜管分散组件等具有气液混合功能的设备中的一种或多种;第一混合进料中,氢气含量为0.1wt%~20wt%,优选2.0wt%~8.0wt%,以重油原料质量为基准。
10.本发明工艺中,管壳式无机膜管组件中氢气通入量为重油原料质量的0.1wt%~20%,优选2.0wt%~10.0wt%。
11.本发明工艺中,所述的反应物料在反应器内由环形区域至上筒交替反应的次数为1~10,优选2~4。
12.本发明工艺中,所述上筒的加氢反应条件为:反应温度150~500℃,优选260~450℃;反应压力1.0~20.0mpa,优选6.0~15.0mpa;新鲜进料液时体积空速0.1~15.0h-1
,优选1.0~10.0h-1
。
13.本发明工艺中,所述环形区域的加氢反应条件为:反应温度150~580℃,优选300~500℃;反应压力1.0~20.0mpa,优选6.0~15.0mpa;新鲜进料液时体积空速0.1~15.0h-1
,优选2.0~20.0h-1
。
14.本发明工艺中,所述第一加氢催化剂的活性高于第二加氢催化剂,优选第一加氢催化剂的活性与第二加氢催化剂的活性之比为1.05:1~10:1。其中所述的活性高低是针对上筒和环形空间内发生的化学反应而言的,以每单位容积(或质量)催化剂在单位时间内转化原料反应物的数量来表示,催化活性的高低可以通过催化剂载体比表面积的大小、表面上活性中心的性质和单位表面积上活性中心的数量等进行选择或制备过程中进行调控。催化剂活性的评价方法如下:在相同的原料组成和反应条件下,同体积催化剂在同一套装置上进行加氢反应,经过相同的停留时间后测定产物组成数据,计算转化率比较大小,作为判断活性高低的依据。
15.本发明工艺中,所述第一和第二加氢催化剂可以根据反应的需要选择适宜的加氢催化剂,以实现不同的加氢目的。例如,所述第一和第二加氢催化剂可以各自独立地选自加氢精制催化剂、预加氢精制催化剂、加氢改质催化剂、选择性加氢催化剂、加氢处理催化剂、加氢裂化催化剂、补充加氢催化剂等,这些催化剂可以选择商品催化剂,也可以采用本领域常规使用的催化剂,或根据现有技术的方法制备。例如,所述第一加氢催化剂和第二加氢催化剂可以相互独立地为现有重油加氢装置所用的催化剂,如抚顺石油化工研究院研制开发的3936、3996,ff-16、ff-24、ff-26、ff-36、ff-46、ff-56加氢处理、uop公司的hc-k、hc-p催化剂、topsoe公司的tk-555、tk-565催化剂、akzo公司的kf-847、kf-848催化剂。
16.本发明工艺中,所述第一和第二加氢催化剂可以各自独立地包含载体和活性组分,例如以加氢催化剂的总重量计,载体含量为45wt%-95wt%,活性组分为5wt%-55wt%,其中所述活性组分优选选自第vib族和第viii族金属元素中的一种或多种,所述载体优选为氧化铝和/或含硅氧化铝。进一步优选地,所述第vib族金属元素一般为mo和/或w,第viii族金属元素一般为co和/或ni。在特别优选的实施方式中,以氧化物计并以加氢催化剂的重量为基准,所述第一和第二加氢催化剂各自独立地包含5-40wt%的第vib族金属元素和3-15wt%的第viii族金属元素。
17.本发明工艺中,所述上筒填装的第一加氢催化剂的活性高于所述环形区域内填装的第二加氢催化剂,且环形区域可以装填活性全部或部分低于上筒活性的加氢催化剂。
18.本发明工艺中,所述的加氢反应可以脱除部分或全部烃类原料中的硫、氮、氧、砷、金属、残碳等杂质,或饱和/部分饱和烯烃、芳烃、二烯烃,或发生烃类分子异构化、烷基化、环化、芳构化、裂化、裂解等反应。
19.本发明同时提供一种固定床加氢反应器,包含反应器外筒体和沿反应器轴向设置的内筒体,所述外筒体包括上封头、直筒段和下封头,外筒体和内筒之间为环形区域,内筒筒壁均匀开孔与环形区域连通,内筒和环形区域在不同高度交替设置若干隔板;所述内筒体由上至下依次包括上筒和下筒,其中,上筒位于所述直筒段内,顶端敞口,底部与下筒顶部连通;下筒位于所述下封头内,由上而下横截面积逐渐增大,底端与下封头内壁密闭连接,所述下筒内设置有沿反应器轴向延伸的无机膜管,从而形成管壳式结构,所述无机膜管的管壁上设置有供气体通过的孔道;下封头设置有液体入口和气体入口,液体入口和气体入口与所述下筒的底部连通,环形区域上部设置由产物出口;其中所述液体入口与下筒的管壳式结构的壳侧连通,所述气体入口与所述管壳式结构的管侧连通。
20.本发明反应器中,所述上筒筒壁开孔,孔的形状可以为圆形、椭圆形、三角形、矩形或多边形等中一种或多种,优选为圆形;内筒筒壁开孔面积与内筒筒壁侧面积比为1:1.1~1:10,优选1:1.5~1:3。开孔大小一般为0.1mm~50mm,优选5~25mm,开孔过小造成压降增加,开孔过大造成物料扩散不均匀。
21.本发明所述反应器的下筒具有管壳式结构,其管侧对应于所述无机膜管的管腔内部空间,而其壳侧对应于所述无机膜管的管壁与所述下筒的筒壁之间的空间。
22.本发明的反应器中,所述下筒为由下至上横截面积逐渐减小的截头圆锥形,其最大横截面直径与反应器直径之比为1:1.05~1:50,优选1:1.15~1:5,最大横截面直径与最小横截面直径之比为1:1.1~1:30,优选1:2~1:10。
23.本发明反应器中,所述下筒可充当减黏组件,其管壳式结构的壳侧连通反应器的液体入口,所述管壳式结构的管侧连通反应器的气体入口,其中所述无机膜管的管壁上设置有孔道,使得管侧的气体可经由所述孔道向另一侧的壳体空间扩散溶解,从而降低位于另一侧的液体物料的黏度,改善其流动性。优选地,所述无机膜管管壁上的孔道具有0.5nm-200nm的平均孔径,使得经由所述孔道扩散出的气泡具有10-1000nm,优选50-500nm的平均尺寸。
24.本发明反应器中,所述的隔板可以水平设置或倾斜一定角度,倾斜角度最好不超过30
°
,优选水平设置;上筒和环形区域在不同高度交替设置隔板数量至少为两块,也可以
根据需要增加隔板数量;所述的隔板为不锈钢板,上筒内隔板固定在上筒内壁表面,环形区域内的隔板固定于反应器内壁表面;物料通过反应器底部进入后,沿隔板分隔的流动通道在上筒和环形区域之间交替流动而发生反应。
25.本发明所述的反应器顶部有气体空间,反应器上封头顶部最高点处设置气体出口,用于连续或间断排放反应过程中的反应气体。
26.本发明反应器的上部通过液位控制反应产物出料,保证整个加氢反应过程为全液相加氢。
27.一般的重油加氢反应过程来说,首先,重油原料的加氢脱杂质比轻质油加氢过程的反应速率低的多,反应条件也更加苛刻,其中一方面原因是重油的黏度大,传质反应界面阻力大,因此原料的黏度对反应速率具有很重要的影响。而对于加氢反应过程来讲,在反应前期,由于反应物中杂质浓度高,反应过程传质推动力大,因此反应速率快、放热剧烈,造成集中放热、放热不均匀的问题,因此反应前期需要控制原料与催化剂逐渐接触,且催化剂活性不宜较高;第二,而在反应中期,当反应物发生部分转化后,降低了反应物中杂质浓度,反应过程传质推动力也逐渐减小,此时不易发生放热剧烈的问题,因此需采用高活性的催化剂来提高反应速率和反应转化率,但又要防止放热剧烈的问题,为此中期阶段采用高活性、低活性交替进行的催化剂较为适宜;第三,在反应后期,当反应到达后期阶段,反应温度较高,继续采用高活性催化剂则会增加副反应和裂解反应,因此需要采用适当低活性的催化剂,减少副反应和裂解反应;第四,基于反应过程的中,前期、后期都需要较低活性催化剂,而中期需要较高活性的催化剂,中期阶段需要高活性、低活性交替进行的催化剂较为适宜,既要保持较高的反应速率和反应转化率,又要减少副反应和裂解反应。
28.本发明通过在反应器进料位置设置特殊结构的管壳式无机膜管组件,降低了物料黏度、改善物料流动性的同时,提高了氢气在原料油中的溶解分散量和分散均匀性和混合状态稳定性,减小氢油传质界面阻力,提高加氢反应速率;加氢反应器分为内筒体(上、下筒)和环形区域,通过交替设置的隔板来控制物料的流动路径,物料在反应前期首先进入环形区域,环形区域装填的低活性催化剂,可以控制反应前期活性和温升,解决这个阶段集中放热、反应不均匀、反应器径向温差大的问题;环形区域流出的物料进入装填的高活性催化剂的上筒,可以控制物料在高活性催化剂表面的停留时间,减少高温高活性催化剂的裂解反应;反应中期,物料与不同活性催化剂交替发生加氢反应,既能够很好的控制副反应、使温升更加均匀,又能保证较高的反应转化率;反应后期反应温度较高,从内筒流出的物料进入环形区域与活性较低催化剂反应,减少了副反应和裂解反应。
附图说明
29.图1是本发明的重油加氢工艺的示意图;图2、图3分别为固定床加氢反应器下筒的侧视图和俯视图。
30.1为氢气,2为重油原料,3为氢油混合器,4为第一混合进料,5为补充氢气管线,6为固定床加氢反应器,7为加氢反应产物,8为重油加氢反应产物出料阀,9为反应器排放气,10为排气控制阀,11为上筒,12为第一加氢催化剂,13为上筒筒壁,14为环形区域,15为第二加氢催化剂,16为上筒隔板,17为环形区域隔板,18为下筒,19为壳侧,20为无机膜管。
具体实施方式
31.下面结合附图说明和实施例对本发明进行详细说明,但不因此限制本发明。
32.以附图1说明本发明的重油加氢加氢工艺:重油原料2与氢气1经氢油混合器3混合后,作为第一混合进料4自固定床加氢反应器6的底部进料,进入下筒18的壳侧19,补充氢气5进入无机膜管的管侧,并由管侧通过无机膜管管壁上的孔道扩散至壳侧19,氢气均匀分散在壳侧19内的液相中形成第二混合进料,推动液相进料穿过内筒的上筒筒壁13横向进入环形区域14;进入环形区域14的物料由下而上与第二加氢催化剂 15发生加氢反应,反应经过一段停留时间后在环形区域隔板17的阻挡下发生横向折流,经上筒筒壁13扩散至上筒11,由下而上与第一加氢催化剂 12发生加氢反应;物料在上筒11经过一定的停留时间后,在上筒隔板16的阻挡下发生横向折流,再进入环形区域14继续进行加氢反应,反应物料按照上述方式在轴向设置交替设置的若干上筒隔板16和环形区域隔板17的作用下,在上筒11和环形区域14交替进行加氢反应,最后加氢产物在出料阀8的作用下经环形区域14上部设置的出料口流出。反应过程产生的反应气体在反应器顶部排气控制阀10的作用下作为排放气9排出。
33.本发明对比例及实施例中采用的原料油为来自某厂的蜡油混合原料,具体性质见表1。
34.表1 蜡油原料性质对比例1以表1所示的蜡油原料作为加氢反应进料,采用常规气、液、固三相固定床加氢反应器及加氢方法,催化剂采用2个床层,两个床层高度相同,第一床层填装抚顺石油化工研究院开发的fzc保护剂/3996催化剂,第二床层填装抚顺石油化工研究院开发的3936催化剂,其中第一床层中的fzc保护剂为3996催化剂床层高度的15%。
35.加氢反应条件如下:平均反应温度为380~435℃,反应压力为15mpag,液时体积空速为0.72h-1
,反应器入口氢油体积比为450。
36.以表1中的蜡油为原料,经过气、液、固三相固定床加氢反应器加氢后得到反应产品,催化剂床层温度分布见表2,液体产品性质见表3。
37.实施例1采用附图1所述的方法,固定床加氢反应器内筒填装的第一加氢催化剂采用抚顺石油
化工研究院开发的fzc保护剂/ff-46催化剂,其中fzc保护剂为外筒总催化剂体积的15%,环形区域填装的第二加氢催化剂采用抚顺石油化工研究院开发的3936催化剂。
38.第一混合进料中中含有的氢气为原料油(新鲜原料油与循环油之和)质量的3.66%;加氢反应器补氢组件中氢气通入量为原料油(新鲜原料油与循环油之和)质量的9.28%;循环比为2.5。
39.加氢反应器内筒的反应条件如下:反应温度为384~401℃,反应压力为15.0mpag,液时体积空速为2.8h-1
;加氢反应器环形区域的反应条件如下:反应温度为385~403℃,反应压力为15.0mpag,液时体积空速为1.5h-1
。
40.上筒筒壁上部均匀开设φ10的圆孔,开孔面积与上筒表面积的比为1:1.15;下筒的最大横截面直径与反应器直径之比为1:3,最大横截面直径与最小横截面直径之比为2:1。
41.以表1中的蜡油为原料,经过本发明的固定床加氢工艺进行加氢反应后得到反应产品,催化剂床层温度分布见表2,液体产品性质见表4。
42.实施例2采用附图1所述的方法,反应器内筒填装的第一加氢催化剂采用抚顺石油化工研究院开发的fzc保护剂/3996催化剂,其中fzc保护剂为外筒总催化剂体积的15%,环形区域填装的第二加氢催化剂采用抚顺石油化工研究院开发的3936催化剂。
43.第一混合进料中含有的氢气为原料油(新鲜原料油与循环油之和)质量的5.40%;加氢反应器补氢组件中氢气通入量为原料油(新鲜原料油与循环油之和)质量的7.74%;循环比为2.0。
44.加氢反应器内筒的反应条件如下:反应温度为382~401℃,反应压力为15.0mpag,液时体积空速为2.2h-1
;加氢反应器环形区域的反应条件如下:反应温度为384~404℃,反应压力为15.0mpag,液时体积空速为1.4h-1
。
45.反应器上筒筒壁上部均匀开设φ8的圆孔,开孔面积与上筒表面积的比为1:1.15;下筒的最大横截面直径与反应器直径之比为1:2,最大横截面直径与最小横截面直径之比为2.5:1。
46.以表1中的蜡油为原料,经过本发明的固定床加氢工艺进行加氢反应后得到反应产品,催化剂床层温度分布见表2,液体产品性质见表5。
47.实施例3采用附图1所述的方法,反应器内筒填装的第一加氢催化剂采用抚顺石油化工研究院开发的fzc保护剂/ff-46催化剂,其中fzc保护剂为外筒总催化剂体积的15%,环形区域填装的第二加氢催化剂采用抚顺石油化工研究院开发的ff-16催化剂。
48.第一混合进料中含有的氢气为原料油(新鲜原料油与循环油之和)质量的7.66%;加氢反应器补氢组件中氢气通入量为原料油(新鲜原料油与循环油之和)质量的5.28%;循环比为2.0。
49.加氢反应器内筒的反应条件如下:反应温度为385~403℃,反应压力为15.0mpag,液时体积空速为2.0h-1
;加氢反应器环形区域的反应条件如下:反应温度为386~405℃,反应压力为15.0mpag,液时体积空速为1.5h-1
。
50.上筒筒壁上部均匀开设φ8的圆孔,开孔面积与上筒表面积的比为1:1.15;下筒的
最大横截面直径与反应器直径之比为1:2.5,最大横截面直径与最小横截面直径之比为2.4:1。
51.以表1中的混合蜡油为原料,经过本发明的固定床加氢工艺进行加氢反应后得到反应产品,上筒和环形区域的催化剂床层温度分布见表2,液体产品性质见表6。
52.表2 对比例1和实施例1-3的催化剂温度分布表3 液体产品性质(对比例1)表4 液体产品性质(实施例1)表5 液体产品性质(实施例2)
表6 液体产品性质(实施例3)由本实施例及对比例的加氢反应效果可以看出,采用本发明的重油加氢工艺,通过在反应器底部进料位置设置管壳式无机膜组件,降低重油原料的黏度,改善了物料流动性,提高氢气的分散溶解性能,为加氢反应过程传质提供了保证。此外,结合管壳式结构的下筒,将反应器分为内筒和环形区域,通过交替设置的隔板来控制物料的流动路径,物料在反应前期部分物料进入环形区域、部分物料进入内筒,环形区域装填的低活性催化剂,低空速操作,而内筒填装高活性催化剂,高空速操作,可以控制反应前期的活性、温升及反应器径向温差,解决这个阶段集中放热、反应不均匀的问题;在反应过程中,环形区域的反应物料与内筒的反应物料交替进行反应,即环形区域流出的物料进入装填的高活性催化剂的内筒,内筒的流出物也进入装有低活性催化剂的环形区域继续反应,这样就可以控制物料在高活性催化剂表面的停留时间和反应剧烈程度,不但使高温区域的反应热更加均匀,而且大幅减少高温高活性催化剂的裂解反应,提高液体收率。