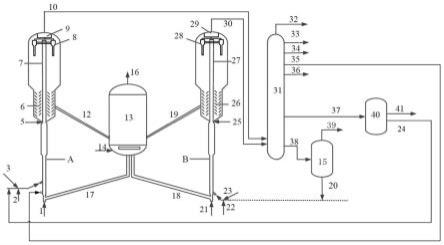
1.本技术石油炼制及石油化工加工过程,具体地,涉及一种制取乙烯和丙烯的催化转化方法。
背景技术:2.乙烯是世界上最多的化工产品之一,占全球整个石化产品产量的75%以上;乙烯的大宗下游产品主要有聚乙烯、环氧乙烷、乙二醇、聚氯乙烯、苯乙烯和醋酸乙烯等。丙烯是重要的有机化工原料,其主要用于制丙烯腈、环氧丙烷和丙酮等。乙烯和丙烯作为重要的化工中间物需求日益增长。
3.采用传统的蒸汽裂解制乙烯、丙烯路线,对轻烃、石脑油等化工轻烃需求量较大。研究机构预计从2018年到2026年,全球汽油复合年均增长率预计将低于1%,但丙烯增长约4%。合理利用炼厂流程中的高碳烯烃来裂解制乙烯、丙烯,即满足了石化企业提质增效的目标,又顺应能源转型的时代需求。
4.中国专利cn101092323a中公开了一种采用c4-c8烯烃混合物为原料,在反应温度400-600℃,绝对压力为0.3-1.1kpa的条件下进行反应,经分离装置将c4馏分30-90重量%循环进反应器再次裂解制备乙烯和丙烯的方法。该方法重点通过c4馏分循环,提高了烯烃转化率,得到的乙烯和丙烯不少于原料烯烃总量的62%,但其乙烯/丙烯比较小,无法根据市场需求灵活调节,而且反应选择性低,产物中丁烯含量大,且存在c4分离能耗等问题。
5.中国专利cn101239878a中公开了一种采用碳四及以上烯烃的富烯烃混合物为原料,在反应温度400-680℃,反应压力为-0.09-1.0mpa,重量空速为0.1~50小时-1
的条件下进行反应,产物乙烯/丙烯较低,低于0.41,随着温度升高乙烯/丙烯增加,同时氢气、甲烷和乙烷增多。
6.因此,本领域亟需一种新的生产高产率的乙烯和丙烯的方法,以实现石油资源高效利用。
技术实现要素:7.本公开的目的在于提供一种生产乙烯和丙烯的催化转化方法,进一步提高乙烯和丙烯产率。
8.为了实现上述目的,本公开提供了一种多产乙烯和丙烯的催化转化方法,该方法包括如下步骤:
9.s1、将烯烃含量在50重量%以上的烃油原料与温度在650℃以上的催化转化催化剂接触并在第一催化转化反应器中进行催化转化反应,得到第一反应物流和第一待生催化剂;
10.s2、将重质原料油与温度在650℃以上的催化转化催化剂接触并在第二催化转化反应器中进行催化转化反应,得到第二反应物流和第二待生催化剂;
11.s3、分离所述第一反应物流和所述第二反应物流,得到乙烯、丙烯、丁烯、含c5以上
烯烃的物流和催化蜡油;将所述丁烯和含c5以上烯烃的物流分别引入所述第一催化转化反应器中继续反应。
12.可选地,步骤s3中,所述丁烯先于所述含c5以上的物流与所述催化转化催化剂接触,所述含c5以上烯烃的物流与所述烃油原料混合共同进料。
13.可选地,所述含c5以上烯烃的物流中烯烃的含量在50重量%以上;所述富含烯烃的物流中的烯烃为c5以上的烯烃。
14.可选地,该方法还包括:将所述第一待生催化剂和第二待生催化剂送至共用再生器中进行烧焦再生,得到再生催化剂;将所述再生催化剂返回至所述第一催化转化反应器和所述第二催化转化反应器。
15.可选地,所述第一催化转化反应的条件包括:反应温度为600-800℃,反应压力为0.05-1mpa,反应时间为0.01-100秒,所述催化转化催化剂与所述烃油原料的重量比为(1-200):1;所述第二催化转化反应的条件包括:反应温度为400-650℃,反应压力为0.05-1mpa,反应时间为0.01-100秒,所述催化转化催化剂与所述重质原料油的重量比为(1-100):1。
16.可选地,所述丁烯引入所述第一催化转化反应器中继续反应的反应条件包括:反应温度为650-800℃,反应压力为0.05-1mpa,反应时间为0.01-10秒,所述催化转化催化剂与所述丁烯的重量比为(20-200):1。
17.优选地,所述丁烯引入所述第一催化转化反应器中继续反应的反应条件包括:反应温度为680-780℃,反应压力为0.1-0.8mpa,反应时间为0.05-8秒,所述催化转化催化剂与所述丁烯的重量比为(30-180):1。
18.可选地,该方法还包括:将所述催化蜡油经过加氢处理后得到加氢催化蜡油,使所述加氢催化蜡油与所述重质原料油混合后共同进入所述第二催化转化反应器。
19.可选地,所述加氢处理的条件包括:氢分压为3.0-20.0兆帕,反应温度为300-450℃,氢油体积比为300-2000,体积空速为0.1-3.0小时-1
。
20.可选地,所述烃油原料中的烯烃含量在80重量%以上;优选地,所述烃油原料中的烯烃含量在90重量%以上;更优选地,所述烃油原料为纯烯烃原料;所述重质原料油选自石油烃和/或矿物油;所述石油烃选自减压瓦斯油、常压瓦斯油、焦化瓦斯油、脱沥青油、减压渣油、常压渣油和重芳烃抽余油中的至少一种;所述矿物油选自煤液化油、油砂油和页岩油中的至少一种。
21.可选地,所述烃油原料中的烯烃来自烷烃原料脱氢产生的c4以上馏分、炼油厂催化裂解装置产生的c4以上馏分、乙烯厂中蒸汽裂解装置的c4以上馏分、mto副产的c4以上的富烯烃馏分、mtp副产的c4以上的富烯烃馏分。
22.可选的,所述烷烃原料选自石脑油、芳烃抽余油和轻质烃中的至少一种。
23.可选地,以所述催化转化催化剂的重量为基准,所述催化转化催化剂包含1-50重量%的分子筛、5-99重量%的无机氧化物和0-70重量%的粘土;
24.可选地,所述分子筛包括大孔分子筛、中孔分子筛和小孔分子筛中的一种或几种;
25.可选地,以所述催化转化催化剂的重量为基准,所述催化转化催化剂还包含0.1-3重量%的活性金属;所述活性金属选自viii族金属、iva族金属和稀土金属中的一种或几种。
26.通过上述技术方案,本公开的方法分别将含有烯烃的原料和重质原料油高温裂解,将分离产物中的烯烃返回所述装置继续反应。通过将油气分离过程中所生产的大分子烯烃以特定的路线进行回炼,降低了甲烷产率,从而达到石油资源高效利用的目的,可以取代传统的高耗能的蒸汽裂解产乙烯和丙烯的方案,同时本公开的方法具有高乙烯和丙烯产率及选择性和低甲烷产率。并且本公开使用共用再生器对将第一待生催化剂和第二待生催化剂进行烧焦再生,然后分别送回第一催化转化反应器和第二催化转化反应器中,重质原料油在酸性催化剂上裂化时不可避免地会产生大量石墨化程度较高的焦炭,可以以此焦炭燃烧带来的热量为烯烃高温裂化提供能量,既实现了催化转化催化剂的循环利用,也进一步提高了石油资源的利用率,同时还减少了装置的能源消耗。
27.本公开的其他特征和优点将在随后的具体实施方式部分予以详细说明。
附图说明
28.附图是用来提供对本公开的进一步理解,并且构成说明书的一部分,与下面的具体实施方式一起用于解释本公开,但并不构成对本公开的限制。在附图中:
29.图1是本公开的一种具体实施方式的流程示意图。
30.附图标记说明
31.a第一反应器
ꢀꢀꢀꢀꢀꢀꢀꢀꢀꢀ
b第二反应器
32.1管线
ꢀꢀꢀꢀꢀꢀꢀꢀꢀꢀꢀꢀꢀꢀꢀꢀ
2管线
ꢀꢀꢀꢀꢀꢀꢀꢀꢀꢀꢀꢀꢀꢀꢀꢀ
3管线
33.5管线
ꢀꢀꢀꢀꢀꢀꢀꢀꢀꢀꢀꢀꢀꢀꢀꢀ
6汽提段
ꢀꢀꢀꢀꢀꢀꢀꢀꢀꢀꢀꢀꢀꢀ
7出口段
34.8沉降器
ꢀꢀꢀꢀꢀꢀꢀꢀꢀꢀꢀꢀꢀꢀ
9集气室
ꢀꢀꢀꢀꢀꢀꢀꢀꢀꢀꢀꢀꢀꢀ
10管线
35.12斜管
ꢀꢀꢀꢀꢀꢀꢀꢀꢀꢀꢀꢀꢀꢀꢀ
13再生器
ꢀꢀꢀꢀꢀꢀꢀꢀꢀꢀꢀꢀꢀ
14管线
36.15加氢处理反应器
ꢀꢀꢀꢀꢀ
16管线
ꢀꢀꢀꢀꢀꢀꢀꢀꢀꢀꢀꢀꢀꢀꢀ
17管线
37.18管线
ꢀꢀꢀꢀꢀꢀꢀꢀꢀꢀꢀꢀꢀꢀꢀ
19斜管
ꢀꢀꢀꢀꢀꢀꢀꢀꢀꢀꢀꢀꢀꢀꢀ
24管线
38.21管线
ꢀꢀꢀꢀꢀꢀꢀꢀꢀꢀꢀꢀꢀꢀꢀ
22管线
ꢀꢀꢀꢀꢀꢀꢀꢀꢀꢀꢀꢀꢀꢀꢀ
23管线
39.24管线
ꢀꢀꢀꢀꢀꢀꢀꢀꢀꢀꢀꢀꢀꢀꢀ
25管线
ꢀꢀꢀꢀꢀꢀꢀꢀꢀꢀꢀꢀꢀꢀꢀ
26汽提段
40.27出口段
ꢀꢀꢀꢀꢀꢀꢀꢀꢀꢀꢀꢀꢀ
28沉降器
ꢀꢀꢀꢀꢀꢀꢀꢀꢀꢀꢀꢀꢀ
29集气室
41.30管线
ꢀꢀꢀꢀꢀꢀꢀꢀꢀꢀꢀꢀꢀꢀꢀ
31产物分离装置
ꢀꢀꢀꢀꢀꢀꢀ
32管线
42.33管线
ꢀꢀꢀꢀꢀꢀꢀꢀꢀꢀꢀꢀꢀꢀꢀ
34管线
ꢀꢀꢀꢀꢀꢀꢀꢀꢀꢀꢀꢀꢀꢀꢀ
35管线
43.36管线
ꢀꢀꢀꢀꢀꢀꢀꢀꢀꢀꢀꢀꢀꢀꢀ
37管线
ꢀꢀꢀꢀꢀꢀꢀꢀꢀꢀꢀꢀꢀꢀꢀ
38管线
44.39管线
ꢀꢀꢀꢀꢀꢀꢀꢀꢀꢀꢀꢀꢀꢀꢀ
40烯烃分离装置
ꢀꢀꢀꢀꢀꢀꢀ
41管线
具体实施方式
45.以下对本公开的具体实施方式进行详细说明。应当理解的是,此处所描述的具体实施方式仅用于说明和解释本公开,并不用于限制本公开。
46.本公开提供了一种多产乙烯和丙烯的催化转化方法,该方法包括如下步骤:
47.s1、将烯烃含量在50重量%以上的烃油原料与温度在650℃以上的催化转化催化剂接触并在第一催化转化反应器中进行催化转化反应,得到第一反应物流和第一待生催化剂;
48.s2、将重质原料油与温度在650℃以上的催化转化催化剂接触并在第二催化转化
反应器中进行催化转化反应,得到第二反应物流和第二待生催化剂;
49.s3、分离所述第一反应物流和所述第二反应物流,得到乙烯、丙烯、丁烯、含c5以上烯烃的物流和催化蜡油;将所述丁烯和所述含c5以上烯烃的物流分别引入所述第一催化转化反应器中继续反应。
50.本公开的发明人经过大量实验发现,烷烃和烯烃在催化剂上反应所形成的产物分布具有差异。烯烃在高温催化剂上进行催化反应时,产物中的氢气、甲烷和乙烷产率较低,乙烯、丙烯产率较高,且乙烯、丙烯选择性明显地改善。因此,本公开的方法将化工过程中所生产的低附加值烯烃以特定的路线进行炼制,有效提高了乙烯和丙烯产率,实现了石油资源的有效利用。
51.本公开的一种优选地实施方式,步骤s3中,所述丁烯先于含c5以上烯烃的物流与催化转化催化剂接触,所述含c5以上烯烃的物流与所述烃油原料混合共同进料。烃类裂化的难度随着碳数减小不断加大,丁烯裂化需要的能量较高,因此如果优选丁烯先和高温的催化转化催化剂接触,含c5以上烯烃的物流后和催化转化催化剂接触,不仅能够提高丁烯转化率和产品乙烯、丙烯选择性,并且避免烯烃同时进料生成较多副产品,实现资源的高效利用。
52.根据本公开,所述含c5以上烯烃的物流中烯烃的含量可以在50重量%以上。
53.本公开的一种优选地实施方式,该方法还可以包括:将所述第一待生催化剂和第二待生催化剂送至共用再生器中进行烧焦再生,得到再生催化剂;将所述再生催化剂返回至所述第一催化转化反应器和所述第二催化转化反应器。本公开使用共用再生器对将第一待生催化剂和第二待生催化剂进行烧焦再生,重质原料油在酸性催化剂上裂化时不可避免地会产生大量石墨化程度较高的焦炭,可以以此焦炭燃烧带来的热量为烯烃高温裂化提供能量,进一步使石油资源高效利用。
54.本公开中,所述第一催化转化反应器和所述第二催化转化反应器各自独立的选自提升管、等线速的流化床、等直径的流化床、上行式输送线和下行式输送线中的一种或两种串联组合,其中,提升管为等直径提升管反应器或者变径流化床反应器。
55.根据本公开,所述第一催化转化反应的条件可以包括:反应温度为600-800℃,反应压力为0.05-1mpa,反应时间为0.01-100秒,所述催化转化催化剂与所述烃油原料的重量比为(1-200):1;优选地,反应温度为630-780℃,反应压力为0.1-0.8mpa,反应时间为0.1-80秒,所述催化转化催化剂与所述烃油原料的重量比为(3-180):1;更优选地,反应温度为650-750℃,反应压力为0.2-0.5mpa,反应时间为0.2-70秒,所述催化转化催化剂与所述烃油原料的重量比为(4-150):1。
56.所述第二催化转化反应的条件可以包括:反应温度为400-650℃,反应压力为0.05-1mpa,反应时间为0.01-100秒,所述催化转化催化剂与所述重质原料油的重量比为(1-100):1;优选地,反应温度为450-600℃,反应压力为0.1-0.8mpa,反应时间为0.1-80秒,所述催化转化催化剂与所述重质原料油的重量比为(3-70):1;更优选地,反应温度为480-580℃,反应压力为0.2-0.5mpa,反应时间为0.2-70秒,所述催化转化催化剂与所述重质原料油的重量比为(4-30):1。
57.根据本公开,所述丁烯引入所述第一催化转化反应器中继续反应的反应条件可以包括:反应温度为650-800℃,反应压力为0.05-1mpa,反应时间为0.01-10秒,所述催化转化
催化剂与所述丁烯的重量比为(20-200):1。
58.进一步优选地,所述丁烯引入所述第一催化转化反应器中继续反应的反应条件可以包括:反应温度为680-780℃,反应压力为0.1-0.8mpa,反应时间为0.05-8秒,所述催化转化催化剂与所述丁烯的重量比为(30-180):1。
59.作为本公开的一种优选的实施方式,所述方法还可以包括:将所述催化蜡油经过加氢处理后得到加氢催化蜡油,使所述加氢催化蜡油与所述重质原料油混合后共同进入所述第二催化转化反应器。本公开的方法将催化蜡油进行加氢处理后再继续反应,进一步减少了生成小分子烷烃和焦炭的副反应,提高了乙烯和丙烯产率,实现了碳原子的有效利用。
60.根据本公开,所述加氢处理的条件可以包括:氢分压为3.0-20.0兆帕,反应温度为300-450℃,氢油体积比为300-2000,体积空速为0.1-3.0小时-1
。所述加氢处理使用的催化剂包括载体以及负载在载体上的金属组分和任选的添加剂,所述载体为氧化铝和/或无定型硅铝,所述金属组分为vib族金属和/或viii族金属,所述添加剂选自氟、磷、钛和铂中至少一种。具体的,所述vib族金属为mo或/和w,所述viii族金属为co或/和ni;以加氢处理的催化剂的重量为基准,所述添加剂的含量为0-10重量%,vib族金属的含量为12-39重量%,viii族金属的含量为1-9重量%。
61.根据本公开,所述烃油原料中的烯烃含量可以在80重量%以上;优选地,所述烃油原料中的烯烃含量在90重量%以上;更优选地,所述烃油原料为纯烯烃原料;所述烃油原料中的烯烃可来自相应的烷烃原料脱氢、炼油厂催化裂解装置产生的c4以上馏分、乙烯厂中蒸汽裂解装置的c4以上馏分或mto副产的c4以上的富烯烃馏分、mtp副产的c4以上的富烯烃馏分;所述重质原料油可以选自石油烃和/或矿物油;所述石油烃可以选自减压瓦斯油、常压瓦斯油、焦化瓦斯油、脱沥青油、减压渣油、常压渣油和重芳烃抽余油中的至少一种;所述矿物油可以选自煤液化油、油砂油和页岩油中的至少一种。所述烷烃原料可以来自石脑油、芳烃抽余油和其他装置的轻质烃中的至少一种。
62.进一步的实施方式中,烷烃脱氢制烯烃的方法,包括将烷烃与脱氢催化剂进行接触反应,反应器的入口温度为400-700℃,烷烃的体积空速为200-5000h-1
,所述接触反应的压力为0-1.0mpa。所述脱氢催化剂由载体以及负载在载体上的活性组分和助剂组成;以催化剂总重为100%计,所述载体的含量为60-90重量%,所述活性组分的含量为8-35重量%,所述助剂的含量为0.1-5重量%;所述载体为含有改性剂的氧化铝;所述改性剂的含量为催化剂总重的0.1-2重量%,所述改性剂为la或ce;所述活性组分为铂或铬;所述助剂为铋和碱金属组分或者铋和碱土金属组分;铋与所述活性组分的摩尔比为1:(5-50);铋与碱金属组分的摩尔比为1:(0.1-5);铋与碱土金属组分的摩尔比为1:(0.1-5);所述碱金属组分为li、na和k中的一种或多种;所述碱土金属组分为mg、ca和ba中的一种或多种。
63.根据本公开,以所述催化转化催化剂的重量为基准,所述催化转化催化剂包含1-50重量%的分子筛、5-99重量%的无机氧化物和0-70重量%的粘土;所述分子筛可以包括大孔分子筛、中孔分子筛和小孔分子筛中的一种或几种;作为本公开的一种优选的实施方式,以所述催化转化催化剂的重量为基准,所述催化转化催化剂还包含0.1-3重量%的活性金属;所述活性金属选自viii族金属、iva族金属和稀土金属中的一种或几种。
64.在本公开的一种实施方式中,所述中孔分子筛可以为zsm分子筛,进一步地,zsm分子筛可以选自zsm-5、zsm-11、zsm-12、zsm-23、zsm-35、zsm-38、zsm-48中的一种或几种。
65.在本公开的一种实施方式中,所述小孔分子筛可以为sapo分子筛,进一步地,sapo分子筛可以选自sapo-34、sapo-11、sapo-47中的一种或几种。
66.在本公开的一种实施方式中,所述大孔分子筛可以选自稀土y分子筛、稀土氢y分子筛、超稳y分子筛、高硅y分子筛、beta分子筛和其它类似结构的分子筛之中的一种或一种以上的混合物。
67.本公开的一种具体的实施方式,如图1所示,预提升介质经管线1由第一催化转化反应器a底部进入,烯烃含量在50%以上的烃油原料经管线3与来自管线2的雾化蒸汽一起注入第一催化转化反应器a的底部,与来自管线17的热再生催化转化催化剂在预提升介质的提升作用下沿第一催化转化反应器a向上加速运动,并发生反应。生成的第一反应物流和第一待生催化剂经出口段7进入沉降器8中的旋风分离器,实现第一反应物流和第一待生催化剂的分离,第一反应物流进入集气室9,第一待生催化剂细粉由料腿返回沉降器。沉降器中第一待生催化剂流向汽提段6,与来自管线5的汽提蒸汽接触。从第一待生催化剂中汽提出的油气经旋风分离器后进入集气室9,汽提后的第一待生催化剂经斜管12进入再生器13。
68.预提升介质经管线21由第二催化转化反应器b底部进入,来自管线18的热再生催化转化催化剂在预提升介质的提升作用下沿第二催化转化反应器器b向上加速运动,重质原料油经管线23与来自管线22的雾化蒸汽一起注入第二催化转化反应器b的底部,重质原料油在热的催化转化催化剂上发生反应,并向上加速运动。生成的第二反应物流和第二待生催化剂经出口段27进入沉降器28中的旋风分离器,实现第二反应物流和第二待生催化剂的分离,第二反应物流和第二待生催化剂进入集气室29,第二待生催化剂细粉由料腿返回沉降器。沉降器中第二待生催化剂流向汽提段26,与来自管线25的汽提蒸汽接触。从第二待生催化剂中汽提出的油气经旋风分离器后进入集气室29,汽提后的第二待生催化剂经斜管19进入再生器13。
69.再生器13中,主风经管线14进入再生器,烧去第一待生催化剂和第二待生催化剂上的焦炭,使失活的第一待生催化剂和第二待生催化剂再生。烟气经管线16进入烟机。再生催化剂经管线17和18分别进入第一催化转化反应器a、第二催化转化反应器b的提升管。
70.第一反应物流和第二反应物流分别经过大油气管线10和管线30进入后续的产物分离装置31,分离得到的氢气、甲烷和乙烷经管线32引出,乙烯经管线33引出,丙烯经管线34引出,丁烯经管线35引入第一催化转化反应器a底部继续反应,丙烷和丁烷经管线36引出,催化蜡油经管线38引入加氢处理反应器15,加氢处理后的轻组分由管线39引出,加氢催化蜡油由管线20引入第二催化转化反应器b底部继续反应,含烯粗物流经管线37引入到烯烃分离装置40,分离得到的烃流由管线41引出,富含烯烃的物流经管线24引入第一催化转化反应器a继续反应。
71.以下通过实施例进一步详细说明本公开。实施例中所用到的原材料均可通过商购途径获得。实施例中所用的原料a、b为重质原料油,性质如表1所示;原料c为催化裂化汽油轻馏分,其组成列于表2。
72.实施例中所用的催化转化催化剂a的制备方法简述如下:
73.用4300克脱阳离子水将969克多水高岭土(中国高岭土公司产物,固含量73%)打浆,再加入781克拟薄水铝石(山东淄博铝石厂产物,固含量64%)和144毫升盐酸(浓度30%,比重1.56)搅拌均匀,在60℃静置老化1小时,保持ph为2-4,降至常温,再加入预先准
备好的5000克浆液,其中中孔zsm-5分子筛和大孔y型分子筛(中国石化催化剂齐鲁分公司生产)1600g,二者重量比9:1。搅拌均匀,喷雾干燥,洗去游离na
+
,得催化剂。将得到的催化剂在800℃和100%水蒸汽下进行老化,老化后的催化剂称为催化转化催化剂a,催化转化催化剂a性质见表3。
74.实施例中所用的催化转化催化剂b商品牌号为cep-1,催化转化催化剂c商品牌号为chp-1,二者均为中国石化催化剂齐鲁分公司生产工业产品,催化剂性质见表3。
75.实施例中所用的加氢处理催化剂d制备方法简述如下:称取偏钨酸铵((nh4)2w4o
13
·
18h2o,化学纯)和硝酸镍(ni(no3)2·
18h2o,化学纯),用水配成200毫升溶液。将溶液加入到氧化铝载体50克中,在室温下浸渍3小时,在浸渍过程中使用超声波处理浸渍液30分钟,冷却,过滤,放到微波炉中干燥约15分钟。该催化剂的组成为:30.0重量%wo3,3.l重量%nio和余量氧化铝,记作加氢处理催化剂d。
76.实施例中所用的加氢脱硫催化剂e的制备过程如下:称取1000克由中国石化催化剂长岭分公司生产的拟薄水铝石,之后加入含硝酸(化学纯)10毫升的水溶液1000毫升,在双螺杆挤条机上挤条成型,并在120℃干燥4小时,800℃焙烧4小时后得到催化剂载体。用含氟化铵120克的水溶液900毫升浸渍2小时,120℃干燥3小时,600℃焙烧3小时;降至室温后,用含偏钼酸铵133克的水溶液950毫升浸渍3小时,120℃干燥3小时,600℃焙烧3小时,降至室温后,用含硝酸镍180克、偏钨酸铵320克水溶液900毫升浸渍4小时用相对于催化剂载体为0.1重%的偏钼酸铵(化学纯)和相对于催化剂载体为0.1重%的硝酸镍(化学纯)的混合水溶液浸渍含氟氧化铝载体4小时,120℃烘干3小时,在600℃下焙烧4小时,制得加氢脱硫催化剂e。
77.表1-1
78.进料性质a密度(20℃)/(千克/米3)859.7康氏残炭,重量%0.07c,重量%85.63h,重量%13.45s,重量%0.077n,重量%0.058fe,微克/克2.3na,微克/克0.6ni,微克/克4.9v,微克/克0.4族组成,重量% 饱和烃58.1芳烃26.3胶质15.3沥青质0.3
79.表1-2
[0080][0081][0082]
表2
[0083]
碳数烷烃重量%烯烃重量%环烷烃重量%芳烃重量%51.804.400.000.0063.9130.200.670.8773.3233.571.812.3982.7910.681.750.5990.400.850.000.00
[0084]
表3
[0085]
催化剂abc化学组成/重%
ꢀꢀꢀ
al2o349.246.326.5na2o0.070.040.19物理性质
ꢀꢀꢀ
比表面积/(m2·
g-1
)/153132堆密度/(g
·
cm-3
)0.790.860.45磨损指数/(%
·
h-1
)1.114.2筛分组成/重%
ꢀꢀꢀ
0-40μm14.217.97.340-80μm53.841.443.7>80μm32040.749.0
[0086]
实施例1
[0087]
本实施例的工艺流程如图1所示,在提升管反应器的中型装置上进行试验。1-戊烯和高温催化转化催化剂a在第一催化转化反应器底部接触,在反应温度700℃,反应压力0.1mpa,反应时间5s,催化转化催化剂a与原料的重量比45:1下发生催化转化反应,重质原
料油a和催化转化催化剂a在第二催化转化反应器底部接触,在反应温度530℃,反应压力0.1mpa,反应时间6s,催化转化催化剂a与原料的重量比5:1下发生催化转化反应,1-戊烯与重质原料之比为1:9。分离反应的反应产物和待生催化剂,将所得待生催化剂一起引入再生器烧焦再生,将所得反应产物一起引入组合分离系统,得到包括乙烯、丙烯、丁烯、富含烯烃的物流(终馏点为250℃)和催化裂化蜡油(初馏点为250℃)等的产品。催化裂化蜡油和加氢催化剂d在温度为350℃,氢分压18mpa,体积空速1.5小时-1
,氢油体积比1500的条件下反应得到加氢催化裂化蜡油。将所得到的丁烯引入第一催化转化反应器底部再裂化,反应温度为740℃,催化转化催化剂与丁烯的重量比为100:1,反应时间为0.2s;富含烯烃的物流引入第一催化转化反应器底部再裂化,反应温度为700℃,反应时间为5s;所述加氢催化裂化蜡油与重质原料油混合,再返回第二催化转化反应器进行反应。反应条件和产品分布列于表4。
[0088]
对比例1
[0089]
本对比例采用与实施例1类似的工艺流程,在提升管反应器的中型装置上进行试验,不同之处在于富含烯烃的物流不返回第一催化转化反应器继续反应。重质原料油a和催化转化催化剂a在第二催化转化反应器底部接触,在反应温度530℃,反应压力0.1mpa,反应时间6s,催化剂与原料的重量比5:1下发生催化转化反应。分离反应的反应产物和待生催化剂,将所得待生催化剂一起引入再生器烧焦再生,将所得反应产物一起引入组合分离系统,得到包括乙烯、丙烯、丁烯、富含烯烃的物流和催化裂化蜡油等的产品。催化裂化蜡油和加氢催化剂d在温度为350℃,氢分压18mpa,体积空速1.5小时-1
,氢油体积比1500的条件下反应得到加氢催化裂化蜡油。将所得到的丁烯引入第一催化转化反应器底部再裂化,反应温度为740℃,催化转化催化剂a与丁烯的重量比为100:1,反应时间为0.2s;所述加氢催化裂化蜡油与重质原料油混合,再返回第二催化转化反应器进行反应。反应条件和产品分布列于表4。
[0090]
实施例2
[0091]
本实施例的工艺流程如图1所示,在提升管反应器的中型装置上进行试验。重质原料油a和催化转化催化剂a在第二催化转化反应器底部接触,在反应温度530℃,反应压力0.1mpa,反应时间6s,催化剂与原料的重量比5:1下发生催化转化反应,分离反应的反应产物和待生催化剂,将所得待生催化剂一起引入再生器进行烧焦再生,将所得反应产物一起引入组合分离系统,得到包括乙烯、丙烯、丁烯、富含烯烃物流和催化裂化蜡油等的产品。催化裂化蜡油和加氢催化剂d在350℃,氢分压18mpa,体积空速1.5小时-1
,氢油体积比1500的条件下反应得到加氢蜡油。将所得到的丁烯引入第一催化转化反应器底部再裂化,反应温度为740℃,催化剂与原料的重量比为100:1,反应时间为0.2s;富含烯烃的物流引入第一催化转化反应器底部再裂化,反应温度为700℃,反应时间为5s;所述加氢催化裂化蜡油与重质原料油混合,再返回第二催化转化反应器进行反应。反应条件和产品分布列于表4。
[0092]
对比例2
[0093]
在提升管反应器的中型装置上进行试验,重质原料油a和催化转化催化剂b在提升管底部接触,在反应温度为610℃,催化剂与原料的重量比为16.9:1,反应压力0.1mpa,反应时间6s下发生催化转化反应,产物不进行加氢处理和返回所述装置继续反应。反应条件和产品分布列于表4。
[0094]
实施例3
[0095]
本实施例按照实施例2的方法生产乙烯和丙烯,所不同的是:使用原料b作为原料。本实施例的催化裂化蜡油不进行深度加氢处理,在加氢脱硫反应器内与加氢脱硫催化剂e接触,在反应压力6.0mpa,反应温度350℃,氢油体积比350,体积空速2.0小时-1
下反应,得到低硫加氢馏分油作为轻油组分。反应条件和产品分布列于表4。
[0096]
对比例3
[0097]
在提升管反应器的中型装置上进行试验,原料b和催化转化催化剂c在提升管底部接触,在反应温度为530℃,催化剂与原料的重量比为5:1,反应压力0.1mpa,反应时间6s下发生催化转化反应,加氢处理与实施例3基本相同,产物不返回所述装置继续反应。反应条件和产品分布列于表4。
[0098]
实施例4
[0099]
本实施例按照实施例1的方法生产乙烯和丙烯,所不同的是:第一催化转化反应器进料为催化裂化汽油轻馏分c。反应条件和产品分布列于表4。
[0100]
实施例5
[0101]
采用实施例1的方法和装置,区别仅在于:各反应区内的反应条件不同,具体的反应条件和产品分布列于表4。
[0102]
表4
[0103]
[0104][0105]
从表4可以看出,实施例1-4中的烯烃高温裂解时乙烯和丙烯有更高产率,得到的反应物流中乙烯和丙烯的含量在60%以上,且原料烯烃含量越多是效果越好,当采用烯烃含量100%的1-戊烯做为原料时,乙烯的含量为26.96%,丙烯的含量为35.57%,两者的总和可以高达62.53%。此外,苯、甲苯和二甲苯产率明显增加。
[0106]
以上详细描述了本公开的优选实施方式,但是,本公开并不限于上述实施方式中的具体细节,在本公开的技术构思范围内,可以对本公开的技术方案进行多种简单变型,这些简单变型均属于本公开的保护范围。
[0107]
另外需要说明的是,在上述具体实施方式中所描述的各个具体技术特征,在不矛盾的情况下,可以通过任何合适的方式进行组合。为了避免不必要的重复,本公开对各种可能的组合方式不再另行说明。
[0108]
此外,本公开的各种不同的实施方式之间也可以进行任意组合,只要其不违背本公开的思想,其同样应当视为本公开所公开的内容。