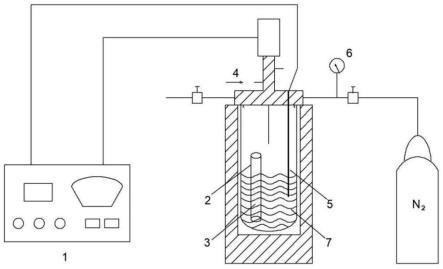
1.本发明涉及中间相沥青制备技术领域,尤其涉及一种采用煤/重油加氢共炼残渣制备中间相沥青的方法。
背景技术:2.煤/油共炼技术能够充分利用煤、油在加氢裂化反应中的协同效应,实现煤与重油的高效转化。但其产生的大量固体残渣难以处理,且综合利用起来有一定难度。而将煤/油共炼残渣经过一系列的处理转化为高附加值的功能性材料是实现残渣有效利用的途径之一。
3.煤/油加氢共炼残渣中含有大量残留的烃类化合物,具有碳氢元素含量较高的特点,如何无害化处理煤油共炼残渣,寻求一种大批量资源化清洁利用、且简单易行的新途径,是迫切需要解决的技术难题。而残渣中甲苯可溶物灰分含量少,杂原子及金属含量低,适合作为一些碳材料的原料。
4.中间相沥青(简称mp)由扁平盘状多环芳烃组成,由沥青、重油、煤焦油和其他原料通过热处理或芳香化合物通过催化缩合制备。中间相沥青被广泛认为是制造碳纤维、针状焦、碳电极材料、泡沫炭和其他高级功能材料的优良前体。
5.但中间相沥青在大规模应用上仍然受到诸多限制,除了生产成本高这一因素,就是中间相沥青的聚合控制难度大。通常以煤沥青和石油沥青为原料制备中间相沥青,虽然原料成本降低,但由于原料沥青由芳烃混合物组成,结构复杂,随着热缩聚反应的进行,不同组分的聚合程度各异,导致合成的中间相沥青不均匀,出现中间相组分与各向同性组分共存的问题,难以制备中间相含量为100%的中间相沥青,或制备的中间相沥青软化点较高,加工性能较差。
技术实现要素:6.本发明提供一种采用煤/重油加氢共炼残渣制备中间相沥青的方法,通过采用热缩聚工艺结合热沉降工艺将低中间相含量沥青中的各向异性与各向同性组分进行分离,提高产品的中间相含量,进而达到改善中间相沥青制备的泡沫炭导热性能的目的。
7.本发明提供的具体技术方案如下:
8.本发明提供的一种采用煤/重油加氢共炼残渣制备中间相沥青的方法,所述方法包括:
9.(1)采用甲苯作为溶剂对煤/重油加氢共炼残渣进行萃取处理,获取煤/重油加氢共炼残渣中的甲苯可溶物原料;
10.(2)将所述甲苯可溶物原料在380℃~420℃、初始压力0mpa~3mpa、反应时间3~8小时、加入5%~15%质量分数的共炭化剂条件下进行热缩聚反应,得到中间相含量为30%~45%的预中间相沥青;
11.(3)将所述预中间相沥青研磨至60目~100目,随后在高压反应釜内进行热沉降处
理,热沉降处理过程的温度为320℃~360℃,热沉降处理时间为3~6小时,热沉降处理的初始压力为0~2mpa;
12.(4)热沉降处理后自下而上按照预设大小切割等质量的样品,得到中间相含量大于95%的中间相沥青。
13.可选的,所述预设大小切割为按照5%~20%质量分数大小。
14.可选的,所述共炭化剂为四氢萘。
15.可选的,热沉降装置包括高压反应釜、石英玻璃管和加热介质,其中,所述预中间相沥青位于所述石英玻璃管的内部,所述石英玻璃管的底部包覆有所述加热介质。
16.可选的,热沉降处理过程的温度为330℃~340℃,热沉降处理时间为4~5小时,热沉降处理的初始压力为1~1.5mpa。
17.本发明的有益效果如下:
18.本发明提供的一种采用煤/重油加氢共炼残渣制备中间相沥青的方法,以甲苯对煤/重油加氢共炼残渣进行萃取,得到的甲苯可溶物在高压反应釜内进行热缩聚反应后得到一定中间相含量的预中间相沥青,由于预中间相沥青中含有较多各向同性组分,对后续制备的材料性能会产生较大影响,需要对各向异性与各向同性组分进行分离,通过在高压反应釜内进行热沉降处理,使底部沥青的组成更加均一,各向异性组分含量高,通过采用热缩聚工艺结合热沉降工艺将低中间相含量沥青中的各向异性与各向同性组分进行分离,提高产品的中间相含量,进而达到改善中间相沥青制备的泡沫炭导热性能的目的。
附图说明
19.为了更清楚地说明本发明实施例中的技术方案,下面将对实施例描述中所需要使用的附图作简单地介绍,显而易见地,下面描述中的附图仅仅是本发明的一些实施例,对于本领域普通技术人员来讲,在不付出创造性劳动的前提下,还可以根据这些附图获得其他的附图。
20.图1为本发明实施例的一种热沉降装置的结构示意图;
21.图2为本发明实施例的一种样品切割示意图。
具体实施方式
22.为了使本发明的目的、技术方案和优点更加清楚,下面将对本发明作进一步地详细描述,显然,所描述的实施例仅仅是本发明一部分实施例,而不是全部的实施例。基于本发明中的实施例,本领域普通技术人员在没有做出创造性劳动前提下所获得的所有其它实施例,都属于本发明保护的范围。
23.本发明实施例提供的一种采用煤/重油加氢共炼残渣制备中间相沥青的方法,以煤/重油加氢共炼残渣中甲苯可溶物为原料,采用热缩聚反应和热沉降分离相结合的工艺制备中间相沥青,不仅生产成本低,工艺简单,而且所制备的中间相沥青中间相含量高,软化点适中,光学结构较好,进而可制备出低导热和导热性能较好的泡沫炭。
24.本发明提供的一种采用煤/重油加氢共炼残渣制备中间相沥青的方法包括以下步骤:
25.(1)采用甲苯作为溶剂对煤/重油加氢共炼残渣进行萃取处理,获取煤/重油加氢
共炼残渣中的甲苯可溶物原料;
26.(2)将所述甲苯可溶物原料在380℃~420℃、初始压力0mpa~3mpa、反应时间3~8小时、加入5%~15%质量分数的共炭化剂条件下进行热缩聚反应,得到中间相含量为30%~45%的预中间相沥青;
27.(3)将所述预中间相沥青研磨至60目~100目,随后在高压反应釜内进行热沉降处理,热沉降处理过程的温度为320℃~360℃,热沉降处理时间为3~6小时,热沉降处理的初始压力为0~2mpa;
28.(4)热沉降处理后自下而上按照预设大小切割等质量的样品,得到中间相含量大于95%的中间相沥青。
29.热沉降法是一种提高中间相沥青性能的有效分离手段,是实现中间相沥青规模化利用的有效途径。热沉降工艺根据分散体系中不同组分的密度差异可以有效地分离中间相沥青中的各向同性与各向异性组分。利用热沉降和过滤分离的手段对中间相沥青进行分离,可以得到高中间相含量的沥青,而且以低中间相含量的中间相沥青作为分离对象,经热沉降处理后可以得到底部中间相含量接近100%的中间相沥青。对于组成和结构复杂的煤/重油共炼残渣,在经甲苯萃取后只通过一步热缩聚反应往往难以达到制备高导热性能泡沫炭的前驱体-中间相沥青的目的,但是,煤/重油共炼残渣经甲苯萃取后的采用热缩聚反应和热沉降分离相结合的工艺制备中间相沥青,可将低中间相含量沥青中的各向异性与各向同性组分进行分离,可以提高产品的中间相含量,进而达到改善泡沫炭导热性能的目的。
30.其中,优选的,参考图2所示,步骤(4)中热沉降处理后自下而上按照5%~20%质量分数大小切割等质量的样品,得到中间相含量大于95%的中间相沥青。步骤(2)中采用的共炭化剂为四氢萘,步骤(2)和步骤(3)均在高压反应釜中进行,参考图1所示,热沉降装置包括高压反应釜、控制器1、石英玻璃管2、冷却介质4、热电偶5、压力表6和加热介质7,其中,中间相沥青3位于石英玻璃管2的内部,石英玻璃管2的底部包覆有加热介质7,优选的,冷却介质4为水,加热介质7为沙子。示例的,可以采用500ml高压反应釜,预中间相沥青放置在石英玻璃管中,高压反应釜内放入传热介质,将石英玻璃管插入高压反应釜内的传热介质中。
31.优选的,热沉降处理过程的温度为330℃~340℃,热沉降处理时间为4~5小时,热沉降处理的初始压力为1~1.5mpa,热沉降处理过程可以在热沉降装置中进行。本发明实施例采用煤/重油加氢共炼残渣中的甲苯可溶物作为原料制备中间相沥青,不仅原料廉价易得,而且对反应设备没有腐蚀性,使用煤/重油加氢共炼残渣中的甲苯可溶物进行缩聚反应,煤/重油加氢共炼残渣中的甲苯可溶物中含有大量多环芳烃组分,且甲苯可去除残渣中大量的灰分及金属,得到的可溶物中灰分及金属含量经检后测均能满足制备中间相沥青的要求。并且制备过程中使用的甲苯可回收再利用,不会对健康和环境造成危害。
32.本发明实施例的采用煤/重油加氢共炼残渣制备中间相沥青的方法,先对原料进行热缩聚反应,之后在反应釜内进行热沉降,可以有效地将沥青中的各向异性组分沉积在反应器底部。另外,分段测定沉降后沥青的中间相含量,可以有效应对在观察各向异性与各向同性组分之间分界线时模糊不清或找不出分界线的情况,避免因切割不准确而造成中间相含量测定不准的问题。分段处理并统计整体的方法可以大大提高制备结果的准确度,使用沉降处理后得到的中间相沥青制备的泡沫炭泡孔大小均匀,密度小,炭化后导热性差,但石墨化后其导热性能非常好。下面将结合具体的实施例对本发明的一种采用煤/重油加氢
共炼残渣制备中间相沥青的方法进行详细说明。
33.实施例1
34.将印尼煤/催化裂化油浆加氢共炼残渣(煤/重油加氢共炼残渣)经甲苯萃取后的可溶物30g加入到100ml高压反应釜中,并加入10%质量分数的共炭化剂。通入高纯氮气分三次吹扫置换高压反应釜内的空气,充入氮气初始压力为1mpa,进行自升压反应。当高压反应釜内温度升至110℃时启动搅拌并通入冷却水,转速为390r/min,反应温度为400℃,反应时间为6h,得到中间相含量为43%的预中间相沥青。然后将预中间相沥青研磨至100目,在500ml高压反应釜(无搅拌杆)内倒入一定量的细沙,使用耐高温的石英玻璃管进行热沉降。由于样品与石英玻璃管直接接触会发生粘连,不利于后续取出,故在石英玻璃管内垫入一层铝箔,将研磨后的沥青加入石英玻璃管内的铝箔中,石英玻璃管插入沙子中,热沉降装置如图1所示。热沉降处理温度为340℃,热沉降处理时间为5小时,高压反应釜内置换空气后充入氮气,初始压力为1mpa。结束后取出样品按5%质量分数自下而上等质量切割样品,如图2所示,将各区间段样品置于偏光显微镜下观察,得到中间相含量为97%的中间相沥青,光学织构为大片流域型,软化点为280℃。
35.以此中间相沥青为前驱体,当发泡温度为450℃时,制备出的泡沫炭经炭化后导热系数仅为0.24w/(m
·
k),抗压强度可达3.6mpa,密度为0.40g/cm3。石墨化后导热系数可达到48w/(m
·
k),密度仅为0.34g/cm3。中间相沥青的光学结构和中间相含量通过偏光显微镜和imageapro plus分析软件得到,软化点采用针入法测得,导热系数由激光导热仪测得,产品的其他性质测定方法可以采用现有技术,本发明实施例在此不再累述。
36.实施例2
37.将印尼煤/催化裂化油浆加氢共炼残渣经甲苯萃取后的可溶物部分30g加入到100ml高压反应釜中,并加入5%质量分数的共炭化剂。置换高压反应釜内空气后,充入氮气初始压力为0.5mpa,进行自升压反应。当高压反应釜内温度升至110℃时启动搅拌并通入冷却水,转速为390r/min,反应温度为410℃,反应时间为4h,得到中间相含量为35%的预中间相沥青。然后将预中间相沥青研磨至60目,在石英玻璃管中进行热沉降处理,沉降温度为340℃,沉降时间为3小时,高压反应釜内初始压力为常压。结束后取出样品按10%质量分数自下而上等质量切割样品,将各区间段样品置于偏光显微镜下观察。得到中间相含量为95%的中间相沥青,软化点为272℃。当发泡温度为450℃时,制备出的泡沫炭经炭化后导热系数仅为0.21w/(m
·
k),抗压强度为2.6mpa,密度为0.35g/cm3。石墨化后导热系数可达到41w/(m
·
k),密度仅为0.31g/cm3。
38.实施例3
39.将印尼煤/催化裂化油浆加氢共炼残渣经甲苯萃取后的可溶物部分30g加入到100ml高压反应釜中,并加入12%质量分数的共炭化剂。置换高压反应釜内空气后,充入氮气初始压力为2mpa,进行自升压反应。当高压反应釜内温度升至110℃时启动搅拌并通入冷却水,转速为390r/min,反应温度为380℃,反应时间为6h,得到中间相含量为40%的预中间相沥青。然后将预中间相沥青研磨至80目,在石英玻璃管中进行热沉降,沉降温度为320℃,沉降时间为6小时,高压反应釜内初始压力为1.5mpa。结束后取出样品按5%质量分数自下而上等质量切割样品,将各区间段样品置于偏光显微镜下观察。得到中间相含量为96%的中间相沥青,光学织构为大片流域型,软化点为275℃。当发泡温度为450℃时,制备出的泡
沫炭经炭化后导热系数仅为0.22w/(m
·
k),抗压强度为3.2mpa,密度为0.38g/cm3。石墨化后导热系数可达到45w/(m
·
k),密度仅为0.33g/cm3。
40.本发明提供的一种采用煤/重油加氢共炼残渣制备中间相沥青的方法,以甲苯对煤/重油加氢共炼残渣进行萃取,得到的甲苯可溶物在高压反应釜内进行热缩聚反应后得到一定中间相含量的预中间相沥青,由于预中间相沥青中含有较多各向同性组分,对后续制备的材料性能会产生较大影响,需要对各向异性与各向同性组分进行分离,通过在高压反应釜内进行热沉降处理,使底部沥青的组成更加均一,各向异性组分含量高,通过采用热缩聚工艺结合热沉降工艺将低中间相含量沥青中的各向异性与各向同性组分进行分离,提高产品的中间相含量,进而达到改善中间相沥青制备的泡沫炭导热性能的目的。
41.显然,本领域的技术人员可以对本发明实施例进行各种改动和变型而不脱离本发明实施例的精神和范围。这样,倘若本发明实施例的这些修改和变型属于本发明权利要求及其等同技术的范围之内,则本发明也意图包含这些改动和变型在内。