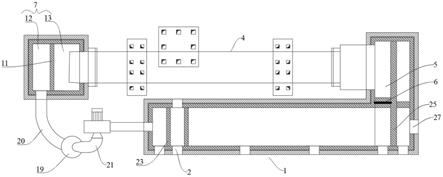
1.本实用新型属于活性炭及兰炭生产领域,具体涉及一种干馏热解法节能环保型炭化装置、工艺。
背景技术:2.活性炭是一种具有丰富孔隙结构和巨大比表面积的碳质吸附材料,它具有吸附能力强、化学稳定性好、力学强度高,且可方便再生等待点.被广泛应用于工业、农业、国防、交通、医药卫生、环境保护等领域,其需求量随着社会发展和人民生活水平提高,呈逐年上升的趋势,尤其是随着环境保护要求的日益提高,使得国内外活性炭的需求量越来越大,逐年增长。 活性炭产品种类很多,按生产原料不同可分为;煤基活性炭、木质活性炭、果壳活件炭和合成活性炭等。为了保护日益减少的森林资源,保护人类的生存环境,木质活性炭生产受到越来越多的限制,在我国活性炭总产量中所占比重逐渐下降,而以煤为原料生产的煤基活性炭所占比重逐渐上升。
3.在活性炭的生产设备领域,中国实用新型cn201620744149.5 公开了一种新型连续回转干馏热解炭化炉包括炭化炉进料仓、炭化炉炉体、燃烧室和炭化炉出料仓,所述的炭化炉炉体的进 口端与所述的炭化炉进料仓的出口端通过密封装置连接,所述的炭化炉炉体的出口端与所 述的炭化炉出料仓的进口端通过密封装置连接,其特征在于,所述的炭化炉炉体的内部设 置一内置辐射热管,所述的内置辐射热管穿过炭化炉炉体,同时,完全或部分穿过炭化炉出料仓。所要解决的技术问题是实现炭化温度较稳定的控制。
4.中国实用新型cn202121677267.6公开了一种烟气充分循环利用的炭化炉装置,包括:炭化炉和烟气循环系统,炭化炉设置有炭化室,炭化室底部设置有炉排,炉排位置炭化室侧壁设置有炉排口,炭化室侧壁设置有进料口,炭化室顶部设置有集烟罩,集烟罩连接有烟气循环管,烟气循环管分为两个支路,一条支路连通第一循环管,另一条支路连通第二循环管,第二循环管连接有脱硫塔,化室下方设置有燃烧室,第一循环管通入燃烧室内,炭化炉连接有压力控制器,炭化炉底盘设置有支撑架。第一循环管用于烟气运输进入燃烧室进行燃烧产生热能,第二循环管连接的脱硫塔对烟气进行脱硫后排出。所要解决的技术问题是现有炭化炉在炭化过程中产生的浓烟对环境的污染问题,又解炭化炉决了炭化炉所需的热能问题,充分做到了自供自给,提高了炭化过程的连续性、经济型,使其变废为宝,既减轻了烟气对环境的污染,又降低了炭化过程中的生产成本。
5.现有技术有效解决了活性炭生产过程中的温度控制以及烟气循环利用的问题,然而,在中国实用新型cn202121677267.6中,进料口与出料口呈竖直位置,无法做到持续生产,进而不能满足活性炭的生产效率要求,并且烟气循环过程中会有大量的灰尘、焦油需要处理。
技术实现要素:6.本实用新型索要解决的技术问题是,1.优化活性炭生产过程中尾气循环利用的各
个环节,包括灰尘、焦油的处理,通过燃烧炉炉膛的改进使尾气燃烧更加充分。
7.2.减少炭化炉中着火现象对炭化后物料表面的损毁。
8.3.实现炭化炉内持续供应物料,持续生产,提高炭化生产效率。
9.为了解决上述问题本实用新型提供了一种新的技术方案:一种干馏热解法节能环保型炭化装置,包括闭环连通的焚烧炉与炭化炉,焚烧炉末端的另一支路连接余热锅炉;
10.还包括:布料仓,布料仓设置于炭化炉的前端;卸料仓,卸料仓设置于炭化炉的末端;
11.循环管道,循环管道用于连接布料仓与焚烧炉的前端;引风机,引风机设置于循环管道上;其中布料仓内设置有集灰室,循环管道上设置有焦油沉降室。
12.进一步地,焚烧炉尾端设置有回转连接部,即焚烧炉总体呈“l”型,回转连接部用于连通炭化炉的末端,连接处采用密封件进行密封。回转连接部与焚烧炉的通道内设置有闸门。闸门用于控制炭化炉的进气量,进而控制炭化炉的炉内温度。
13.进一步地,炭化炉外部设置有齿轮带与支撑台,齿轮带与驱动装置连接。在生产过程中炭化炉持续滚动翻转。
14.进一步地,炭化炉的前端通入布料仓,并且采用密封件密封连接,炭化炉的进料口连接进料管,进料管上端连接滚筒给料装置,滚筒给料装置连接料斗滚筒给料装置。布料仓内设置有竖直的第一隔墙,第一隔墙顶部与布料仓的顶部存在空隙,第一隔墙将布料仓分隔为集灰室和布料室,第一隔墙两侧分别设置有第一斜坡与第二斜坡,第一斜坡与第二斜坡分别向布料仓的两个侧壁倾斜,第一斜坡与第二斜坡的底部分别设置有第一排灰管道与第二排灰管道,第一排灰管道与第二排灰管道贯通布料仓的侧壁,并且分别连接第一水封槽与第二水封槽。第一水封槽与第二水封槽可以是连通的,烟气进入布料仓后通过第一个强顶部的孔隙到隔墙的另一侧。而一部分灰尘沿第一隔墙、斜坡从排灰管道排出,排出的灰可回收利用。此处需要说明的是,集灰室与布料室均具有一定的除灰作用,在此基础上将进料管通入的一侧命名为布料室。
15.进一步地,集灰室的侧壁上设置有第一连接孔,连接孔的位置低于第一隔墙的高度,并且高于第第一斜坡或第二斜坡的顶部,连接孔用于连接循环管道。烟气沿第一连接孔进入循环管道。
16.进一步地,还包括焦油沉降室,循环管道包括用于连接布料仓与焦油沉降室的第一段循环管道和用于连接焦油沉降室与焚烧炉的第二循环管道,焦油沉降室包括圆筒形的上部与倒锥形的下部,倒锥形下部设置有废料出口,废料出口连接第三水封槽,排出的废料可回收利用,上部侧壁上设置第二连接孔,第一连接孔与第二连接孔通过第一段循环管道连通;
17.上部的顶部设置有第三连接孔,第三连接孔与焚烧炉前端通过第二循环管道连通,引风机设置于第二循环管道上。烟气低进高出,相当于二次除尘,并且焦油等胶状成分也再次沉降。
18.进一步地,焚烧炉的前端设置有第四连接孔,第四连接孔用于连通第二循环管道第四连接孔设置于焚烧炉前端的下部,在焚烧炉内部靠近第四连接孔一侧设置有竖直的第二隔墙,隔墙上开设第一拱形孔,第一拱形孔位于第二隔墙的下部。第一拱形孔设置于第二隔墙的下部,有利于烟气沿焚烧炉的下方进入炉膛,进而有利于有机挥发份的充分燃烧。
19.进一步地,第一拱形孔的直径为d,高度为h,第二隔墙宽度为d,高度为h;
20.0.5d≤d≤0.8d,0.15h≤h≤0.3h。
21.进一步地,焚烧炉尾端竖直设置有第三隔墙,第三隔墙延伸至回转连接部内,并且与回转连接部侧壁封闭连接。
22.进一步地,第三隔墙与回转连接部靠近焚烧炉一侧侧壁之间形成烟气通道。闸门设置于烟气通道内。
23.进一步地,第三隔墙上开设第二拱形孔,第二拱形孔与与焚烧炉的炉膛正对,第二拱形孔所在出口为连接余热锅炉的另一支路。
24.进一步地,焚烧炉末端开设有烟气出口,烟气出口和第二拱形孔中间设置有sncr脱硝装置,烟气出口处设置有scr脱硝装置,对排出烟气进行脱硝处理。
25.进一步地,还包括除尘设备、排风设备、脱硫设备,scr脱硝装置后依次连接余热锅炉、除尘设备、排风设备以及脱硫设备。排风设备不仅用于该装置的尾气排出并且可以与引风机、闸门协同作用共同控制炭化炉内的进气量。
26.本实用新型的有益效果为,
27.1.闭环连接的焚烧炉与炭化炉内的烟气通过引风机实现循环,能够凭借自身燃烧提供热源,不需要再依靠外热源即可进行炭化生产。
28.2.生产系统负压控制,控制烟气流量和流速及炭化温度,消除炭化烟气无组织排放。
29.3.通过改进焚烧炉炉膛结构,使炭化炉内的有机挥发份燃烧更加充分,在提高了尾气利用率的同时,减少了系统末端的尾气排放,更加环保。
30.4.布料仓内集灰室、排灰管道以及焦油沉降室的设置,达到一定的除尘效果,对炭化所产生的尾气进行了初步处理,与此同时,减少了循环过程中流入炭化炉的杂质含量,进一步提升了成品的质量。
31.5.对焚烧炉末端通入余热锅炉的烟气进行scr&sncr联合脱硝,并且在排放末端进一步脱硫处理,实现烟气净化能够达标排放。
附图说明
32.图1为本实用新型实施例的俯视示意图,
33.图2为本实用新型实施例的焚烧炉侧视剖面示意图;
34.图3为图2中a-a切面示意图;
35.图4为图2中b-b的切面示意图;
36.图5为图2中c-c的切面示意图;
37.图6为本实用新型实施例中炭化炉及布料仓的侧视剖面图;
38.图7为图6中a-a的切面示意图;
39.图8为图6中b-b的切面示意图。
40.图中:1、焚烧炉;2、燃料喷射口;3、回转连接部;4、炭化炉;5、烟气通道;6、闸门;7、布料仓;8、进料管;9、滚筒给料装置;10、料斗;11、第一隔墙;12、集灰室;13、布料室;14、第一斜坡;15、第二斜坡;16、第一排灰管道;17、第二排灰管道;18、第一连接孔;19、焦油沉降室;20、第一循环管道;21、第二循环管道;22、第四连接孔;23、第二隔墙;24、第一拱形孔;
25、第三隔墙;26、第二拱形孔;27、烟气出口;28、sncr脱硝装置。
具体实施方式
41.如图1所示:一种干馏热解法节能环保型炭化装置,包括闭环连通的焚烧炉1与炭化炉4,所述焚烧炉1末端的另一支路通过烟气出口27连接余热锅炉;
42.如图2所示:焚烧炉1内为拱形的内腔,内腔铺设有蓄热体,焚烧炉1的前端开设有燃料喷射口2,尾端设置有回转连接部3,即焚烧炉1总体呈“l”型,回转连接部3用于连通炭化炉4的末端,并且炭化炉4末端与回转连接部3之间设置有卸料仓,卸料仓卸料仓仓体为筒形结构,其底部设置有星型卸料器,炭化炉4末端与卸料仓连接处采用密封件进行密封。回转连接部3与焚烧炉1的烟气通道5内设置有闸门6。闸门6用于控制炭化炉4的进气量,进而控制炭化炉4的炉内温度。
43.如图6所示:炭化炉4外部设置有齿轮带与支撑台,齿轮带与驱动装置连接。在生产过程中炭化炉4持续滚动翻转。
44.炭化炉4的前端通入布料仓7,并且采用密封件密封连接,炭化炉4的进料口连接进料管8,进料管8上端连接滚筒给料装置9,滚筒给料装置9连接料斗10滚筒给料装置。布料仓7内设置有竖直的第一隔墙11,第一隔墙11顶部与布料仓7的顶部存在空隙,第一隔墙11将布料仓7分隔为集灰室12和布料室13,第一隔墙11两侧分别设置有第一斜坡14与第二斜坡15,第一斜坡14与第二斜坡15分别向布料仓7的两个侧壁倾斜,第一斜坡14与第二斜坡15的底部分别设置有第一排灰管道16与第二排灰管道17,第一排灰管道16与第二排灰管道17贯通布料仓7的侧壁,并且分别连接第一水封槽与第二水封槽。第一水封槽与第二水封槽可以是连通的,烟气进入布料仓7后通过第一个强11顶部的孔隙到隔墙的另一侧。而一部分灰尘沿第一隔墙11、斜坡从排灰管道排出。
45.集灰室12的侧壁上设置有第一连接孔18,连接孔的位置低于第一隔墙11的高度,并且高于第第一斜坡14或第二斜坡15的顶部,连接孔用于连接循环管道。烟气沿第一连接孔18进入循环管道。
46.还包括焦油沉降室19,循环管道包括用于连接布料仓7与焦油沉降室19的第一段循环管道和用于连接焦油沉降室19与焚烧炉1的第二循环管道21,循环管道上分别设置内保温层与外保温层,内保温层采用耐火材料,外保温层采用岩棉与铁皮包裹,焦油沉降室19包括圆筒形的上部与倒锥形的下部,倒锥形下部设置有废料出口,废料出口连接第三水封槽,上部侧壁上设置第二连接孔,第一连接孔18与第二连接孔通过第一段循环管道连通;
47.上部的顶部设置有第三连接孔,第三连接孔与焚烧炉1前端通过第二循环管道21连通,引风机设置于第二循环管道21上。烟气低进高出,相当于二次除尘,并且焦油等胶状成分也再次沉降。
48.如图2-图5所示:焚烧炉1的前端设置有第四连接孔22,第四连接孔22用于连通第二循环管道21第四连接孔22设置于焚烧炉1前端的下部,在焚烧炉1内部靠近第四连接孔22一侧设置有竖直的第二隔墙23,隔墙上开设第一拱形孔24,第一拱形孔24位于第二隔墙23的下部。第一拱形孔24设置于第二隔墙23的下部,有利于烟气沿焚烧炉1的下方进入炉膛,进而有利于有机挥发份的充分燃烧。
49.第一拱形孔24的直径为d,高度为h,第二隔墙23宽度为d,高度为h;0.5d≤d≤
0.8d,0.15h≤h≤0.3h。
50.焚烧炉1尾端竖直设置有第三隔墙25,第三隔墙25延伸至回转连接部3内,并且与回转连接部3侧壁封闭连接。
51.第三隔墙25与回转连接部3靠近焚烧炉1一侧侧壁之间形成烟气通道5。闸门6设置于烟气通道5内。
52.第三隔墙25上开设第二拱形孔26,第二拱形孔26与与焚烧炉1的炉膛正对,第二拱形孔26所在出口为连接余热锅炉的另一支路。
53.焚烧炉1末端开设有烟气出口27,烟气出口27和第二拱形孔26中间设置有sncr脱硝装置28,烟气出口处设置有scr脱硝装置。
54.还包括除尘设备、脱硫设备, scr脱硝装置后依次连接余热锅炉、除尘设备、排风设备以及脱硫设备,对排出烟气进行脱硝处理。
55.还包括除尘器、排风机、脱硫塔,联合脱硝装置28后依次连接余热锅炉、除尘设备、排风设备以及脱硫设备。排风设备不仅用于该装置的尾气排出并且可以与引风机、闸门6协同作用共同控制炭化炉4内的进风量。
56.此外焚烧炉1炉膛基座为混凝土,外层为普通红砖,内层为耐火砖,第一隔墙11、第二隔墙23、第三隔墙25均为硅藻土砖;布料仓7外层为普通红砖,内层为耐火砖,斜坡内为耐火填充物。
57.焚烧炉1内部设置有蓄热体,焚烧炉1在点炉阶段向内部喷入燃料如甲醇、天然气,煤粉等,引风机运行后炭化炉内产生负压,闸门6开启后,焚烧炉1内产生高温烟气进入炭化炉4,物料温度提升进而产生有机挥发份,有机挥发份通过引风机引入焚烧炉1后再次燃烧持续提供热源,即炭化炉4尾气经过引风机由尾气进口送入焚烧炉1燃烧,燃烧后的高温烟气进入炭化炉4产品通道加热物料进行炭化,焚烧炉温度达到800℃以上即可停止外部热源供给,依靠自身烟气燃烧提供炭化所需温度。因此不再需要提供外热源,减少了能源损耗。
58.炭化炉4内设置温度传感器,实时监测炉内温度,当温度超过或低于炭化所需温度时通过引风机、闸门6、排风设备协同调整循环气量进而调节炭化炉内温度,将炭化炉4内温度控制在250℃—800℃。
59.余热锅炉连接有蒸汽管道,蒸汽管道通入卸料仓末端,用于向炭化炉内提供蒸汽,通入的蒸汽能够减少炭化炉4内着火现象,提高成品的品质。
60.炭化炉4倾斜设置,即进料端高于卸料端,并且其内壁设置有螺旋叶片,通过旋转炭化炉4实现炉内输料,炭化炉4持续运转,成品通过卸料口卸下,布料仓7持续供料,实现了炭化炉4的连续生产,提高了活性炭生产效率。