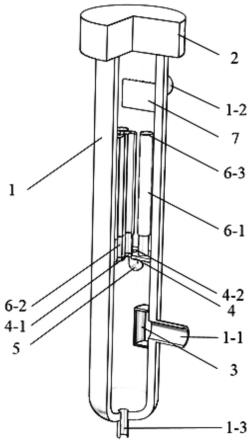
1.本发明属于油气田设备领域,涉及一种储气库注气压缩机除油器及其工作方法。
背景技术:2.储气库由于具有调峰能力强、投资成本低、储量大及安全系数高等优势,是目前天然气调峰的首要方式。
3.注气环节中,进站天然气首先进入过滤分离器,去除粒径在1μm以上较为细小的固体颗粒杂质和较大液滴,通过两级处理后达到气质要求的天然气进入压缩机进行加压。压缩机工作时,会向气缸内注入润滑油进行润滑和密封,这些润滑油会被排出的天然气携带到压缩机下游管道。增压后的天然气在输送至井口的过程中,随着温度降低润滑油会逐渐析出,附着在沿程的管道内壁上,导致管道直径变小,注采井能力变小,严重影响注采井生产,因此在注气压缩机出口处,需要使用高效的除油器对排气端的含油天然气进行分离过滤。
4.注气压缩机除油器所处理的油气混合物流量大、压力高,其通常为立式结构,由上下两部分组成。底部为初级分离腔,油气混合物首先到达该部分,通过惯性碰撞分离出直径为10μm以上的较大油滴。除油器中上部有规整排布的滤芯,油气混合物以较慢速度进入滤芯后,通过在纤维表面的聚结再分离,将未在初分离设备中实现分离的微小油滴进行进一步脱除。
5.除油器的效率不仅对润滑油的利用率、滤芯的使用寿命等有重要影响,气体的纯净度还对下游管道以及其他设备的平稳运行起到至关重要的作用。但现有除油器除油效率低,滤芯需频繁更换,且下游管道上仍会聚集润滑油,甚至注采井中也会有润滑油进入,对整个储气库的安全生产带来极大的困扰。
技术实现要素:6.为解决现有技术中存在的问题,本发明的目的在于提供一种储气库注气压缩机除油器及其工作方法,本发明能够增强初分离腔内的碰撞分离效率,并且改善进入滤芯的流场均匀性,从而使得除油器的整体效率得到大幅提升,运行成本降低。
7.本发明采用的技术方案如下:
8.一种储气库注气压缩机除油器,包括除油器本体,除油器本体的筒体的内壁上在与除油器本体的入口管的出口相对的位置设有入口挡板,入口挡板为一u型结构,入口挡板的底边与入口管的出口正对,入口挡板的两个翼边分别位于入口管出口的上下两侧并与筒体连接,入口挡板底边水平方向的两侧与筒体内壁之间具有供流体流过的通道。
9.优选的,所述入口挡板的底边的形状为内凹弧形,入口管的出口与入口挡板底边的底部正对。
10.优选的,所述入口挡板的底边的形状为一段圆柱面,该圆柱面所在圆柱的轴线与筒体的轴线平行。
11.优选的,所述圆柱面的直径与筒体的直径相同。
12.优选的,入口挡板底边的宽度不小于入口管的直径,入口挡板底边的高度不小于入口管的直径。
13.优选的,入口挡板两侧的通流面积均与入口管的截面积相等。
14.优选的,筒体的内腔在除油器本体的出口管的位置设有整流板。
15.优选的,筒体的内腔设有支撑板,支撑板位于入口管出口的上方,支撑板上开设有导油管通孔和若干滤芯通孔,支撑板的下部在导油管通孔处连接有导油管,导油管的出口延伸至筒体的外部;支撑板的上部在每个滤芯通孔处分别连接有除油过滤器,筒体的底部设有排污管。
16.优选的,所述除油过滤器包括支撑管和滤芯,支撑管的一端与滤芯通孔连通,支撑管的另一端与滤芯的连接。
17.本发明所提出的储气库注气压缩机除油器在储气库注气压缩机排气端的具体实施方式如下:
18.压缩机排气端来流的压缩天然气-润滑油混合物由入口管进入除油器筒体;
19.气液混合物进入后,正向撞击弧形内凹挡板,混合物中较大粒径的油滴附着于挡板内壁,在挡板内壁上聚合铺展形成油膜后沿挡板流下,汇聚于下包板后,从两侧滴落流下,到达除油器筒体底部;
20.气液混合物碰撞竖直挡板后分为两股,从挡板两侧流出,沿着弧形内壁面运动一定距离后汇合于初分离腔内部,随后顺着压差方向向上流动;
21.在初分离腔中运动的油气混合物不断与筒体壁面碰撞接触,因此其中的油滴不断在筒体壁面上汇聚,其聚集形成液膜后沿着筒体壁面流到筒体底部。初分离腔底部的润滑油液积累到一定量后,通过排污控制操作实现排污。
22.本发明如上所述的储气库注气压缩机除油器的工作方法,包括如下过程:
23.压缩机排气端的天然气-润滑油混合流体从入口管进入筒体中,随后天然气-润滑油混合流体冲击入口挡板的底边,入口挡板的底边内壁面上汇聚附着形成液膜,液膜在重力的作用下不断沿着入口挡板的底边向下运动并流动到入口挡板的下翼边;同时,天然气-润滑油混合流体从入口挡板与筒体内壁之间通道流出,并沿筒体壁面继续运动,在天然气-润滑油混合流体沿筒体壁面运动过程中,天然气-润滑油混合流体再次在筒体壁面上发生碰撞分离,同时天然气-润滑油混合流体的侧向运动使入口挡板下翼边上积聚的油液从入口挡板下翼边的两侧滴落,随后沿筒体壁面运动的天然气-润滑油混合流体绕流后向上方运动。
24.本发明具有如下有益效果:
25.本发明储气库注气压缩机除油器在除油器本体的入口管的出口位置加装有u型的入口挡板,该入口挡板可以实现油气混合物的初次碰撞分离,并将除油器本体初分离腔内的流场改变为从两侧环绕进入筒体的形式,增强了油气混合物在初分离腔内的绕流,从而液滴与筒体内壁面的碰撞机会增加,初分离效率得到提升。
26.进一步的,入口挡板的底边的形状为内凹弧形,入口挡板的内凹形设计可以实现较低的湍动能,因此腔体内流场较为均匀,从而进入除油器本体几根滤芯的流场具有较高的均匀性,可以发挥滤芯整体的最大效率,使得排出气体更加洁净。
附图说明
27.图1为本发明储气库注气压缩机除油器的整体结构图。
28.图2为本发明储气库注气压缩机除油器的内部剖视图。
29.图3为本发明中入口挡板的具体结构示意图。
30.图4为本发明中入口挡板的安装尺寸示意图。
31.图5为本发明中入口挡板不同安装距离下入口管中轴线水平截面位置的速度云图。
32.图6为本发明中入口挡板不同安装距离下滤芯入口处的速度云图。
33.图中:1-筒体,1-1-入口管,1-2-出口管,1-3-排污管,2-顶盖,3-入口挡板,3-1-竖直挡板,3-2-上包板,3-3-下包板,4-支撑板,4-1-滤芯通孔,4-2-导油管通孔,5-导油管,6-1-滤芯,6-2-支撑管,6-3-滤芯上盖,7-整流板。
具体实施方式
34.在下文中,将参考附图对本技术的具体实施例进行详细地描述,依照这些详细的描述,所属领域技术人员能够清楚地理解本技术,并能够实施本技术。在不违背本技术原理的情况下,各个不同的实施例中的特征可以进行组合以获得新的实施方式,或者替代某些实施例中的某些特征,获得其它优选的实施方式。
35.针对现有除油器除油效率低,滤芯需频繁更换,且下游管道上仍会聚集润滑油,甚至注采井中也会有润滑油进入,对整个储气库的安全生产带来极大的困扰。经过研究发现,造成该现象的主要原因是,现有的储气库注气压缩机除油器设计不合理,初分离区域为简单的空腔,油气混合物从入口进入后径直对撞筒体壁面,随后向上折流进入滤芯中,混合物在初分离腔内绕流不充分,与壁面接触机会小,碰撞分离效率低下,滤芯载荷高。并且到达滤芯入口的流场均匀性差,使得滤芯整体难以发挥出最高的效率,滤芯易拥堵,更换周期短,在影响分离效率的同时也造成资源浪费。有鉴于此,本发明提供了以下储气库注气压缩机除油器。
36.具体的,如图1~图4所示,本发明储气库注气压缩机除油器主要包括筒体1和顶盖2,顶盖2通过螺纹与密封垫固定于筒体1上方,对整个除油器起到密封作用;筒体1的外部下方焊接有入口管1-1,筒体1的上部焊接有出口管1-2,入口管1-1与出口管1-2成90
°
分布,筒体1底部中心焊接有排污管1-3,入口管1-1、出口管1-2和排污管1-3均与筒体1的内腔连通。筒体1的内部有入口挡板3,入口挡板3整体为一u形结构,其包括与入口管正对的竖直挡板3-1(即u型结构的底边),以及与筒体通过焊接相连的上包板3-2(即u型结构的上翼边)与下包板3-3(即u型结构的下翼边)。竖直挡板为内凹弧形(图3所示的竖直挡板为一段圆柱面,竖直挡板所在圆柱面的轴线与筒体1的轴线平行),弧形半径r与筒体1半径一致,挡板宽度w不严格限制,只需能覆盖入口管1-1的直径2r即可。挡板高度h亦不做严格限制,只需在纵向方向上能覆盖入口管1-1的直径2r即可,可比挡板宽度w略大。挡板与筒体内壁面的距离d通过计算求得,其计算原理为入口挡板3两侧的通流面积均与入口管的截面积相等,则d的具体计算公式为:
37.38.弧形内凹挡板与筒壁的距离经过合理计算求得,其应基于入口管内径,并根据所选挡板高度与宽度计算所得,本发明设计完成后通过流场分析证明了所设计挡板与入口间距离的合理性。
39.本发明入口挡板3为上下半包结构,限制气体从挡板两侧流出,则流出的气液混合物不会干扰挡板壁面上向下流动的液膜,难于形成卷吸飞溅,避免了由此造成的分离效率的损失。上下包板的前侧面均焊接于筒体壁面,可以很好的连接挡板与筒体为一体,起到较好的稳固作用,使得竖直挡板不会在长期运行过程中掉落或变形。因此入口挡板3结构简单易加工,因此实用性极高。
40.筒体1内部中部焊接有支撑板4以承托滤芯。支撑板4位于入口管1-1和出口管1-2之间的位置且相对更靠近入口管1-1,支撑板4至出口管1-2之间的距离要满足安装过滤器的需求,支撑板4上开有六个滤芯通孔4-1以及靠近筒体侧边的一个接通导油管5的导油管通孔4-2。每个滤芯通孔4-1上方安装一根支撑管6-2,支撑管6-2上部安装有滤芯6-1,滤芯6-1顶部具有防止气体泄漏的滤芯上盖6-3。导油管通孔4-2与导油管5相连,导油管5连通到筒体外部。筒体1出口管1-2前加装平直整流板7。本发明提供的除油器为初分离与精分离上下一体的立式结构,因此可以处理高压大排量的油气混合物,适用于储气库注气压缩机。
41.本发明储气库注气压缩机除油器在储气库注气压缩机中应用时,具体的除油过程如下:
42.压缩机排气端的高压天然气-润滑油混合物从入口管1-1进入筒体1中,随后气液混合物冲击竖直挡板3-1。上包板3-2限制流体向上方运动,防止气流直接向上冲击进入滤芯而造成带液量过大。下包板3-3限制冲击挡板后的气液混合物从下方向上折流运动。由于气液混合物持续撞击竖直挡板3-1时,混合物中较大粒径的油滴附着于挡板内壁,挡板内壁面上会汇聚附着形成液膜,液膜在重力的作用下不断沿着竖直挡板向下运动,气流如果从挡板下方向上折流运动,会卷吸滴落的液滴再次进入气相流场中,从而造成液体夹带,使得滤芯的负荷增大,因此下包板可以有效阻止液滴卷吸夹带的发生。在上下包板的限制下,撞击竖直挡板3-1后的气液混合物被迫从挡板3两侧流出,沿筒体壁面继续运动,在此过程中,气液混合物再次在筒体壁面上发生碰撞分离。并且气体的侧向运动可以迫使下包板3-3上积聚的油液从两侧滴落,强化排液,这些都可以提高初分离腔(指的是筒体1中支撑板4以下的腔室)的效率。随后沿筒体壁面运动的流体在初分离腔体内进一步绕流后向上方运动。
43.从入口挡板3上以及初分离腔侧壁上流下的油液汇聚到筒体1的底部,当油液积聚到一定量后,通过排污控制从排污管1-3中排出。
44.在初分离腔中实现较大粒径油滴的分离后,携带有较小油滴的气液混合物向上运动,从滤芯通孔4-1中进入支撑管6-2,随后进入滤芯6-1的中通管中,滤芯顶部有滤芯上盖6-3,防止气体泄漏,迫使气液混合物在滤芯中内进外出,借助滤芯纤维实现分离。气液混合物在滤芯纤维上聚结,在重力作用下,汇聚的油液沿滤芯6-1表面导流,向下流动到支撑板4上,分离的油液积累到一定量后,从导油管通孔4-2进入导油管5中,沿导油管5排出到筒体1外。
45.从滤芯6-1侧面流出的净化后的高压天然气进一步向上运动,经过整流板7形成较为平稳的气流,然后从出口管1-2排出,进入下游管道。
46.挡板弧度与筒体一致时,根据对称性能得到较为均一、稳定的流场,进入滤芯的流
场不均匀度较小,从而滤芯整体的效率较高。挡板的宽度和高度则是以能完全覆盖入口管直径为最佳,既可以对所有来流进行初次碰撞分离,同时也不应太宽太长影响后方流动。在这些参数确定后,本发明提出了挡板到筒体的距离根据侧边出口的通流面积与入口管截面积相等的原则设计,这样既能起到较好的导流作用,同时流场的流速也较为合理。
47.针对权利要求中所提出的挡板距离设计原则,本发明根据一特定除油器尺寸结构进行了计算,并对几种挡板距离下的初分离腔结构进行了流场分析。研究中的除油器入口管半径r为80mm,初步选定的挡板高度h为320mm,宽度w为200mm,则根据公式在挡板结构尺度一定的情况下,模拟研究了几组不同挡板距离d的流场结果,入口管中轴线水平截面和滤芯入口处的速度场分布分别如图5、图6所示。可以看出,原腔体中气液混合物来流进入入口管后径直向前运动冲击筒体壁面,随后向上方流动,与壁面的碰撞不充分。而应用本发明所提出的入口弧形挡板结构后,流体从挡板两侧流出,沿壁面运动到入口对侧后,两股流体相遇并汇聚进入筒体中部,随后才向上运动,因此混合物中的液滴可与壁面充分碰撞,且在入口对侧相遇的两股流体也会形成一定的冲击作用,在该作用下,小液滴会聚并成为更大的液滴,从而易于分离。
48.有/无挡板以及几组挡板距离下初分离腔的分离效率、压降等结果汇总于表1,可以看出,本发明所提出的挡板到筒体距离的设计准则具有较好的综合表现。
49.表1
[0050][0051]
从上述方案可以看出,本发明很好的解决了以下问题:储气库注气压缩机除油器分离效率低,排气端仍含有大量油滴,其在运动到下游管道后冷凝析出,附着于管壁,严重影响注采井生产。解析其具体原因为,初分离腔结构不合理,气液混合物绕流不充分,气液分离效率低下,导致滤芯处过滤负荷过高,且进入滤芯的流场均匀性较差,滤芯无法实现最高效的过滤性能,从而失效快,更换周期短,除油器运行成本高昂。