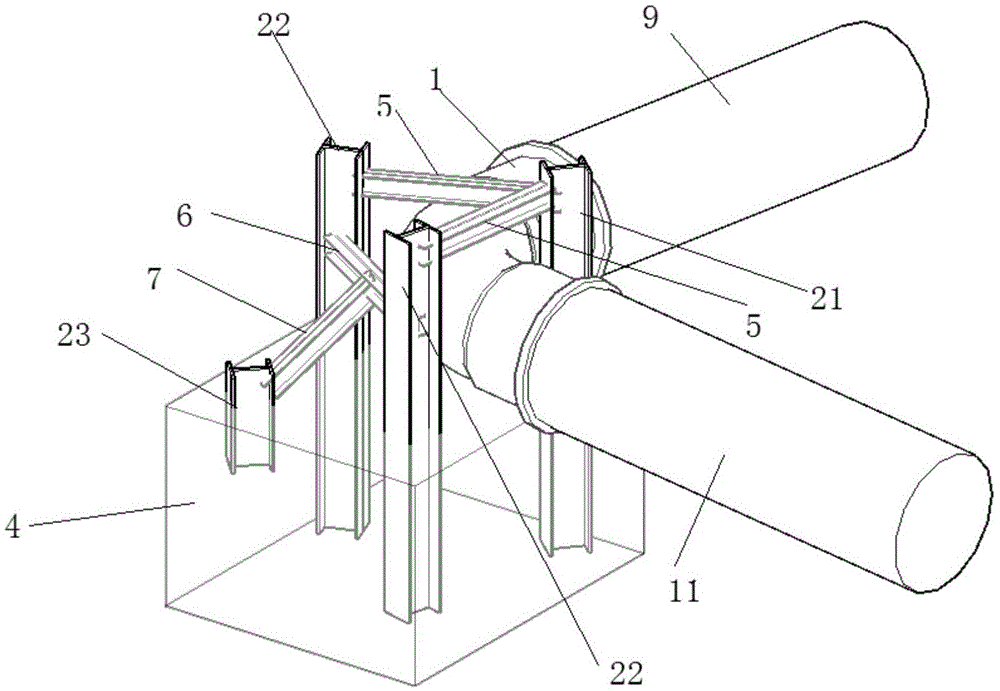
本发明涉及管道改迁施工的
技术领域:
,具体涉及一种弯头接入点临时止推块及其施工方法和设计方法。
背景技术:
:卡塔尔东部高速连接多哈国际机场与工业区,由中交集团旗下的中国港湾总承包,属一带一路沿线工程和中交集团的重点关注项目。本项目地所在卡塔尔位于波斯湾西岸,属典型的中东热带沙漠气候,境内无天然淡水,生活用水全部依靠海水淡化工程提供,通过压力管网输送全国。该项目需要改扩建约32公里市政自来水管线,对于承插型压力管道的弯头部位,按照压力和管径大小,需配置足够重量的止推块(又名镇墩)。输水管道的新建、改线、扩线工作,具有管道流量大,影响用户多,停水施工窗口期短,开挖切割准备工作复杂,大型设备管理要求高等特点,必须保证一次成功。特别是对于直线改折线的工程,接入点止推块在管道通水加压后不能发生大的位移,承插式接头不发生扭曲和脱出(位移需小于lcm),止推结构必须安全可靠。对1200腿及以上的大直径压力管道,对接入止推方案设计和工艺是该类工程施工的重难点。国外对于该类结构物的设计文献及施工指导手册多数为基本工艺设计,国内目前对长距离普通压力输水管线的止推块设计施工,对复杂条件下的接入改线止推方案的研究相对较少。技术实现要素:本发明的目的就是针对现有技术的缺陷,提供一种弯头接入点临时止推块及其施工方法和设计方法,保证前期管道受力稳定,又能够保持后续镇墩浇筑的整体稳定性,同时因为提前施工临时止推结构,节省了断水时间及空间。本发明提供了一种用于压力管道改迁工程的弯头接入点临时止推块,其特征在于:它包括位于弯头接入点下方的嵌入式基座,基座的上表面垂直预埋有一根第一型钢和两根第二型钢,其中第一型钢位于弯头接入点管道的内侧,两根第二型钢分别对称设置于弯头接入点管道外侧,所述一根第一型钢和两根第二型钢呈三角分布,弯头接入点管道位于三根型钢之间;其中第一型钢的顶端与两根第二型钢的顶端之间分别焊接有第一连接型钢,两根第二型钢的之间设置有与基座上表面平行的第二连接型钢,第一连接型钢位于弯头接入点管道的上方,第二连接型钢位于弯头接入点管道中部外侧;还包括第三型钢和斜撑型钢,第三型钢垂直预埋于基座上表面,第三型钢位于第一型钢和两根第二型钢形成的三角结构外侧;斜撑型钢连接于第三型钢靠近于基座上表面的端部和第二连接型钢之间。上述技术方案中,第一型钢位于弯头接入点的圆心处。上述技术方案中,第三型钢位于弯头接入点的角平分线上。上述技术方案中,第二型钢的腹板与弯头接入点的圆心连线重合。上述技术方案中,两个第二型钢和第二连接型钢与弯头管体接入点之间设置有马鞍支座,所述马鞍支座的圆弧面与弯头接入点管道外壁相配合。上述技术方案中,第二型钢与弯头接入点管道拐点处的切线相平行。上述技术方案中,两根第二型钢与弯头接入点管道外侧的基座上表面之间于设置有斜撑,所述斜撑一端焊接在垂直对应的第二型钢上,另一端焊接在混凝土中外侧基座表面预埋的短型钢上,以辅助支撑第二型钢。本发明提供了一种用于压力管道改迁工程的弯头接入点临时止推块的设计方法,其特征在于包括以下步骤:第一步,作弯头接入点平面位置图,确定连接弯头和现有管道的位置尺寸关系;第二步,判断弯头的圆心位置o,确定上述圆心位置为第一型钢的安装位置h0;第三步,作弯头的角平分线,确定第三型钢的安装位置h1在弯头外侧的角平分线上;第四步,确定第一根第二型钢h2的位置,保证第二型钢紧靠现有管道,并使腹板方向与拟建弯头管壁相切,以使h2和圆心连线与oh1夹角最小,利于弯头压力的传递;第五步,以角平分线为基线做oh2的镜像,确定第二根第二型钢的安装初始位置h3,当h3与现有管道冲突时,则沿oh3方向适当调整直至翼板与现有管道接触;第六步,按照悬臂梁中间受集中荷载简化计算模型,校核应力和挠度并确定型钢规格尺寸,微调h2和h3的位置,保证其与新建管道保持5-10cm,在型钢和弯头之间预留马鞍支座的焊接空间;第七步,确保混凝土基座尺寸及位置,保证型钢外侧保护层大于15cm;第八步,计算第二连接型钢的尺寸和规格,第一连接型钢分别设置于第一型钢与两个第二型钢顶部之间,第一连接型钢的长度不小于第一型钢与第二型钢的顶部之间的间距;第二连接型钢设置于两个第二型钢之间,确定弯头拐点的切线位置作为第二连接型钢的安装位置,在第二连接型钢和弯头之间预留马鞍支座的焊接空间;第九步,确定斜撑型钢的尺寸和规格及安装位置,斜撑型钢位于第二连接型钢中点和第三型钢外露于基座部分的底端之间。上述技术方案中,第一型钢、第二型钢、第三型钢的安装角度均垂直于弯头管道所在平面,各型钢预埋在底部设计的混凝土基座中,基座整体嵌固在现有管道下部的非扰动岩土体中,形成抗力支撑体系。上述技术方案中,第二连接型钢的安装角度均平行于弯头管道所在平面。上述技术方案中,第一型钢、第二型钢、第三型钢的腹板平行于压力方向布置,根据弯头接入点的水压力计算型钢规格,每根型钢可承受二分之一的水压力的总负荷并满足抗弯强度要求和马鞍支座处挠度限制值1cm。上述技术方案中,基坑的深度等于管道直径d+0.3m,当为土质地基时,还需满足抗倾覆验算要求。上述技术方案中,型钢的预埋深度不小于管道直径。上述技术方案中,根据弯头的高度和弯头接入点的水压力计算第一型钢、第二型钢的高度,其中预埋深度不小于管道直径,外露部分不小于管道直径+0.3m。上述技术方案中,根据弯头接入点的水压力确定斜撑的角度或者第三型钢和第一型钢之间的间距,使得斜撑与弯头管道所在平面的锐夹角小于45°。上述技术方案中,根据弯头尺寸确定马鞍支座的圆弧面的曲率半径,保证马鞍支座和弯头的外壁有效贴合。本发明提供了一种用于压力管道改迁工程的弯头接入点止推块的施工方法,包括以下步骤:第一步,开挖弯头接入点管道下方基坑,清理后浇筑混凝土垫层;第二步,在基坑内配筋绑扎钢筋笼,并在弯头接入点的内侧和外侧定位安装h型钢;第三步,在基坑内浇筑混凝土形成基座并养护;第四步,申请断水时间,正常切割管道,装配弯头及垫圈第五步,在相邻的h型钢之间焊接第二连接型钢,在第二连接型钢外侧斜撑,使弯道接入点管道位于h型钢、第二连接型钢和斜撑配合形成的钢门架中,焊接管壁垫板及楔子,稳固弯头;第六步,连接弯头和管道,检查管道具备通水条件后,开阀通水,监测h型钢结构变形情况,确保稳定性;第七步,在弯头外侧继续绑扎永久止推快钢筋、装模,按设计完成永久止推块浇筑施工。上述技术方案中,所述h型钢包括一根第一型钢和两根第二型钢,其中第一型钢位于弯头接入点管道的内侧,两根第二型钢分别对称设置于弯头接入点管道外侧,所述一根第一型钢和两根第二型钢呈三角分布,弯头接入点管道位于三根型钢之间。上述技术方案中,所述第二连接型钢包括两根第一连接型钢,两根第一连接型钢焊接于第一型钢的顶端与两根第二型钢的顶端之间,两根第二型钢的之间设置有与基座上表面平行的第二连接型钢,第一连接型钢位于弯头接入点管道的上方,第二连接型钢位于弯头接入点管道中部外侧。上述技术方案中,所述h型钢还包括第三型钢,第三型钢位于第一型钢和两根第二型钢形成的三角结构外侧;斜撑连接于第三型钢靠近于基座上表面的端部和第二连接型钢之间。上述技术方案中,第一步中,基坑开挖结合地质情况,采用挖机,凿岩炮头或牙轮头开槽,基坑宽度大于管道直径0.6m。上述技术方案中,第二步中,基座需在改线安装前至少7天浇筑,基座采用c20及以上标号混凝土浇筑,钢筋选用直径12mm@150mm普通带肋绑扎钢筋笼;保护层厚度大于5cm,h型钢立柱距混凝土外边缘大于10cm。上述技术方案中,第五步中,在第一型钢和两根第二型钢与弯头的间隙之间插入鞍座并焊接;鞍座与管道表面接触部位垫0.5cm橡胶皮进行保护。上述技术方案中,第六步中,弯头和管道的连接处的所有法兰螺栓安装完毕后,清理场地,在弯头承插口顶面位置安装弹簧位移计,将弹簧位移计吸附在直管道表面,位移探针接触于弯头插口环上,调整位置使其稳定,并连接数据采集器用于监测h型钢结构变形情况。上述技术方案中,第一型钢位于弯头接入点的圆心处;第三型钢位于弯头接入点的角平分线上。上述技术方案中,第二型钢的腹板与弯头接入点的圆心连线重合;两个第一连接型钢之间的夹角小于90度。本发明解决了市政项目常见的复杂的地下管线约束下,没有足够的作业空间及施工窗口期,且现有传统设计施工方法存在质量风险问题。通过提出一种原位现浇混凝土预埋型钢止推结构法,形成大直径球墨铸铁压力管道弯头处快速接入止推的工艺,并多次在市政自来水主干网络断水迁改工作中成功应用。通过浇筑基座时预埋型钢支架,型钢钢架和基座的施工期间无需断水,仅仅在切割老管道安装弯头改迁期间需要停水,通过型钢作为临时止推装置,在永久止推块的施工期就可以运营通水。钢结构受力及结构安全性分析方法简明可量化,利于承包商上报项目监理工程师获得批复。相比传统的预制混凝土块拼装工艺或早强混凝土现浇工艺,在安全性、经济性和施工便利性上都具有很大优势,避免了风险高、耗时长的起重作业。本发明极大的节约了断水连接到恢复供水的停运时间和安全质量风险,减少了停水对用户的影响,成为发明人所在项目类似复杂条件下断水施工的推荐工法。附图说明图1是为本发明的结构示意图;图2-7是为本发明的设计流程示意图;图8是为本发明施工完成后的示意图;图9是本发明施工状态监测图示意图;图10是监测设备安装示意图;图11是马鞍支座的结构示意图;图12是具体实施例2中的工况示意图。其中,1-弯头,21-第一型钢,22-第二型钢,23-第三型钢,3-马鞍支座,4-基坑,5-第一连接型钢,6-第二连接型钢,7-斜撑型钢,8-永久止推块,9-新管道,10-沟槽,11-旧管道,12-弹簧位移计,12.1-磁铁基座,12.2-锁扣,12.3-伸缩位移针,12.4-数据采集器,13-弯头插口环。具体实施方式下面结合附图和具体实施例对本发明作进一步的详细说明,便于清楚地了解本发明,但它们不对本发明构成限定。如图1所示,本发明提供了一种弯头接入点临时止推块,它包括位于弯头1接入点下方的基座,基座的上表面垂直预埋有一根第一型钢21和两根第二型钢22,其中第一型钢21位于弯头1接入点管道的内侧,两根第二型钢22分别对称设置于弯头1接入点管道外侧,所述一根第一型钢21和两根第二型钢22呈三角分布,弯头1接入点管道位于三根型钢之间;其中第一型钢21的顶端与两根第二型钢22的顶端之间分别焊接有第一连接型钢5,两根第二型钢22的之间设置有与基座上表面平行的第一连接型钢6,第一连接型钢5位于弯头1接入点管道的上方,第一连接型钢6位于弯头1接入点管道中部外侧;还包括第三型钢23和斜撑型钢7,第三型钢23垂直预埋于基座上表面,第三型钢23位于第一型钢21和两根第二型钢22形成的三角结构外侧;斜撑型钢7连接于第三型钢23靠近于基座上表面的端部和第一连接型钢6之间。第一型钢21、第二型钢22和第一连接型钢5形成三角形的钢门架结构,为弯头1提供有效的支撑力;第一连接型钢6在弯头1拐点,通过第三型钢23和斜撑型钢7在弯头1拐点处提供有有效支撑。所述钢结构为弯头1提供临时止推。所述第一型钢21位于弯头1接入点的圆心处,起到平衡两根第二型钢的受力并贡献抗弯刚度。所述第三型钢23位于弯头1接入点的角平分线上,与弯头受水压后产生的推力方向重合。所述第二型钢22的腹板与弯头1接入点的圆心连线重合,使型钢抗弯能力在推力的分力方向得到最大发挥。所述两个第一连接型钢5之间的夹角小于90度。所述两个第二型钢22和第一连接型钢6与弯头1管体接入点之间设置有马鞍支座3,所述马鞍支座3的圆弧面与弯头1接入点管道外壁相配合,保证弯头1外壁的受力均匀。铸铁管相对于钢管延展性不足,容易造成局部破坏,因此钢结构施工时需要在型钢与管道接触点做好马鞍形垫层保护,分散接触点应力。第一连接型钢6与接入点管道拐点处的切线相平行,使得弯头在水压作用下产生的推力与型钢6位于同一个平面,不产生偏转力。所述第一连接型钢6与弯头1接入点管道外侧的基座上表面之间于设置有斜撑。所述斜撑进一步强化整个钢构体系抗弯能力。综合考虑停水时间成本和材料设备成本,施工安全性等因素,推荐使用预埋钢构后浇筑方案。首先,通过测量校核,确保预埋型钢在断水前能避开切割点,安装弯头1后能准确定位锁住管体。正常施工切管、连接、固定及钢架焊接,待所有接入工作完成后进行永久挡块整体浇筑。此方案既能够保证前期管道受力稳定,又能够保持试运行期间后续镇墩浇筑的整体稳定性,同时因为提前施工临时止推结构,节省了断水时间及空间;h型钢重量轻,吊装设备简单,操作方便,不影响后续既有管线移除工作。所述的一种弯头接入点止推块的施工方法,包括以下步骤:第一步,开挖弯头1接入点管道下方基坑4,,基坑深度满足支撑型钢的嵌固深度,长宽满足型钢外侧保护层厚度的要求,清理后浇筑混凝土垫层;基坑4开挖结合地质情况,采用挖机,凿岩炮头或牙轮头开槽,基坑4宽度大于管道直径0.6m。第二步,在基坑4内配筋绑扎钢筋笼,并在弯头1接入点的内侧和外侧定位安装h型钢;钢筋选用直径12mm@150mm普通带肋绑扎钢筋笼;保护层厚度大于5cm,h型钢立柱距混指基坑4边缘外边缘大于10cm。第三步,在基坑4内浇筑混凝土形成基座并养护;基座需在改线安装前至少7天浇筑,基座采用c20及以上标号混凝土浇筑,第四步,申请管道迁改的断水时间,正常切割管道,装配弯头1及垫圈;第五步,连接弯头和管道,在相邻的h型钢之间焊接第二连接型钢,在第二连接型钢外侧斜撑,使弯道接入点管道位于h型钢、第二连接型钢和斜撑配合形成的钢门架中,焊接管壁垫板及楔子,稳固弯头1;在第一型钢21和两根第二型钢22与弯头1的间隙之间插入鞍座并焊接;鞍座与管道表面接触部位垫0.5cm橡胶皮进行保护。第六步,连接弯头1和管道,检查管道具备通水条件后,开阀通水,监测h型钢结构变形情况,确保稳定性;弯头1和管道的连接处的所有法兰螺栓安装完毕后,清理场地,在弯头1承插口顶面位置安装弹簧位移计12,将弹簧位移计12吸附在新管道和旧管道的直线管管道表面,位移探针接触于弯头插口环上13,调整位置使其稳定,并连接数据采集器用于监测试运营期间弯头插口脱出及结构变形情况。整个断水改线工程从切割安装至具备开阀通水时间小于8小时,弹簧位移计12检测到h型钢结构未发生明显变形,完全满足工艺要求。第七步,在弯头1外侧继续绑扎永久止推快钢筋、装模,按设计完成永久止推块8浇筑施工,临时型钢无需移除,浇筑包裹在永久止推块中。上述技术方案中,临时止推块位于现有管道的下方,采用现浇法嵌入在非扰动的岩土体内,在管道运行的状态下提前完成用于迁改的临时止推结构。临时止推块由嵌入岩土体地基的混凝土体和预埋在混凝土中的h型钢组成,所述h型钢包括一根第一型钢21和两根第二型钢22,其中第一型钢21位于弯头1接入点管道的内侧,两根第二型钢22分别对称设置于弯头1接入点管道外侧,所述一根第一型钢21和两根第二型钢22呈三角分布,弯头1接入点管道位于三根型钢之间。所述一种弯头接入点临时止推块的设计方法,其特征在于包括以下步骤:第一步,作弯头1接入点平面位置图,确定连接弯头1和现有管道的位置尺寸关系;第二步,判断弯头1的圆心位置o,确定上述圆心位置为第一型钢21的安装位置h0;第三步,作弯头1的角平分线,确定第三型钢23的安装位置h1在弯头1外侧的角平分线上;第四步,确定第一根第二型钢h2的位置,保证第二型钢紧靠现有管道,并使腹板方向与拟建弯头管壁相切,以使h2和圆心连线与oh1夹角最小,利于弯头压力的传递;第五步,以角平分线为基线做oh2的镜像,确定第二根第二型钢的安装初始位置h3,当h3与现有管道冲突时,则沿oh3方向适当调整直至翼板与现有管道接触;第六步,按照悬臂梁中间受集中荷载简化计算模型,校核应力和挠度并确定型钢规格尺寸,微调h2和h3的位置,保证其与新建管道保持5-10cm,在型钢和弯头1之间预留马鞍支座3的焊接空间;第七步,计算第二连接型钢的尺寸和规格,第一连接型钢分别设置于第一型钢21与两个第二型钢22的顶部之间,第一连接型钢的长度不小于第一型钢21与第二型钢22的顶部之间的间距;第二连接型钢设置于第三型钢23和第四型钢之间,确定弯头1拐点的切线位置作为第二连接型钢的安装位置,在第二连接型钢和弯头1之间预留马鞍支座3的焊接空间;第八步,确定斜撑的尺寸和规格及安装位置,斜撑位于第二连接型钢重点即第二型钢22外露于基座部分的底端之间;第七步,确保混凝土基座尺寸及位置,保证型钢外侧保护层大于15cm。上述技术方案中,第一型钢21、第二型钢22、第三型钢23的安装角度均垂直于弯头1管道所在平面。各型钢预埋在底部设计的混凝土基座中,基座整体嵌固在现有管道下部的非扰动岩土体中,形成抗力支撑体系。上述技术方案中,第二连接型钢的安装角度均平行于弯头1管道所在平面。上述技术方案中,第一型钢21、第二型钢22、第三型钢23的腹板平行于压力方向布置,根据弯头1接入点的水压力计算型钢规格,每根型钢可承受二分之一的水压力的总负荷,并满足抗弯强度要求和马鞍支座处挠度限制值1cm。上述技术方案中,根据弯头1接入点的水压力计算基坑4的深度等于管道直径d+0.3m,当为土质地基时,还需满足抗倾覆验算要求。上述技术方案中,型钢的预埋深度,不小于管道直径。上述技术方案中,根据弯头1的高度和弯头1接入点的水压力计算第一型钢21、第二型钢22的高度,其中预埋深度不小于管道直径,外露部分不小于管道直径+0.3m。上述技术方案中,根据弯头接入点的水压力确定斜撑的角度或者第三型钢和第一型钢之间的间距,使得斜撑与弯头管道所在平面的锐夹角小于45°上述技术方案中,根据弯头1尺寸确定马鞍支座3的圆弧面的曲率半径,保证马鞍支座3和弯头1的外壁有效贴合。具体实施例中,按照现场沟槽10开挖形式和沟槽10基岩面边界,设计浇筑基座完全嵌入超挖沟槽10内,高度1.8m,混凝土方量40m3。设计型钢支柱共三根,布置情况如图3。三根型钢支墩呈现正三角形,其一条中分线与管道成45°,既保证不影响停水时的切割连接,又使得型钢抗力的合力在主压力方向。最后通过型钢顶部焊接连接梁,形成整体支撑。型钢选用hw400x400xl3x21mmq235h型钢,垂直腹板方向界面惯性矩i=66900cm。焊接斜撑作为安装期间的额外安全保障,不计入受力验算。由于整个混凝土基座现浇嵌入围岩,背墙与岩体直接粘合,此处可不作抗滑移和抗倾覆验算,仅做受弯构件验算即可。止推结构计算基本参数表见下表:弯头1推力按截面受压合力计算:结合型钢参数表,按照集中荷载作用下悬臂梁计算公式,对h型钢进行抗弯强度校核,容易得到h型钢立柱最大弯曲应力和接触点最大挠度分别为:σmax=134.03mpa,小于容许应力210mpa=3.9mm,ωc=3.9mm,满足位移小于2cm要求。具体实施例2中,考虑到基座为现浇混凝土嵌入沟槽10底部,受四周岩土体约束,不考虑整体滑移及倾覆。按照受集中荷载作用的悬臂梁强度和位移控制。典型算例取悬臂高度h=1400mm,管道半径r=600mm,型钢间距b=1600mm。集中力作用点位于型钢悬臂段中部,距混凝土700mm。h型钢材料选用标准见下表:h型钢截面几何性质标准见下表:管道介入弯头1的推力计算结果见下表:管道压力ρ600kpa管直径r1.2m圆周率ⅱ3.14159面积a1.131m^2管道压力p=ρ*a678.583kn转角度α90/1.571deg/rad弯头压力f=p*2sin(α/2)960kn主型钢数n2nos型钢接触压力f’=f/n480kn悬臂长度h’0.7m由于三根立柱型钢通过联系钢梁彼此搭接,形成共同受力的超静定结构共同抵抗压力变形。型钢腹板平行于压力方向布置,为便于计算将总的水压力按平均分配原则,每根弯头1背后的型钢抵抗1/2的总荷载,在型钢立柱小变形情况下,这种假设可满足工程设计的精度需要。最大弯曲应力155mpa,小于设计强度215mpa,计算安全系数fs=215/100>2,弯头1小半径内侧的第三根立柱及设计的斜撑进一步提高了结构的抗弯能力。结构最大挠度约1mm,远小于承插接头容许位移10mm要求。同理,可计算得到满足安全要求的钢结构选材情况如下表:本说明书未作详细描述的内容属于本领域专业技术人员公知的现有技术。当前第1页12