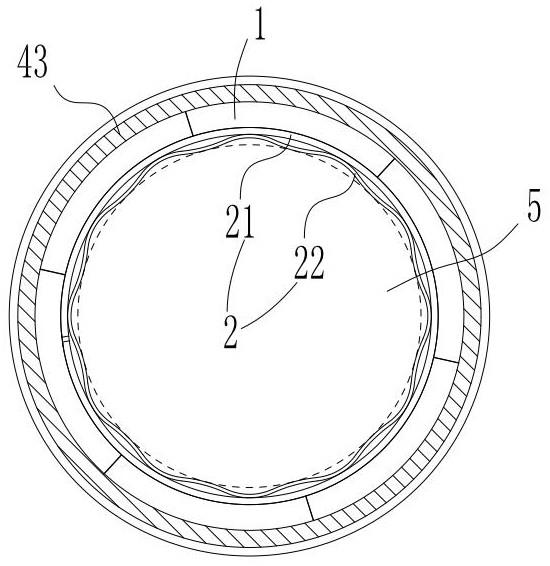
1.本发明涉及物料输送阀气缸活塞密封技术领域,尤其为一种具有自动补偿功能的密封环,以及具有该密封环的气缸和磨盘阀。
背景技术:2.现广泛使用的物料输送阀(比如磨盘阀)都是由气缸推动阀板实现阀门的开关功能,因为物料输送的工艺要求,需要阀门频繁的接通和截断物料输送。而目前使用的物料输送阀气缸活塞密封不能自动补偿,使用一段时间就会产生内泄,使气缸推力减少,达不到阀门全开和全闭的效果,影响物料输送;再者,物料输送的环境温度较高,现在使用的橡胶密封容易产生老化,因此需要频繁更换,影响生产。
技术实现要素:3.本发明的目的在于提供一种具有自动补偿功能的密封环组件,通过合理的结构创新设计,解决现有技术中活塞密封环在使用过程中出现磨损时,因不能自动补偿而造成密封效果不佳的问题。
4.为实现上述目的,本发明采用的技术方案如下:具有自动补偿功能的密封环组件,其包括:密封环本体,其呈圆环状,且所述圆环的横截面为矩形;弹性件,其设置于所述密封环本体的内侧,为所述密封环本体提供由内至外的弹力,所述弹性件用于在所述密封环本体被磨损时,向外延展所述密封环本体,以自动补偿所述密封环本体的磨损量;其中,所述密封环本体具有切口结构,所述切口结构连通所述密封环本体的内壁面和外壁面,使得所述密封环本体在受力状态下可在预设的径向尺寸内自由扩张;所述切口结构将所述密封环本体分隔为多个密封环本体单体,多个所述密封环本体单体相互连接而不会自由断开。
5.可选的,所述弹性件包括第一弹性件和第二弹性件;所述第一弹性件为开口支撑圈,所述第二弹性件为波纹弹簧;其中,所述开口支撑圈的外壁面与所述密封环本体的内壁面相抵接,为所述密封环本体提供由内至外的径向柔性支撑;所述波纹弹簧的外壁面与所述开口支撑圈的内壁面相抵接。
6.可选的,所述密封环本体由耐高温材料制成。
7.可选的,所述耐高温材料为聚四氟乙烯材料。
8.可选的,所述密封环本体上具有多个切口结构;每一个所述切口结构包括第一切口和第二切口;所述第一切口起始于所述密封环本体的一端面,并终止于所述密封环本体中部;
所述第二切口起始于所述密封环本体的另一端面,并终止于所述密封环本体中部;所述第一切口与所述第二切口之间未连通。
9.可选的,所述第一切口包括顺次首尾连接的第一切口i段、第一切口ii段、第一切口iii段、第一切口iv段;所述第一切口i段、第一切口ii段、第一切口iii段、第一切口iv段所限定的方向彼此相交;所述第二切口包括顺次首尾连接的第二切口i段、第二切口ii段、第三切口iii段、第四切口iv段;所述第二切口i段、第二切口ii段、第二切口iii段、第二切口iv段所限定的方向彼此相交;所述第一切口iv段的末端与第二切口iv段的末端不重合。
10.可选的,所述第一切口i段、第一切口ii段、第一切口iii段、第一切口iv段所限定的方向彼此垂直;所述第二切口i段、第二切口ii段、第二切口iii段、第二切口iv段所限定的方向彼此垂直;所述第一切口iv段的末端与第二切口iv段的末端不重合。
11.可选的,所述第一切口和所述第二切口成中心对称结构,且所述第一切口ii段、第一切口iii段、第一切口iv段所限定的切口形状与所述第二切口ii段、第二切口iii段、第二切口iv段所限定的切口形状呈互相扣合的位置关系。
12.可选的,所述切口结构的数量为3~6个。
13.可选的,所述第一切口和所述第二切口可以为折线形,也可以为曲线形,也可以为曲线和折线的结合。
14.基于同样的发明构思,本发明还提供一种气缸,其包括气缸体、活塞和密封环;其中,所述气缸体包括前端盖、后端盖和缸筒,所述活塞滑配于所述缸筒内,所述活塞的周向壁面上开设有自其壁面表面向活塞内部下沉的环形安装槽,所述环形安装槽内安装有所述密封环组件;所述密封环组件为上述技术方案中所述的具有自动补偿功能的密封环组件。
15.基于同样的发明构思,本发明还提供一种磨盘阀,其包括阀体、阀板及气缸;所述气缸设置于所述阀体上,其工作端与所述阀板相连接,藉以推动所述阀板执行开闭动作;所述气缸为上述技术方案中所述的其活塞上安装有具有自动补偿功能的密封环组件的气缸。
16.与现有技术相比,本发明的有益效果体现在:1、本发明的密封环组件,其密封环本体内套接设置有弹性件,弹性件的开口支撑圈和波纹弹簧也为套接设置,开口支撑圈为密封环本体提供由内至外的均匀的径向柔性支撑,波纹弹簧对开口支撑圈具有径向弹性伸展压力,当密封环本体表面出现磨损时,波纹弹簧的径向弹性伸展压力将通过开口支撑圈传递到密封环本体,使密封环本体向外扩张,自动补偿磨损量,从而始终确保密封性能。
17.2、本发明的活塞密封环,其密封环本体采用聚四氟乙烯制成,不仅摩擦系数小,且耐高温,不易老化,延长了密封环在物料输送阀气缸内高温工作环境中的使用寿命长,降低了密封环因老化更换的频率,有利于生产效率的提高。
18.3、本发明的活塞密封环,其密封环本体上设置了切口结构,使活塞密封环在装配和使用中能径向扩大,且因形成切口结构的第一切口和第二切口并不连通,即切口结构未切断密封环本体,因此也不会导致物料串漏。该结构与波纹弹簧的自动补偿功能相结合,可以增大密封环的密封口径范围,进而提高密封环的适用范围。
附图说明
19.为了更清楚地说明本技术实施例中的技术方案,下面将对实施例描述中所需要使用的附图作简单地介绍,显而易见地,下面描述中的附图仅仅是本技术的一些实施例,对于本领域普通技术人员来讲,在不付出创造性劳动的前提下,还可以根据这些附图获得其他的附图。
20.图1为本发明所述的密封环组件的剖面结构示意图。
21.图2为本发明所述的密封环本体的结构示意图。
22.图3为本发明所述的切口结构展开后的平面示意图。
23.图4为本发明一个实施例中所述的曲线形切口结构的平面示意图。
24.图5为本发明所述的气缸的局部剖视结构示意图。
25.附图标记:1
‑
密封环本体;2
‑
弹性件,21
‑
开口支撑圈,22
‑
波纹弹簧;3
‑
切口结构,31
‑
第一切口,32
‑
第二切口;311
‑
第一切口i段,312
‑
第一切口ii段,313
‑
第一切口iii段,314
‑
第一切口iv段;321
‑
第二切口i段,322
‑
第二切口ii段,323
‑
第三切口iii段,324
‑
第四切口iv段;4
‑
气缸体,41
‑
前端盖,42
‑
后端盖,43
‑
缸筒;5
‑
活塞。
具体实施方式
26.在下文中,仅简单地描述了某些示例性实施例。正如本领域技术人员可认识到的那样,在不脱离本发明的精神或范围的情况下,可通过各种不同方式修改所描述的实施例。因此,附图和描述被认为本质上是示例性的而非限制性的。
27.下面结合附图对本发明的实施例进行详细说明。
28.实施例一如图1~图3所示,本实施例提供一种具有自动补偿功能的密封环组件,该密封环组件包括密封环本体1和套设于其内的弹性件2;所述密封环本体1呈圆环状,且所述圆环的横截面为等尺寸矩形;所述弹性件2设置于所述密封环本体1的内侧,为所述密封环本体1提供由内至外的弹力;具体的,所述弹性件2用于在所述密封环本体1被磨损时,向外延展所述密封环本体1,以自动补偿所述密封环本体1的磨损量,从而始终确保密封性能良好。
29.具体的,本实施例中,所述弹性件2包括第一弹性件和第二弹性件,所述第一弹性
件为开口支撑圈21,所述第二弹性件为波纹弹簧22;其中,所述开口支撑圈21的外壁面与所述密封环本体1的内壁面相抵接,为所述密封环本体1提供由内至外的径向柔性支撑;所述波纹弹簧22的外壁面与所述开口支撑圈21的内壁面相抵接。本实施例中,所述波纹弹簧22为圈状多层波形弹簧,其对所述开口支撑圈21具有径向弹性伸展压力,当密封环本体1表面出现磨损时,所述波纹弹簧22的径向弹性伸展压力将通过所述开口支撑圈21传递到密封环本体1,使密封环本体1向外扩张,自动补偿磨损量,从而始终确保密封性能。
30.所述密封环本体1由耐高温材料制成,本实施例中,所述密封环本体1由聚四氟乙烯材料制成。将所述密封环本体1采用聚四氟乙烯制成,不仅摩擦系数小,且耐高温,不易老化,延长了密封环本体1在物料输送阀气缸内高温工作环境中的使用寿命长,降低了密封环本体1因老化更换的频率,有利于生产效率的提高。
31.在其他实施例中,所述耐高温材料也可为聚四氟丙烯,或者采用填充有聚苯酯的聚四氟乙烯复合材料,本发明不做具体限制。
32.如图2~图3所示,所述密封环本体1上具有多个切口结构3,切口结构3连通所述密封环本体1的内壁面和外壁面,使得所述密封环本体1在受力状态下可在预设的径向尺寸内自由扩张;此外,切口结构3将密封环本体1分隔为多个密封环本体单体,多个所述密封环本体单体相互连接而不会自由断开。
33.具体地,本实施例中,所述切口结构3为两个;每一个所述切口结构3均包括第一切口31和第二切口32;所述第一切口31起始于所述密封环本体1的左端面p,并终止于所述密封环本体1中部;所述第二切口32起始于所述密封环本体1的右端面q,并终止于所述密封环本体1中部;且所述第一切口31与所述第二切口32之间未连通。该结构设置使活塞密封环本体1在装配和使用中能径向扩大,且因形成切口结构3的第一切口31和第二切口32并不连通,即切口结构3未切断密封环本体1,因此也不会导致物料串漏。该结构与波纹弹簧22的自动补偿功能相结合,可以增大密封环的密封口径范围,进而提高密封环的适用范围。
34.在一个具体的实施场景中,所述第一切口31包括顺次首尾连接的第一切口i段311、第一切口ii段312、第一切口iii段313、第一切口iv段314;所述第一切口i段311、第一切口ii段312、第一切口iii段313、第一切口iv段314所限定的方向彼此相交;所述第二切口32包括顺次首尾连接的第二切口i段321、第二切口ii段322、第三切口iii段323、第四切口iv段324;所述第二切口i段321、第二切口ii段322、第三切口iii段323、第四切口iv段324所限定的方向彼此相交;所述第一切口iv段314的末端与第二切口iv段324的末端不重合,以确保所述密封环本体1不被切断、保持结构的连整性。
35.作为优选方案,本实施例中,所述第一切口31和所述第二切口32成中心对称结构,所述第一切口i段311、第一切口ii段312、第一切口iii段313、第一切口iv段314所限定的方向彼此垂直,所述第二切口i段321、第二切口ii段322、第三切口iii段323、第四切口iv段324所限定的方向彼此垂直,且所述第一切口ii段312、第一切口iii段313、第一切口iv段314所限定的切口形状与所述第二切口ii段322、第三切口iii段323、第四切口iv段324所限定的切口形状呈互相扣合的位置关系。该结构设计有利于所述密封环本体1在装配过程中需要径向拉大其直径时,其直径拉大量保持统一、密封环本体在切口结构3处的受力保持均衡,有利于规范、便捷的进行装配。
36.本实施例中,所述第一切口31和所述第二切口32均为折线形;在其他实施例中,所
述第一切口31和所述第二切口32也可以为曲线形,如图4所示;在其他实施例中,所述第一切口31和所述第二切口32还可以为曲线和折线的结合。
37.实施例二本实施例提供一种气缸,如图5所示,其包括气缸体4、活塞5和密封环组件;其中,所述气缸体4包括前端盖41、后端盖42和缸筒43,所述活塞5滑配于所述缸筒43内,所述活塞5的周向壁面上开设有自其壁面表面向活塞内部下沉的环形安装槽,所述环形安装槽内安装有所述密封环组件;所述密封环组件为实施例一中所述的具有自动补偿功能的密封环组件,该密封环组件套设于活塞的外壁面。所述密封环本体1由聚四氟乙烯材制成,耐高温,摩擦系数小,且所述活塞密封环本体1内设置有弹性件2,可以对密封环本体1的磨损量自动补偿,确保密封效果,所述密封环本体1内还设置了切口结构3,使活塞密封环本体1在装配和使用中能径向扩大,因切口结构3未切断密封环本体,物料不会产生串漏。通过所述具有自动补偿的活塞密封环,可以避免气缸在使用过程中发生内泄的现象,提高气缸推力做功的效率,使阀门达到全开/全闭的效果,提高物料输送率。
38.实施例三本实施例提供一种磨盘阀,其包括阀体、阀板及气缸;所述气缸设置于所述阀体上,其工作端与所述阀板相连接,藉以推动所述阀板执行开闭动作;所述气缸为实施例二所述的其活塞上安装有具有自动补偿功能的密封环组件的气缸。
39.在本发明的描述中,需要理解的是,术语“上”、“下”、“内”、“外”、“左”、“中”、“右”、“前”、“后”以及“i段、ii段、iii段、iv段”等指示的方位或位置关系为基于附图所示的方位或位置关系,或者是本发明产品使用时惯常摆放的方位或位置关系,或者是本领域技术人员惯常理解的方位或位置关系,仅是为了便于描述本发明和简化描述,而不是指示或暗示所指的装置或元件必须具有特定的方位、以特定的方位构造和操作,因此不能理解为对本发明的限制。
40.同时除非另有明确的规定和限定,术语“设置”、“连接”、“安装”等术语应做广义理解,例如,可以是固定连接,也可以是可拆卸连接,或成一体;可以是机械连接,也可以是焊接连接;可以是直接相连,也可以通过中间媒介间接相连,可以是两个元件内部的连通或两个元件的相互作用关系,除非另有明确的限定,对于本领域的普通技术人员而言,可以根据具体情况理解上述术语在本发明中的具体含义。
41.此外,术语“第一”、“第二”仅用于描述目的,而不能理解为指示或暗示相对重要性或者隐含指明所指示的技术特征的数量。由此,限定有“第一”、“第二”的特征可以明示或者隐含地包括一个或者更多个该特征。
42.尽管已经示出和描述了本发明的实施例,对于本领域的普通技术人员而言,可以理解在不脱离本发明的原理和精神的情况下可以对这些实施例进行多种变化、修改、替换和变型,本发明的范围由所附权利要求及其等同物限定。