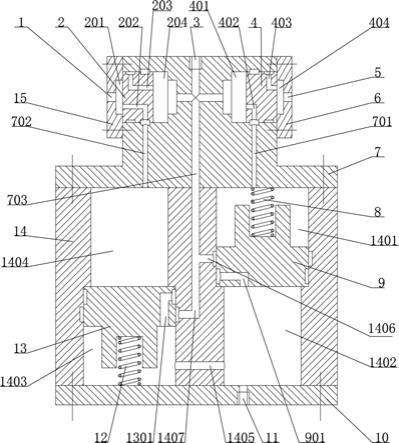
1.本实用新型属于阀门技术领域,特别涉及一种压力自适应可换向止回阀。
背景技术:2.止回阀即单向阀,现有的止回阀,通常只有一个止回方向;在确定它的止回方向且安装到位后,止回方向就不再改变;对于一些需要改变止回方向的场合,如一个容器(管道)内的工作压力既可能高于环境压力也可能低于环境压力。通常做法是将管路截止后重新调整止回阀的止回方向,或是并联设置多组不同止回方向的止回阀及截止阀,通过打开和关闭相应截止阀来选择合适止回方向的止回阀投入工作;现有的一些可换向的止回阀采用翻板式,或者利用内置的电气动作部件来进行换向,不仅可靠性较差,且成本较高;以上方案存在设备繁杂,调整耗时较长,系统运行可能中断,人力投入较大等缺点。
技术实现要素:3.本实用新型所要解决的技术问题是提供一种压力自适应可换向止回阀,该装置解决了现有止回阀难以实现换向,换向操作繁琐、费时费力,成本较高,可靠性差的问题,具有结构稳定、使用方便,可根据环境压力以及阀门两端压力差自动改变活塞的位置,从而使压力源与容器之间相互连通或截断,进而实现自行适应压力变化而改变止回方向的功能的特点。
4.为解决上述技术问题,本实用新型所采用的技术方案是:一种压力自适应可换向止回阀,包括中空的缸体,缸体上端连接有上缸盖,下端连接有下缸盖,缸体内部分隔成第一腔体和第二腔体,第一腔体和第二腔体均为圆柱形腔体,腔体内壁中部均设置有台阶面将腔体内部分隔成直径不同的两段;第一腔体内壁设置有第一主活塞,第一主活塞将第一腔体分隔成第一活塞腔和第二活塞腔;第二腔体内壁设置有第二主活塞,第二主活塞将第二腔体分隔成第三活塞腔和第四活塞腔;上缸盖顶部设置有容器端接口,容器端接口通过第一通压孔与缸体内部连通。
5.优选地,第一腔体中直径较大的一段为第一活塞腔,第一主活塞与第一活塞腔接触滑动;第一主活塞盲孔一端通过第一弹簧与第一活塞腔内壁连接。
6.优选地,第二腔体中直径较大的一段为第三活塞腔,第二主活塞与第三活塞腔接触滑动;第二主活塞盲孔一端通过第二弹簧与第三活塞腔内壁连接。
7.优选地,第三活塞腔与第二活塞腔同侧,三活塞腔与第二活塞腔之间设置有平压孔连通两个腔室;第二活塞腔底部的下缸盖上设置有压力源接口。
8.优选地,第一通压孔端部通过第二通压孔与第一活塞腔连通;第一通压孔端部通过第三通压孔与第三活塞腔连通。
9.优选地,第一主活塞表面开设有第一连通孔,第一连通孔一端与第二活塞腔连通,另一端位于第一主活塞侧表面;当第一主活塞位于上止点时,第一连通孔连通第二活塞腔以及第二通压孔。
10.优选地,第二主活塞表面开设有第二连通孔,第二连通孔一端与第三活塞腔连通,另一端位于第二主活塞侧表面;当第二主活塞位于下止点时,第二连通孔连通第三活塞腔以及第三通压孔。
11.优选地,上缸盖侧表面开设有圆柱状的第三腔体;第三腔体内壁设置有第一先导活塞,第一先导活塞将第三腔体内部分隔成朝外的第五活塞腔和向内的第六活塞腔;第五活塞腔与第一端盖表面的第一环境压力孔连通;第六活塞腔与第一通压孔连通;第三腔体内壁设置有第四通压孔连通第三腔体和第四活塞腔,第一先导活塞表面开设有第三连通孔和第四连通孔,当第一先导活塞位于左止位时,第三连通孔连通第五活塞腔和第四通压孔;当第一先导活塞位于右止位时,第四连通孔连通第六活塞腔和第四通压孔。
12.优选地,上缸盖侧表面开设有圆柱状的第四腔体;第四腔体内壁设置有第二先导活塞,第二先导活塞将第三腔体内部分隔成朝外的第七活塞腔和向内的第八活塞腔;第七活塞腔与第二端盖表面的第二环境压力孔连通;第八活塞腔与第一通压孔连通;第四腔体内壁设置有第五通压孔连通第四腔体和第一活塞腔,第二先导活塞表面开设有第五连通孔和第六连通孔,当第二先导活塞位于左止位时,第六连通孔连通第七活塞腔和第五通压孔;当第二先导活塞位于右止位时,第五连通孔连通第八活塞腔和第五通压孔。
13.进一步地,流体介质可以为气体也可为液体。
14.进一步地,第一端盖上的第一环境压力孔与第二端盖上的第二环境压力孔可通过隔膜后再与环境相连通,实现介质与环境隔离但压力可传导,防止介质外泄造成环境污染。
15.进一步地,第一端盖上的第一环境压力孔与第二端盖上的第二环境压力孔可与一个压力可调整的压力源连通,即可对该止回阀止回方向的切换压力进行受控调整。
16.本实用新型的有益效果为:
17.1、适应范围广,流体介质可以为气体,也可为液体,正压或者负压环境均可工作;
18.2、具有一般止回阀不具备的放空阀的功能;
19.3、根据工作压力是正压还是负压来自动切换止回方向,无需其他设备或人工辅助判断和操作;
20.4,容器侧的正压或负压均可在环境压力下保持,压力源可以以更高压力或真空度向容器侧充压或抽真空;而容器侧的正压或负压需要泄压或消除真空度时,只须将压力源变成反向的负压或正压即可;无需内置电气动作部件,可靠性强,且成本较低。
附图说明
21.图1为本实用新型的结构示意图;
22.图2为本实用新型充压状态下的内部压力流向图;
23.图3为本实用新型持压状态下的内部压力流向图;
24.图4为本实用新型泄压状态下的内部压力流向图;
25.图5为本实用新型抽真空状态下的内部压力流向图;
26.图6为本实用新型保持真空状态下的内部压力流向图;
27.图7为本实用新型真空破坏状态下的内部压力流向图;
28.图中附图标记为:第一环境压力孔1,第一先导活塞2,第五活塞腔201,第三连通孔202,第四连通孔203,第六活塞腔204,容器端接口3,第二先导活塞4,第八活塞腔401,第五
连通孔402,第六连通孔403,第七活塞腔404,第二环境压力孔5,第二端盖6,上缸盖7,第五通压孔701,第四通压孔702,第一通压孔703,第一弹簧8,第一主活塞9,第一连通孔901,下缸盖10,压力源接口11,第二弹簧12,第二主活塞13,第二连通孔1301,缸体14,第一活塞腔1401,第二活塞腔1402,第三活塞腔1403,第四活塞腔1404,平压孔1405,第二通压孔1406,第三通压孔1407,第一端盖15。
具体实施方式
29.如图1中,一种压力自适应可换向止回阀,包括中空的缸体14,缸体14上端连接有上缸盖7,下端连接有下缸盖10,缸体14内部分隔成第一腔体和第二腔体,第一腔体和第二腔体均为圆柱形腔体,腔体内壁中部均设置有台阶面将腔体内部分隔成直径不同的两段;第一腔体内壁设置有第一主活塞9,第一主活塞9将第一腔体分隔成第一活塞腔1401和第二活塞腔1402;第二腔体内壁设置有第二主活塞13,第二主活塞13将第二腔体分隔成第三活塞腔1403和第四活塞腔1404;上缸盖7顶部设置有容器端接口3,容器端接口3通过第一通压孔703与缸体14内部连通。
30.优选地,第一腔体中直径较大的一段为第一活塞腔1401,第一主活塞9与第一活塞腔1401接触滑动;第一主活塞9盲孔一端通过第一弹簧8与第一活塞腔1401内壁连接。
31.优选地,第二腔体中直径较大的一段为第三活塞腔1403,第二主活塞13与第三活塞腔1403接触滑动;第二主活塞13盲孔一端通过第二弹簧12与第三活塞腔1403内壁连接。
32.优选地,第三活塞腔1403与第二活塞腔1402同侧,三活塞腔与第二活塞腔1402之间设置有平压孔1405连通两个腔室;第二活塞腔1402底部的下缸盖10上设置有压力源接口11。
33.优选地,第一通压孔703端部通过第二通压孔1406与第一活塞腔1401连通;第一通压孔703端部通过第三通压孔1407与第三活塞腔1403连通。
34.优选地,第一主活塞9表面开设有第一连通孔901,第一连通孔901一端与第二活塞腔1402连通,另一端位于第一主活塞9侧表面;当第一主活塞9位于上止点时,第一连通孔901连通第二活塞腔1402以及第二通压孔1406。
35.优选地,第二主活塞13表面开设有第二连通孔1301,第二连通孔1301一端与第三活塞腔1403连通,另一端位于第二主活塞13侧表面;当第二主活塞13位于下止点时,第二连通孔1301连通第三活塞腔1403以及第三通压孔1407。
36.优选地,上缸盖7侧表面开设有圆柱状的第三腔体;第三腔体内壁设置有第一先导活塞2,第一先导活塞2将第三腔体内部分隔成朝外的第五活塞腔201和向内的第六活塞腔204;第五活塞腔201与第一端盖15表面的第一环境压力孔1连通;第六活塞腔204与第一通压孔703连通;第三腔体内壁设置有第四通压孔702连通第三腔体和第四活塞腔1404,第一先导活塞2表面开设有第三连通孔202和第四连通孔203,当第一先导活塞2位于左止位时,第三连通孔202连通第五活塞腔201和第四通压孔702;当第一先导活塞2位于右止位时,第四连通孔203连通第六活塞腔204和第四通压孔702。
37.优选地,上缸盖7侧表面开设有圆柱状的第四腔体;第四腔体内壁设置有第二先导活塞4,第二先导活塞4将第三腔体内部分隔成朝外的第七活塞腔404和向内的第八活塞腔401;第七活塞腔404与第二端盖6表面的第二环境压力孔5连通;第八活塞腔401与第一通压
孔703连通;第四腔体内壁设置有第五通压孔701连通第四腔体和第一活塞腔1401,第二先导活塞4表面开设有第五连通孔402和第六连通孔403,当第二先导活塞4位于左止位时,第六连通孔403连通第七活塞腔404和第五通压孔701;当第二先导活塞4位于右止位时,第五连通孔402连通第八活塞腔401和第五通压孔701。
38.优选地,上述一种压力自适应可换向止回阀的工作原理如下:
39.s1,容器端接口3处压力为p1,压力源接口11处压力为p2;第一环境压力孔1和第二环境压力孔5处压力相同,均为环境压力p3;
40.s2,当容器端为正压状态时,即p1> p3时,此时装置基本状态如下:
41.第一先导活塞2在第五活塞腔201和第六活塞腔204的压力差下位于左止点,第四活塞腔1404通过第四通压孔702和第三连通孔202与第五活塞腔201连通,感应环境压力p3,第三活塞腔1403压力为p2;第二先导活塞4在第八活塞腔401与第七活塞腔404的压力差下位于右止点,此时第一活塞腔1401通过第五通压孔701和第五连通孔402与第八活塞腔401连通,感应容器侧压力p1,第二活塞腔1402压力为p2;此时随着压力源压力p2的变化,装置有如下三种动作方式:
42.如图2中,当p2>p1,即压力源压力高于容器端压力时,压力差克服第一弹簧8的弹力,第一主活塞9向上移动,第二通压孔1406与第一连通孔901连通,使压力源接口11与容器端接口3连通,使压力源向容器端充压;
43.如图3中,当p3≤p2<p1时,即压力源压力逐渐减小,直到与环境压力相同时,第二主活塞13与第一主活塞9均位于初始位置,压力源接口11与容器端接口3未被连通,容器侧压力p1将保持;
44.如图4中,当p2<p3,即压力源为负压时,压力差克服第二弹簧12的弹力后,第二主活塞13向下移动,第三通压孔1407与第二连通孔1301连通,使压力源接口11与容器端接口3连通,容器侧朝向压力源侧进行泄压;
45.s3,当容器端为负压状态时,即p1< p3时,此时装置基本状态如下:
46.第一先导活塞2在第五活塞腔201与第六活塞腔204的压力差下位于右止点,第四活塞腔1404通过第四通压孔702和第四连通孔203与第六活塞腔204连通,感应容器端压力p1,第三活塞腔1403压力为p2;第二先导活塞4在第八活塞腔401与第七活塞腔404的压力差下位于左止点,此时第一活塞腔1401通过第五通压孔701和第六连通孔403与第七活塞腔404连通,感应环境压力p3,第二活塞腔1402压力为p2;此时随着压力源压力p2的变化,装置有如下三种动作方式:
47.如图5中,当p2<p1,即压力源真空度大于容器侧真空度时,两者压力差克服第二弹簧12的弹力后,第二主活塞13向下移动,第三通压孔1407与第二连通孔1301连通,使压力源接口11与容器端接口3连通,容器侧被抽真空;
48.如图6中,当p1<p2≤p3时,即压力源真空度减小,直到与环境压力相同时;第二主活塞13与第一主活塞9均位于初始位置,压力源接口11与容器端接口3未被连通,容器端真空度将保持;
49.如图7中,当p2>p3,即压力源为正压时,两者压力差克服第一弹簧8(8)的弹力后,第一主活塞9向上移动,第二通压孔1406与第一连通孔901连通,使压力源接口11与容器端接口3连通,容器端吸入压力源侧的介质,真空度减小,真空被破坏。
50.进一步地,流体介质可以为气体也可为液体。
51.进一步地,第一端盖15上的第一环境压力孔1与第二端盖6上的第二环境压力孔5可通过隔膜后再与环境相连通,实现介质与环境隔离但压力可传导,防止介质外泄造成环境污染。
52.进一步地,第一端盖15上的第一环境压力孔1与第二端盖6上的第二环境压力孔5可与一个压力可调整的压力源连通,即可对该止回阀止回方向的切换压力进行受控调整。
53.上述的实施例仅为本实用新型的优选技术方案,而不应视为对于本实用新型的限制,本技术中的实施例及实施例中的特征在不冲突的情况下,可以相互任意组合。本实用新型的保护范围应以权利要求记载的技术方案,包括权利要求记载的技术方案中技术特征的等同替换方案为保护范围。即在此范围内的等同替换改进,也在本实用新型的保护范围之内。