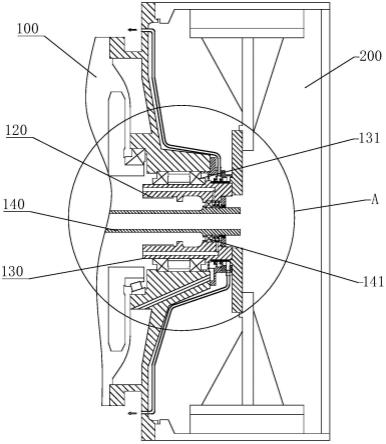
1.本实用新型涉及一种风电齿轮箱油封,具体涉及一种齿轮箱输出轴密封结构。
背景技术:2.随着能源情况的逐步恶化,风能作为可再生的、无污染的自然能源逐渐受到重视。风力发电装置是一种能够将风能转化为电能的装置,齿轮箱是风力发电装置中必不可少的部件。为了防止漏油,现有的齿轮箱高速级输出装置一般采用两道,三道或者更多道密封形式,每一道回油密封腔都是一个独立封闭的回油通道,但是由于高速轴的快速运转会引起封闭密封腔内的油温、轴承的温度快速升高,使得油雾浓厚且密封腔内气压不断增大。由于油雾浓厚以及密封腔压力增大会使得高速级输出端漏油。由于局部零部件承受高温高压会使零件遭受一定的冲击以及金属机械性能恶化,强度降低,脆性增加等问题,这严重影响了齿轮箱的寿命,接触式密封往往因为材质的原因很难满足使用期限内的密封效果,一旦发生泄漏就需要停机维修及时更换,不仅劳动强度较大,而且影响发电机的正常使用。而非接触的迷宫式密封装置虽然使用寿命较长,但是其结构相对复杂,且依然有油雾渗出现象,随着半直驱技术发展,齿轮箱与电机集成度越来越高,在高度集成化设计中,齿轮箱与电机之间的密封成为较大难题,一旦漏油将会影响发电机的正常运转,严重时将损毁发电机。
技术实现要素:3.发明目的:本实用新型的目的在于针对现有技术的不足,提供一种半直驱风电齿轮箱输出轴密封结构,避免输出轴以及管轴处润滑油的泄漏,实现齿轮箱润滑油的可靠密封,同时实现对油雾的排放。
4.技术方案:本实用新型所述的一种半直驱风电齿轮箱输出轴密封结构,包括齿轮箱以及发电机,所述齿轮箱的输出轴、管轴的轴颈处对应设有第一密封部、第二密封部,所述第一密封部包括不少于两个第一环腔,所述第一环腔至少有一个连通有箱外油雾排出部,所述第一环腔还连通有第一箱内回油部,所述第一环腔由相邻的第一挡油环和/ 或第一甩油环围成,所述第二密封部包括至少一个第二环腔,所述第二环腔由相邻的第二挡油环和/或第二甩油环围成,所述第二环腔连通有第二箱内回油部。
5.所述箱外油雾排出部直接将第一密封部的第一环腔与大气连通,以使齿轮箱内的油雾第一时间通过油雾排出部排至外部大气,而不会通过第一环腔进入发电机内部。
6.所述输出轴通过输出轴轴承设于齿轮箱上,相对于所述输出轴轴承最近处以及最远处的第一环腔须对应设置第一箱内回油部、箱外油雾排出部。
7.所述第一箱内回油部为设于箱体壁上的油道,所述箱外油雾排出部为设于齿轮箱外部的排油管,所述排油管一端连通于大气,所述排油管另一端通过第一挡油环贯通于第一环腔。
8.相对于所述输出轴的输出轴轴承最近处的第一环腔由第一挡油环围成,其余相邻第一环腔之间通过相互嵌套的第一挡油环与第一甩油环间隔开,所述第一挡油环和第一甩
油环之间具有阻止润滑油溢出的迷宫式间隙。
9.所述输出轴位于第一密封部处的轴颈处设有轴肩,所述第一甩油环过盈配合于轴肩低阶侧,相邻于所述输出轴轴承的第一挡油环与轴肩高阶侧间隙配合。
10.所述第一环腔可同时连通于箱外油雾排出部、第一箱内回油部,或第一环腔择一连通于箱外油雾排出部、第一箱内回油部。
11.所述管轴通过管轴轴承设于输出轴的轴向空腔内,所述第二箱内回油部为设于输出轴轴壁内的油道。
12.所述输出轴轴壁内的油道包括平行于输出轴的轴向部,以及垂直于输出轴的径向部,所述轴向部、径向部通过弯折部连通,所述轴向部外端通过第二甩油环连通于第二环腔。
13.相对于所述管轴轴承最远处的第二环腔的外侧设有管轴透盖,所述管轴透盖设有作用于管轴轴颈的环形油封。
14.有益效果:本实用新型的半直驱风电齿轮箱输出轴密封结构,在输出轴的轴颈处设置若干道第一环腔,每个第一环腔均具有阻止润滑油泄漏的作用,由于第一环腔叠加使用,远离输出轴轴承方向的第一环腔内泄漏的润滑油逐渐减少,但是由于输出轴轴承工作温度很高,产生的热量会使得一部分润滑油雾化,这些油雾可以通过箱外油雾排出部直接排至外界大气中,取代了让油雾积聚在第一环腔内或者通过回油至齿轮箱内的设计,这样的气压平衡设计大大降低了第一环腔内部压力,完全杜绝了润滑油向发电机处泄漏的可能性;
15.距输出轴轴承最近的第一环腔连接第一箱内回油部,保证齿轮箱内的润滑油全部回至齿轮箱内部,距输出轴轴承最远的第一环腔连接箱外油雾排出部,避免其内部压力将油雾泄漏至发电机,或影响相邻的第一环腔破坏其密封性能,位于距输出轴轴承最近或最远处之间第一环腔可根据齿轮箱功率选择连接第一箱内回油部和/或箱外油雾排出部,通过灵活的选择第一箱内回油部、箱外油雾排出部,设计不同密封等级的密封结构,以适配不同齿轮箱,模块化设计降低生产成本;
16.距输出轴轴承最近的第一环腔采用第一挡油环单独围成,而未采用第一挡油环与第一甩油环嵌套的设计,优点在于此处的润滑油量较多,若设置第一甩油环的话,会更容易增加润滑油的压力和温度,当润滑油经第一道第一环腔的第一挡油环阻拦后,进入相邻的第一环腔内的润滑油大大减少,此时第一甩油环才可以发挥其最优工况,且输出轴轴承主要承受轴向力,第一甩油环紧贴输出轴轴承设置容易产生破坏性的应力,管轴的轴颈处设置若干第二环腔,其第二箱内回油部设置在输出轴轴壁内,充分利用了输出轴旋转时的离心力,提高了第二环腔内润滑油回油至齿轮箱内部的效率。
附图说明
17.图1为本实用新型的半直驱风电齿轮箱的局部剖视图;
18.图2为本实用新型的图1中a部分的部分放大图;
19.图3为本实用新型的输出轴处第一密封部剖视图;
20.图4为本实用新型的输出轴处第一密封部剖视图;
21.图5为本实用新型的输出轴处第一密封部剖视图;
22.图6为本实用新型的输出轴处第一密封部剖视图;
23.图7为本实用新型的管轴处第二密封部剖视图;
24.图8为本实用新型的挡油环、甩油环定位结构示意图。
具体实施方式
25.下面对本实用新型技术方案进行详细说明,但是本实用新型的保护范围不局限于所述实施例。
26.如图1~8所示,本实用新型的一种半直驱风电齿轮箱输出轴密封结构,包括齿轮箱 100以及发电机200,半直驱风电的齿轮箱100与发电机200集成度越来越高,齿轮箱 100的输入轴连接有行星级增速系或者平行级增速系,在本实用新型的图示中,本实施例采取行星级增速系,其太阳轮通过花键120连接于齿轮箱100的输出轴130,输出轴 130通过输出轴轴承131转动的支撑于输出轴透盖处,为了方便发电机200的线缆布置,使得线缆能够从发电机200穿过齿轮箱100连接到其他设备,齿轮箱100的太阳轮、输出轴130均设有供线缆等部件穿过的轴向空腔,该轴向空腔内设有用于容纳线缆的管轴 140,管轴140设置为不随输出轴130转动,线缆设在管轴140中不会发生缠绕,避免线缆磨损以及被润滑油浸泡,管轴140通过管轴轴承141相对于转动的输出轴130静支撑于管轴透盖处,由于齿轮箱100内的润滑油系统需要对输出轴轴承131、管轴轴承141 进行充分的润滑,齿轮箱100的输出轴130、管轴140的轴颈处对应设有避免润滑油泄漏的第一密封部、第二密封部,因此第一密封部、第二密封部的密封性对于半直驱风电至关重要,稍有润滑油泄漏即可污染发电机200导致严重后果;
27.第一密封部包括不少于两个第一环腔300,第一环腔300至少有一个连通有箱外油雾排出部400,第一环腔300还连通有第一箱内回油部330,第一环腔300由相邻的第一挡油环310和/或第一甩油环320围成,第二密封部包括至少一个第二环腔500,第二环腔500由相邻的第二挡油环510和/或第二甩油环520围成,第二环腔500连通有第二箱内回油部530,进一步的,为了满足不同的密封性能设计,得到不同密封等级的密封结构,第一环腔300可同时连通于箱外油雾排出部400、第一箱内回油部330,或第一环腔300择一连通于箱外油雾排出部400、第一箱内回油部330,在输出轴130的轴颈处设置若干道第一环腔300,每道第一环腔300均具有阻止润滑油泄漏的作用,实际使用时,根据实际指标统计发现,经一道第一环腔阻拦后,二道第一环腔内的泄漏的润滑油已经非常少,油脂基数变小加之温度的上升导致油雾的占比较升高,虽然第一环腔300 叠加使用,远离输出轴轴承131方向的第一环腔300内泄漏的润滑油逐渐减少,但是由于输出轴轴承131工作温度很高,产生的热量会使得一部分润滑油雾化,雾化的润滑油可以通过更小的间隙,久而久之形成润滑油泄漏,本实用新型的方案设计为:让这些油雾可以通过箱外油雾排出部400直接排至外界大气中,取代了让油雾积聚在第一环腔 300内或者通过回油结构流回至齿轮箱100内的设计,原有的回油至齿轮箱100内无法彻底消除第一环腔300内气压,这样的气压平衡设计大大释放了第一环腔300内部压力,因此第一挡油环310和第一甩油环320之间迷宫式间隙340中的润滑油不会受气压驱使流动,进而完全杜绝了润滑油向发电机200处泄漏的可能性,距输出轴轴承131最近的第一环腔300连接第一箱内回油部330,保证齿轮箱100内的润滑油全部回至齿轮箱100 内部,距输出轴轴承131最远的第一环腔300连接箱外油雾排出部400,箱外油雾排出部
400直接将第一密封部的第一环腔300与大气连通,以使第一环腔300不受齿轮箱100 内部压力影响,避免其内部压力将油雾泄漏至发电机200,或影响相邻的第一环腔300 破坏其密封性能;
28.第一环腔300设有三个及以上的情况时,距输出轴轴承131最近或最远处之间的第一环腔300可根据齿轮箱功率选择连接第一箱内回油部330和/或箱外油雾排出部400,通过灵活的选择第一箱内回油部330、箱外油雾排出部400,设计不同密封等级的密封结构,可以适配不同齿轮箱油封使用要求,这种模块化设计降低了生产成本,例如,在本实用新型的图1~7示中,第一环腔300设置有四道,本技术说明书中约定沿靠近输出轴轴承131至远离输出轴轴承131方向,各第一环腔300分别命名为依次为一道第一环腔、二道第一环腔、三道第一环腔、四道第一环腔,其中,一道第一环腔连接第一箱内回油部330,四道第一环腔连接箱外油雾排出部400,也就是相对于输出轴轴承131最近处以及最远处的第一环腔300须对应设置第一箱内回油部330、箱外油雾排出部400,这样设计的原因在于:若一道第一环腔直接连接箱外油雾排出部400会造成润滑油的浪费,对齿轮箱100内部结构润滑以及外界环境均不友好,而二道第一环腔、三道第一环腔分别可以择一或同时连接第一箱内回油部330、箱外油雾排出部400,也就是二道第一环腔、三道第一环腔均具有三种选择方式,根据排列组合,第一环腔300设置有四道的情况下,可供选择的第一箱内回油部330、箱外油雾排出部400的使用排布方式可以达到九种模式,根据不同密封需求情况可以选择上述九种模式之一使用,另外几种示范性情况中:若第一环腔300设置有三道,根据上述的排列方式计算,根据不同情况可以选择三种模式之一使用,若第一环腔300设置仅有二道,那么二道第一环腔须同时连接第一箱内回油部330、箱外油雾排出部400;
29.第一箱内回油部330为设于箱体壁101上的油道,箱外油雾排出部400为设于齿轮箱外部的排油管,排油管一端连通于大气,排油管另一端通过第一挡油环310贯通于第一环腔300,第一挡油环310可开孔,排油管通过密封接头连接于该开孔,排油管可弯曲布置在齿轮箱100与发电机200之间的安装腔中,为了更好的平衡润滑性能与密封性能,相对于输出轴130的输出轴轴承131最近处的第一环腔300仅由第一挡油环310围成,其余相邻第一环腔300之间通过相互嵌套的第一挡油环310与第一甩油环320间隔开,第一挡油环310和第一甩油环320之间具有阻止润滑油溢出的迷宫式间隙340,距输出轴轴承131最近的第一环腔300采用第一挡油环310单独围成,而未采用第一挡油环310与第一甩油环320嵌套的设计,优点在于此处的齿轮箱100内流动过来的润滑油量较多,若设置第一甩油环320的话,会更容易增加润滑油的压力和温度,当润滑油经第一道第一环腔300的第一挡油环310阻拦后,进入相邻的第一环腔300内的润滑油大大减少,此时再使用第一甩油环320才可以发挥其最优工况,且输出轴轴承131主要承受轴向力,第一甩油环320紧贴输出轴轴承131设置容易产生破坏性的应力,为了避免输出轴轴承131与第一甩油环320直接接触,在输出轴130位于第一密封部处的轴颈处设有轴肩132,第一甩油环320过盈配合于轴肩132低阶侧,相邻于输出轴轴承131的第一挡油环310与轴肩132高阶侧间隙配合,以降低输出轴130运转过程中的阻力;
30.管轴140通过管轴轴承141设于输出轴130的轴向空腔内,第二箱内回油部530为设于输出轴130轴壁内的油道,输出轴130轴壁内的油道包括平行于输出轴130的轴向部531,以及垂直于输出轴130的径向部532,轴向部531、径向部532通过弯折部533 连通,轴向部531外端通过第二甩油环520连通于第二环腔500,相对于管轴轴承141 最远处的第二环腔
500的外侧设有管轴透盖,管轴透盖设有作用于管轴140轴颈的环形油封600,管轴140的轴颈处设置若干第二环腔500,其第二箱内回油部530设置在输出轴130轴壁内,充分利用了输出轴130旋转时的离心力,提高了第二环腔500内润滑油回油至齿轮箱100内部的效率,以上第一甩油环320、第一挡油环310以及第二甩油环520、第二挡油环510均通过销轴700定位。
31.如上所述,尽管参照特定的优选实施例已经表示和表述了本实用新型,但其不得解释为对本实用新型自身的限制。在不脱离所附权利要求定义的本实用新型的精神和范围前提下,可对其在形式上和细节上作出各种变化。