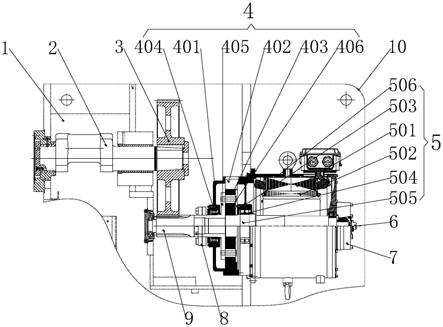
1.本实用新型涉及压力机技术领域,具体涉及一种伺服压力机专用减速电机结构。
背景技术:2.金属塑性成型产业未来发展主要趋势是轻量化、省能源化及高稳定性、高生产率,与此相配套冲压设备亦要积极朝向精密化、高速化、系统化、多种少量弹性化生产、快速换模、节约材料、维修容易、省能源化趋势发展,以智能数控和伺服驱动压力机为代表的中高档机械压力机由此将迎来空前的发展机遇。据锻压协会数据显示,目前国产伺服机械压力机占整个机械压力机比重大概为3%以内,且伺服化趋势明显,市场空间巨大。据行业协会数据预测,到2025年,我国机械压力机的国内销售收入将达到750亿,届时伺服机械压力机保守估计将占到30%比重,伺服压力机市场规模有望达到近300亿。因此,越来越多的厂家采用自适应控制技术,利用伺服电机驱动曲柄滑块机构,通过计算机控制伺服电机的转速,可以精确地控制滑块相对于电机转角的位置,进一步精确地控制压力机冲锤的位置和速度,满足生产加工工艺对冲锤速度特性的要求。伺服压力机在实际生产中将会获得很大的社会效益和经济效益,也充分体现了绿色制造中的节能、降噪的先进思想。由于伺服压力机主传动结构中,大齿轮和齿轮轴是浸油润滑,齿轮轴是安装在齿轮油箱里,因此齿轮轴与伺服电机连接部分必须是密封结构,而且伺服电机的安装要可靠、无间隙连接,拆卸要方便,便于后续维护、维修,因此合理的伺服电机安装结构是非常关键的。另外,为了使电机在扭矩不变的情况下增加压力机输出力,这样就需要增大齿轮传动比来实现,而伺服压力机的运动方式为正反转和加减速频繁切换的运动方式,所以齿轮传动就需要较高的精度,才能满足其动态响应精度,所以增加的齿轮箱的设计就非常重要。
3.现有技术的缺陷和不足:
4.现有技术中为了增加压力机输出力,有以下四种解决方案,但都有其缺点和不足,下面逐一分析。
5.1、现有方案一,为增大压力机输出力,最简单的方式是加大伺服电机的输出扭矩。其缺点是:加大伺服电机的扭矩一方面会使伺服电机的尺寸变大,可能会导致与机床安装尺寸不匹配的问题,另一方面,伺服电机的成本几乎使与输出扭矩成正比,这样无疑会大大增加压力机床的制造成本,使其不具备良好的经济性和市场推广性;
6.2、现有方案二,为增大压力机输出力,用两个或多个小扭矩的伺服电机来驱动同一套传动机构。其缺点是:需要两套或多套驱动系统和同步控制系统,增加了控制系统的难度,电机的同步控制精度和两对或多对齿轮的传动间隙的一致性精度都会影响整个机床的运动精度和噪音,传动精度和可靠性降低。传动系统多了一组一致性精度需要保证,加大了机床的制造难度,在批量生产的机床上难推广;
7.3、现有方案三,为增大压力机输出力,通过增加一级普通的直齿轮传动,增大总传动比,提高最终的扭矩输出来提高压力机的力输出。其缺点是:由于增加的普通直齿轮传动,其传动精度低,不能满足高动态响应精度。直齿轮传动啮合度低,线速度允许值较低,因
此,电机输入转速受限不能太高,使整机的生产效率较低。
8.4、现有方案四,为增大压力机输出力,通过增加一级行星齿轮箱,增大总传动比,提高最终的扭矩输出来提高压力机的力输出。其缺点是:由于增加了行星齿轮箱,其机床传动系统加长,压力机床前后方向尺寸变大,影响机床的结构布置和整机协调性,另外齿轮箱热功率受限需要单独的冷却系统,成本增加。
技术实现要素:9.本实用新型所要解决的技术问题是:为了克服现有技术中的不足,本实用新型提供一种伺服压力机专用减速电机结构。
10.本实用新型解决其技术问题所要采用的技术方案是:一种伺服压力机专用减速电机结构,包括机体、曲轴、大齿轮、大齿轮箱体、齿轮轴、行星齿轮箱和伺服电机,其中,所述曲轴设置在机体内部,且曲轴一端与设置在大齿轮箱体内的大齿轮连接,所述行星齿轮箱和伺服电机集成在一起且共享作为支撑的主传动轴承,缩短了结构尺寸;且浸油安装于大齿轮箱体内,所述齿轮轴一端与行星齿轮箱传动连接,另一端与大齿轮啮合。
11.进一步,所述伺服电机包括电机壳体,以及设置在电机壳体内的电机定子、电机转子、电机轴承座、电机轴承和电机轴,所述电机转子设置在电机轴的外侧,电机定子设置在电机转子外侧,所述电机轴一端延伸出电机壳体且端部安装有编码器和制动器,电机轴另一端为输出端,所述电机轴承设置在电机轴的输出端上,且电机轴承通过电机轴承座与电机壳体连接,所述电机输出端延伸出电机轴承的端部上设有与行星齿轮箱的太阳轮连接的外花键。
12.进一步,所述行星齿轮箱包括齿轮箱轴承座、外齿圈、行星轮、齿轮箱轴承、行星轮支架和太阳轮,所述太阳轮位于电机轴承远离电机转子的一侧,所述太阳轮上设有内花键,通过内花键和外花键将所述太阳轮固定安装在电机轴上,所述外齿圈通过定位安装固定在电机轴承座上,所述行星轮设置在行星轮支架上,且行星轮外侧与外齿圈啮合,内侧与太阳轮啮合;所述行星轮支架远离行星轮的一端上设有齿轮箱轴承,所述齿轮箱轴承通过齿轮箱轴承座与外齿圈连接,且所述齿轮箱轴承座与外齿圈定位安装;所述行星轮支架延伸出齿轮箱轴承的一端上设有锁紧套,所述齿轮轴穿过行星轮支架中心孔,通过锁紧套抱紧固定在齿轮轴上。
13.具体的,由于齿轮轴与行星轮支架之间通过锁紧套锁紧,因此,所述齿轮轴与行星轮支架中心孔过盈连接,从而保证了传动的稳定性,以及传动精度。
14.具体的,所述电机轴承为主传动轴承。
15.由于集成在一起的行星齿轮箱和伺服电机是整体安装在大齿轮箱体内,为了保证密封性,避免行星齿轮箱和伺服电机与大齿轮箱体之间互相串油,进一步,所述齿轮箱轴承座与外齿圈的连接端面之间设有第一密封圈,所述外齿圈与电机轴承座的连接端面之间设有第二密封圈,所述电机轴承座与电机壳体的连接端面之间均设有第三密封圈。
16.进一步,所述电机轴承座的外缘设有安装法兰,所述安装法兰与机体之间设有第四密封圈,防止漏油。
17.进一步,为了避免大齿轮箱体和行星齿轮箱之间的油互串,所述齿轮箱轴承的两侧面均设有第一轴承端盖,所述第一轴承端盖与行星轮支架的连接面之间设有挡油槽。
18.进一步,所述电机轴承的两侧面均设有第二轴承端盖,电机轴承与靠近伺服电机一侧的第二轴承端盖的连接面之间设有第五密封圈,靠近伺服电机一侧的第二轴承端盖与电机轴和电机轴承的连接面之间设有骨架滑动密封圈,且骨架滑动密封圈外侧的第二轴承端盖与电机轴的连接面之间设有挡油槽;靠近行星齿轮箱一侧的第二轴承端盖与电机轴的连接面之间设有挡油槽。
19.传动原理:伺服电机轴端部为外花键,行星齿轮箱的太阳轮为内花键,通过内外花键将太阳轮安装在电机轴上,内外花键连接为常规的连接方式;电机轴输出端设计有电机轴承支撑,且电机轴承通过电机轴承座固定安装在电机的定子外壳上,行星齿轮箱的外齿圈通过定位安装固定在电机轴承座上,行星轮通过支架固定,行星轮支架设置有齿轮箱轴承,齿轮箱轴承座与外齿圈定位安装,行星轮支架上设置有锁紧套,齿轮轴穿过行星轮支架中心孔,通过锁紧套抱紧固定,这样齿轮轴就和行星轮的传动连接就固定好了,齿轮轴带动大齿轮,大齿轮带动曲轴旋转,完成整个动力的传输过程。
20.本实用新型的有益效果是:本实用新型提供的一种伺服压力机专用减速电机结构,通过将行星齿轮箱和低速大扭矩伺服电机集成设计,共享主传动轴承,使其成本降低的同时,结构尺寸减小,采用现有小吨位压力机使用的标准伺服电机可直接安装在大吨位压力机上,并满足其压力机输出的需求。另外,由于是将齿轮箱和伺服电机集成,大大降低了设备制造厂的加工装配难度,适合批量生产,且齿轮箱安装在现有大齿轮箱体里面,浸油安装,齿轮箱可通过大齿轮油箱冷却,不需要单独的冷却系统。齿轮箱由于内嵌在大齿轮箱体里,所以安装齿轮变短,不影响整个机床的结构布置和协调性。由于齿轮轴和行星轮支架是过盈连接,不存在间隙,连接后动态响应精度无影响,伺服电机正反转和加减速的控制精度高;对后续反复拆卸、维修齿轮轴或更换制动器和维修伺服电机,都可以分别单独拆卸维护,为后续的维修保养提供了便利和可行性解决方案。
附图说明
21.下面结合附图和实施例对本实用新型作进一步说明。
22.图1是本实用新型伺服压力机专用减速电机结构的结构示意图。
23.图2是图1中行星齿轮箱和伺服电机的放大结构示意图。
24.图3是密封圈位置示意图。
25.图4是图2中a处的放大结构示意图。
26.图5是图2中b处的放大结构示意图。
27.图中:1、机体,2、曲轴,3、大齿轮,4、行星齿轮箱,401、齿轮箱轴承座,402、外齿圈,403、行星轮,404、齿轮箱轴承,405、行星轮支架,406、太阳轮,407、第一轴承端盖,5、伺服电机,501、电机定子,502、电机转子,503、电机轴承座,504、电机轴承,505、电机轴,506、电机壳体,507、第二轴承端盖,6、编码器,7、制动器,8、锁紧套,9、齿轮轴,10、大齿轮箱体,11、第一密封圈,12、第二密封圈,13、第三密封圈,14、第四密封圈,15、安装法兰,16、第五密封圈,17、骨架滑动密封圈,18、挡油槽。
具体实施方式
28.现在结合附图对本实用新型作详细的说明。此图为简化的示意图,仅以示意方式
说明本实用新型的基本结构,因此其仅显示与本实用新型有关的构成。
29.如图1和图2所示,本实用新型的一种伺服压力机专用减速电机结构,包括机体1、曲轴2、大齿轮3、大齿轮箱体10、齿轮轴9、行星齿轮箱4和伺服电机5,其中,所述曲轴2设置在机体1内部,且曲轴2一端与设置在大齿轮箱体10内的大齿轮3连接,所述行星齿轮箱4和伺服电机5集成在一起且共享作为支撑的主传动轴承,缩短了结构尺寸;且浸油安装于大齿轮箱体10内,所述齿轮轴9一端与行星齿轮箱4传动连接,另一端与大齿轮3啮合,大齿轮箱体10设置在机体1的一侧,大齿轮3、行星齿轮箱4和伺服电机5均设置在大齿轮箱体10内部。
30.伺服电机5包括电机壳体506,以及设置在电机壳体506内的电机定子501、电机转子502、电机轴承座503、电机轴承504和电机轴505,所述电机转子502设置在电机轴505的外侧,电机定子501设置在电机转子502外侧,该伺服电机5为内转子电机;所述电机轴505一端延伸出电机壳体506且端部安装有编码器6和制动器7,电机轴505另一端为输出端,所述电机轴承504设置在电机轴505的输出端上,且电机轴承504通过电机轴承座503与电机壳体506连接,所述电机输出端延伸出电机轴承504的端部上设有与行星齿轮箱4的太阳轮406连接的外花键。
31.行星齿轮箱4包括齿轮箱轴承座401、外齿圈402、行星轮403、齿轮箱轴承404、行星轮支架405和太阳轮406,所述太阳轮406位于电机轴承504远离电机转子502的一侧,所述太阳轮406上设有内花键,通过内花键和外花键将所述太阳轮406固定安装在电机轴505上,所述外齿圈402通过定位安装固定在电机轴承座503上,所述行星轮403设置在行星轮支架405上,且行星轮403外侧与外齿圈402啮合,内侧与太阳轮406啮合;所述行星轮支架405远离行星轮403的一端上设有齿轮箱轴承404,所述齿轮箱轴承404通过齿轮箱轴承座401与外齿圈402连接,且所述齿轮箱轴承座401与外齿圈402定位安装;所述行星轮支架405延伸出齿轮箱轴承404的一端上设有锁紧套8,所述齿轮轴9穿过行星轮支架405中心孔,通过锁紧套8抱紧固定在齿轮轴9上,实现齿轮轴9与行星轮支架405中心孔过盈连接,从而保证了传动的稳定性,以及传动精度。
32.如图3所示,集成在一起的行星齿轮箱4和伺服电机5是整体安装在大齿轮箱体10内,为了保证密封性,避免行星齿轮箱4和伺服电机5与大齿轮箱体10之间互相串油,所述齿轮箱轴承座401与外齿圈402的连接端面之间设有第一密封圈11,所述外齿圈402与电机轴承座503的连接端面之间设有第二密封圈12,所述电机轴承座503与电机壳体506的连接端面之间均设有第三密封圈13。所述电机轴承座503的外缘设有安装法兰15,所述安装法兰15与机体1之间设有第四密封圈14,防止漏油。
33.为了防止串油,除了在上述连接端面之间设置密封圈之外,其余轴承压盖与轴接触位置均设置有挡油槽,具体如下:
34.如图4所示,齿轮箱轴承404的两侧面均设有第一轴承端盖407,所述第一轴承端盖407与行星轮支架405的连接面之间设有挡油槽18。
35.如图5所示,电机轴承504的两侧面均设有第二轴承端盖507,电机轴承504与靠近伺服电机5一侧的第二轴承端盖507的连接面之间设有第五密封圈16,靠近伺服电机5一侧的第二轴承端盖507与电机轴505和电机轴承504的连接面之间设有骨架滑动密封圈17,且骨架滑动密封圈17外侧的第二轴承端盖507与电机轴505的连接面之间设有挡油槽18;靠近行星齿轮箱4一侧的第二轴承端盖507与电机轴505的连接面之间设有挡油槽18。
36.以上述依据本实用新型的理想实施例为启示,通过上述的说明内容,相关的工作人员完全可以在不偏离本实用新型的范围内,进行多样的变更以及修改。本项实用新型的技术范围并不局限于说明书上的内容,必须要根据权利要求范围来确定其技术性范围。