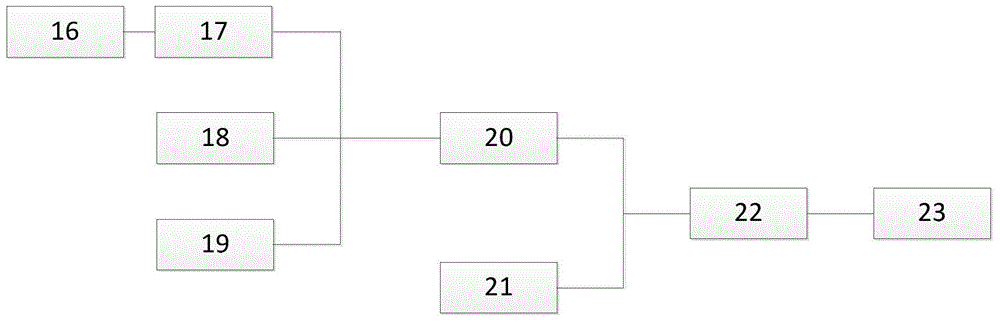
本发明涉及锅炉能耗诊断领域,尤其涉及的是智能化诊断和潜力分析的方法和系统。
背景技术:
:在全球能源安全和气候变暖形势日益严峻的情况下,迫切要求实施高效、低污染和低排放的技术经济模式。近年来,我国能源利用量大幅增加,尽管新能源技术开发使煤炭比例有所减低,但在未来相当长的一段时间内,以煤炭为主的能源结构不会发生根本性改变。2010年,中国工业锅炉总耗煤量约6亿吨,占中国煤炭消耗总量的1/5,多数工业锅炉的实际运行效率约只有70%左右,只有极少量锅炉的效率能够达到80%,能源利用率低,能耗大。排烟热损失是燃煤锅炉各项热损失中最大的一项,降低排烟温度、回收烟气余热是提高锅炉效率的最直接和最有效的途径。一般地,锅炉的排烟温度每降低15℃~20℃,锅炉效率可提高1%。由此可见,中国工业锅炉存在着很大的节能潜力和节能空间。通过技术查新报告显示,目前现有技术大多是通过对锅炉结构的改进,如增加省煤器、改进换热盘管等,达到提高锅炉效率的目的,而针对工业锅炉系统能耗诊断及节能潜力分析的方法则没有相关报道。技术实现要素:针对现有技术中只对锅炉结构本身进行效率改进的问题,本发明的目的之一在于提供一种锅炉系统能耗智能化诊断和节能潜力分析方法,该方法通过对锅炉系统能耗诊断工具和潜力分析,提出相应的节能方案,有助于提高耗能企业的经济效益、能源应用效率监测和检测,达到节能减排的目的。为了实现上述目的,本发明采用的技术方案如下:一种锅炉系统能耗智能化诊断及潜力分析方法,其包括以下步骤:步骤1、存储相互关联和相互调用的监测数据、标准数据和参考数据;其中,所述监测数据为通过分项计量和监测工具采集锅炉系统测试点的数据,所述标 准数据由国家规定的锅炉能效指标数据整理而成,所述参考数据为与所述锅炉系统能耗相关的气象以及燃料分析参数;步骤2、基于所述监测数据和参考数据,计算热损失、空气过量系数和锅炉系统热效率;步骤3、将所述锅炉系统热效率、空气过量系数以及监测数据中的炉渣成份含量、炉体表面温度、排烟温度和烟气成分与所述标准数据进行对比分析,获得所述锅炉系统的节能潜力;步骤4、依据所述节能潜力的结果,自动生成锅炉系统节能潜力分析文档,并制定节能措施和针对节能措施对锅炉系统中的能耗设备进行调整生成节能方案。所述锅炉系统包括给水泵、锅炉给水进口、第一换热器、锅筒、锅炉蒸汽/热水出口、鼓风机、燃烧机进风口、第二换热器、燃烧机、锅炉燃料、燃烧机燃料进口、燃烧机烟气出口、锅炉烟气出口、烟囱、锅炉炉渣出口,锅炉用水通过给水泵进入锅炉给水进口形成锅炉给水,锅炉给水通过第一换热器进入锅筒,锅筒内的水通过燃烧机加热,产生蒸汽或热水,送至锅炉蒸汽/热水出口供用户使用;室外空气通过鼓风机进入燃烧机进风口形成锅炉空气,锅炉空气通过第二换热器进入燃烧机,锅炉燃料通过燃烧机燃料进口进入燃烧机,室外空气和燃料在燃烧机内充分燃烧,燃烧后的炉渣通过锅炉炉渣出口排出,燃烧机排放的烟气通过燃烧机烟气出口,首先进入第二换热器与锅炉空气进行热交换,其次进入第一换热器与锅炉给水进行热交换,再次进入锅炉烟气出口,最后进入烟囱排出。所述热损失包括排烟热损失q2、气体未完全燃烧热损失q3、固体未完全燃烧热损失q4、锅炉散热损失q5和灰渣物理热损失q6;其中:排烟热损失q2是由于锅炉系统排烟带走的热量所造成的损失,计算如下:q2=(x+yαpy)(tpy-tlk100)(1-q4100)---(1)]]>其中,x、y为燃料计算系数,根据燃料种类进行选取;αpy为空气过量系数,tpy,tlk为监测数据中的锅炉烟气出口处的排烟温度和鼓风机处入炉空气温度;为修正系数;气体未完全燃烧热损失q3是由于可燃气体未燃烧放热就随烟气离开锅炉系 统而造成的热损失,与锅炉烟气出口处排烟中一氧化碳的浓度有关:当所述一氧化碳的浓度小于等于0.05%或者500ppm时,q3=0.2;当所述一氧化碳的浓度大于0.05%且小于等于0.1%、或者大于500ppm且小于等于1000ppm时,q3=0.5;当所述一氧化碳的浓度大于0.1%或者1000ppm时,q3=1;所述一氧化碳的浓度通过锅炉烟气出口处排出的烟气化验分析所得;固体未完全燃烧热损失q4针对燃煤锅炉系统,燃料中未燃烧或未燃尽碳造成的热损失,计算如下:q4=328.66×AarQnet,v,ar×(αfhCfh100-Cfh+αlmClm100-Clm+αlzClz100-Clz)---(2)]]>其中,Aar为燃料收到基灰分,通过燃料分析得到;Qnet,v,ar为燃料收到基低位发热量,通过燃料分析得到;Cfh为飞灰可燃物含量,通过锅炉烟气出口处排出的烟气化验分析得到;Clm为漏煤可燃物含量,通过炉排缝隙碳颗粒化验得到,只存在于层燃炉中;Clz为炉渣可燃物含量,通过锅炉炉渣出口得到的炉渣化验得到;αfh、αlm、αlz分别为飞灰、漏煤、炉渣含灰量占入锅炉燃料总量的重量百分比,αfh+αlm+αlz=100;锅炉散热损失q5是由于锅炉本体及锅炉内各种管道、附件的温度高于环境温度而散失的热量:q5=1670FBQr×100%---(3)]]>其中,F为锅炉散热表面积,由参考数据获得;对于燃油和燃气锅炉而言,B为监测数据中的燃料耗量;Qr为监测数据中的输入热量;对于电锅炉:BQr=3600N(4)N为耗电量,通过电锅炉中电压和电流的监测数据计算获得;灰渣物理热损失q6只计算炉渣的物理热损失,飞灰、漏煤的物理热损失不计,计算公式如下:q6=αlzAar(ct)lzQnet,v,ar(100-Clz)×100%---(5)]]>c为炉渣比热容;t为炉渣温度;锅炉系统热效率η通过锅炉系统反平衡热效率计算获得:η=1-q2-q3-q4-q5-q6(6)。所述空气过量系数αpy的计算为:当燃料为煤或油时:当燃料为气时:其中,O2‘,CO′,H2‘,CmH′n,RO2‘,CH4′,N2′分别为锅炉烟气出口排烟处气体O2、CO、H2、CmHn、RO2、CH4、N2体积百分比,通过监测数据得出;CO2,CO,CmHn,H2S,N2分别为燃料成分中气体CO2、CO、CmHn、H2S、N2体积百分比,通过监测数据得出。当式(7)和式(8)中各气体体积百分比无法测出时,通过下表:选取过量空气系数。根据排烟热损失q2、气体未完全燃烧热损失q3、固体未完全燃烧热损失q4分别与空气过量系数αpy关系获取最佳空气过量系数,以提高锅炉系统的节能潜力,其方法为作图法:以横坐标为空气过量系数αpy和纵坐标为热损失建立平面坐标系,通过选取不同的空气过量系数αpy在该平面坐标系中绘制排烟热损失q2、气体未完全燃烧热损失q3和固体未完全燃烧热损失q4之和的曲线,该曲线上纵坐标最小的点所对应的横坐标即为最佳空气过量系数。所述节能潜力从经济性、节能性和环保性进行判断,其包括以下步骤:由锅炉系统正平衡效率的计算公式:η=q1=Q1BQr---(9)]]>可知,在需求和燃料成分不变的情况下,锅炉系统热效率η与燃料耗量B成反比,因此:经济性节能潜力:(B1-B2)×C×T;节能性节能潜力:(B1-B2)×T;环保性节能潜力:(B1-B2)×a×T;其中,q1为锅炉系统热利用效率;Q1为锅炉系统有效利用的热量,B1、B2分别为节能方案实施前后燃料耗量,C为燃料市场价格,a为烟气排放量,T为锅炉系统运行时间。所述节能方案至少为减少排烟温度、改变空气过量系数、改变燃料性质和燃烧方式中的一种或多种。本发明的另一目的在于提供一种锅炉系统能耗智能化诊断和节能潜力分析系统,该系统通过对锅炉系统能耗诊断工具和潜力分析,提出相应的节能方案,有助于提高耗能企业的经济效益、能源应用效率监测和检测,达到节能减排的目的。为了实现上述目的,本发明采用的技术方案如下:一种锅炉系统能耗智能化诊断及潜力分析系统,其包括:数据存储单元,用于存储相互关联和相互调用的监测数据、标准数据和参考数据;其中,所述监测数据为通过分项计量和监测工具采集锅炉系统测试点的数据,所述标准数据由国家规定的锅炉能效指标数据整理而成,所述参考数据为与所述锅炉系统能耗相关的气象以及燃料分析参数;能耗诊断单元基于所述监测数据和参考数据,计算热损失、空气过量系数和锅炉系统热效率;节能潜力分析单元,用于将所述锅炉系统热效率、空气过量系数以及监测数据中的炉渣成份含量、炉体表面温度、排烟温度和烟气成分与所述标准数据进行对比分析,获得所述锅炉系统的节能潜力;节能方案生成单元,用于依据所述节能潜力的结果,自动生成锅炉系统节能潜力分析文档,并制定节能措施和针对节能措施对锅炉系统中的能耗设备进行调整生成节能方案。本发明的有益效果:本发明通过提供一种高效、易用、可量化的能耗诊断技术和潜力分析手段,提高锅炉系统能源利用效率,科学及时提出节能改造方案。有助于提高耗能企业的经济效益、能源应用效率监测和检测,为国家节能减排做贡献。附图说明图1为本发明锅炉系统的结构示意图;图2为本发明一种锅炉系统能耗智能化诊断及潜力分析系统的结构框图;图3为作图法获得的最佳空气过量系数的示意图。具体实施方式下面结合具体实施方式对本发明作进一步的说明。参见图1和图2,本发明提供的系统包括给水泵1、锅炉给水进口2、第一换热器3、锅筒4、锅炉蒸汽/热水出口5、鼓风机6、燃烧机进风口7、第二换热器8、燃烧机9、锅炉燃料10、燃烧机燃料进口11、燃烧机烟气出口12、锅炉烟气出口13、烟囱14、锅炉炉渣出口15、分项计量和监测工具16、监测数据17、标准数据18、参考数据19、数据存储单元20、能耗诊断单元21、节能潜力分析单元22和节能方案生成单元23。所述给水泵1、锅炉给水进口2、第一换热器3、锅筒4、锅炉蒸汽/热水出口5、鼓风机6、燃烧机进风口7、第二换热器8、燃烧机9、锅炉燃料10、燃烧机燃料进口11、燃烧机烟气出口12、锅炉烟气出口13、烟囱14、锅炉炉渣出口15组成锅炉系统测试的基本单元。所述锅炉用水通过给水泵1进入锅炉给水进口2,锅炉给水通过第一换热器3进入锅筒4,锅筒4内的水通过燃烧机加热,产生蒸汽或热水,送至锅炉蒸汽/热水出口5供用户使用。室外空气通过鼓风机6进入锅炉空气进口7,锅炉空气通过第二换热器8进入燃烧机9,锅炉燃料(煤/油/气等)10通过燃烧机燃料进口11进入燃烧机9,室外空气和燃料在燃烧机9内充分燃烧,燃烧后的炉渣通过锅炉炉渣出口15排出,燃烧机排放的烟气通过燃烧机烟气出口12,首先进入第二换热器8和室外空气换热,其次进入第一换热器3和锅炉给水换热,再次进入锅炉烟气出口13, 最后进入烟囱14排出。分项计量和监测工具16包括电能质量分析仪、水表、燃料计量仪表、温湿度表、蒸汽流量计、气体质量分析仪等计量和监测工具,其得到的数据即为监测数据17。标准数据18包括锅炉系统热效率、空气过量系数、炉渣成分含量、炉体表面温度、排烟温度和烟气成分等国家规定的锅炉能效指标。参考数据19包括燃料分析数据、典型气象等数据。数据存储单元20由监测数据17、标准数据18和参考数据19组成。能耗诊断单元21是用来计算锅炉系统热效率、空气过量系数、排烟温度、排烟损失、炉渣可燃物含量和排烟处污染物的浓度。节能潜力分析单元22是用来对比分析能耗诊断单元21得出的锅炉能效等一系列数据和数据存储单元20中的标准数据是否具有节能潜力;节能方案生成单元23是根据节能潜力分析单元22分析的结果自动生成的锅炉节能潜力分析文档。该系统的具体工作原理如下:步骤1:分项计量和监测工具16采集锅炉给水进口2、锅筒4、锅炉蒸汽/热水出口5、燃烧机进风口7、燃烧机燃料进口11、燃烧机烟气出口12、锅炉烟气出口13和锅炉炉渣出口15等测试点的温度、压力、流量、电能、电压、电流和烟气成份等参数。步骤2:将步骤1采集的数据定义为监测数据.步骤3:根据国家规定的标准建立标准数据。步骤4:购买与锅炉系统能耗相关的气象、燃料分析等参数建立参考数据。步骤5:将监测数据、标准数据和参考数据建成相互关联,相互调用的数据存储单元。步骤6:通过能耗诊断单元对数据存储单元数据进行热效率、热损失、排烟温度和成份等指标计算,并给出影响指标的关键因素;热效率计算公式:η=1-q2-q3-q4-q5-q6或者(10)公式(10)中,前者为锅炉系统反平衡热效率计算公式,后者为正平衡热效率,采用正平衡热效率无法分析热损失产生的原因和寻找降低热损的方法,采用反平衡热效率计算公式,有利于对各项热损失进行分析,并寻找改造措施。q2—排烟热损失,%;q3—气体未完全燃烧热损失,%;q4—固体未完全燃烧热损失,%;q5—锅炉散热损失,%;q6—灰渣物理热损失,%。q1—锅炉热利用效率,%;Q1—锅炉系统有效利用的热量,kW。B—燃料耗量,kg/s;监测数据;Qr—输入热量,kJ/kg;监测数据;排烟热损失q2是由于锅炉排烟带走的热量所造成的损失,计算如下:q2=(x+yαpy)(tpy-tlk100)(1-q4100)---(11)]]>x、y—计算系数,根据燃料种类按照表1选取表1不同燃料的计算系数燃料种类褐煤烟煤无烟煤油、气x0.60.40.30.5y3.83.63.53.45αpy—锅炉烟气出口13处的空气过量空气系数,对煤、油对气O2‘,CO′,H2‘,CmH′n,RO2‘,CH4′,N2′分别为锅炉烟气出口13排烟处气体O2、CO、H2、CmHn、RO2、CH4、N2体积百分比,%,通过监测数据得出;CO2,CO,CmHn,H2S,N2分别为燃料(这里的燃料是指燃气)成分中气体CO2、CO、CmHn、H2S、N2体积百分比,%,通过监测数据得出。如果锅炉测试中不要求测试上述参数或上述气体成分体积百分比无法测出,在数值模拟过程中,可根据表2选取过量空气系数:表2锅炉烟气出口13处的过量空气系数αpytpy,tlk分别为监测数据中的锅炉烟气出口处的排烟温度和锅炉空气进口处入炉空气温度,℃;通过温度监测得到;—修正系数,q4具体详见固体未完全燃烧热损失q4求解,公式(14)。对电锅炉:q2为0。气体未完全燃烧热损失q3是由于CO、H2、CH4等可燃气体未燃烧放热就随烟气离开锅炉而熬成的热损失,计算如下:气体未完全燃烧热损失q3与排烟处的一氧化碳CO浓度有关,CO浓度通过化验分析得到,气体未完全燃烧热损失q3的取值见表3表3气体未完全燃烧热损失q3对电锅炉:q3为0。固体未完全燃烧热损失q4是燃料中未燃烧或未燃尽碳造成的热损失,计算如下:对燃煤锅炉,q4=328.66×AarQnet,v,ar×(αfhCfh100-Cfh+αlmClm100-Clm+αlzClz100-Clz)---(14)]]>Aar—燃料收到基灰分,%;通过燃料分析得到;Qnet,v,ar—燃料收到基低位发热量,kJ/kg;通过燃料分析得到;Cfh—飞灰可燃物含量,%;通过锅炉烟气出口处13排出的烟气化验分析得到;Clm—漏煤可燃物含量,%;通过炉排缝隙碳颗粒化验得到,只存在于层燃炉中;Clz—炉渣可燃物含量,%;通过炉渣化验得到;αfh、αlm、αlz—飞灰、漏煤、炉渣含灰量占入炉燃料总量的重量百分比,%,按照表4选取。表4灰、漏煤、炉渣含灰量占入炉燃料总量的重量百分比(%)注:在选取时应满足αfh+αlm+αlz=100对燃油、燃气、电锅炉:q4=0。如果上述燃料数据和化验数据无法得到,在数值计算中采用表5数据。表5锅炉固体未完全燃烧热损失q4设计值(%)锅炉散热损失q5是由于锅炉本体及锅炉范围内各种管道、附件的温度高于环境温度而散失的热量,可采用查表法和计算法两种方法:查表法:表6蒸汽锅炉散热损失q5锅炉出力t/h≤461015203565散热损失q5,%2.92.41.71.51.31.10.8表7热水锅炉散热损失q5锅炉出力MW≤2.84.27.010.5142946散热损失q5,%2.92.41.71.51.31.10.8计算法:包括燃油、燃气和电锅炉的近似计算q5=1670FBQr×100%---(15)]]>F—锅炉散热表面积,m2;试验数据或设备资料(参考数据)。对于燃油和燃气锅炉而言,B为监测数据中的燃料耗量;Qr为监测数据中的输入热量。对于电锅炉:BQr=3600NN—耗电量,kWh/h,通过电锅炉中电压和电流的监测数据计算获得。灰渣物理热损失q6只计算炉渣的物理热损失,飞灰、漏煤的物理热损失不计,计算公式如下,q6=αlzAar(ct)lzQnet,v,ar(100-Clz)×100%---(16)]]>Aar—燃料收到基灰分,%;通过燃料分析得到;Qnet,v,ar—燃料收到基低位发热量,kJ/kg;通过燃料分析得到;Clz—炉渣可燃物含量,%;通过炉渣化验得到;αlz—炉渣含灰量占入炉燃料总量的重量百分比,%,按照表4选取。c—炉渣比热容,kJ/(kg·℃);查表计算;t—炉渣温度,层燃炉和固态排渣煤粉炉t=600℃;硫化床锅炉炉渣t=800℃。对燃油、燃气和电锅炉,q6=0。影响锅炉热损失等指标的关键因素主要通过分析得出,其关键因素主要有:(1)影响锅炉排烟热损失q2的因素有:排烟温度和烟气排量。排烟温度越高,烟气排量越大,则排烟热损失越大,排烟温度增加15-20℃,排烟处的过量空气系数增加0.15,则q2增加越1%。在煤粉炉及油、气锅炉中,排烟热损失是最大的一项热损失,为5-10%。锅炉排烟温度的高低与锅炉受热面积有关。降低排烟温度,一方面可以降低排烟热损失,另一方面也增加了锅炉尾部的受热面积。锅炉排烟量的大小,一般与燃料中的水分、炉膛过量空气系数及锅炉的漏风量有关。若燃料中的水分越多,过量空气系数越大,锅炉漏风越严重,则烟气的排量就越大。(2)影响锅炉气体未完全燃烧热损失q3的因素有:燃料的挥发分含量,炉内过量空气系数、炉膛温度、炉膛结构以及炉内空气动力工况等。若燃料中的挥发分含量高,则炉内可燃气体的量就多,当炉内空气动力工况不良时,就使q3增加。(3)影响锅炉固体未完全燃烧热损失q4的因素有:炉内灰渣量和灰渣含碳量(即灰渣中残炭的含量)。其中,炉内灰渣量与燃料中灰分的百分含量有关,而灰渣中残炭的含量则与燃料性质、燃烧方式、过量空气系数、炉膛温度、锅炉运行工况及司炉的操作调整水平有关。(4)影响锅炉整体热损失的因素还有烟道出口过量空气αpy:一般来说,q2随αpy的增加而增加,q3随αpy的增加而减小,而q4随αpy的增加先减少,后增加。总体来说,上述三项损失之和随αpy的增加先减少,后增加。最佳烟道出口过量空气αpy应使上述三项损失之和达到最小。因此可以采用作图法进行获取,如图3所示:以横坐标为空气过量系数αpy和纵坐标为热损失建立平面坐标系,通过选取不同的空气过量系数αpy在该平面坐标系中绘制排烟热损失q2、气体未完全燃烧热损失q3和固体未完全燃烧热损失q4之和的曲线,该曲线上纵坐标最小的点所对应的横坐标即为最佳空气过量系数。步骤7:节能潜力分析软件根据诊断工具诊断结果,从经济性、节能性、环 保性等方面给出节能潜力,理论上讲上述步骤6计算得到的锅炉系统热效率与标准数据中的锅炉系统热效率进行比对,其相差的量即可视为该锅炉系统的节能潜力参数。但是在实际上,只能通过改变影响锅炉系统热效率指标中的一个或几个变量时,得出相应的热效率,使其接近标准数据。例如排烟温度从tpy,1降低到tpy,2,从公式(11)可知,排烟热损失也相应从q2,1降低到q2,2,从公式(10)可以得出两个热效率当锅炉的热效率从η1提高η2,由锅炉系统热效率的定义出发,锅炉的热效率为锅炉有效利用的热量和输入锅炉系统的总热量的比值,即为用户需求的热量,在需求和燃料成分不变的情况下,热效率η和燃料耗量B成反比,当热效率从η1提高η2,燃料耗量从B1吨/小时减少到B2吨/小时,设定燃料煤的市场价格为C元/吨,燃烧1吨煤所产生的CO2排量为a吨,锅炉年运行时间为t小时,则锅炉系统一年节省燃料为(B1-B2)×t吨/年,一年节省的费用为(B1-B2)×C×t元/年,一年减少CO2排量为(B1-B2)×a×t吨/年,最后从经济性、节能性、环保性三方面给出锅炉系统的节能潜力。步骤8:依据节能分析潜力结果,给出多种节能措施,针对每一种节能措施对能耗设备进行调整生成节能方案。具体是根据步骤7潜力分析的结果,我国可以得出提高热效率的关键因素,例如步骤7的案例可以得出降低排烟温度可以减少排烟热损失,降低排烟温度的主要措施有:可以是适当地增加锅炉尾部的受热面积。在节能调整方案中,可以增加一个换热器在锅炉尾部(例如图1中所示增加的第一换热器3和第二换热器8)。上列详细说明是针对本发明可行实施例的具体说明,该实施例并非用以限制本发明的专利范围,凡未脱离本发明所为的等效实施或变更,均应包含于本案的专利范围中。当前第1页1 2 3