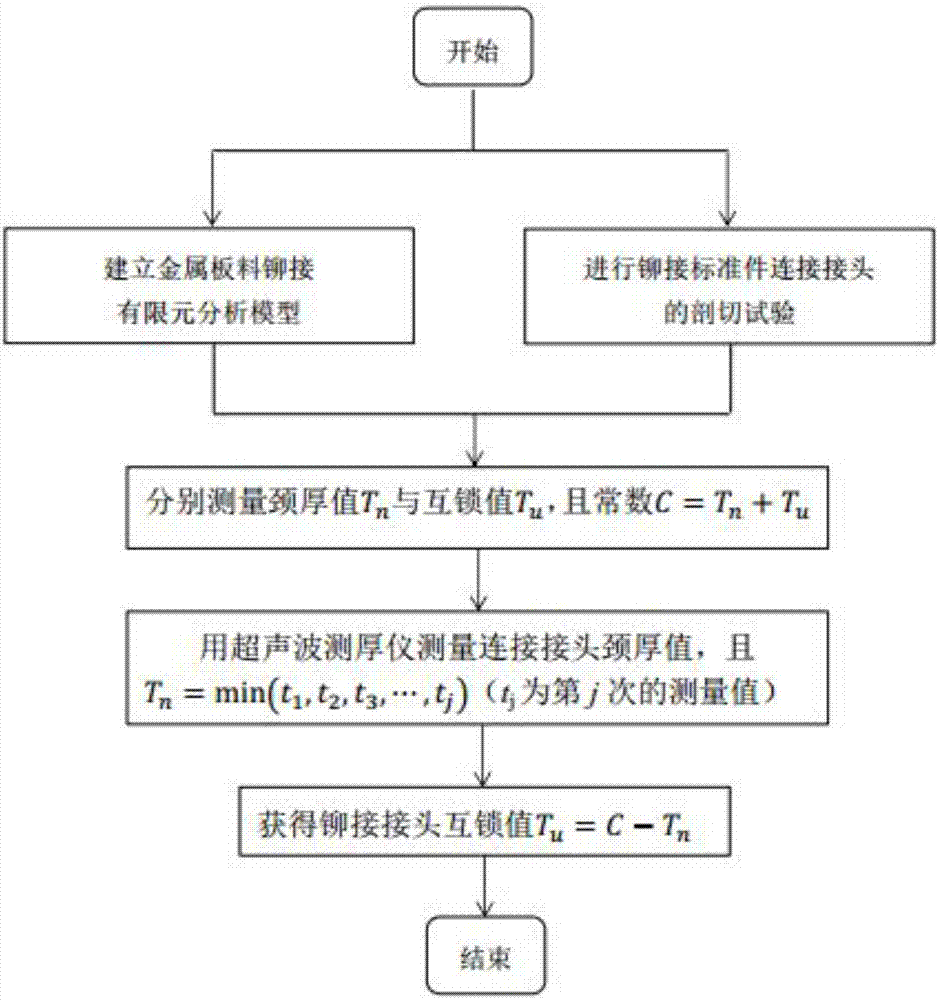
本发明涉及材料连接
技术领域:
,具体涉及一种铆接接头几何参数检测方法。
背景技术:
:轻量化已经成为汽车、航空、航天等工业发展的必然趋势,而大量使用铝合金和高强度钢等先进轻量化材料则是现阶段实现轻量化的重要手段。由于钢、铝热物理属性的巨大差异以及焊缝中脆性金属间化合物的形成,常规的电阻点焊工艺难以实现钢、铝的异种连接。无铆钉自冲铆是一种新兴的连接技术,它可以克服电阻点焊工艺在连接异种金属方面存在的技术瓶颈,同时具有生产过程中不散发烟雾和热量、噪音低、无飞溅、对涂层材料无损害或损害较小的优势,符合未来绿色工业的发展趋势。此外,无铆钉自冲铆工艺连接快速,无需预冲孔,冲、铆一次完成,尤其适合钢-铝、钢-钢等同种或异种材料连接的规模化和自动化生产,具有广阔的应用前景。图1为无铆钉自冲铆连接接头示意图,图中tn为颈厚值,tu为互锁值。颈厚值与互锁值是评价无铆钉自冲铆连接质量的最重要参数,其值大小决定了铆接接头的连接质量和可靠性。颈厚值过小,铆接件在使用过程中容易发生断裂失效。互锁值过小,铆接件在使用过程中容易发生脱扣失效。铆接接头的互锁值因为成型形状复杂的原因,尚不能通过无损测量手段直接测量出来。目前无铆钉自冲铆连接接头的颈厚值与互锁值主要是通过将铆接件接头切开,用测厚工具对两个参数进行测量。这种方法费时、费力,不适用于工业生产。技术实现要素:本发明要解决的技术问题是,针对现有技术存在的上述缺陷,提供了一种铆接接头几何参数检测方法,实现无铆钉自冲铆连接接头几何参数的快速、准确检测,同时实现了无损测量,提高了铆接接头的测量效率,降低了测量误差。本发明为解决上述技术问题所采用的技术方案是:一种铆接接头几何参数检测方法,包括以下步骤:1)在有限元分析软件中建立铆接分析模型,通过分析模型模拟多组无铆钉自冲铆连接过程,求得铆接接头对应两种铆接材料板相应的铆接常数c,并求证得铆接常数c=tn+tu,其中,tn为颈厚值,tu为互锁值;2)用测厚仪器沿铆接接头内侧确定测量区域b;3)用测厚仪器沿铆接接头内侧,在测量区域b中测得铆接接头的颈厚值tn;4)通过铆接常数c和所测得的颈厚值tn,求得铆接接头互锁值tu=c-tn。按照上述技术方案,在所述步骤1)中,通过有限元分析软件中的分析模型模拟多组无铆钉自冲铆连接过程,求得铆接接头对应两种材料板的铆接常数c具体包括以下步骤:通过有限元分析软件中的分析模型开展总试验组数为n的正交试验方法,模拟无铆钉自冲铆连接过程,对每组的颈厚值与互锁值进行测量,令多数情况下,-10%≤δi≤10%,由此可以认为,在误差允许的范围内:tn+tu=c其中,i为试验组号;tni第i组颈厚值;tui为第i组互锁值;δi为相对偏差;n为试验设计总组数,c为铆接常数。按照上述技术方案,在所述的步骤1)中,也可通过多组无铆钉自冲铆连接接头剖切试验替代在限元分析软件中通过分析模型模拟多组无铆钉自冲铆连接过程。按照上述技术方案,在所述的步骤2)中,测量区域b=h-h,其中h为铆接点凹槽深度,h为在铆接接头两端水平处上板料厚度。按照上述技术方案,在所述的步骤3)中,测得铆接接头的颈厚值tn的具体过程为:在测量区域b中多次测量上板料板厚t,从多次测量结果中选取最小值作为铆接接头颈厚值tn=min(t1,t2,t3,···,tj),其中,j为测量次数,tj为第j次的测量值。按照上述技术方案,在所述步骤2)和步骤3)中,测厚仪器为超声波测量仪器或激光测量仪器。本发明具有以下有益效果:本专利
发明内容利用有限元或试验手段获得连接接头的几何参数关系规律,并通过测厚仪测得颈厚值,根据关系规律间接得到互锁值,实现无铆钉自冲铆连接接头几何参数的快速、准确检测,同时实现了无损测量,提高了铆接接头的测量效率,降低了测量误差。附图说明图1是本发明实施例中铆接接头的截面示意图;图2是本发明实施例中铆接接头几何参数检测方法的实施步骤流程图;图3是本发明实施例中铆接有限元软件模拟图;图4是本发明实施例中有限元软件模拟多组正交试验的颈厚值与互锁值曲线图;图5是本发明实施例中有限元软件模拟多组正交试验的颈厚值与互锁值之和分布图;图6是本发明实施例中1#铆接接头连接断面图;图中,1-上板料,2-下板料。具体实施方式下面结合附图和实施例对本发明进行详细说明。参照图1~图3所示,本发明提供的一个实施例中的铆接接头几何参数检测方法,包括以下步骤:1)在有限元分析软件中建立铆接分析模型,通过分析模型模拟多组无铆钉自冲铆连接过程,求得铆接接头对应两种铆接材料板在特定板厚下(特定板厚是指铆接接头的铆接材料板对应的板厚)相应的铆接常数c,并求证得铆接常数c=tn+tu,其中,tn为颈厚值,tu为互锁值,铆接常数与两种材料的种类和板材厚度有关;2)用测厚仪器沿铆接接头内侧确定测量区域b;3)用测厚仪器沿铆接接头内侧,在测量区域b中测得铆接接头的颈厚值tn;4)通过铆接常数c和所测得的颈厚值tn,求得铆接接头互锁值tu=c-tn。进一步地,在所述步骤1)中,通过有限元分析软件中的分析模型模拟多组无铆钉自冲铆连接过程,求得铆接接头对应两种材料板的铆接常数c具体包括以下步骤:通过有限元分析软件中的分析模型开展总试验组数为n的正交试验方法,模拟无铆钉自冲铆连接过程,分析模具的冲头直径、冲头拔模角度、冲头圆角、凹模沟槽深度和凹模深度对颈厚值与互锁值的影响,在有限元分析软件中可直接通过模拟数据计算得到每组的颈厚值与互锁值,对每组的颈厚值与互锁值进行测量,令多数情况下,-10%≤δi≤10%,由此可以认为,在误差允许的范围内:tn+tu=c其中,i为试验组号;tni第i组颈厚值;tui为第i组互锁值;δi为相对偏差;n为试验设计总组数,c为铆接常数。进一步地,在所述的步骤1)中,也可通过多组无铆钉自冲铆连接接头剖切试验替代在限元分析软件中通过分析模型模拟多组无铆钉自冲铆连接过程。进一步地,在所述的步骤2)中,测量区域b=h-h,其中h为铆接点凹槽深度,h为在铆接接头两端水平处上板料厚度,铆接点凹槽深度h和铆接接头两端水平处上板料厚度h均可很方便的测量。进一步地,在所述的步骤3)中,测得铆接接头的颈厚值tn的具体过程为:在测量区域b中多次测量上板料板厚t,从多次测量结果中选取最小值作为铆接接头颈厚值tn=min(t1,t2,t3,···,tj),其中,j为测量次数,tj为第j次的测量值。进一步地,在所述步骤2)和步骤3)中,测厚仪器为超声波测量仪器或激光测量仪器。进一步地,在所述的步骤1)中,通过有限元分析软件中的分析模型模拟多组无铆钉自冲铆连接过程具体包括以下步骤:a.在有限元分析软件(具体实施例中有限元分析软件为abaqus)中,如图1所示,建立铆接分析模型,其中上板料是1.5mm厚的铝合金aa6061-t6,下板料是1.6mm厚的钢板dp590;b.在有限元分析软件中输入铆接板料的材料属性,分别赋予到上板料和下板料,并将冲头、压边圈和凹模设置为刚体;c.建立分析步,采用动态显示算法,并使用ale自适应网格重画技术;d.设置接触与边界条件,凹模、压边圈固定,冲头行程预设3.52mm,各面间的摩擦系数设置为0.15;e.网格划分,接头附近的网格尺寸为0.06×0.06,其余部分网格尺寸为0.006×0.8;f.建立job,并提交运算。本发明提出了一种无铆钉自冲铆连接接头几何参数的快速检测方法,具体实施步骤如下:实施例(一):步骤1:在有限元软件中建立钢、铝铆接分析模型,其中上板料是1.6mm厚的钢板dp590,下板料是1.5mm厚的铝合金aa6061-t6;步骤2:测量有限元软件计算后的模型的颈厚值与互锁值,如图3所示,颈厚值tn为0.61mm,互锁值tu为0.131mm,通过以下公式获得常数c,其中,c=tn+tu=0.61+0.131=0.741mm选用l25(56)正交试验表,在有限元软件中研究模具的冲头直径、冲头拔模角度、冲头圆角、凹模沟槽深度和凹模深度对颈厚值与互锁值的影响,正交试验表和模拟结果如表1所示,对每组的颈厚值与互锁值进行分析,令其中,l1为冲头直径;l2为冲头拔模角度;l3为冲头圆角半径;l4为凹模凹沟槽深;l5为凹槽深度;i为试验组号;tni第i组颈厚值;tui为第i组互锁值;δi为标准差;n为试验设计总组数;表中数据经处理得到图4~图5所示,绝大多数情况下,满足-10%≤δi≤10%,即在误差允许的范围内tn+tu=c;步骤3:进行实际的钢、铝铆接试验,并用超声波测厚仪沿铆接接头内侧测量b处范围内上板料的厚度。然后从多次测量结果中选取最小值作为铆接接头颈厚值,即:tn=min(0.60,0.61,0.80,0.63,0.58,0.75,0.90)mm求到颈厚值tn为0.58mm;步骤4:铆接接头互锁值可以通过下式获得:tu=c-tn=0.741-0.58=0.161mm。实施例(二):步骤1:进行钢、铝无铆钉自冲铆试验,其中上板料是1.6mm厚的钢板dp590,下板料是1.5mm厚的铝合金aa6061-t6,对不同工艺参数下的两个铆接接头进行编号。步骤2:切开1#铆接接头,如图6所示,用测量工具测量连接断面的颈厚值与互锁值,颈厚值tn为0.58mm,互锁值tu为0.17mm,故常数c为:c=tn+tu=0.58+0.17=0.75mm步骤3:用超声波测厚仪沿2#铆接接头内侧多次测量b处范围内上板料的板厚,然后从多次测量结果中选取最小值作为铆接接头颈厚值,即:tn=min(0.63,0.61,0.85,0.56,0.57,0.73,0.89)mm测量结果tn为0.56mm。步骤4:铆接接头互锁值可以通过下式获得:tu=c-tn=0.75-0.56=0.15mm有限元分析软件中的分析模型开展总试验组数为n的正交试验方法,所得到的正交试验和模拟数据表,如表1所示:表1il1/mml2/°l3/mml4/mml5/mmtni/mmtui/mmtli/mmδi15.620.20.41.30.5710.1110.682-1.1%25.630.30.51.40.5640.1480.7123.2%35.640.40.61.50.5580.1540.7123.2%45.650.50.71.60.5770.1380.7153.6%55.660.60.81.70.5850.050.635-7.9%65.830.20.71.70.3840.3340.7184.1%75.840.30.81.30.5760.1630.7397.1%85.850.40.41.40.640.0030.643-6.7%95.860.50.51.50.6130.0680.681-1.2%105.820.60.61.60.5740.1660.747.3%116.040.20.51.60.4340.2850.7194.3%126.050.30.61.70.480.1590.639-7.3%136.060.40.71.30.6590.0350.694-0.6%146.020.50.81.40.5810.1750.7569.6%156.030.60.41.50.6140.0730.687-0.4%166.250.20.81.50.4640.1370.601-12.8%176.260.30.41.60.5080.1510.659-4.4%186.220.40.51.70.450.2620.7123.2%196.230.50.61.30.6560.0890.7458.0%206.240.60.71.40.6460.0980.7447.9%216.460.20.61.40.5340.0450.579-16.0%226.420.30.71.50.4540.2910.7458.0%236.430.40.81.60.4420.1430.585-15.2%246.440.50.41.70.4840.1850.669-3.0%256.450.60.51.30.7010.0280.7295.7%综上所述,本发明提出的检测方法,在确定铆接材料与铆接板厚之后,通过有限元模拟获得铆接常数c,之后再使用测厚仪器测量铆接接头的颈厚值tn,再通过铆接常数c求得互锁值tu=c-tn,传统检测方法相比,对颈厚值与互锁值的测量不需要通过连接断面,即不需要将铆接件切开,实现了颈厚值与互锁值的快速和准确的无损测量,提高了铆接接头的测量效率,降低了测量误差,铆接常数c只与铆接材料和板材厚度有关,故在实际生产中对于确定板材的无铆钉自冲铆可以随意更改工艺参数,颈厚值与互锁值我们也可以快速确定,避免传统测量方法中无铆钉自冲铆连接接头颈厚值与互锁值的传统测量方法费时、费力,而且不能实现无损测量。以上的仅为本发明的较佳实施例而已,当然不能以此来限定本发明之权利范围,因此依本发明申请专利范围所作的等效变化,仍属本发明的保护范围。当前第1页12