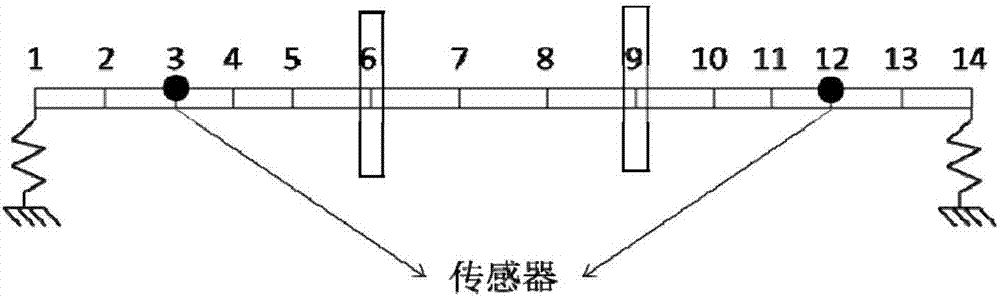
本发明属于旋转机械动平衡
技术领域:
,具体涉及一种转子多点不平衡量识别方法。
背景技术:
:现代社会中,旋转机械应用十分广泛,在诸如钢铁、石化、航空航天等大型生产企业中,包括了风机、汽轮机、电机、燃气轮机、压缩机、鼓风机、航空发动机、泵等关键设备,其运行状况的好坏直接影响企业的生产,一旦因故障停机,将造成巨大的经济损失和严重的后果。因此,企业对这类设备的状况非常关注。大型旋转机械面临的一个最大的问题是振动问题,由于振动而造成机械性能损坏占有很大的比例。在产生振动的各种原因中,最主要的是转子不平衡。据统计,旋转机械的各种振动故障中,不平衡引起的振动占60%左右。因此,动平衡技术对大型旋转机械显得尤为重要。传统转子动平衡方法,如影响系数法和模态平衡法,从提出至今已经有了长足发展,但仍存在一些不足。影响系数法需要多次启停转子来获取系统的影响系数矩阵,模态平衡法则需对转子系统进行精准的模态分析,工程实现难度较大。因此,若能提前了解转子的不平衡分布或者对其具有一定的预估,即对转子进行不平衡量识别,则可大大加快动平衡效率。旋转机械不断向着高速化、复杂化方向发展,若只进行单点不平衡量识别,无法适用于复杂多变的工业现场。因此,寻求一种转子多点不平衡量识别方法对现场动平衡很有必要。技术实现要素:本发明的目的在于克服传统不平衡量识别方法需要多次启停车添加试重的不足,提供了一种转子多点不平衡量识别方法,该方法根据转子固有结构及实测振动信息,识别转子不平衡量。为达到上述目的,本发明采用如下的技术方案:一种转子多点不平衡量识别方法,包括以下步骤:1)获取转子系统固有的结构及模态信息:转子长度l、直径d、密度ρ、弹性模量e,转盘直径d、厚度t和位置,轴承刚度k、阻尼c和支承位置;2)对转子系统进行节点划分,建立转子系统集中质量模型;3)采用riccati传递矩阵,结合步骤2)中集中质量模型,获得转子系统理论不平衡响应;4)采集转子系统实际运行的振动信号;5)结合转子系统理论响应和实测振动信号,使用遗传算法进行不平衡量数目识别;6)在步骤5)所得不平衡量数目的基础上,使用粒子群算法进行不平衡量位置和大小识别。本发明进一步的改进在于,步骤2)中建立转子集中质量模型,具体过程如下:将转子系统离散成圆盘、轴段和支承基本单元,把每个轴段的质量和转动惯量集总到左右两端构成的刚性薄圆盘上,轴段本身则简化成无质量的弾性轴;其中圆盘的属性包括集总质量mi、集总直径转动惯量jdi和集总极转动惯量jpi;集总质量:集总极转动惯量:集总直径转动惯量:节点集总化参数:式中,和分别为原节点i处转盘的质量、直径转动惯量和极转动惯量;轴承处节点等效刚度为:ksi=ki+iω·ci(5)若第i节点存在不平衡,则该节点不平衡量:ui=mie(cosα+isinα)(6)式中,mi为不平衡质量,e、α为不平衡量的幅值和相位。本发明进一步的改进在于,步骤3)中采用riccati传递矩阵法计算不平衡响应,具体步骤如下:设第i个截面的状态矢量为其中mx和my为截面弯矩,qx和qy为截面剪力,x和y为截面挠度,a和b为截面斜率,将此向量记为zi,将每个圆盘和轴段组成一个构件,则构件两端的截面矢量分别记为zi和zi+1,构件所受外力记为fi,构件两端的矢量关系为:zi+1=tizi+fi(7)式中,ti是第i个构件的传递矩阵;将状态矢量中的元素分为{f}、{e}两组,分别代表状态矢量中前四个元素和其余元素,引入riccati变换,则:{f}i={s}i{e}i+{p}i(8)根据左截面边界条件fi=0,ei=0和右界面边界条件fi=0,递推求出各截面状态矢量ei,即转子不平衡响应的复数形式。本发明进一步的改进在于,步骤4)中不平衡振动信号为设定固定转速下、有限传感器位置处振动信号。本发明进一步的改进在于,步骤5)中遗传算法目标函数,引入正则化思想,在传统目标函数的基础上增加l1正则化项,形成新的目标函数,得到不平衡量稀疏性的结果,目标函数如下:式中:u-转子不平衡量向量;xr-转子系统实测振动信号;f(u)-转子系统理论不平衡响应;λ-正则化因子;使用遗传算法进行不平衡数目识别具体步骤如下:a.初始化,随机产生一组初始个体构成初始种群p(t),并通过式(9)评价每个个体的适应度值;b.判断算法是否满足终止条件,即误差是否小于设定值或达到设定迭代次数,若满足终止条件则输出结果,终止运算;否则执行以下步骤;c.选择运算,根据适应度大小,以用户设置的代沟值为选择概率,从种群中选择若干个体;d.交叉运算,根据用户设置的交叉概率,随机指定一个或多个交叉点,对随机选择的两个个体交换交叉点单侧或中间的基因,形成两个新的个体;e.变异运算,根据用户设置的变异概率,将个体基因座上随机选择的部分基因用其他基因替换,形成新的个体;f.经过上述操作得到下一代群体p(t+1),返回步骤b。本发明进一步的改进在于,在步骤6)中所用粒子群算法,在初值选取时并非直接优化变量的整个范围,而是根据不平衡量识别的特点,适当缩小初值选取范围,提高识别准确率,具体步骤如下:a.初始化,随机产生一组初始个体构成初始种群p(t),计算各粒子适应度值;b.判断算法是否满足终止条件,,即误差是否小于设定值或达到设定迭代次数,若满足终止条件则输出结果,终止运算;否则执行以下步骤;c.计算当前粒子下一代运动速度:式中,w为惯性权重因子;c1,c2为学习因子;r1、r2为服从[0,1]均匀分布的随机数;为当前粒子第k代停留位置;为当前粒子历史最好位置;为群体历史最好位置;d.根据粒子运动速度更新粒子位置:e.计算新一代粒子适应度值,返回步骤b。本发明进一步的改进在于,学习因子c1、c2均为2。与现有技术相比,本发明具有以下有益效果:本发明所述的是一种转子多点不平衡量识别方法,通过对转子系统进行集中质量建模,获得系统理论不平衡响应,并与实测不平衡振动信号进行比较,通过遗传算法和粒子群算法对转子不平衡量进行识别。整个识别过程无需添加试重,避免多次启车,缩短检修时间,降低修理费用,减少停机时间,且本发明只需采集某固定转速下振动信息,无需转子多次转速调节,即可识别出转子不平衡量数目、位置、质量及相位信息,大大提高了平衡效率,并可为后续精准的动平衡提供指导。进一步,本发明引入正则化思想,通过遗传算法准确识别转子多点不平衡数目,可为其他不平衡量识别方法提供先验知识。进一步,本发明通过适当缩小粒子群算法初值选取范围,可对不平衡量位置分布进行良好的估计,为现场转子维护和转子动平衡提供参考。附图说明图1为本发明的基本流程图。图2为转子系统节点划分示意图。图3为转子系统集中质量模型各节点信息。图4为转子系统模型前两阶振型。图5为遗传算法识别不平衡量数目的框图。图6为正则化因子中惩罚函数h(n)示意图。具体实施方式为了验证本发明的转子多点不平衡量识别方法的优越性,以下结合附图和实施例对本发明作进一步的详细描述。转子多点不平衡识别方法具体描述如下:1)获取转子系统固有的结构及模态信息:转子长度l、直径d、密度ρ、弹性模量e,转盘直径d、厚度t和位置,轴承刚度k、阻尼c和支承位置;2)对转子系统进行节点划分,建立转子系统集中质量模型;3)采用riccati传递矩阵,结合步骤2)中集中质量模型,获得转子系统理论不平衡响应;4)采集转子系统实际运行的振动信号;5)结合转子系统理论响应和实测振动信号,使用遗传算法进行不平衡量数目识别;6)在步骤5)所得不平衡量数目的基础上,使用粒子群算法进行不平衡量位置和大小识别。为了检验本发明方法的准确性和实用性,做了以下实例。参阅图1所示不平衡量识别流程,即首先通过转子建模,获得转子理论不平衡响应,其次采集转子实际振动信号,提取工频分量幅值和相位,与理论值进行比较,最后通过智能优化算法进行不平衡量识别。因转子不平衡信息包括数目、位置、质量和相位四个方面,直接识别参数较多,故将其分为不平衡数目识别和其他信息识别两部分,依次进行识别。1)针对某一转子系统,获取其固有的结构及模态信息如表1所示。表1转子系统结构信息2)获取结构信息后,对转子进行节点划分如图2所示。将转子划分为13个轴段,共计14个节点;转盘位置为节点6和节点9,传感器位置为节点3和节点12,轴承支承位置为节点1和节点14。3)根据划分的节点,建立转子系统集中质量模型,计算各节点模型参数,转子系统集中质量模型各节点信息如图3所示,主要包括各节点质量、极转动惯量、直径转动惯量、外径、等效抗弯刚度、轴段长度、支承刚度。采用riccati传递矩阵计算转子系统不平衡响应,选择平衡转速为1020rpm,计算转子系统前两阶振型如图4所示。可以看出,一阶振型具有0个节点;二阶振型具有1个节点,且节点两侧质点同一时刻振动相位相反,振型情况与实际相符。4)采集转子振动信号,并通过精确fft对工频分量,即频率为17hz的信号幅值相位进行提取。5)使用遗传算法进行不平衡量数目识别,流程如图5所示。将每一代遗传算法优化参数所得不平衡响应与实际不平衡响应对比,通过目标函数计算适应度值,直至达到收敛准则。因传感器位于节点3和节点12处,设定遗传算法目标函数如下所示:式中:u-转子待优化不平衡量向量;xr3,xr12-转子系统节点3、12实测振动信号;f3,f12-转子系统节点3、12理论不平衡响应;λ-正则化因子。目标函数第一部分为转子残余振动平方和,第二部分为正则化项。根据本转子系统实际振动响应,正则化因子设定如下:λ=107/(2.0503*10-4*xr2-0.0468*xr+2.320)/h(n)(13)式中:xr-转子节点3和节点12实测不平衡振动幅值之和;n-节点位置;h(n)-节点位置n的函数;h(n)函数可看作惩罚函数,如图6所示,对于同一不平衡量,若其位置距离轴承越近,h(n)值越大,目标函数值则越小,从而避免识别结果集中在转子距离轴承最远的节点位置。遗传算法采用二进制编码,最大迭代次数为50,识别范围为[0,100]g.mm,此步骤中假设所有不平衡量相位信息都为0°。6)不平衡量数目识别完成后,采用粒子群算法进行不平衡位置大小识别。不平衡质量范围为[0,100]g.mm,初始粒子范围设为[0,45]g.mm。不平衡相位范围为[0,360],初始粒子范围同识别范围。事实证明,此初始粒子范围可获得更高的识别精度。本转子系统设有两个加重盘,故分别进行单点和两点不平衡量识别。本转子系统单点不平衡量识别结果如表2所示,表中“@”前后分别代表不平衡质量和相位。分别对不同质量和不同相位的不平衡量进行识别,结果表明,识别效果较好。表2单点不平衡量识别结果不平衡量设置识别数目识别位置识别大小节点60.8g@0160.8445g@-1.4213节点61.6g@-45161.8182g@-48.8202节点61.2g@0161.3031g@-0.1565节点61.2g@45161.4400g@45.7317节点61.2g@90161.3291g@91.2589节点61.2g@135161.3575g@133.6578节点61.2g@180161.3303g@183.6312节点61.2g@225161.3202g@223.9846节点61.2g@270161.3334g@265.7787节点61.2g@315161.3031g@315.0562本转子系统两点不平衡量识别结果如表3所示,表中“@”前后分别代表不平衡质量和相位。分别对不同质量和不同相位的不平衡量进行识别,结果表明,不平衡量数目识别完全正确,不平衡大小具有一定识别效果。表3两点不平衡量识别结果当前第1页12