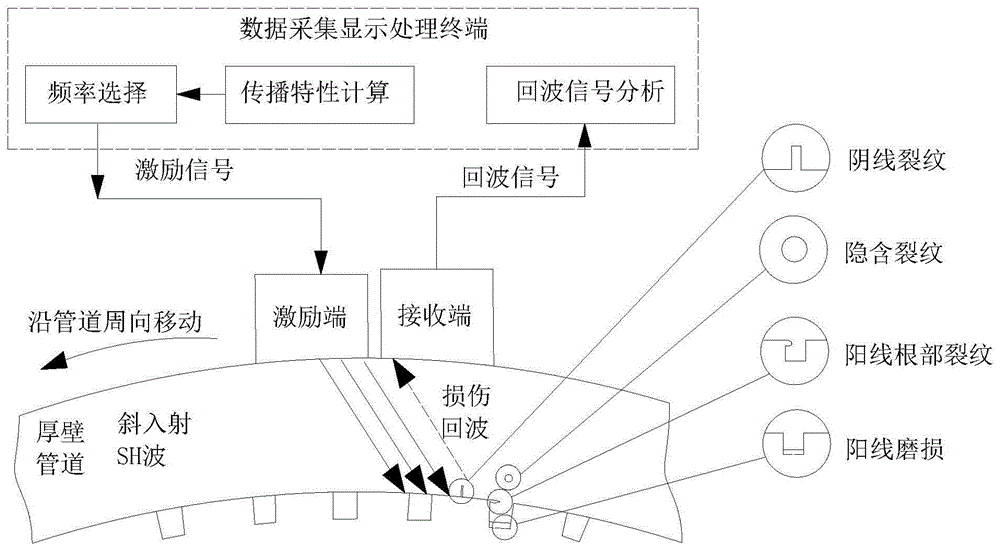
本发明涉及管道无损检测领域,具体是涉及一种管道内膛损伤状态诊断方法。
背景技术:
:厚壁管道常被用于军事装备及其他流程工业中,在使用过程中,管道内壁受到高温(2500℃~3200℃)、高压(140mpa~700mpa)的燃气形成的热冲击应力以及机械摩擦作用,极易造成厚壁管道出现裂纹、磨损、断裂、烧蚀及镀层脱落等损伤。长期使用后内壁会产生较多微损伤,难以预测剩余使用寿命,成为影响构件安全运行的重大隐患。现有的厚壁管道检测手段无法对厚壁管道管壁内部缺陷进行检测,也无法定量检测出厚壁管道损伤尺寸,已不能满足装备保障技术发展趋势。技术实现要素:为解决上述技术问题,本发明提供了一种管道内膛损伤状态诊断方法,能够检测出管道内部的损伤位置和损伤尺寸。为实现上述目的,本发明采用了以下技术方案:一种管道内膛损伤状态诊断方法,该诊断方法用于获取被检测管道内膛的损伤位置和损伤尺寸,包括如下步骤:s1,超声波电磁超声激励端和超声波电磁超声接收端沿同一径向平面设置在被检测管道的外壁上,超声波电磁超声激励端向被检测管道的内膛或内壁发送的信号为发射信号,被检测管道反射出去的信号为反射信号,超声波电磁超声接收端获取该反射信号;建立波形数据库,波形数据库包括管道的无损伤波形和损伤波形;s2,将反射信号对应的波形与波形数据库中的波形进行比对,若反射信号对应的波形与损伤波形相吻合,则该被检测管道为内膛损伤管道,该反射信号为损伤反射信号,进行步骤s3,否则被检测管道为无损伤管道;s3,通过时间δt和信号传播的速度cg计算步骤s2中内膛损伤管道的损伤位置,其中,δt为损伤反射信号传送至超声波电磁超声接收端所用的时间,cg为常数;通过损伤反射信号的幅值获取内膛损伤管道的损伤尺寸。进一步,步骤s2和s3中的反射信号为步骤s1中的反射信号预处理之后的,预处理s1中的反射信号的具体步骤如下:窄带高q值带通滤波器对超声波电磁超声接收端获取的反射信号进行滤波,微弱信号调理器对滤波之后的反射信号进行放大,获取预处理之后的反射信号。进一步,步骤s3中计算内膛损伤管道的损伤位置的具体步骤如下:其中,t为从超声波电磁超声激励端的发射信号至超声波电磁超声接收端接收到反射信号所用的时间,t激励为超声波电磁超声激励端的发射信号的周期,k等于发射信号被反射的次数加一,l为超声波电磁超声激励端与管道损伤处的直线距离,即损伤位置。进一步,步骤s2中损伤波形包括阴线裂纹波形、阳线磨损波形、阳线根部裂纹波形、隐含缺陷波形;损伤反射信号的幅值包括阴线裂纹波形的信号幅值y阴,阳线磨损波形的信号幅值y磨损,阳线根部裂纹波形的信号幅值y阳,隐含缺陷波形的信号幅值y隐;步骤s3中的损伤尺寸包括阴线裂纹波形对应的被检测管道的阴线裂纹沿管道轴向的尺寸x阴,阳线磨损波形对应的被检测管道的阳线沿管道径向的磨损尺寸x磨损,阳线根部裂纹波形对应的被检测管道的阳线根部沿管道周向的裂纹尺寸x阳,隐含缺陷波形对应的被检测管道的隐含缺陷对应的孔沿管道径向的尺寸x隐;y磨损=a2x磨损+b2y隐=a4x隐+b4其中,a1、b1、c1、a2、b2、a3、b3、c3、d3、e3、a4、b4均为常数。进一步优选的,k的计算公式如下:l探头=r2×n×θk=n+2其中,管道在激励端和接收端的位置处的径向截面的圆心为o;r1为损伤位置与圆心o之间的距离,记为直线oa的长度;r2为激励端与与圆心o之间的距离,记为直线ob的长度;a为第一个反射信号的路径与ob之间的夹角;β为第一个反射信号的路径与oa之间的夹角;θ为ob与oa之间的夹角;l探头激励端探头与接收端探头沿圆弧面的距离;n为偶数。进一步优选的,:管道的内直径为155mm,厚度为23.5mm,激励端与接收端沿管道外壁的弧长为81.56mm,k的值取6。进一步,超声波电磁超声激励端向被检测管道的内膛发送的超声导波为斜入射sh波。进一步,超声波电磁超声激励端和超声波电磁超声接收端之间的距离保持不变,且均转动设置在管道外壁上。进一步优选的,a1为-0.09082,b1为1.41307,c1为0.09685,a2为2.09091,b2为3.59364,a3为-0.07284,b3为-0.04597,c3为0.41958,d3为-0.52316,e3为3.74889,a4为2.15939,b4为0.30267。本发明的有益效果如下:(1)本发明通过对反射信号进行分析,计算出损伤位置;提取反射信号的幅值,依据幅值计算出损伤尺寸。本发明的诊断方法适应多种厚壁管道内壁复杂结构的缺陷检测与识别,检测出厚壁管道的内部缺陷以及损伤位置,能够对厚壁管道隐含缺陷进行及时检测,以便维修保障,能够有效降低系统运行维护成本。(2)常用的管道无损检测难以准确检测和定量管道内壁缺陷,效率较低,导致管道提前报废,造成大量资源浪费。本发明针对厚壁管道内壁复杂结构的损伤提供一种基于超声波的检测和定量方法,能够对厚壁管道内壁阴线裂纹、阳线磨损、阳线根部裂纹、隐含缺陷进行有效的检测,便于进一步预估管道的使用寿命,为厚壁管道关键部件结构健康监测提供依据和装备维修保障提供技术支持。(3)斜波在遇到界面不连续或边界处损失能量较少,信号分析较为容易,更适合用于缺陷检测。斜波具有较强的穿透性,常被用于焊缝检测、管道检测、缺陷板检测、试样测厚等。(4)由于超声波本身固有特性,基于超声波的厚壁管道损伤状态定量检测方法能够对厚壁管道内壁缺陷进行检测。本发明分别计算阴线裂纹尺寸、阳线磨损尺寸、阳线根部裂纹尺寸、隐含缺陷尺寸,采用了控制变量法将多变量变化的复杂问题简化为多个单独变量变化的问题。(5)超声波电磁超声激励端和超声波电磁超声接收端之间的距离保持不变,保证信号的反射次数维持不变,便于计算。激励端和接收端安装在套环上,套环套设在管道的外部,当套环携带激励端和接收端旋转一周时,可以检测该段的管道是否有损坏的,不会漏检,提高了检测的准确性。附图说明图1为本发明的管道损伤检测示意图;图2为本发明的管道结构示意图;图3为本发明的损伤定位示意图;图4为本发明的流程图;图5为本发明的阴线裂纹缺陷回波信号对应的波形图;图6为本发明的阴线裂纹尺寸与回波幅值的函数图;图7为本发明的阳线磨损的尺寸与回波幅值的函数图;图8为本发明的阳线根部裂纹的尺寸与回波幅值的函数图;图9为本发明的隐含缺陷的尺寸与回波幅值的函数图;图10为本发明的激励端和接收端沿管道移动的示意图。具体实施方式以下结合实施例和说明书附图,对本发明中的技术方案进行清楚、完整地描述。基于本发明中的实施例,本领域普通技术人员在没有做出创造性劳动前提下所获得的所有其他实施例,都属于本发明保护的范围。实施例一种管道内膛损伤状态诊断方法,该诊断方法用于获取被检测管道内膛的损伤位置和损伤尺寸,包括如下步骤:s1,如图1和图3所示,超声波电磁超声激励端和超声波电磁超声接收端沿同一径向平面设置在被检测管道的外壁上,超声波电磁超声激励端和超声波电磁超声接收端之间的距离保持不变,均转动设置在管道外壁上,如图10所示,沿厚壁管道的周向移动。超声波电磁超声激励端向被检测管道的内膛发送发射信号,本实施中,发射信号为超声导波信号,本实施例中超声导波为斜入射sh波,被检测管道的内膛反射出去的反射信号,本实施例中,反射信号为回波信号,超声波电磁超声接收端获取该回波信号。建立波形数据库,波形数据库包括管道的无损伤波形和损伤波形。本实施中由agilent33220a任意波形发生器生成高达20mhz,稳定、精确、纯净和低失真的正弦输出信号,通过riecga-2500a高功率门控rf脉冲放大器对信号进行放大,经过前置阻抗匹配将高频电流输入到电磁超声探头激励端中,电磁超声探头接收端将接收到微弱振动转化为电流信号,通过后置阻抗匹配系统后,将回波信号输入到高(低)通滤波器和olympus5072pr进行滤波和超低噪音的信号放大,由数据采集卡完成模数转换,并将数据送入安装在计算机上的labview软件界面,从而完成数据采集、波形显示和数据存储,获取样本数据,依据样本数据建立波形数据库,波形数据库包括厚壁管道的无损伤波形和损伤波形。本实施例中,也可以不进行信号的预处理,获取的反射信号微弱,会降低损伤诊断的准确性。s2,将反射信号对应的波形与波形数据库中的波形进行比对,若反射信号对应的波形与损伤波形相吻合,则该被检测管道为内膛损伤管道,该反射信号为损伤反射信号,进行步骤s3,否则被检测管道为无损伤管道;s3,通过时间δt和信号传播的速度cg计算步骤s2中内膛损伤管道的损伤位置,其中,δt为损伤反射信号传送至超声波电磁超声接收端所用的时间,cg为常数。具体过程如下:其中,t为从超声波电磁超声激励端的发射信号至超声波电磁超声接收端接收到反射信号所用的时间,t激励为超声波电磁超声激励端的发射信号的周期,k等于发射信号被反射的次数加一,即激励端的信号被接收端接收到时传播的路径条数,发射信号到达损伤位置为第一条路径,损伤位置将信号反射出去为第二条路径,直至接收端接收到信号时路径的总的条数。l为超声波电磁超声激励端与管道损伤处的直线距离,即损伤位置,本实施例中,如图3所示,k的值为6。l为超声波电磁超声激励端与管道损伤处的直线距离,即损伤位置。k的具体计算过程如下:l探头=r2×n×θk=n+2其中,管道在激励端和接收端的位置处的径向截面的圆心为o;r1为损伤位置与圆心o之间的距离,记为直线oa的长度;r2为激励端与与圆心o之间的距离,记为直线ob的长度;a为第一个反射信号的路径与ob之间的夹角,本实施例中,a为30度;β为第一个反射信号的路径与oa之间的夹角;θ为ob与oa之间的夹角;l探头激励端探头与接收端探头沿圆弧面的距离;n为偶数。本实施例中,厚壁管道的内直径155mm、壁厚23.5mm、长度10mm,激励端与接收端沿管道外壁的弧长为81.56mm。cg=3260m/s,t取59.87μs,t激励取5μs,计算得出被检测厚壁管道损伤位置为距离激励端31.17mm位置处,该距离为直线距离。而被检测厚壁管道实际损伤位置为距离激励端30.61mm位置处,相对误差为0.56mm,如图3所示。表1为阴线裂纹实际损伤位置与通过本发明的方法计算得出的损伤位置。通过如图5所示的损伤反射信号的幅值获取内膛损伤管道的损伤尺寸,损伤尺寸包括阴线裂纹波形对应的被检测管道的阴线裂纹沿管道轴向的尺寸x阴,阳线磨损波形对应的被检测管道的阳线沿管道径向的磨损尺寸x磨损,阳线根部裂纹波形对应的被检测管道的阳线根部沿管道周向的裂纹尺寸x阳,隐含缺陷波形对应的被检测管道的隐含缺陷对应的孔沿管道径向的尺寸x隐。其中,如图2所示,阴线为管道内膛向外部凹下去的部分,阳线管道内膛向中新凸出来的部分。如图1所示,隐含缺陷为管道内部出现的缺陷。下面对阴线裂纹沿管道轴向的尺寸x阴、阳线沿管道径向的磨损尺寸x磨损、阳线根部沿管道周向的裂纹尺寸x阳、隐含缺陷对应的孔沿管道径向的尺寸x隐分别进行介绍。阴线裂纹沿管道轴向的尺寸改变阴线裂纹轴向长度尺寸,保持阴线裂纹的周向宽度和径向深度不变,通过步骤s1中的样本数据建立阴线裂纹尺寸与缺陷回波的曲线图,如图6所示。将被检测厚壁管道对应的缺陷回波信号的幅值输入到轴向长度与回波幅值的曲线图中,获取被检测厚壁管道的阴线裂纹轴向长度尺寸,其中,该曲线图的横坐标为阴线裂纹轴向长度尺寸,纵坐标为回波幅值。y阴=a1x阴2+b1x阴+c1其中y阴为损伤反射信号的幅值,a1、b1、c1均为常数,本实施例中,a1为-0.09082,b1为1.41307,c1为0.09685。阳线沿管道径向的磨损尺寸y磨损=a2x磨损+b2表2给出了阳线磨损尺寸与回波信号的幅值的对应关系。如图7所示,阳线磨损与回波信号的幅值成线性相关,a2、b2均为常数,本实施例中,a2为2.09091,b2为3.59364。阳线根部沿管道周向的裂纹尺寸y阳=a3x阳4+b3x阳3+c3x阳2+d3x阳+e3如图8所示,随着阳线根部裂纹尺寸增加,回波信号的幅值逐渐下降。本实施例中,a3、b3、c3、d3均为常数,本实施例中,a3为-0.07284,b3为-0.04597,c3为0.41958,d3为-0.52316,e3为3.74889。隐含缺陷对应的孔沿管道径向的尺寸y隐=a4x隐+b4如图9所示,隐含缺陷直径与回波信号的幅值成线性相关,本实施例中,a4为2.15939,b4为0.30267。表1表2阳线磨损尺寸/mm回波信号的幅值/10-13mm03.60.0053.610.013.620.023.640.043.670.063.710.083.750.13.80.123.840.143.880.163.940.183.980.24.01当前第1页12