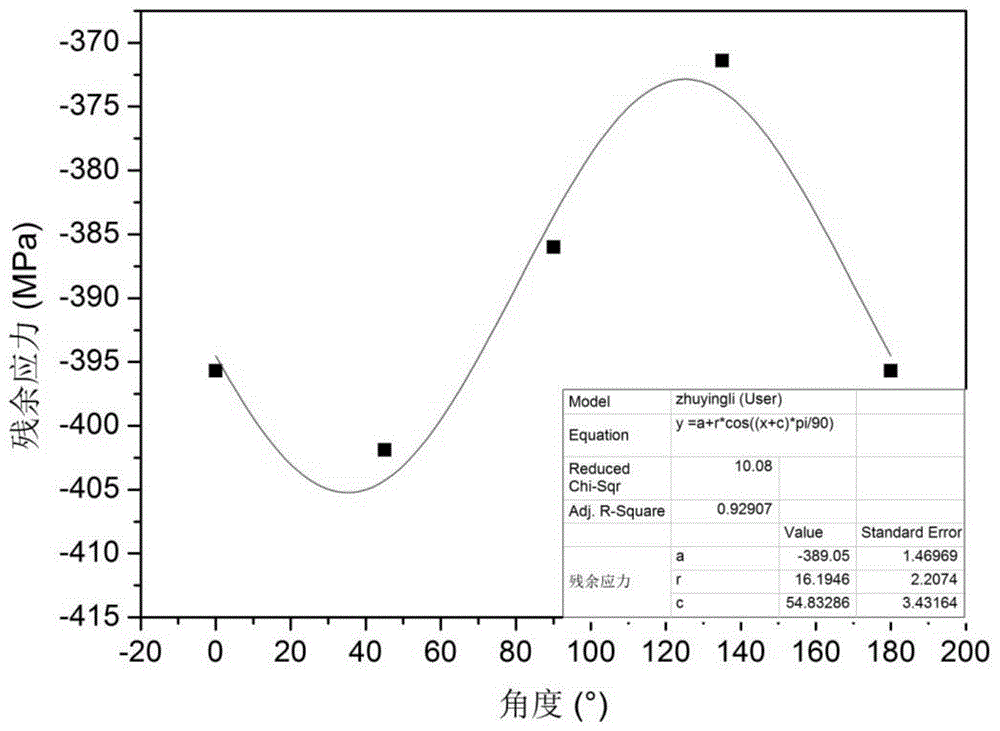
本发明涉及xrd法检测残余应力的准确性检验及切应力计算方法,属于金属材料检测方法
技术领域:
。
背景技术:
:xrd即x-raydiffraction的缩写,中文翻译是x射线衍射。xrd法可以通过对材料进行x射线衍射,分析其衍射图谱,获得材料的成分、材料内部原子或分子的结构或形态等信息,利用xrd法检测金属材料的残余应力是众多xrd法的应用之一。在运用xrd法检测残余应力过程中,难免会由于材料、设备和操作等方面的影响造成检验结果的不可靠,同时在试验过程中采用不同的参考晶面以及数据处理中采用不同的寻峰方式也可能会导致结果的不一致。在国家标准gb/t7004-2017无损检测x射线应力测定方法中,提到了对残余应力检测结果只是进行概略性评估,即测量所得应力值的正反和数量级是否符合人们的预期。标准中所提到的概略性评估很大程度上依赖试验人员的主观预期,并且不能定量的描述测量值与真实值偏差大小,并且当测量值的正反和数量级与预期不符时往往残余应力测量值与真实值之间的差距已经达到了一定的程度。因此需要一种方法可以客观、有效地对残余应力检测结果的准确性进行描述。另外xrd法的检测结果较为单一,不能对平面残余应力状态进行表述。尤其是其原理为通过测量应力状态下晶面距的改变并通过一定的计算获得材料表面沿某一方向上正向残余应力的大小,因此无法对不引起晶面距的改变的切应力进行测量。国家标准gb/t7004-2017中虽提到了测量3个方向后τxy的计算方法,但仅能提供一个方向上切应力的数值而不能提供不同角度下切应力分布情况,并且其依据的数据较少,难以保证计算结果的可信性。xrd测量残余应力的检测结果物理意义是二维平面上沿测量方向残余应力正应力的大小,根据弹性力学的相关理论可推导出该物理量与角度之间存在余弦函数关系,而对应的残余应力切应力则符合同位向的正弦含糊分布。通过对不同角度xrd方法残余应力检测结果进行余弦函数拟合,比较测量结果与余弦函数符合的程度,即可实现对残余应力检测结果准确性的表征,根据拟合参数即可实现对残余应力切应力的计算。技术实现要素:本发明要解决的技术问题是提供xrd法检测残余应力的准确性检验及切应力计算方法,这种方法提供了一种能够对使用xrd法的残余应力检测结果准确性进行评价的手段,避免了因设备和操作问题得出的错误数值被当做正确数值使用,保证了使用xrd法检测残余应力的可靠性和准确性。解决上述技术问题的技术方案是:xrd法检测残余应力的准确性检验及切应力计算方法,它采用以下步骤进行:(1)采用xrd对试样进行多个角度的残余应力测量,检测角度为0°~180°之间选取4个及以上的角度,经数据处理后,获得残余应力检测结果;(2)对测试结果进行拟合,拟合的余弦函数形式为式中θ和σ分布代表测量角度和测量角度下的残余应力检测结果,将检测结果导入到origin软件中,做出角度(θ)—应力值(σ)散点图后运用非线性函数拟合功能对数据点进行拟合,其中角度变量均以角度制数值带入式中,拟合过程中运用余弦函数周期性修正r、β的数值,使r值为正,β值控制在0~180范围内,经多次迭代后获得a、r、β的最佳拟合值;(3)确定a、r、β后,即可获得确定的角度-残余应力值余弦函数关系,将不同的测量角度带入该余弦函数表达式中,得到不同角度下残余应力结果的拟合值;(4)将不同角度的测量值与拟合值进行比较,可分析每个角度上检测结果的精确程度,每个值的偏差可计算测量值与拟合值差值的绝对值,然后求得其余拟合值的百分比表示;(5)将拟合获得参数a、r、β与拟合过程中给出的对应的误差水平进行比较,分析测量结果的整体精确程度,a、r值偏差可用误差水平与拟合值的百分比表示,β值本身与测量时0°角度的选取有关,其误差水平与拟合值的比值意义不大。上述xrd法检测残余应力的准确性检验及切应力计算方法,试样检测的最大及最小主应力的计算公式为σmax,min=a±r,最大主应力方向为0°方向顺时针转过β角度。上述xrd法检测残余应力的准确性检验及切应力计算方法,试样检测的不同角度下切向残余应力分布公式为切应力方向以对应角度顺时针选择90°方向为正。本发明的有益效果是:1.本发明提供了一种xrd测量残余应力的准确性检测方法,使得对xrd的残余应力检测结果有手段对其是否正确进行评估,避免了因设备和操作问题得出的错误数值被当做正确数值使用。2.可根据准确性的检测结果对xrd仪器进行校准,保证xrd设备的正常运行。3.对于不同衍射晶面选择、不同寻峰方式等因素导致的结果不一致的情况,可使用本方法对不同因素选取下的结果进行评价,从而正确选择实验过程中参考晶面、寻峰方式等因素。4.在本方法中,不需要标准试样,而是采用同一试样自身不同角度下的残余应力数据进行对照来确定检验的准确性,操作方便并节省了购买标样的成本。5.采用一定的方式对xrd法的残余应力检测结果进行了整理,进而使xrd法残余应力结果可完备的表述试样表面的二维应力状态,突破了xrd法不能测量切向残余应力的限制,拓宽了xrd法测量残余应力的检测范围,同时提供了一种无损的切向残余应力检测方法。本发明是xrd法检测金属材料的残余应力的创新,本方法提出的残余应力正应力与切应力随角度的变化规律分别符合相同振幅和初位向的余弦函数和正弦函数是发明人首次推导得出,未见以往的各类文献中。在以往的文献中虽然进行了多角度的测量,但并未意识到可从余弦函数拟合的角度去分析,只是对测量结果随角度的变化进行了一般性的描述。对与平面状态下最大、最小主应力方向互相垂直可根据本发明提到的余弦函数很简单地进行证明,而在弹性力学教材中则是采用了更为复杂的基于二次方程的证明方法。基于以上两点本发明所提出的方法是对现有理论的突破,尤其是将其进一步与x射线衍射法的残余应力检测结果进行结合更是首次使用,解决了现有的xrd法检测金属材料的残余应力存在的问题。附图说明图1是本发明的一个实施例的残余应力检测结果余弦函数拟合图;图2是另一个实施例残余应力检测结果余弦函数拟合图;图3是第三个实施例残余应力检测结果余弦函数拟合图;图4是第一个实施例试样表面切向残余应力随角度变化曲线;图5是第三个实施例试样表面切向残余应力随角度变化曲线。具体实施方式本发明推导出不同角度下xrd法的残余应力检测结果应服从余弦函数分布,使用origin软件对4个及以上不同角度残余应力检测结果进行余弦函数拟合,通过比较测量结果与拟合结果的偏差及拟合参数的偏差提供了一种有效的xrd法残余应力检测结果的准确性检验方法,通过拟合获得的参数及相应公式提供了一种残余应力切应力的计算方法。本发明的具体实施步骤如下:(1)采用xrd法对试样在0~180°之间选择4个及以上角度的残余应力测量,获得不同方向上的残余应力检测结果。(2)将结果导入到origin软件中,做出应力值(σ)—角度(θ)散点图后运用非线性函数拟合功能对数据点进行拟合,拟合函数的形式为其中θ变量均以角度制数值带入式中。拟合过程中运用余弦函数周期性修正r、β的数值,使r值为正,β值控制在0~180范围内,经多次迭代后获得a、r、β的最佳拟合值。运用origin软件对散点图进行拟合的操作是origin软件中的常规操作,熟悉origin软件的人均可进行拟合的操作。r、β值的调整方式是依据余弦函数的周期性进行调整的,运用的也是基础的三角函数知识。(3)确定a、r、β后,即可获得确定的角度-残余应力值余弦函数关系,将不同的测量角度带入该余弦函数表达式中,得到不同角度下残余应力结果的拟合值。(4)将不同角度的测量值与拟合值进行比较,可分析每个角度上检测结果的精确程度,每个值的偏差可计算测量值与拟合值差值的绝对值,然后求得其与拟合值绝对值的百分比表示。(5)将拟合获得参数a、r、β与拟合过程中给出的对应的误差水平进行比较,分析测量结果的整体精确程度,a、r值偏差可用误差水平与拟合值的百分比表示,β值本身与测量时0°角度的选取有关,其误差水平与拟合值的比值意义不大。(6)计算最大及最小主应力,计算公式为σmax,min=a±r,最大主应力方向为0°方向顺时针转过β角度。(7)不同角度下切向残余应力分布公式为切应力方向以对应角度顺时针选择90°方向为正。对于上述步骤(2)中,获得a、r、β的最佳拟合值的方法如下:在origin软件fittingfunctionorganizer功能中构建自定义拟合函数,输入的函数形式为y=a+r*cos((x+c)*pi/90),其中x为自变量对应测量角度θ,y为因变量对应残余应力测量值σ,a、r、c为拟合参数,分别对应a、r、β值。将不同测量角度及对应的残余应力测量值输入到origin中,并作出角度(θ)-应力(σ)散点图,使用nonlinearcurvefit功能调用上述构建的函数对数据点进拟合。拟合时对话框切换至parameter列表并对a、r、c赋值(value列)如1、1、1,逐步进行迭代拟合(1iteration图标选项),拟合过程运用余弦函数周期性实时调整r、c数值,调整方法为:若r值为正,则r值保持不变,c值加减180的整数倍使c值保持在0~180之间;若r值为负调整为其相反数,c值加减90的奇数倍使c值保持在0~180度间。如实施例1在迭代过程中,r为-16.1946,c值为1764.83286,将r值取相反数修正为16.1946,c值调整为1764.83286-90*19=54.83286。经多次迭代拟合后获得a、r、c(即a、r、β)的最佳拟合值,同时输出误差水平。本发明的实施例如下:按照上述实施步骤在不同的xrd设备上进行不同试样的多角度残余应力测量、数据拟合及误差分析,构成实施例1~3。实施例1以轧制方向为0°方向,角度计量以逆时针为正,按照实施步骤1~5对热轧带钢试样进行45°、90°、135°、180°(0°)共4个方向进行测量、数据拟合及误差分析,如表1、表4和附图1所示。实施例2以轧制方向为0°方向,角度计量以逆时针为正,按照实施步骤1~5对热轧带钢试样进行30°、60°、90°、120°、150°、180°(0°)共6个方向进行测量、数据拟合及误差分析,如表2、表4和附图2所示。实施例3以轧制方向为以轧制方向为0°方向,角度计量以逆时针为正,按照实施步骤1~5对热轧带钢试样进行22.5°、45°。67.5°、90°、112.5°、135°、157.5°、180°(0°)共8个方向进行测量、数据拟合及误差分析,如表3、表4和附图3所示。表1实施例1不同角度下残余应力结果测量值、拟合值及偏差分析角度/°4590135180(0)测量值/mpa-401.9-386.0-371.4-395.7拟合值/mpa-404.3-383.6-373.8-394.5偏差值/mpa2.42.42.41.2偏差百分比/%0.590.630.640.30表2实施例2不同角度下残余应力结果测量值、拟合值及偏差分析角度306090120150180测量值/mpa-98.4-63.9-136.0-130.8-111.6-101.2拟合值/mpa-83.2-91.5-115.7-131.5-123.2-99.0偏差值/mpa15.227.620.30.711.62.2误差百分比/%18.3730.1617.550.539.422.22表3实施例3不同角度下残余应力结果测量值、拟合值及偏差分析角度22.54567.590112.5135157.5180测量值/mpa-447.4-479.4-445.8-426.1-383.5-340.9-372.8-404.8拟合值/mpa-448.9-471.3-459.1-419.7-376.0-353.6-365.7-405.2偏差值/mpa1.58.113.36.47.512.77.10.4误差百分比/%0.331.722.901.521.993.591.940.10比较不同角度测量值与拟合值的偏差,实施例1和实施例3最大偏差百分比分别为0.64%和3.59%,整体控制在5%以下,结果可信度高。实施例1中所有4个角度和实施例3中22.5°、180°两个角度的偏差均控制在0.5%,检测结果准确可信度高。实施例2最大偏差为30.16%,30°、60°、90°偏差均超过10%,测量值可信度差。对3个实施例的拟合值误差进行了分析,如表4所示。表4残余应力拟合参数偏差分析结合本次测量试样的特征,其残余应力数值不同角度下波动范围大大小于其均值的大小,因此呈现出a值大,r值小的特征,相应的a值的误差百分比较小,r值误差百分比较大。比较拟合参数的偏差发现,以实施例1、3拟合较为精确,实施例2拟合误差较大。对实施例2使用的xrd设备进行检查,发现该设备测试点中心、x射线光斑中心、测角仪回转中心三者的对正不良,造成检测结果偏差精度较差。对拟合效果较好、测量精度较高的实施例1和实施例3进一步按照步骤6、7计算其对应的最大最小主应力和不同角度切应力分布。实施例1根据其拟合参数a=-389.1,r=16.2,β=54.8,经计算得最大主应力σmax=-405.3mpa,最小主应力σmin=-372.9mpa,最大主应力方向为测量过程规定0°方向顺时针旋转54.8°。该试样不同角度θ下切向残余应力分布公式为如附图图4所示。实施例3根据其拟合参数a=-412.4,r=59.3,β=41.5经计算得最大主应力σmax=-471.7mpa,最小主应力σmin=-353.1mpa,最大主应力方向为测量过程规定0°方向顺时针旋转41.5°。该试样不同角度θ下切向残余应力分布公式为如附图图5所示。当前第1页12