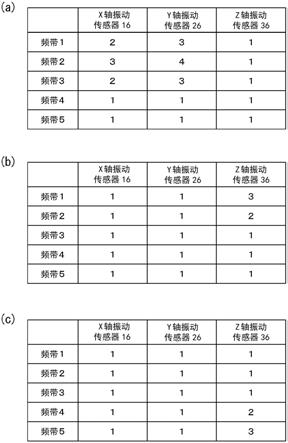
1.本发明涉及进行具有多个控制轴的设备的异常诊断的系统以及其异常诊断方法。
背景技术:2.在机器人、工作机械、半导体/液晶制造装置等各种装置类中使用用于引导可动部的前进路线的部件。例如,在可动部进行直线前进的部位使用直线导轨。在这样的部件的选定时,通常选定具有相对于乘以安全系数的载荷有余量的额定载荷的部件,但近年,例如也进行如下尝试:在部件安装应变计,算出施加于部件的实际载荷来对部件更合格地进行管理(例如,参照专利文献1)。
3.此外,在专利文献2中,公开了对直线导轨的产品寿命高精度地进行诊断的技术。因此,基于移动构件相对于直线导轨的轨道构件所形成的轨道的位移量,按沿着轨道的方向对移动构件的滚动面进行划分而得的假想的每个区间,算出移动构件进行移动时在各区间产生的应力即移动时应力,并且基于位移量按每个区间算出伴随移动构件沿着轨道移动时的摇摆而重复产生的移动时应力的产生次数。然后,基于所算出的移动时应力的大小和移动时应力的产生次数来进行直线导轨的寿命诊断。
4.在先技术文献
5.专利文献
6.专利文献1:jp特开2007
‑
263286号公报
7.专利文献2:jp特开2018
‑
109538号公报
技术实现要素:8.发明想要解决的课题
9.机器人、工作机械等设备由各种部件构成。一般,为了使该设备执行期望的动作而搭载多个电动机,且与该期望动作相匹配地驱动各电动机。为了使设备合适地运转,需要迅速检测所发生的不良情况,并适时地实施设备的维护。由于一般的设备存在很多驱动部位,因此作为设备整体,可出现异常状态的部位很多,为了检测异常状态,也需要大量传感器等检测装置。因此,在搭载多个电动机的设备中,检测异常状态并不容易,提高其检测精度很困难。
10.关于设备的维护,有如下情况:从设备实际发生故障后进行与该故障对应的事后维修;基于与该设备相关的到此为止的运行经验、运行历史记录等,在故障未发生的时间点进行维修应对。但是,在这样的维修应对中,使设备在比较长的期间停止,或作为设备尽管仍可以进行稳定的运行但也无益地使设备停止,很难说能够进行高效的设备运转。另一方面,为了进行高效的设备运转,优选在导致故障前迅速检测作为其预兆的异常状态并牵涉到维护的实施。
11.本发明鉴于上述的问题而完成,其目的在于,提供能够兼顾设备的适当维护和其高效的运转的技术。
12.用于解决课题的手段
13.在本发明中,为了解决上述课题,本发明的异常诊断系统采用如下构成:通过在设备所包含的多个控制轴的每一个设置振动传感器这样的简便的结构,来基于与多个控制轴对应的振动等级的分布状态进行各控制轴的异常诊断。
14.详细来说,本发明是一种异常诊断系统,在如下设备中进行与各控制轴相关联的异常诊断,该设备装入多个具有电动机以及由该电动机驱动的输出部的控制轴,该多个控制轴的至少一轴构成为在与其他控制轴的至少一轴对应的该电动机进行驱动时被传递该驱动导致的振动,该异常诊断系统具备:设置在所述多个控制轴的每一个且检测与各控制轴所对应的所述电动机的驱动相关联地产生的振动的多个振动传感器;基于由所述多个振动传感器分别检测到的振动信息来按所述多个控制轴的每一个算出多个给定的频率范围中的振动等级的算出部;以及基于由所述算出部算出的所述多个控制轴中的所述多个给定的频率范围中的所述振动等级的分布状态来执行与各控制轴相关联的异常诊断的诊断部。
15.发明效果
16.能够谋求兼顾设备的适当维护和其高效的运转。
附图说明
17.图1是表示实施方式所涉及的设备即立式加工中心的概略结构的图。
18.图2是表示实施方式所涉及的异常诊断系统的功能性的结构的图。
19.图3是由异常诊断系统执行的异常诊断控制的流程图。
20.图4是表示图3所示的异常诊断控制中利用的振动等级的分布状态的第1图。
21.图5是表示图3所示的异常诊断控制中利用的振动等级的分布状态的第2图。
具体实施方式
22.本实施方式的异常诊断系统在如下设备中进行各控制轴的异常诊断,该设备装入多个控制轴,多个控制轴的至少一轴构成为在其他控制轴当中的至少一轴中其该电动机进行驱动时被传递所产生的振动。这里所说的控制轴间的振动的传递,意思是将该设备构成为使振动在控制轴间相互作用。此外,各控制轴具有对应的电动机和输出部。在一个控制轴中可以包含多个电动机、多个输出部。控制轴的输出部并不一定与设备中的输出部一致,也可以将多个控制轴的输出部组合而形成为设备中的输出部。
23.在这样构成的设备中,若驱动与多个控制轴当中的某控制轴对应的电动机,则因该驱动而产生的振动就会作用到其他控制轴。因此,通过设置于各控制轴的振动传感器来检测此时的振动。换言之,设置于多个控制轴的多个振动传感器能够检测在设置于各控制轴的对应的电动机进行驱动时传递到设备整体的振动。此外,由设备中设置于各控制轴的振动传感器检测的振动等级(振动的大小)并不全都相同,而是反映了设备的机械结构。
24.在此,在设备中其机械结构处于正常状态的情况下和该机械结构处于异常状态的情况下,从振动传递的观点来看,在机械的条件中产生差异。另外,所谓本实施方式中的“异常状态”,从设备的维护的观点来看,是需要进行用于使该设备继续运转的维护的与设备的运转状况相关的状态,与该设备完全不能运转这样的所谓的故障状态不同。换言之,所谓设备中的异常状态是虽然是设备仍能运转的状态但需要进行任意部件更换等维护的状态,是
指与正常状态相区别的状态。并且,与设备中的异常状态的程度(以下设为包含有无异常状态)相应地,在各控制轴中检测的振动等级与设备处于正常状态的情况相比有变化。此外,由于根据设备中可产生的异常状态的种类的不同,与该设备中的振动传递相关的机械条件也会按每个该种类而不同,因此能够将按控制轴整体观察时的振动等级的分布状态与异常状态的每个种类建立关联。
25.因此,在本实施方式的异常诊断系统中,为了能够合适地辨别出设备中会产生的异常状态的种类,在算出部基于由振动传感器检测的振动信息按多个给定的频率范围的每一个频率范围算出振动等级的基础上,诊断部基于遍及多个控制轴得到的控制轴整体中的振动等级的分布状态,来执行与设备中的各控制轴相关联的异常诊断。上述多个给定的频率范围能够考虑设备的机械结构、用于容易地检测在那里设想的异常状态的振动特性(振动的谐振频率等)来适当地进行设定。多个频率范围各自并不一定需要是连续的频率范围,此外,各频率范围的广度并不一定需要相同。
26.这样,在上述异常诊断系统中,通过在各控制轴设置振动传感器这样的比较简便的构成,能够考虑振动在控制轴间相互作用这一情况来合适地执行设备中的异常诊断。特别地,由于供异常诊断用的信息是实际设备运转而得到的信息,因此准确地反映了此时的设备的异常状态的程度,并且能够在合适地维持设备的运转的同时合适地实现该异常诊断。其结果,也能够适当地设定实施设备的部件更换等维护的定时。
27.以下,基于附图说明本发明的具体的实施方式。本实施方式记载的构成部件的尺寸、材质、形状、其相对配置等只要没有特别记载,主旨就不是将发明的技术范围仅限定于这些。
28.<实施方式>
29.图1表示应用本实施方式的异常诊断系统的设备1的一例即立式加工中心的概略结构。特别地,图1的上段(a)表示设备1的加工区域的外观,下段(b)表示构成设备1的3个控制轴的概略结构。设备1是具有x轴、y轴以及z轴这3个控制轴的立式加工中心,将x轴以及y轴配置在水平面上,将z轴配置于铅垂方向。如图1的上段(a)所示,在设备1的加工区域中,配置有放置工件的载台2。载台2按照x轴以及y轴被控制。在x轴配置盖11,在y轴配置盖21。此外,配置主轴31,且主轴31按照z轴来控制其位置,以便能够对设置于载台2的工件进行切削加工。另外,主轴31的电动机主体配置于盖32内。
30.在此,基于图1的下段(b)来说明各控制轴的详细情况。在x轴上,配置x轴的致动器即电动机13,电动机13的输出轴与滚珠丝杠14连结,与滚珠丝杠14对应的螺母15相当于x轴的输出部。此外,x轴是对载台2直接进行驱动的控制轴,其沿着x轴的移动通过轨12a和在其上滑动的同时支承载台2的移动构件12b来实现。相同地,在y轴中,也配置y轴的致动器即电动机23,电动机23的输出轴与滚珠丝杠24连结,与滚珠丝杠24对应的螺母25相当于y轴的输出部。另外,y轴是驱动载台2和上述的x轴的结构的控制轴,其沿着y轴的移动通过轨22a和在其上滑动的同时支承载台2以及x轴结构的移动构件22b实现。此外,在z轴中,配置z轴的致动器即电动机33,电动机33的输出轴与滚珠丝杠34连结,与滚珠丝杠34对应的螺母35相当于z轴的输出部。此外,z轴是在铅垂方向上驱动主轴31的控制轴,其沿着z轴的移动通过轨32a和在其上滑动的同时支承主轴31的移动构件32b来实现。
31.在这样构成的设备1中,x轴和y轴是一起实现水平面上的载台2的移动的控制轴,
将与x轴相关联的机械结构配置在y轴上。由此,x轴以及y轴能够理解为是由各自的电动机13、23的驱动产生的振动可相互传递的结构。此外,z轴虽然与x轴以及y轴不同是使主轴31在铅垂方向上移动的控制轴,但能够理解为是经由加工中心即设备1的壳体在z轴与x轴以及y轴之间也可传递振动的结构。另外,在x~z轴上,并不是所有的振动都相互传递,根据振动的特性(振幅、频率等),也可存在实质在控制轴间不传递的振动。
32.进一步地,在x轴~z轴的各控制轴,为了检测各自的振动而配置有振动传感器16、26、36。另外,由x轴的振动传感器16检测的振动方向是x轴方向,由y轴的振动传感器26检测的振动方向是y轴方向,由z轴的振动传感器36检测的振动方向是z轴方向。各振动传感器16、26、36为了不成为各控制轴中的输出部的移动的妨碍,而配置在各控制轴所包含的轨12a、22a、32a的端部。另外,作为振动传感器16、26、36,能够利用公知的振动传感器或者加速度传感器,其详细情况的说明省略。
33.在此,基于图2来说明本实施方式的异常诊断系统的结构。另外,该异常诊断系统由处理装置5和与其电连接的x轴~z轴的振动传感器16、26、36构成。处理装置5实质上是具有运算处理装置以及存储器的计算机,因此通过执行给定的控制程序,而形成图2所示的功能部。另外,由振动传感器16、26、36的各自检测到的振动信息被交给处理装置5。
34.处理装置5具有算出部51、诊断部52以及存放部53。算出部51从振动传感器16、26、36的每一个接受各控制轴中的振动信息,并且基于该振动信息,按每个控制轴算出多个给定的频率范围中的振动等级。设备1中设想会发生的多个异常状态能够与各控制轴中发生的各种振动建立关联。例如有如下情况:在第1异常状态下,与其他控制轴相比,容易在x轴产生振动,在第2异常状态下,与其他控制轴相比,容易在z轴产生振动。此外有如下情况:在第3异常状态和第4异常状态下,虽然有与其他控制轴相比更在y轴产生振动的倾向,但在y轴产生的振动的频率特性(例如,振动的谐振频率)会不同。在这样将设备1中发生的各种异常状态和与各控制轴中的振动相关的特征建立关联时,通过利用与该振动相关的特征,能够诊断设备1中的异常状态。考虑这一点,设定多个给定的频率范围。即,能够基于用于容易地检测设备1中设想会发生的异常状态的振动特性,来适当设定各个给定的频率范围。
35.例如,在后述的图4中,作为给定的频率范围,设定5个范围(频带1~频带5)。在各频率范围间没有频率重复,关于属于各范围的频率的相关性,为频带1<频带2<频带3<频带4<频带5的关系。各频率范围各自并不一定需要是连续的频率范围,此外,各频率范围的广度(各频带的宽度)并不一定需要相同。另外,所设定的多个给定的频率范围对各控制轴共通使用。
36.算出部51对从振动传感器16、26、36分别接受到的振动信息实施高速傅里叶变换(fft)处理,基于预先设定的频率范围中的中的与频率相关的给定的特征量,来算出该频率范围中的振动等级。作为该给定的特征量,例如,可以采用该频率范围中的fft处理值的峰值、平均值等。算出部51在相同的定时下算出各控制轴中的与多个给定的频率范围的每一个频率范围对应的振动等级。在本实施方式中,振动等级是以设备1中未发生异常状态的正常状态下的各控制轴的上述给定的特征量为基准如例如下述的式子那样相对地算出的指数。
37.振动等级=(实际的给定的特征量)/(正常状态下的给定的特征量)
38.因此,例如,在图4所示的示例中,在实际的给定的特征量与正常状态下的给定的
特征量为相同值的情况下,将振动等级设为“1”,通过将设备1中的异常状态的程度反映到实际的给定的特征量,从而振动等级的数值发生变动。即,意思是,随着振动等级的数值超过1而变大,设备1中的异常状态的程度变大。
39.接着,诊断部52基于由算出部51算出的多个给定的频率范围的每一个频率范围中的控制轴整体中的振动等级的分布状态,来执行与各控制轴关联的异常诊断。由于根据设备1中的异常状态的种类的不同,易于受到影响的控制轴、易于表现其影响的频率范围会发生变动,因此该分布状态能够称为是反映设备1中的异常状态的种类的信息。因此,如上述那样,诊断部52能够基于振动等级的分布状态来执行异常诊断。并且,为了进行该异常诊断,将与该分布状态进行比较的振动分布信息存放于存放部53。该振动分布信息是与设备1中设想会发生的异常状态建立关联的信息,且是该异常状态假设在设备1中发生时基于在各控制轴中检测的振动信息形成的振动等级的分布信息。换言之,振动分布信息是对设备1中发生的一个异常状态以能够与其他异常状态相区别的方式进行表示的与振动分布相关的信息。因此,诊断部52能够在振动等级的分布状态与某振动分布信息一致时,或者与该振动分布信息近似时,诊断为在设备1中发生了该振动分布信息所表示的异常状态。
40.在此,基于图3所示的流程图来说明处理装置5的与异常诊断控制相关的处理的一例。该异常诊断控制能够在设备1中开始工件加工前、结束工件加工后等给定的定时下执行。首先,在s101中,开始为了检测设备1中的异常状态而预先设定的诊断用的各控制轴的电动机13、23、33、主轴31的驱动。例如,可以驱动3个控制轴的电动机当中的1个电动机、主轴31,也可以同时驱动多个控制轴的电动机、主轴31。通过这样驱动为了进行异常诊断而预先设定的电动机等,能够将与该电动机等的驱动相关联的异常状态某种程度缩小范围,能够提高异常状态的检测精度。若s101的处理结束,就前进到s102。
41.在s102中,在s101中开始驱动的电动机等的驱动中,通过设置于各控制轴的振动传感器16、26、36来检测各控制轴中的振动,由算出部51取得与该振动相关的振动信息。若s102的处理结束,就前进到s103。并且,在s103中,判定s101中开始驱动的电动机等的该驱动是否完成。若s103中进行了肯定判定,则处理就前进到s104,若进行了否定判定,则继续进行s102的处理。
42.并且,在s104中,算出部51基于s102中取得的各控制轴的振动信息,按每个控制轴算出多个给定的频率范围中的振动等级。接着,在s105中,诊断部52生成振动等级的分布状态,进而在s106中,基于该生成的分布状态来诊断设备1中异常状态的程度。
43.在此,基于图4来说明诊断部52的与异常状态的程度相关的诊断。图4将设备1中发生例示的3个异常状态时的s105中生成的振动等级的分布状态以(a)~(c)进行表示。更具体来说,图4的上段(a)表示在y轴的盖21发生异常状态的情况下的振动等级的分布状态。该分布状态通过驱动y轴的电动机23来检测并生成。在该异常状态下,受到盖21的影响,基于y轴的振动传感器26的振动信息的振动等级在频带1~频带3的频率范围中相对变高。进一步地,如上述那样,由于在设备1中x轴与y轴重叠配置,因此因盖21的异常状态引起的振动易于传递到x轴。另一方面,若是盖21的异常状态,则该振动一般不会传递到z轴。其结果,x轴的振动等级与y轴相同地在频带1~频带3的频率范围下相对变高,但相比y轴是更低的等级。进一步地,z轴的振动等级不会受到x轴以及y轴的影响。这样,图4的上段(a)所示的振动等级的分布状态可以说与y轴的盖21的异常状态建立有关联。
44.此外,图4的中段(b)表示在z轴的主轴31发生异常状态的情况下的振动等级的分布状态。该分布状态通过驱动主轴31来检测并生成。在该异常状态下,设为在主轴31中产生周期性的机械振动。此时,基于z轴的振动传感器36的振动信息的振动等级在频带1~频带2的频率范围中相对变高,另一方面,该振动一般不会传递到x轴以及y轴。这样,图4的中段(b)所示的振动等级的分布状态可以说与主轴31的某异常状态(即,产生上述周期性的机械振动的异常状态)建立有关联。此外,4的下段(c)也表示在z轴的主轴31发生异常状态的情况下的振动等级的分布状态,但在该异常状态下,设为在主轴31中发生金属彼此的摩擦。另外,该分布状态也通过驱动主轴31来检测并生成。此时,基于z轴的振动传感器36的振动信息的振动等级在比较高的频率范围即频带4~频带5的频率范围下相对变高,另一方面,该振动一般不会传递到x轴以及y轴。这样,图4的下段(c)所示的振动等级的分布状态可以说与主轴31的某异常状态(即,发生金属彼此的摩擦的异常状态)建立有关联。
45.这样,如图4所示,将设备1中会发生的异常状态与振动等级的分布状态建立关联。因此,诊断部52通过对这样的分布状态和存放部53中存放的振动分布信息进行比较,能够基于该比较结果在与所存放的振动分布信息的任一者一致的情况下,诊断为在设备1中发生了该振动分布信息所表示的异常状态。另外,即使是所生成的分布状态和所存放的振动分布信息有差异的情况,在该差异量收于给定的范围的情况下(例如,在与振动分布信息有差异的频率范围的数量为给定数量以下等条件成立的情况下),视作与该振动分布信息近似,该分布状态也能够诊断为在设备1中发生了该振动分布信息所表示的异常状态。
46.这样,根据本异常诊断控制,能够通过用在各控制轴设置振动传感器16、26、36这样的比较简便的结构来考虑在控制轴间振动发生相互作用这一情况,来合适地执行设备1中的异常诊断。特别是,由于供异常诊断用的信息是实际设备1运转而得到的信息,因此准确地反映了此时的设备1的异常状态的程度,而且能够在合适地维持设备1的运转的同时实现该异常诊断。其结果,也能够适当地设定实施设备1的部件更换等维护的定时。
47.另外,在上述的异常诊断控制中,在s101中进行异常诊断用的电动机等的驱动,但该驱动并不一定是必须的处理。即,可以在为了设备1中进行工件的加工等而进行电动机等的驱动时,进行s102的振动信息的取得。
48.此外,在图4中,用数值的分布来表示振动等级的分布状态,但也可以取代该方式,而如图5所示那样,将各振动等级用对应的图像(image)信息来表示。在图5中,将振动等级与图像建立对应,使得随着振动等级变高,图像的着色逐渐变浓。并且,图5所示的上段(a)与图4的上段(a)对应,图5所示的中段(b)与图4的中段(b)对应,图5所示的下段(c)与图4的下段(c)对应。通过这样将振动等级图像化,就易于利用伴有图像处理的公知的深度学习技术。其结果,易于对振动等级的分布状态和存放部53中存放的振动分布信息进行比较来判断其一致、近似程度,而且,能够合适地诊断设备1中的异常状态的程度。
49.<变形例>
50.在到上述为止的实施方式中,对振动等级的分布状态和振动分布信息进行比较,诊断设备1中的异常状态的程度。在此,关于设备1中会发生的异常状态,有时该异常状态会突然发生,也有时该异常状态会需要某程度的时间而逐渐发生。在后者的情况下,认为是与设备1中的异常状态的推移相应地,振动等级的分布状态也逐渐推移,最终成为与振动分布状态一致或者近似的状态,从而成为发生了给定的异常状态的状态。
51.因此,诊断部52能够通过利用这样的振动等级的分布状态的推移,来预测异常状态什么时候会发生。具体来说,能够基于设备1中的各控制轴中的电动机13、23、33、主轴31的驱动历史记录和振动等级的分布状态的推移,来进行异常状态的预测。例如,当前时间点的振动等级的分布状态下的与x轴以及y轴相关的频带1~频带3的数值是图4的上段(a)所示的数值的一半,若将到此为止的y轴的电动机23的驱动历史记录设为1000小时,则能够预测为在进一步将电动机23驱动1000小时时,会发生图4的上段(a)所示的异常状态,即,y轴的盖21的异常状态。
52.若这样由诊断部52来预测异常状态,则从处理装置5对用户通知其预测结果,能够促进用户的维护作业的准备。此外,在进行了该异常状态的预测的情况下,也能够通过执行图3所示的异常诊断控制,来在实际发生该异常状态时,迅速检测其发生。
53.附图标记说明
[0054]1···
设备,5
···
处理装置,13,23,33
···
电动机,16,26,36
···
振动传感器,31
···
主轴