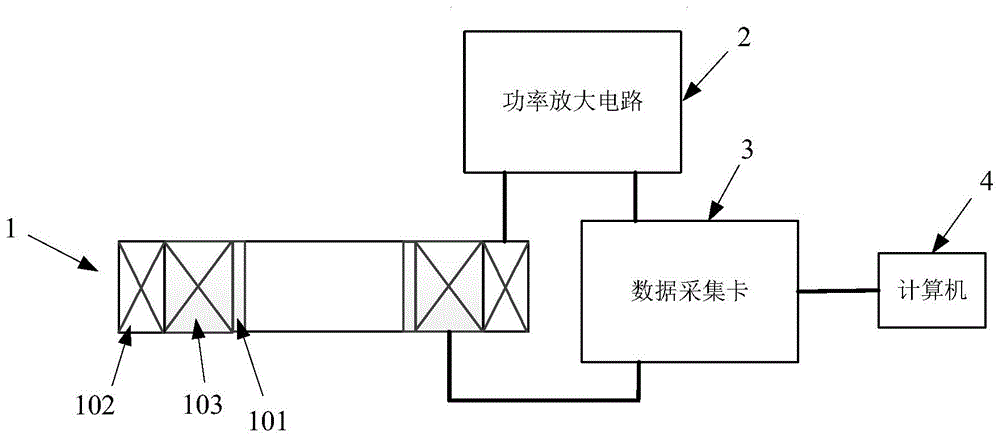
本发明涉及电磁无损检测
技术领域:
,具体是一种检测金属套管间距的脉冲涡流检测方法及装置。
背景技术:
:在核电、石油、石化等工业领域,有大量金属套管的应用,套管由内管和外管相套组成,内、外管之间还保留一定的间隙。在套管工作过程中,由于压力、介质温度等因素会导致内管的径向移动,使得内、外管之间一侧的间距减小,这很有可能会引起内、外管的接触而造成内管局部温度变化、加速腐蚀等后果。因此需要一种检测技术定期检测内、外管之间的间距,监测套管最小间距是否超过设计下限值。对于不锈钢等非铁磁材质的金属套管,已采用多频正弦涡流法来检测套管间距,往激励线圈中通入正弦变化的电流,通过检测线圈两端感应电压的幅值,来反映间距变化。多频涡流法检测施加的是正弦激励电流,由于线圈发热限制,一般所加激励电流幅值较小,探头的穿透能力有限,很难用于含铁磁材料的金属套管的检测。脉冲涡流法是一种非接触的电磁无损检测方法。激励线圈通入脉冲激励电流,产生脉冲强磁场,变化的磁场在导体内感应出漩涡状分布的涡流,此涡流场又在检测线圈两端感应出感应电压信号。通过测量时域信号的衰减过程检测导体的几何尺寸和电磁参数。脉冲涡流法的优势在于穿透能力强,对壁厚、间距等几何参数,以及电导率、磁导率等电磁参数的变化更灵敏。目前主要用于带包覆层铁磁管道壁厚腐蚀的在役检测,电磁材料电磁参数检测。技术实现要素:针对上述问题,本发明提出一种金属套管间距脉冲涡流检测方法及装置,本发明金属套管间距脉冲涡流检测方法,具体如下:首先,设计标定套管,测量标定套管感应电压时域信号;保持探头位置不变,将内外管道间距减小距离k,测量此时标定套管感应电压时域信号;通过前后两个感应电压时域信号,绘制感应电压的差值曲线,确定差值曲线的峰值时刻t0。随后保持探头位置不变,以距离k为步长渐减少标定套管间距,采集不同套管间距对应的感应电压信号,并提取t0时刻的信号幅值为特征量。最后采用曲线拟合的方法找到v和套管间距d之间的函数关系为信号特征量与套管间距之间的函数关系v=ad+b(1)其中a,b均为常数。最终,在进行被检套管间距测量时,在检测点设置探头,获得检测点处的感应电压时域信号,并提取感应电压时域信号在t0时刻的信号幅值代入函数关系式(1)中,求解得到检测点处被检套管间距。针对上述方法本发明还提出一种金属套管间距脉冲涡流检测装置,包括线圈探头、功率放大电路、数据采集卡与计算机。所述线圈探头由线圈骨架、激励线圈和检测线圈组成。其中,线圈骨架、检测线圈与激励线圈三者间由内至外同轴套接;或者线圈骨架、激励线圈、检测线圈三者间由内至外同轴套接。激励线圈两端接功率放大电路的输出端;检测线圈的两端接数据采集卡;数据采集卡连接计算机。所述计算机用于实现信号采集、处理、结果显示、数据存储等功能,对接收的离散信号数据进行处理,获得被检测套管的套管间距信息。本发明的优点在于:1、脉冲涡流法信号信噪比更高。正弦涡流法由于激励线圈的发热问题,施加的正弦激励电流幅值一般不能太大,一般在几十到几百毫安,所激发的激励磁场比较弱,探头穿透能力弱,检测的套管间距范围小。与正弦涡流法相比,脉冲电流的持续时间短,发热问题减弱,激励电流的峰值可达十几安培,从而产生瞬态强磁场,在导体内激发出更强的涡流场,最终大幅提升检测信号的强度,提高了信噪比,避免微弱信号采集引入的检测误差。2、脉冲涡流法的信号包含更多信息量。多频涡流法采用离散的几个频率点来检测套管间距,提供的信息量有限,因此检测结果容易受到内、外壁厚度,材料电导率等其它参数变化的影响。而脉冲涡流法采集的时域感应电压响应信号,其频谱是连续的,比多频涡流法包含了更多的频率成分,能反映更多关于被检对象的信息。3、脉冲涡流法对套管间距的检测灵敏度更高。正弦涡流场中激励电流的入射磁场会在检测线圈中感应出一个非常强的入射场电压信号,从而淹没反映套管间距的涡流场电压信号,大大降低了对套管间距等参数的检测灵敏度。在脉冲涡流法中,随着脉冲激励电流的快速关断,入射场快速衰减到零,检测信号中仅含有可反映被检套管参数差异的涡流散射场电压信号,从而可明显提高检测信号对套管间距、壁厚、电导率等参数的检测灵敏度。附图说明图1为本发明金属套管间距脉冲涡流检测装置结构示意图。图2为本发明金属套管间距脉冲涡流检测装置信号采集方法框图。图3为探头放置于套管内的俯视图。图4为探头放置于套管外的俯视图。图5为标称间距感应电压时域信号曲线图。图6为感应电压的差值曲线图。图7为不同套管间距下脉冲涡流检测信号曲线图。图中:1-线圈探头2-功率放大电路3-数据采集卡4-计算机5-被检套管101-线圈骨架102-激励线圈103-检测线圈具体实施方式下面将结合附图和实施例对本发明做进一步的详细说明。本发明采用由设计的脉冲涡流检测装置,实现对被检套管(材质可以是导电、导磁的铁磁性金属材料,也可以是导电、不导磁的非铁磁性金属材质)的感应电压时域信号的采集,并结合提出的金属套管间距脉冲涡流检测方法,实现金属套管间距测量。如图1所示,所述脉冲涡流检测装置包括空心圆柱线圈探头1、功率放大电路2、数据采集卡3与计算机4。其中,空心圆柱线圈探头1由线圈骨架101、激励线圈102和检测线圈103组成。其中,线圈骨架101、检测线圈103与激励线圈102三者间由内至外同轴套接;或者线圈骨架101、激励线圈102、检测线圈103三者间由内至外同轴套接。空心圆柱线圈探头1中,激励线圈102两端接功率放大电路2的输出端;检测线圈103的两端接数据采集卡3;数据采集卡3连接计算机4。计算机4能够实现信号采集、处理、结果显示、数据存储等功能,对接收的离散信号数据进行处理,获得被检测套管的套管间距信息。采用前述检测装置利用脉冲涡流检测系统对被检套管5的感应电压时域信号的采集,称为信号采集过程,signalacquisitionprocedure,sap;如图2所示,具体采集方法如下:步骤sap-1:将空心圆柱线圈探头1沿管道径向放置于被检套管5内,如图3所示;或者放置于被检套管5外,如图4所示。保持探头下边缘与被检套管5表面之间的距离(探头提离距离)l0保持不变,l0的取值范围为0~5mm。步骤sap-2:通过计算机4输出脉宽为10~100ms,幅值为0.1~1v的激励数字信号;激励数字信号经数据采集卡3中的da数模转换器5后,变成持续脉宽为10~100ms,幅值为0.1~1v的激励模拟信号,输出给功率放大电路2;经功率放大电路2放大功率后,输出持续脉宽为10~100ms,幅值为0.1~5a的脉冲激励电流至激励线圈;步骤sap-3:通过数据采集卡3采集检测线圈103两端的u(t)(单位v),并将采集得到的感应电压时域信号u(t)经数据采集卡3中的ad数模转换器转换成离散信号存储到计算机4内。结合上述检测装置本发明金属套管间距脉冲涡流检测方法具体步骤如下:步骤一:获得套管间距与信号特征量之间的标定函数为了获得脉冲涡流检测信号与套管间距之间的变化规律,须在实际检测前,提取信号特征量并找到特征量与套管间距之间的对应关系。固定探头位置不变,改变内、外管道之间的间距,采集不同套管间距对应的感应电压信号。找到对套管间距最灵敏的时刻,提取该时刻的信号幅值为特征量。最后采用曲线拟合的方法找到信号特征量与套管间距之间的函数关系。本发明中,利用实验套管采集不同套管间距下脉冲涡流检测信号,并标定信号特征量与套管间距之间函数关系的步骤,称为信号特征量标定步骤,featurecalibrationprocedure,fcp。具体操作步骤如下:步骤fcp-1:为了减少内、外管壁厚、材质等因素变化的影响,利用与实际待检套管材质、管径、壁厚相同的金属管道组成标定套管,标定套管轴向长度取300mm左右,内、外管之间间距取为实际标称间距;步骤fcp-2:将空心圆柱线圈探头1置于标定套管轴线方向的中间位置,用卡尺测量标定套管间距为d0;随后实施前述sap步骤,得到感应电压时域信号为uref(t),存储到计算机4内;步骤fcp-3:保持探头位置不变,将套管间距减小1mm左右,用卡尺测量套管间距为d1,重新实施sap步骤,获得感应电压时域信号u1(t),存储到主机内;步骤fcp-4:绘制感应电压的差值曲线u1(t)-uref(t),找到差值曲线的峰值时刻t0,分别从uref(t)和u1(t)中提取t0时刻的信号幅值v0和v1,作为套管间距为d0和d1对应的信号特征量;步骤fcp-5:以1mm为步长逐渐减少标定套管间距至1mm,标定套管间距依次记为di,在每一个套管间距下实施sap步骤,采集得到感应电压时域信号,并提取感应电压信号在t0时刻对应的幅值为信号特征量vi,存储到主机内;步骤fcp-6:提取基于以上步骤得到的所有在t0时刻的感应电压幅值vi作为函数值,对应的标定套管间距di为自变量,通过直线拟合,得到信号特征量v和套管间距d之间的函数关系为:v=ad+b(1)其中a,b均为常数。步骤二:利用信号特征量检测套管间距本发明中,利用采集到的脉冲涡流检测信号,通过标定的信号特征量与套管间距之间的函数关系,获得探头所在位置处套管间距大小的步骤称为套管间距检测步骤,testingforcasingspacing(tcs)。步骤tcs-1:将线圈探头1沿管道径向放置于被检套管5内或者被检套管5外要求的检测点位置,实施sap步骤,获得该处的感应电压时域信号um(t);步骤tcs-2,提取感应电压信号um(t)在t0时刻的信号幅值vm,将vm代入函数关系式(1)中,求解得到该点被检套管5间距为步骤tcs-3,移动线圈探头1位置至下一个检测点,重复步骤tcs-1和步骤tcs-2,获得该点的信号特征量和套管间距为vm+1和dm+1。实施例下面给出采用本发明方法对套管间距实施脉冲涡流检测的实例。检测对象是两根相套的金属管道,内、外管的材质均为304不锈钢。内管壁厚为4.5mm,内直径为100mm,外管壁厚5.0mm,内直径为128mm,两管长度均为600mm。内、外管同心时,套管间距约10mm。套管标称间距设为d0=10.33mm,实施sap步骤,获得感应电压时域信号为uref(t),如图5所示。实施步骤fcp-3和fcp-4,绘制感应电压的差值曲线u1(t)-uref(t)如图6所示,找到差值曲线的峰值时刻t0=0.75ms。实施fcp过程,得到不同套管间距下脉冲涡流检测信号,如图7所示提取t0时刻信号幅值为信号特征量,得到信号特征量v与套管间距d之间的拟合函数关系为:v=-0.0084d+0.385由此解得将此式存于检测程序中,后续采集得到信号幅值后,即可反算出套管间距d。使用游标卡尺测量4组不同套管间距,记录为真实值,并使用上述方法进行脉冲涡流检测,记录为检测值,实验结果如下表所示。真实值与检测值之间相对误差小,说明通过该检测方法可以获得准确的套管间距值。真实值(mm)检测值(mm)相对误差2.762.770.5%4.844.751.86%5.845.931.88%8.228.022.39%当前第1页12