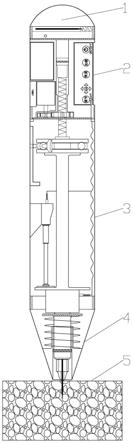
1.本发明涉及一种软岩强度测试针贯入装置及其使用方法,属于岩土工程检测技术领域。
背景技术:2.单轴抗压强度作为软岩的一个重要力学指标,对软岩稳定性研究具有重要意义,但由于软岩强度较低,结构松散,往往难以加工成标准试件,通过室内单轴测试仪器测得单轴抗压强度。行业内引入了一种方便快速野外测试软岩强度的针贯入仪,测试其贯入量和贯入力,通过经验公式推算其单轴抗压强度。但传统针贯入仪在人为加载过程中,会出现贯入速率不均匀、人工读数不准确导致实验数据不可靠,或是操作不当、用力过大、贯入量过深等情况导致断针的现象。
技术实现要素:3.本发明提供了一种软岩强度测试针贯入装置,通过合理的机械设计搭建了一种新的软岩强度测试针的贯入结构,配合本发明提供的一种软岩强度测试针贯入装置使用方法,可以有效地用于贯入针入岩、出岩。
4.本发明的技术方案是:一种软岩强度测试针贯入装置,包括加载仓2、贯入仓4;
5.加载仓2,用于通过电动机2
‑
8提供动力,驱动齿轮组2
‑
6带动螺纹杆2
‑
5向下/向上运动,从而实现加载/卸载;
6.贯入仓4,用于通过加载仓2的加载/卸载,进而带动贯入针4
‑
5入/出岩。
7.所述加载仓2包括金属外壳2
‑
1及安装在金属外壳2
‑
1中的螺纹杆2
‑
5、齿轮组2
‑
6、电动机2
‑
8,齿轮组2
‑
6包括齿轮ⅰ2
‑6‑
1、齿轮ⅱ2
‑6‑
2;其中,电动机2
‑
8的输出轴固定齿轮ⅱ2
‑6‑
2,齿轮ⅱ2
‑6‑
2外齿与齿轮ⅰ2
‑6‑
1外齿啮合,螺纹杆2
‑
5从齿轮ⅰ2
‑6‑
1中心开孔穿出后通过螺帽2
‑
7拧紧固定。
8.所述加载仓2包括备用针槽2
‑
2,备用针槽2
‑
2内部装有备用针2
‑2‑
1,备用针2
‑2‑
1针尖部位通过位于备用针槽2
‑
2中的海绵2
‑2‑
2保护,备用针槽2
‑
2一侧螺纹接口处设开口槽2
‑2‑
3。
9.所述加载仓2包括智能数控装置2
‑
4、usb接口2
‑
9、蓄电池2
‑
10,智能数控装置2
‑
4包括显示屏2
‑4‑
1、转换器2
‑4‑
2、控制主板2
‑4‑
3、电源开关键2
‑4‑
4、加载键2
‑4‑
5、恢复键2
‑4‑
6、调节键2
‑4‑
7;还包括滑动仓3,滑动仓3包括带凸点外壳3
‑
1、直线式位移传感器3
‑
3、受力杆3
‑
4、压电式压力传感器3
‑
5、可伸缩数据线3
‑
6;
10.所述控制主板2
‑4‑
3上引出数据线分别接入显示屏2
‑4‑
1、转换器2
‑4‑
2、电动机2
‑
8、usb接口2
‑
9、蓄电池2
‑
10,转换器2
‑4‑
2上另设有可伸缩数据线3
‑
6分别连接直线式位移传感器3
‑
3与压电式压力传感器3
‑
5;
11.所述控制主板2
‑4‑
3上的电源开关键2
‑4‑
4控制整个装置的供电;供电后,按下控制主板2
‑4‑
3上的调节键2
‑4‑
7进行上下左右调整实现参数的设置,设置完成按下加载键2
‑
4
‑
5进入加载模式,加载模式下,控制主板2
‑4‑
3先控制电动机2
‑
8转动,进而通过齿轮ⅰ2
‑6‑
1内圈带动螺纹杆2
‑
5向下运动实现加载;按下恢复键2
‑4‑
6进入卸载模式,卸载模式下,控制主板2
‑4‑
3控制电动机2
‑
8转动,进而齿轮ⅰ2
‑6‑
1内圈带动螺纹杆2
‑
5向上运动实现卸载;
12.所述带凸点外壳3
‑
1内部从上往下依次设置受力杆3
‑
4、压电式压力传感器3
‑
5,受力杆3
‑
4底部一侧设有与带凸点外壳3
‑
1内壁固定的直线式位移传感器3
‑
3,通过螺纹杆2
‑
5的向下/向上运动,带动受力杆3
‑
4、压电式压力传感器3
‑
5共同向下/向上运动,进而通过直线式位移传感器3
‑
3采集向下运动的位移经可伸缩数据线3
‑
6传递至转换器2
‑4‑
2,通过压电式压力传感器3
‑
5采集向下运动时的压力信息经可伸缩数据线3
‑
6传递至转换器2
‑4‑
2;转换器2
‑4‑
2将信息传至控制主板2
‑4‑
3,通过控制主板2
‑4‑
3驱动显示屏2
‑4‑
1显示。
13.还包括保护装置,所述保护装置包括转动轴承3
‑
2、l形开口滑槽;所述l形开口滑槽包括滑动槽3
‑1‑
1、锁定槽3
‑1‑
2、感应片3
‑1‑
3,转动轴承3
‑
2包括方形卡扣3
‑2‑
1、弹簧卡扣3
‑2‑
2、轴承盖板3
‑2‑
3、转动圈3
‑2‑
4、轴承底座3
‑2‑
5、钢珠3
‑2‑
6、弹簧ⅰ3
‑2‑
7;
14.所述滑动槽3
‑1‑
1一端与锁定槽3
‑1‑
2一端连接呈l形,感应片3
‑1‑
3位于锁定槽3
‑1‑
2自由端;方形卡扣3
‑2‑
1固接在转动圈3
‑2‑
4外圈上,弹簧卡扣3
‑2‑
2固定在轴承盖板3
‑2‑
3与轴承底座3
‑2‑
5之间,方形卡扣3
‑2‑
1与弹簧卡扣3
‑2‑
2通过弹簧ⅰ3
‑2‑
7连接,轴承底座3
‑2‑
5的底部凸台依次与转动圈3
‑2‑
4内圈配合、与轴承底座3
‑2‑
5固定连接,转动圈3
‑2‑
4通过钢珠3
‑2‑
6安装在轴承底座3
‑2‑
5的底部凸台处且转动圈3
‑2‑
4能绕轴承盖板3
‑2‑
3旋转;弹簧ⅰ3
‑2‑
7处于压缩状态下,方形卡扣3
‑2‑
1、弹簧卡扣3
‑2‑
2及弹簧ⅰ3
‑2‑
7沿滑动槽3
‑1‑
1滑动。
15.所述贯入仓4包括圆锥形外壳4
‑
1、固定垫片ⅱ4
‑
2、贯入杆4
‑
3、针夹4
‑
4、贯入针4
‑
5、螺旋套4
‑
6、弹簧ⅱ4
‑
7;所述圆锥形外壳4
‑
1内设有弹簧卡槽4
‑1‑
1、贯入杆滑槽4
‑1‑
2,弹簧ⅱ4
‑
7套在弹簧卡槽4
‑1‑
1底部与固定垫片ⅱ4
‑
2之间,贯入杆4
‑
3另一端嵌入贯入杆滑槽4
‑1‑
2后连接针夹4
‑
4,针夹4
‑
4为外侧带螺纹的开口夹,贯入针4
‑
5放入针夹4
‑
4后通过螺旋套4
‑
6旋紧固定贯入针4
‑
5。
16.一种软岩强度测试针贯入装置的使用方法,使用上述的软岩强度测试针贯入装置,包括如下步骤:
17.s1、检查整个设备螺纹口处是否拧紧;
18.s2、按下电源开关键2
‑4‑
4,启动智能数控装置2
‑
4:
19.1)、确保方形卡扣3
‑2‑
1处于非锁定状态;
20.2)、按下调节键2
‑4‑
7,调节设置模式;
21.s3、单手握住带凸点外壳3
‑
1,将贯入仓4孔口对准测试岩面,按下加载键2
‑4‑
5进入加载模式,同时直线式位移传感器3
‑
3、压电式压力传感器3
‑
5开始工作;其中,停止加载条件为:当达到设置模式设置的条件时,设备停止加载;当转动轴承3
‑
2向下运动使方形卡扣3
‑2‑
1弹入锁定槽3
‑1‑
2时,触发感应片3
‑1‑
3,设备停止加载;
22.s4、通过直线式位移传感器3
‑
3、压电式压力传感器3
‑
5采集的数据经转换器2
‑4‑
2转化为数字信号传至控制主板2
‑4‑
3,通过控制主板2
‑4‑
3驱动显示屏2
‑4‑
1显示;
23.s5、待加载停止后,将方形卡扣3
‑2‑
1拨回滑动槽3
‑1‑
1,按下恢复键2
‑4‑
6进入卸载模式,直到显示屏2
‑4‑
1数据归零;
24.s6、若达到试验要求组数,则需关闭电源。
25.所述s1步骤还包括检查保护装置是否处于锁定状态:如果处于锁定状态,则手动调节方形卡扣3
‑2‑
1,使弹簧ⅰ3
‑2‑
7压缩;否则,不做处理。
26.所述加载模式具体为:电动机2
‑
8驱动输出轴沿a方向转动,进而通过齿轮组2
‑
6带动螺纹杆2
‑
5向下运动,加载贯入针4
‑
5入岩;所述卸载模式具体为:电动机2
‑
8驱动输出轴沿b方向转动,通过齿轮组2
‑
6带动螺纹杆2
‑
5向上运动,卸载并收回贯入针4
‑
5;其中a方向为顺/逆时针时,则b方向为逆/顺时针方向。
27.本发明的有益效果是:本发明设计加载仓,由电动机驱动进行顺时针或逆时针匀速转动,通过齿轮组带动螺纹杆向下或者向上的匀速运动,从而实现均匀加载或卸载,避免了手动加载卸载时用力过猛导致的断针现象;设计智能数显装置,采用直线式位移传感器、压电式压力传感器采集数据,通过集线器将电信号转化为数字信号,最终通过显示屏输出贯入量、贯入力、单轴抗压强度等参数,采用高精度传感器使得读数更为精确,装置停止加载后数据不会回弹丢失;设计保护装置,当方形卡扣弹入锁定槽时将会触发感应片,装置立即停止加载,避免加载时超出量程范围,延长设备使用寿命。整体结构小巧美观,方便携带,对于难以制备标准室内试样的软岩,可用本装置进行原位试验测试其单轴抗压强度。
附图说明
28.图1为本发明工作时示意图;
29.图2为本发明非工作状态下示意图;
30.图3为本发明半球形后盖示意图;
31.图4为本发明加载仓示意图;
32.图5为本发明加载仓外壳示意图;
33.图6为本发明圆形固定槽示意图;
34.图7为本发明数控装置示意图;
35.图8为本发明螺纹杆、齿轮组、电动机示意图;
36.图9为本发明滑动仓示意图;
37.图10为本发明滑动仓外壳左视图;
38.图11为本发明转动轴承剖示图;
39.图12为本发明转动轴承俯视图;
40.图13为本发明转动轴承分解图;
41.图14为本发明直线式位移传感器示意图;
42.图15为本发明压电式压力传感器示意图;
43.图16为本发明贯入仓示意图;
44.图17为本发明圆锥形外壳示意图;
45.图18为本发明贯入仓内部结构;
46.图19为本发明操作流程示意图;
47.图中各标号为:半球形后盖1、圆形针孔1
‑
1、加载仓2、金属外壳2
‑
1、显示器开口2
‑1‑
1、功能键开口2
‑1‑
2、usb开口2
‑1‑
3、备用针槽2
‑
2、备用针2
‑2‑
1、海绵2
‑2‑
2、开口槽2
‑2‑
3、固定槽2
‑
3、智能数控装置固定槽2
‑3‑
1、螺纹杆滑槽2
‑3‑
2、齿轮卡槽2
‑3‑
3、电动机卡槽2
‑3‑
4、蓄电池卡槽2
‑3‑
5、智能数控装置2
‑
4、显示屏2
‑4‑
1、转换器2
‑4‑
2、控制主板2
‑4‑
3、
电源开关键2
‑4‑
4、加载键2
‑4‑
5、恢复键2
‑4‑
6、调节键2
‑4‑
7、螺纹杆2
‑
5、橡皮圈ⅰ2
‑5‑
1、齿轮组2
‑
6、齿轮ⅰ2
‑6‑
1、齿轮ⅱ2
‑6‑
2、螺帽2
‑
7、电动机2
‑
8、usb接口2
‑
9、蓄电池2
‑
10、固定垫片ⅰ2
‑
11、带孔固定垫片2
‑
12、滑动仓3、带凸点外壳3
‑
1、滑动槽3
‑1‑
1、锁定槽3
‑1‑
2、感应片3
‑1‑
3、转动轴承3
‑
2、方形卡扣3
‑2‑
1、弹簧卡扣3
‑2‑
2、轴承盖板3
‑2‑
3、转动圈3
‑2‑
4、轴承底座3
‑2‑
5、钢珠3
‑2‑
6、弹簧ⅰ3
‑2‑
7、直线式位移传感器3
‑
3、受力杆3
‑
4、压电式压力传感器3
‑
5、可伸缩数据线3
‑
6、贯入仓4、圆锥形外壳4
‑
1、弹簧卡槽4
‑1‑
1、贯入杆滑槽4
‑1‑
2、固定垫片ⅱ4
‑
2、贯入杆4
‑
3、橡皮圈ⅱ4
‑3‑
1、针夹4
‑
4、贯入针4
‑
5、螺旋套4
‑
6、弹簧ⅱ4
‑
7、试验试样5。
具体实施方式
48.实施例1:如图1
‑
18所示,一种软岩强度测试针贯入装置,包括加载仓2、贯入仓4;加载仓2,用于通过电动机2
‑
8提供动力,驱动齿轮组2
‑
6带动螺纹杆2
‑
5向下/向上运动,从而实现加载/卸载;贯入仓4,用于通过加载仓2的加载/卸载,进而带动贯入针4
‑
5入/出岩。
49.进一步地,可以设置所述加载仓2包括金属外壳2
‑
1及安装在金属外壳2
‑
1中的螺纹杆2
‑
5、齿轮组2
‑
6、电动机2
‑
8,齿轮组2
‑
6包括齿轮ⅰ2
‑6‑
1、齿轮ⅱ2
‑6‑
2;其中,电动机2
‑
8的输出轴通过焊接/键槽配合等方式固定齿轮ⅱ2
‑6‑
2,齿轮ⅱ2
‑6‑
2外齿与齿轮ⅰ2
‑6‑
1外齿啮合,螺纹杆2
‑
5从齿轮ⅰ2
‑6‑
1中心开孔穿出后通过螺帽2
‑
7拧紧固定且螺纹杆2
‑
5与中心开孔螺纹配合。
50.进一步地,可以设置所述加载仓2包括备用针槽2
‑
2,备用针槽2
‑
2位于金属外壳2
‑
1顶部,备用针槽2
‑
2内部装有备用针2
‑2‑
1,备用针2
‑2‑
1针尖部位通过位于备用针槽2
‑
2中的海绵2
‑2‑
2保护,备用针槽2
‑
2一侧螺纹接口处设开口槽2
‑2‑
3。
51.进一步地,可以设置所述加载仓2包括智能数控装置2
‑
4、usb接口2
‑
9、蓄电池2
‑
10,智能数控装置2
‑
4包括显示屏2
‑4‑
1、转换器2
‑4‑
2、控制主板2
‑4‑
3、电源开关键2
‑4‑
4、加载键2
‑4‑
5、恢复键2
‑4‑
6、调节键2
‑4‑
7;还包括位于加载仓2与贯入仓4之间的滑动仓3,滑动仓3包括带凸点外壳3
‑
1、直线式位移传感器3
‑
3、受力杆3
‑
4、压电式压力传感器3
‑
5、可伸缩数据线3
‑
6;
52.所述控制主板2
‑4‑
3上引出数据线分别接入显示屏2
‑4‑
1、转换器2
‑4‑
2、电动机2
‑
8、usb接口2
‑
9、蓄电池2
‑
10,转换器2
‑4‑
2上另设有可伸缩数据线3
‑
6分别连接直线式位移传感器3
‑
3与压电式压力传感器3
‑
5;
53.所述usb接口2
‑
9连接外部电源,控制主板2
‑4‑
3上的电源开关键2
‑4‑
4控制整个设备的供电进入工作状态;供电后,按下控制主板2
‑4‑
3上的调节键2
‑4‑
7进行上下左右调整实现参数的设置,设置完成按下加载键2
‑4‑
5进入加载模式,加载模式下,控制主板2
‑4‑
3先控制电动机2
‑
8的输出轴做顺时针转动,齿轮ⅰ2
‑6‑
1内圈带动螺纹杆2
‑
5向下匀速运动实现加载;按下恢复键2
‑4‑
6进入卸载模式,卸载模式下,控制主板2
‑4‑
3控制电动机2
‑
8的输出轴做逆时针转动,齿轮ⅰ2
‑6‑
1内圈带动螺纹杆2
‑
5向上匀速运动实现卸载(或者也可加载模式采用逆时针转动、卸载模式采用顺时针转动);通过机械运动控制方式,避免了手动加载时用力过猛导致的断针现象。再者加载键2
‑4‑
5、恢复键2
‑4‑
6启动前检查保护装置是否锁定,如果锁定,则手动调整方形卡扣,使弹簧ⅰ3
‑2‑
7压缩;检查可以人工检查,或者智能控制,即控制主板收集的感应片信息为响应状态,则锁定调节键2
‑4‑
7。
54.所述带凸点外壳3
‑
1内部从上往下依次设置受力杆3
‑
4、压电式压力传感器3
‑
5(如果设置了保护装置,则受力杆3
‑
4上端连接转动轴承;如果没有设置保护装置,则受力杆3
‑
4上端直接与加载仓中的螺帽2
‑
7连接),受力杆3
‑
4底部一侧设有与带凸点外壳3
‑
1内壁固定的直线式位移传感器3
‑
3,通过螺纹杆2
‑
5的向下/向上运动,带动受力杆3
‑
4、压电式压力传感器3
‑
5共同向下/向上运动,进而通过直线式位移传感器3
‑
3采集向下运动的位移经可伸缩数据线3
‑
6传递至转换器2
‑4‑
2,通过压电式压力传感器3
‑
5采集向下运动时的压力信息经可伸缩数据线3
‑
6传递至转换器2
‑4‑
2;转换器2
‑4‑
2将信息传至控制主板2
‑4‑
3,通过控制主板2
‑4‑
3驱动显示屏2
‑4‑
1显示。
55.进一步地,可以设置还包括保护装置,所述保护装置包括转动轴承3
‑
2、l形开口滑槽,(如果设置了受力杆3
‑
4,则转动轴承3
‑
2用于连接螺帽2
‑
7及受力杆3
‑
4;或者转动轴承3
‑
2用于连接螺帽2
‑
7及贯入仓4中的垫片);所述l形开口滑槽包括滑动槽3
‑1‑
1、锁定槽3
‑1‑
2、感应片3
‑1‑
3,转动轴承3
‑
2包括方形卡扣3
‑2‑
1、弹簧卡扣3
‑2‑
2、轴承盖板3
‑2‑
3、转动圈3
‑2‑
4、轴承底座3
‑2‑
5、钢珠3
‑2‑
6、弹簧ⅰ3
‑2‑
7;
56.所述滑动槽3
‑1‑
1一端与锁定槽3
‑1‑
2一端连接呈l形,位于锁定槽3
‑1‑
2自由端的感应片3
‑1‑
3连接控制主板2
‑4‑
3/或者可以将信息传动电动机驱动装置进而驱动电动机停止;方形卡扣3
‑2‑
1焊接在转动圈3
‑2‑
4外圈上,弹簧卡扣3
‑2‑
2焊接固定在轴承盖板3
‑2‑
3与轴承底座3
‑2‑
5之间,方形卡扣3
‑2‑
1与弹簧卡扣3
‑2‑
2通过弹簧ⅰ3
‑2‑
7连接,轴承底座3
‑2‑
5的底部凸台依次与转动圈3
‑2‑
4内圈配合、与轴承底座3
‑2‑
5固定连接,转动圈3
‑2‑
4通过钢珠3
‑2‑
6安装在轴承底座3
‑2‑
5的底部凸台处且转动圈3
‑2‑
4能绕轴承盖板3
‑2‑
3旋转;弹簧ⅰ3
‑2‑
7处于压缩状态下,方形卡扣3
‑2‑
1、弹簧卡扣3
‑2‑
2及弹簧ⅰ3
‑2‑
7沿滑动槽3
‑1‑
1滑动;通过给方形卡扣3
‑2‑
1施力带动其随转动圈3
‑2‑
4转动,进而压缩与弹簧卡扣3
‑2‑
2连接的弹簧ⅰ3
‑2‑
7使其能沿滑动槽3
‑1‑
1滑动;方形卡扣3
‑2‑
1移动至滑动槽3
‑1‑
1底端,会使弹簧ⅰ3
‑2‑
7回弹至锁定槽。即所述上部方形卡扣3
‑2‑
1嵌入滑动槽3
‑1‑
2时,弹簧ⅰ3
‑2‑
7处于压缩状态,当方形卡扣3
‑2‑
1滑至刻度端底端时,弹簧ⅰ3
‑2‑
7回弹,将方形卡扣3
‑2‑
1弹入锁定槽3
‑1‑
2,触发感应片3
‑1‑
3,使电动机2
‑
8停止转动,停止加载;从而避免加载时超出量程范围,延长设备使用寿命。
57.进一步地,可以设置所述贯入仓4包括圆锥形外壳4
‑
1、固定垫片ⅱ4
‑
2、贯入杆4
‑
3、针夹4
‑
4、贯入针4
‑
5、螺旋套4
‑
6、弹簧ⅱ4
‑
7;所述圆锥形外壳4
‑
1内设有呈上下布置的弹簧卡槽4
‑1‑
1、贯入杆滑槽4
‑1‑
2如果贯入装置包括加载仓2、贯入仓4,则两者外壳连接,如果还包括滑动仓3,则加载仓2与滑动仓3外壳连接、滑动仓3与贯入仓4连接,固定垫片ⅱ4
‑
2连接贯入杆4
‑
3一端(如果设置了滑动仓3,则固定垫片ⅱ4
‑
2另一端面连接压电式压力传感器3
‑
5;或者如果没有滑动仓3,有保护装置,则连接转动轴承3
‑
2;或者直接连接加载仓2中的螺帽2
‑
7),弹簧ⅱ4
‑
7套在弹簧卡槽4
‑1‑
1底部与固定垫片ⅱ4
‑
2之间,通过固定垫片进行限制贯入杆向下的运动距离,贯入杆4
‑
3另一端套有橡皮圈ⅱ4
‑3‑
1后嵌入贯入杆滑槽4
‑1‑
2且端部连接针夹4
‑
4一端(通过橡皮圈ⅱ4
‑3‑
1实现贯入杆4
‑
3与贯入杆滑槽4
‑1‑
2接触);针夹4
‑
4为外侧带螺纹的开口夹,贯入针4
‑
5放入针夹4
‑
4后通过螺旋套4
‑
6旋紧固定贯入针4
‑
5。
58.如图19所示,一种软岩强度测试针贯入装置的使用方法,使用上述的软岩强度测试针贯入装置,包括如下步骤:
59.进行原位试验时需选择合适的软岩露头(即试验试样5),用砂纸打磨岩面,使其平整。
60.s1、检查整个设备螺纹口处是否拧紧;
61.s2、按下电源开关键2
‑4‑
4,启动智能数控装置2
‑
4:
62.1)、确保方形卡扣3
‑2‑
1处于非锁定状态:如果处于锁定状态,则锁定调节键2
‑4‑
7,否则进入下一操作;
63.2)、按下调节键2
‑4‑
7,调节设置模式;
64.s3、单手握住带凸点外壳3
‑
1,将贯入仓4孔口对准测试岩面,按下加载键2
‑4‑
5进入加载模式,同时直线式位移传感器3
‑
3、压电式压力传感器3
‑
5开始工作,加载时另一支手扶在半球形后盖1处,尽量确保设备贯入方向不变;其中,停止加载条件为:当达到设置模式设置的条件时,设备停止加载(比如加载时间达至设置值时,停止);当转动轴承3
‑
2向下运动使方形卡扣3
‑2‑
1弹入锁定槽3
‑1‑
2时,触发感应片3
‑1‑
3,设备停止加载;
65.s4、通过直线式位移传感器3
‑
3、压电式压力传感器3
‑
5采集的数据经转换器2
‑4‑
2转化为数字信号传至控制主板2
‑4‑
3,通过控制主板2
‑4‑
3驱动显示屏2
‑4‑
1显示(即通过显示屏2
‑4‑
1输出贯入深度、贯入力、单轴抗压强度等参数);
66.s5、待加载停止后,将方形卡扣3
‑2‑
1拨回滑动槽3
‑1‑
1,按下恢复键2
‑4‑
6进入卸载模式,直到显示屏2
‑4‑
1数据归零;
67.s6、若达到试验要求组数,则需关闭电源,清洁装置。
68.进一步地,可以设置所述s1步骤还包括检查保护装置是否处于锁定状态:如果处于锁定状态,则手动调节方形卡扣3
‑2‑
1,使弹簧ⅰ3
‑2‑
7压缩;否则,不做处理。
69.进一步地,可以设置所述加载模式具体为:电动机2
‑
8驱动输出轴沿a方向转动,进而通过齿轮组2
‑
6带动螺纹杆2
‑
5向下运动,加载贯入针4
‑
5入岩;所述卸载模式具体为:电动机2
‑
8驱动输出轴沿b方向转动,通过齿轮组2
‑
6带动螺纹杆2
‑
5向上运动,卸载并收回贯入针4
‑
5;其中a方向为顺/逆时针时,则b方向为逆/顺时针方向。
70.再进一步地,可以设置如下:
71.部件加载仓2上可以设置由不锈钢金属制成的半球形后盖1,螺纹口处设有圆形针孔1
‑
1。呈上下布置的半球形后盖1、加载仓2、滑动仓3、贯入仓4可以将其外壳通过螺纹接口连接固定。
72.满足以半球形后盖1、加载仓2、滑动仓3、贯入仓4的顺序从上往下布置;
73.所述金属外壳2
‑
1右侧设有显示器开口2
‑1‑
1用于安装显示屏2
‑4‑
1、设有功能键开口2
‑1‑
2用于安装功能键,左下侧设有usb开口2
‑1‑
3用于安装usd接口2
‑
9,备用针槽2
‑
2位于金属外壳2
‑
1顶部,所述备用针槽2
‑
2为塑料圆管,圆管内部装有备用针2
‑2‑
1,备用针2
‑2‑
1右侧针尖部位通过位于备用针槽2
‑
2中的海绵2
‑2‑
2保护,左侧螺纹接口处设开口槽2
‑2‑
3(将半球形后盖1部分拧松,圆形针孔1
‑
1与螺纹接口处的开口槽2
‑2‑
3对齐后可将备用针2
‑2‑
1倒出;或者将半球形后盖1拧下来,通过螺纹接口处的开口槽2
‑2‑
3将备用针2
‑2‑
1倒出);金属外壳2
‑
1设有肩部,固定垫片ⅰ2
‑
11卡入金属外壳2
‑
1内侧并通过金属外壳2
‑
1肩部限位,通过固定垫片ⅰ2
‑
11对螺纹杆2
‑
5向上运动的位置进行限制;固定垫片ⅰ2
‑
11的下方设有固定槽2
‑
3,固定槽2
‑
3具体的包括:位于金属外壳2
‑
1内侧的智能数控装置卡槽2
‑3‑
1,中心设置螺纹杆滑槽2
‑3‑
2、下方设置齿轮组卡槽2
‑3‑
3,左侧设置电动机卡槽2
‑3‑
4、电
池卡槽2
‑3‑
6;转换器2
‑4‑
2、显示屏2
‑4‑
1、控制主板2
‑4‑
3通过螺栓连接嵌入智能数控装置卡槽2
‑3‑
1;电动机2
‑
8嵌入电动机卡槽2
‑3‑
4中,蓄电池2
‑
10嵌入蓄电池卡槽2
‑3‑
5中,齿轮ⅰ2
‑6‑
1、齿轮ⅱ2
‑6‑
2外齿咬合,组成齿轮组2
‑
6,齿轮ⅰ2
‑6‑
1内部带螺纹,齿轮ⅱ2
‑6‑
2焊接在电动机2
‑
8转动轴上,齿轮组2
‑
6嵌入齿轮卡槽2
‑3‑
3位置,螺纹杆2
‑
5上端设有橡皮圈ⅰ2
‑5‑
1,螺纹杆2
‑
5从上往下穿过滑槽2
‑3‑
2、齿轮ⅰ2
‑6‑
1、带孔固定垫片2
‑
12后用螺帽2
‑
7拧紧固定;带孔固定垫片2
‑
12通过滑动仓3中带凸点外壳3
‑
1支撑,通过固定垫片2
‑
12支撑安装在其上的固定槽2
‑
3、齿轮组。
74.所述直线式位移传感器3
‑
3右侧设有数据线接口,压电式压力传感器3
‑
5右侧设有数据线接口,直线式位移传感器3
‑
3与压电式压力传感器3
‑
5的数据线接口通过可伸缩数据线3
‑
6连接接入加载仓2的转换器2
‑4‑
2内。加载时通过直线式位移传感器3
‑
3、压电式压力传感器3
‑
5采集数据传至转换器2
‑4‑
2将电信号转化为数字信号,控制主板2
‑4‑
3写入计算程序并整合数据,最终通过显示屏2
‑4‑
1输出贯入深度、贯入力、单轴抗压强度等参数。
75.所述直线式位移传感器3
‑
3可以为高精度直线式位移传感器,使得可测精度为0.1mm,量程为0.1
‑
60mm;所述压电式压力传感器3
‑
5可以采用压电式压力传感器,使测量范围为3
‑
50kg。
76.所述贯入针4
‑
5为高强度,高韧性材质钢针,直径为1mm。
77.上面结合附图对本发明的具体实施方式作了详细说明,但是本发明并不限于上述实施方式,在本领域普通技术人员所具备的知识范围内,还可以在不脱离本发明宗旨的前提下做出各种变化。