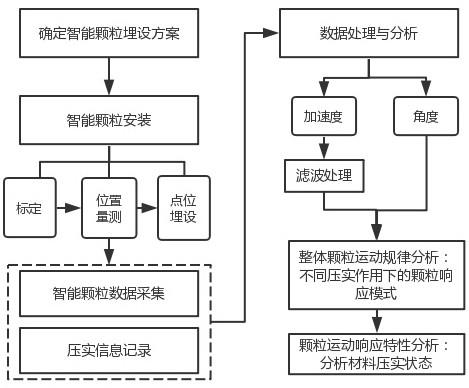
1.本发明属于道路工程技术领域,具体涉及一种基于智能颗粒的沥青路面压实实时监测方法。
背景技术:2.沥青混合料的压实是道路施工中的关键步骤之一。压实直接决定混合料的孔隙率及孔隙分布、材料的均匀性、路面的平整度等性能,并最终影响道路承载力和耐久性,且与路面早期损坏如车辙、水损害等具有直接关系。因此,有效的路面施工压实质量控制对于保障路面使用性能、提高路面使用寿命等具有重要的意义。
3.路基路面压实质量是道路施工质量管理最重要的内在指标之一,通常以压实度为监测指标。对于沥青路面,压实度指现场实际达到的密度与室内标准密度的比值。传统的沥青路面压实工艺的控制多以经验和宏观分析为主,现场压实机械参数的控制很大程度上依赖工程人员的现场经验,而对压实度的检测需在路面完全冷却后通过随机选点钻孔取样进行,该压实质量控制方法不仅具有破坏性,且效率低、代表性差,更无法为路面施工工艺提供实时性指导与监控,一旦路面质量检测结果不合格,大量的返工无疑是费时、费力和增加成本的。其他传统压实度检测方法包括核子/无核密度仪法、路面雷达技术等,这些方法能够对路面压实质量进行评定,但属于外部探测方法,其准确度依赖于标定参照物。所以,传统的路面压实监测几乎没有现场实时反馈,加之现场路面压实条件的复杂性,发生路面过压实、欠压实、均匀性差等问题的概率较大。
4.由于传统方法具有诸多弊端,近年来,智能压实技术以其能够实时监测压实质量、提高压实效率、能有效识别基层薄弱点、能通过压实曲线确定最佳压实遍数、减少人为主观误判造成的欠压、过压现象等优势,正受到道路施工行业的广泛关注。较为典型的智能压实系统,国外如dynapac/volvo公司的cmv检测系统、bomag公司的evib材料动态模量检测系统,国内长安大学开发的cms
‑
01压实度实时检测系统。各方面的研究认可了智能压实技术的显著优势,但是,由于沥青混合料具有较高的阻尼系数和变异性,建立准确、可靠、应用性强的振动轮
‑
材料的动力学模型难度较大,且智能压实的测量指标反映的是路面各个结构层(路基、基层、面层)的综合劲度,与铺层压实质量指标之间的关联关系仍需要大量研究。
5.从技术角度来看,智能压实技术仍然属于一种从外部探测材料响应的方法,影响对于路面内部材料压实度判断的准确度。为了改善这一现状,研究人员通过在路面内部埋设传感器的方法,例如光纤光栅传感器,实现了对于沥青路面压实过程的监测。但光纤光栅传感器存在安装过程复杂、与沥青混合料协同性差、测量值单一等问题。因此,迫切需要一种安装简便、能够实时、准确检测沥青混合料摊铺层内部压实质量的方法。
技术实现要素:6.本发明的目的在于针对上述现有技术中的不足,提供一种基于智能颗粒的沥青路面压实实时监测方法。
7.为达到上述目的,本发明通过以下技术方案予以实现:1)智能颗粒的安装,包括智能颗粒埋设方案的确定、初始标定、埋设和采集压实全过程中智能颗粒运动响应传感数据,记录压实机械碾压数据;2)智能颗粒加速度时域信号滤波处理;3)绘制智能颗粒传感数据中加速度与转动角度数据随时间的变化曲线,与压实机械碾压数据结合,获取不同压实机械作用相对应的颗粒运动响应模式;4)提取各次压实作用下的最大加速度响应值,以及各次压实机械作用下的整体角度变化值和相对角度变化值;5)根据4)中获取的智能颗粒运动响应特性的变化规律进行分析,实现对于路面压实状态的实时监测。
8.所述的步骤1)具体包括:设计智能颗粒埋设方案,包括智能颗粒埋设数量、埋设深度、横向纵向分布的确定;对传感器进行初始标定,于压实开始前,将智能颗粒传感器静置于水平地面上,保持与接收端连接状态并采集2
‑
3分钟数据,为了便于分析,在标定过程中传感器静置方向通常为z轴竖直向下,x、y轴分别平行于行车方向和垂直于行车方向;根据智能颗粒路面层埋设方案,用卷尺量测确定颗粒埋设点位,在摊铺机摊铺之后,迅速在埋设点位根据埋设深度,用小铲挖出一定沥青混合料、放入传感器、并用沥青混合料重新填充和整平;压实全过程中保持智能颗粒与接收端的连接并采集数据,包括颗粒三轴加速度与三轴转动值;对智能颗粒埋设点位处的压路机类型、作用时间、作用方向信息,采用影像方式记录。
9.所述的步骤2)具体包括:加速度信号滤波处理,对加速度时域信号进行傅里叶变换,获得频域信号,并选取能量突出的主频率段,对时域信号进行带通滤波处理,过滤白噪音。
10.所述的步骤3)具体包括:绘制智能颗粒传感数据加速度与转动角随时间的变化曲线,并与压实机械碾压数据对应,获取不同压实机械作用相对应的颗粒运动响应模式;所述的步骤4)中提取最大加速度响应值的方法为,在单次压实作用下颗粒的加速度响应数据中选取具有最大绝对值的加速度值;计算整体角度变化值和相对角度变化值的方法为,整体角度变化值为压实机械作用前后的颗粒角度变化值,相对角度变化值为单次压实机械作用过程中的颗粒最大、最小角度差值。
11.所述的步骤5)中的数据分析过程包括对于最大加速度响应值、整体角度变化值和相对角度变化值在压实过程中变化规律的分析,颗粒加速度、角度的变化趋势与沥青混合料的密实状态相关。
12.与现有技术相比,本发明具有以下优点:一、本发明采用的智能颗粒通过无线传输数据的方式进行数据采集,安装过程简单,可操作性强,传感器尺寸与粗集料大小相近,不破坏沥青混合料的整体性、与沥青混合料相融性优良;二、本发明能够真正获得沥青混合料压实过程中,细观层面颗粒的响应特性,从颗粒自身运动响应的角度出发进行动态的、实时的压实监测。颗粒的转动和移动状态,与混合料的密实状态、性能变化密切相关,通过智能颗粒的实时监测过程,能够给予工程施工人员及时的反馈以实现压实机械参数的调整。
13.三、本发明采用的智能颗粒从沥青混合料内部的角度对颗粒运动行为进行监测,不仅不影响传统压实机械、甚至智能压实机械的正常运行和监测,还可以作为它们的有效补充,使铺层整体外部响应测量结果和内部颗粒响应相结合,提高沥青面层压实质量监测的准确性。
附图说明
14.图1为本发明的方法流程图。
15.图2为本发明实施例智能颗粒埋设示意图。
16.图3为本发明实施例加速度数据滤波处理过程示意图。
17.图4为本发明实施例现场压实智能颗粒的运动响应。
18.图5为本发明实施例颗粒最大加速度响应值提取图。
19.图6为本发明实施例颗粒整体角度变化值和相对角度变化值提取图。
20.图7为本发明实施例智能颗粒最大加速度响应值变化图。
21.图8为本发明实施例智能颗粒整体角度变化图。
22.图9为本发明实施例智能颗粒相对角度变化图。
具体实施方式
23.如图1所示,本发明提供一种基于智能颗粒的沥青路面压实实时监测方法,提出了智能颗粒在现场路面压实中的标定、埋设与监测方法,进一步,通过提取颗粒典型的运动响应形态,分析颗粒在不同压实机械作用下的响应模式,从材料内部反映压实作用机理,并根据颗粒响应特征值在压实过程中的变化规律,分析判断材料的压实状态,为压实监测给予实时性指导。
24.下面结合附图和具体实施例对本发明进行详细说明。
25.本实例对沥青路面面层的压实采用智能颗粒技术进行监测。面层材料类型为sup
‑
25,材料设计参考superpave混合料设计法(aashto m323)进行,集料最大公称粒径为25mm,设计厚度11cm,设计沥青含量为3.9%,矿料间隙率为12.4%,有效沥青饱和度为67.5%。所用集料为石灰岩,具体级配如表1所示。所用沥青为70号道路石油沥青。
26.表1 现场路面层集料级配筛孔尺寸通过率(%)筛孔尺寸通过率(%)37.5mm1002.36mm24.326.5mm92.11.18mm17.819mm79.20.612.313.2mm54.30.399.5mm45.90.156.54.75mm35.60.0754.3本实例中的现场压实项目中所用到的压实机械主要为,悍马hd 138双钢轮压路机和徐工xp302轮胎压路机。悍马hd 138的主要参数为,静线压力32.5(前) /32.0(后) kg/cm,振动频率42(i)/50(ii) hz,振幅0.81(i)/0.41(ii)mm,激振力195(i)/139(ii)kn。徐工xp302为轮胎数量前4后5的轮胎压路机,接地比压为250
‑
480kpa。压实过程包括初压、复压
和终压三个阶段。初压阶段为1
‑
2遍静压实和振动压实的组合,持续约2分钟。复压阶段以轮胎压路机为主,其间穿插了2
‑
3遍振动压实,持续时长约25分钟。终压过程采用2
‑
3遍胶轮压路机进行,起到整平表面,消除轮迹的作用,持续时长约5分钟。整个压实过程的持续时间约为35分钟,压实环境温度在10
‑
15℃之间。
27.本实施例的具体实施过程如下所示:1、智能颗粒埋设方案的确定。如图2所示,选用两颗智能颗粒,埋设于第二行车道的轮迹带处,纵向上接近于面层的底部,距离层底约1cm高度,横向上间距为300cm。确定智能颗粒布设方案的主要考虑因素为:(1)将智能颗粒放置于层位底部,主要起到在压实机械高压力作用下保护颗粒的作用;(2)仍与层底保留1cm的高度距离是为了减轻边界作用的影响,使智能颗粒数据能够较为准确地代表所在层位处材料颗粒的运动规律;(3)埋设于行车道的轮迹带处,是为了使智能颗粒能够在路面使用期间发挥出监测交通信息和疲劳开裂、车辙等病害的潜在作用。
28.2、压实前智能颗粒标定。压实开始前,将智能颗粒按照所需局部坐标系的方向静置2
‑
3分钟,并采集数据,所采集的数据即可用于数据在大地坐标系与局部坐标系之间的转化。本实例中确定的局部坐标系即图2中所绘制的坐标系,z轴为竖直方向,y轴平行于行车方向,x轴垂直于行车方向。
29.3、智能颗粒的埋设。摊铺前做好智能颗粒埋设位置标记,在摊铺机完成摊铺工作后,通过卷尺测量确定智能颗粒埋设点位,用小铲将点位处沥青摊铺层按照设计埋设深度挖出混合料、将智能颗粒放入、再用混合料重新填充坑洞并粗略整平,智能颗粒埋设需在摊铺完成后迅速进行,以免影响后续跟进的压实过程。
30.4、压实与智能颗粒数据采集。在随后的压实过程中不间断采集智能颗粒数据,并通过相机录制视频的方式记录不同压实机械在智能颗粒埋设点位的作用时刻及压实方向信息。
31.5、智能颗粒加速度数据处理。如图3所示,首先将加速度时域信号转化为频域信号,根据频谱图选择能量较大的频率波段,本例中为0.4
‑
0.9hz段,采用带通滤波法,允许0.4
‑
0.9hz频段的波通过的同时,将其他范围的频率分量衰减到极低水平。由图3,经过带通滤波处理过后的加速度数据结果平滑。
32.6、智能颗粒在压实作用下的整体运动规律分析。不同压实机械作用时刻及智能颗粒加速度和角度变化响应如图4所示。结合图4,可以总结得到不同压实机械作用相对应的颗粒运动响应模式为:(1)静压实作用下,混合料在压路机自重作用下发生塑性变形,产生初步压密,其中的颗粒在z方向(竖直方向)上产生移动,这样的作用通常只在混合料较为松散的初压阶段;(2)振动压实作用下,混合料颗粒之间静摩擦力转化为动摩擦力,从而使混合料进一步密实。其中的颗粒在z方向(竖直方向)上产生移动;(3)胶轮压实作用下,混合料在揉搓作用下发生进一步密实。其中的颗粒在x和y方向上发生移动,同时在三个方向上均发生转动。并且x方向上的移动和z方向上的转动较为显著。
33.7、智能颗粒运动响应特性分析。如图5所示,提取各次振动压实作用下的颗粒最大
加速度响应值,如图6所示,提取各次胶轮压实过程中,颗粒的整体角度变化值和相对角度变化值。智能颗粒在各次振动压实作用下的最大加速度响应值变化规律如图7所示,智能颗粒在胶轮压实作用下的整体角度变化规律如图8所示,智能颗粒在胶轮压实作用下的相对角度变化规律如图9所示。
34.由图7,颗粒在振动压实作用下的z轴加速度响应值在初始1
‑
2遍碾压时较大,分别为0.9g和0.5g,但在之后迅速降低到较低水平(0.2g
‑
0.3g)。振动压实在初压阶段的作用关键,可以较为有效的密实混合料。而进入到复压阶段后,振动压实对于颗粒移动的影响变得十分有限,材料变形能力降低。
35.由图8,颗粒的三轴整体角度呈现前期连续变化、后期稳定的趋势。在压实前期的550s内,颗粒能够有效地与其他颗粒相互作用、调整位置以形成更加稳定的集料骨架结构,促进混合料的进一步密实。在压实550s至压实结束,颗粒整体角度稳定,集料骨架结构已基本形成,后续的胶轮压实作用不再对调整集料骨架有所作用。
36.由图9,颗粒的三轴相对角度变化大体上呈现逐渐降低的趋势,且在z轴和y轴上较为显著。室内旋转压实中,颗粒相对角度变化趋势与沥青混合料密度的变化趋势密切相关。现场颗粒相对角度变化与室内结果较为一致,随着胶轮压实作用下颗粒相对角度变化的减小,混合料的密度增大。
37.本实例的数据结果证明了将智能颗粒应用于现场沥青路面压实监测的可行性、可靠性。