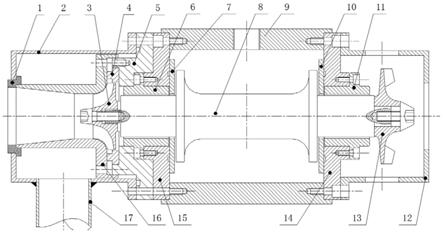
1.本发明涉及高速气体轴承、深冷及大型低温系统领域,特别是大型氦低温系统领域,具体是一种高压气体驱动动压气体轴承性能测试结构。
背景技术:2.在高速气体轴承领域、高速离心式压缩机领域、深低温领域、透平机械领域、超导、航空航天、大型氢&氦低温系统等对高速气体轴承、大型深低温有需求的领域,这些领域都有一个共同的特征:转子转速高、需要高速轴承支持。特别是大型氦低温系统、大型氢低温系统等的核心部件透平膨胀机。一般情况下,这些大型深低温系统,都需要用到透平膨胀机。透平膨胀机的转子高速旋转,需要用到高速气体轴承,动压气体轴承对中小型透平膨胀机的稳定性和运行效率有较大的影响,特别是超导核聚变氦低温系统的氦透平膨胀机。
3.全动压气体轴承技术为一种非供气、非接触式轴承支撑技术,具有零消耗、低摩擦、应用范围广、温区宽、转速高等优点。特别适合氦/氢低温系统的氦/氢透平膨胀机,可以显著降低运行成本,提高透平膨胀机的运行效率,大大提高氦/氢低温系统的运行稳定性与运行效率。
技术实现要素:4.本发明的目的是提供一种高压气体驱动动压气体轴承性能测试结构,提供一种新型动压气体轴承的性能测试结构,可以满足不同类型全动压气体轴承的测试需求,特别适合中小型氦/氢透平膨胀机用全动压气体轴承。
5.为了达到上述目的,本发明所采用的技术方案为:
6.一种高压气体驱动动压气体轴承性能测试结构,包括排气密封件、进气蜗壳、膨胀叶轮、喷嘴、喷嘴底座、左径向气体轴承、左止推气体轴承、主轴、机壳、右止推气体轴承、右径向气体轴承、风机蜗壳、制动叶轮、右径向气体轴承座、左径向气体轴承座、扩压器和进气管道。高压气体驱动膨胀叶轮,带着转子高速旋转(膨胀叶轮是动力源);膨胀叶轮(驱动叶轮)和制动叶轮分别放置于主轴两端;气体轴承采用的是全动压气体轴承,气体轴承分置于止推盘两端;转子结构采用双止推结构;两端气体轴承分别由左右轴承座限位,保证止推轴承轴向间隙为0.08~0.12mm。喷嘴内嵌于喷嘴底座,膨胀叶轮与制动叶轮分别通过螺纹与主轴连接。扩压器与喷嘴底座装配连接,通过调整喷嘴与喷嘴底座的调整垫片来调整膨胀叶轮与扩压器的叶顶间隙,保证叶顶间隙在0.2mm~0.3mm。本发明的一种高压气体驱动动压气体轴承性能测试结构亦可以应用于其他方面使用。
7.进一步地,所述的喷嘴底座材质为g10材料。
8.进一步地,所述气体轴承是全动压气体轴承。
9.进一步地,所述膨胀叶轮和制动叶轮由锻铝材料制成。
10.进一步地,所述的转速测量在机壳中部,转速计探头通过螺纹与机壳连接并保证探头与主轴的间隙。
11.进一步地,膨胀端进气管道,在膨胀叶轮侧,与进气蜗壳焊接。进气管道的长度根据现场需要,长度可以增加或减小。
12.本发明的安装过程如下:
13.先把左右径向气体轴承安装到左右径向气体轴承座内,再分别把左右止推气体轴承安装到轴承座上。接着把膨胀叶轮端轴承座安装到机壳上,并固定完成;把主轴(不带叶轮)从另一端安装到左径向气体轴承内,接着把右端轴承座安装到机壳上(需保证止推间隙,止推间隙通过右端轴承座和机壳之间的间隙调整垫片来保证),并固定完成,这样主体部分就安装完毕;接着安装制动叶轮,和风机蜗壳,右端部分就安装完毕。左端部分,安装喷嘴底座,安装喷嘴,安装膨胀叶轮,安装扩压器,安装排气密封件,安装进气蜗壳。保证出口密封垫片有被压紧,防止泄露。安装时要保证扩压器内壁回转面与膨胀轮外轮廓之间的间隙(叶顶间隙),叶顶间隙可通过喷嘴与喷嘴底座之间的调整垫片来调整。这样一个一种高压气体驱动动压气体轴承性能测试结构设计就完成了。
14.采用本发明结构装置,可有省去轴承气供气,简化透平膨胀机结构,可以有效改善转子结构形式,提高转子的临界转速,对转子的稳定运行有很大的益处。另外,运行时,风机蜗壳的进口可有用硬纸板来封堵,可以调节制动循环气量,从而调整转子转速,可以使得,在小的驱动力时,也可以形成高的转速。另外,通过更换轴承座部件,来实现不同气体轴承的测试,这样可以大大提高零部件的利用率,降低加工成本,提高效率。本发明具有良好的经济效益与现实效益。
附图说明
15.图1本发明的整机结构示意图;
16.图2排气密封件结构示意图;
17.图3进气蜗壳结构示意图;
18.图4膨胀叶轮结构示意图;
19.图5喷嘴结构示意图;
20.图6喷嘴底座结构示意图;
21.图7左径向轴承结构示意图;
22.图8左止推轴承结构示意图;
23.图9主轴结构示意图;
24.图10机壳结构示意图;
25.图11右止推轴承结构示意图;
26.图12右径向轴承结构示意图;
27.图13风机蜗壳结构示意图;
28.图14制动叶轮结构示意图;
29.图15右径向轴承座结构示意图;
30.图16左径向轴承座结构示意图;
31.图17扩压气结构示意图;
32.图18膨胀端进气管道结构示意图。
33.图中,1
‑
排气密封件、2
‑
进气蜗壳、3
‑
膨胀叶轮、4
‑
喷嘴、5
‑
喷嘴底座、6
‑
左径向气
体轴承、7
‑
左止推气体轴承、8
‑
主轴、9
‑
机壳、10
‑
右止推气体轴承、11
‑
右径向气体轴承、12
‑
风机蜗壳、13
‑
制动叶轮、14
‑
右径向气体轴承座、15
‑
左径向气体轴承座、16
‑
扩压器、17
‑
进气管道。
具体实施方式
34.下面结合附图和实施例对本发明进一步说明。
35.如图1
‑
图18所示,一种高压气体驱动动压气体轴承性能测试结构,主要由排气密封件1、进气蜗壳2、膨胀叶轮3、喷嘴4、喷嘴底座5、左径向气体轴承6、左止推气体轴承7、主轴8、机壳9、右止推气体轴承10、右径向气体轴承11、风机蜗壳12、制动叶轮13、右径向气体轴承座14、左径向气体轴承座15、扩压器16、进气管道17及部分标准等组成。
36.高压气体驱动膨胀叶轮3,带着转子高速旋转;膨胀叶轮3和制动叶轮13分别放置于主轴8两端;气体轴承采用的是全动压气体轴承,气体轴承分置于止推盘两侧;转子结构采用双止推结构;两端气体轴承分别由左右轴承座限位,保证止推轴承轴向间隙为0.08~0.12mm。喷嘴4内嵌于喷嘴底座5,膨胀叶轮3与制动叶轮13分别通过螺纹压紧并与主轴8连接。扩压器16与喷嘴4底座装配连接,扩压压紧喷嘴4上表面,通过调整喷嘴4与喷嘴底座5的调整垫片来调整膨胀叶轮3与扩压器16的叶顶间隙,保证叶顶间隙在0.2mm~0.3mm。膨胀叶轮3为驱动叶轮,是动力源。所述的喷嘴4底座材质为g10材料。所述气体轴承是全动压气体轴承。膨胀端进气管道17,在膨胀叶轮3侧,与进气蜗壳2焊接(焊接过程需要氩气保护)。进气管道17的长度根据现场需要,长度可以增加或减小。
37.本发明的安装过程如下:
38.先分别把左径向气体轴承6、右径向气体轴承11安装到左径向气体轴承座15、右径向气体轴承座14内,再分别把左止推气体轴承7、右止推气体轴承10分别安装到左径向气体轴承座15、右径向气体轴承座14上。接着把膨胀叶轮端轴承座安装到机壳9上,并固定完成;把主轴8(不带叶轮)从另一端安装到左径向气体轴承6内,接着把右端轴承座安装到机壳9上(需保证止推间隙,止推间隙通过右端轴承座和机壳9之间的间隙调整垫片来保证),并固定完成,这样主体部分就安装完毕;接着安装制动叶轮13,和风机蜗壳12,右端部分就安装完毕。左端部分,安装喷嘴底座5,安装喷嘴4,安装膨胀叶轮3,安装扩压器16,安装排气密封件1,安装进气蜗壳2。保证出口密封垫片有被压紧,防止泄露。安装时要保证扩压器16内壁回转面与膨胀轮外轮廓之间的间隙(叶顶间隙),叶顶间隙可通过喷嘴4与喷嘴底座5之间的调整垫片来调整。这样一种高压气体驱动动压气体轴承性能测试结构设计就完成了。
39.膨胀叶轮3与制动叶轮13由锻铝材料制成,气体轴承体为不锈钢材料,箔片是inconel x750材料,主轴为3cr13材料,喷嘴底座5为g10材料,排气密封件1为聚四氟乙烯材料,其余为304不锈钢材料。所述的转速测量在机壳9中部,转速计探头通过螺纹与机壳9连接并保证探头与主轴的间隙。
40.本发明未详细阐述部分属于本领域技术人员的公知技术。以上所述的实施例仅是对本发明的优选实施方式进行描述,优选实施例并没有详尽叙述所有的细节,也不限制该发明仅为所述的具体实施方式。在不脱离本发明设计精神的前提下,本领域普通技术人员对本发明的技术方案做出的各种变形和改进,均应落入本发明权利要求书确定的保护范围内。